Rocket Powder
Table of Contents
Imagine a world where metal transforms into a potent force, not just for building bridges and skyscrapers, but for propelling rockets towards the stars. This world isn’t science fiction; it’s the reality of Rocket Powder, a revolutionary class of metal powders designed to push the boundaries of performance in various industrial applications.
But what exactly is Rocket Powder, and how does it differ from your average metal dust? Buckle up, because we’re about to embark on a thrilling journey into the heart of this innovative material.
Elements of Rocket Powder
Unlike the black powder used in old-fashioned fireworks, Rocket Powder doesn’t contain any explosive compounds. Instead, it’s a meticulously crafted blend of various metal elements, each playing a crucial role in its unique properties. Here’s a peek into the symphony of elements that make up Rocket Powder:
Element | Function |
---|---|
Rhenium (Re) | The star of the show, Rhenium boasts exceptional high-temperature strength and oxidation resistance, allowing Rocket Powder to withstand extreme conditions. |
Tantalum (Ta) | This robust element complements Rhenium by enhancing creep resistance, a vital property for components under constant stress at elevated temperatures. |
Tungsten (W) | Think of Tungsten as the muscle behind the brawn. It contributes to overall strength and hardness, crucial for demanding applications. |
Molybdenum (Mo) | A master of versatility, Molybdenum offers a good balance between strength, machinability, and high-temperature performance. |
Nickel (Ni) | This element acts as a binder, holding the other elements together and ensuring the powder retains its shape during processing. |
Chromium (Cr) | A sprinkle of Chromium enhances corrosion resistance, protecting the Rocket Powder from environmental degradation. |
The specific composition of Rocket Powder can vary depending on the desired properties and application. Some manufacturers might add other elements like Cobalt (Co) or Hafnium (Hf) for even more specialized functionalities.
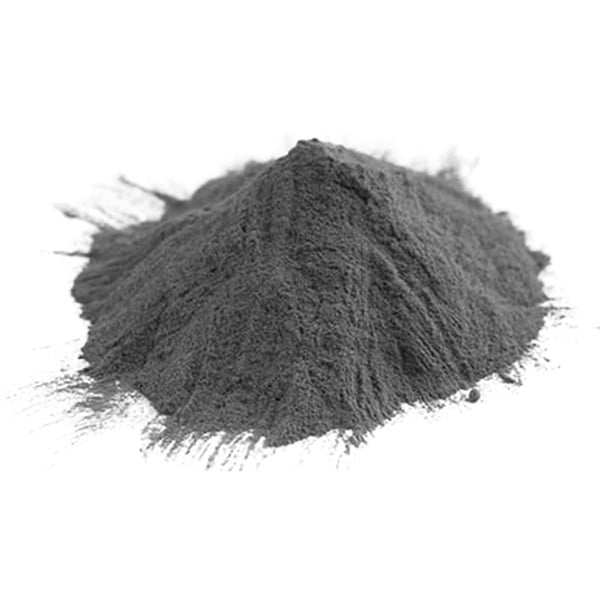
Applications of Rocket Powder
Now that we understand the building blocks, let’s explore where Rocket Powder truly shines:
Application | Advantages of Rocket Powder |
---|---|
High-Temperature Applications (e.g., turbine blades, rocket engine components) | – Exceptional high-temperature strength allows components to operate efficiently at scorching temperatures, exceeding the capabilities of traditional materials. – Superior creep resistance prevents components from warping or deforming under constant stress at high temperatures. |
Aerospace and Defense | – Lightweight nature reduces overall vehicle weight, improving fuel efficiency and payload capacity. – Outstanding mechanical properties ensure components can withstand the harsh environments encountered in aerospace and defense applications. |
Chemical and Petrochemical Processing | – Impenetrable resistance to corrosion protects equipment from harsh chemicals, extending service life and minimizing maintenance costs. – High-temperature stability allows for efficient processing of chemicals at elevated temperatures. |
These are just a few examples, and the potential applications of Rocket Powder are constantly expanding as engineers discover its remarkable properties.
Specific Metal Powder Models
With a diverse range of applications comes a diverse range of Rocket Powder models. Here’s a closer look at ten specific models and their unique characteristics:
- GRCop-42 (KBM Advanced Materials): This classic Rocket Powder formulation features a balanced blend of Rhenium and Tantalum, making it ideal for high-temperature applications like turbine blades and rocket engine components.
- AM321 (Höganäs AB): This model introduces Chromium alongside Rhenium and Tantalum, offering superior oxidation resistance for components operating in harsh environments.
- ATI-64 (ATI Allegheny Ludlum): This powerhouse option boasts a higher Tungsten content, translating to exceptional strength and wear resistance for demanding applications like wear plates and rolling mill components.
- Kennametal DM40 (Kennametal Inc.): This model prioritizes machinability alongside high-temperature performance. The inclusion of Molybdenum allows for easier shaping and fabrication while maintaining excellent strength at elevated temperatures.
- Plansee GW45 (Plansee SE): This Rocket Powder variant incorporates Hafnium, further enhancing its high-temperature capabilities and making it suitable for extreme aerospace applications.
- LPW Direct Manufacturing Diron 125 (LPW Technology Ltd.): Focusing on printability for additive manufacturing processes, this model prioritizes a finer particle size for smooth powder bed fusion while retaining the core strengths of Rocket Powder.
- Sandvik Osprey AM265 (Sandvik AB): This option from Sandvik boasts a unique combination of Rhenium, Tantalum, and Chromium, offering a well-rounded blend of high-temperature strength, oxidation resistance, and good printability for additive manufacturing.
- ExOne M2 Tool Steel (ExOne GmbH): This Rocket Powder formulation is specifically designed for additive manufacturing processes like binder jetting. It offers a balance of strength, wear resistance, and affordability, making it suitable for producing durable tools and molds.
- Höganäs AM12 (Höganäs AB): This budget-friendly option prioritizes cost-effectiveness while maintaining good overall performance. It’s a suitable choice for applications where absolute top-tier high-temperature properties aren’t essential.
- Carpenter Additive Wire 18Cr1NiMoVA (Carpenter Technology Corporation): This Rocket Powder variant caters to applications requiring exceptional corrosion resistance alongside high-temperature strength. The inclusion of a higher Chromium content makes it ideal for components exposed to harsh chemicals and elevated temperatures.
Application | Advantages of Rocket Powder | Disadvantages of Rocket Powder |
---|---|---|
High-Temperature Applications (e.g., turbine blades, rocket engine components) | – Exceptional high-temperature strength allows components to operate efficiently at scorching temperatures, exceeding the capabilities of traditional materials. – Superior creep resistance prevents components from warping or deforming under constant stress at high temperatures. | – Compared to some commonly used high-temperature alloys, Rocket Powder can be significantly more expensive due to the inclusion of rare earth elements like Rhenium. |
Aerospace and Defense | – Lightweight nature reduces overall vehicle weight, improving fuel efficiency and payload capacity. – Outstanding mechanical properties ensure components can withstand the harsh environments encountered in aerospace and defense applications. | – Due to its relatively new nature, there might be a lack of extensive long-term data on the performance of Rocket Powder in certain aerospace applications compared to well-established materials. |
Chemical and Petrochemical Processing | – Impenetrable resistance to corrosion protects equipment from harsh chemicals, extending service life and minimizing maintenance costs. – High-temperature stability allows for efficient processing of chemicals at elevated temperatures. | – Machinability of certain Rocket Powder models can be lower compared to some traditional materials, requiring specialized techniques or tooling. |
Selecting the Right Rocket Powde
This list just scratches the surface of the diverse Rocket Powder models available. With a growing number of manufacturers entering the fray, the selection continues to expand. Choosing the right Rocket Powder for your specific application requires careful consideration of several factors:
- Operating Temperatures: How hot will the components get during operation? Different Rocket Powder models offer varying degrees of high-temperature strength.
- Required Mechanical Properties: Does the application prioritize strength, wear resistance, or a combination of both? The specific elements and their ratios within the Rocket Powder will influence these properties.
- Environmental Considerations: Will the components be exposed to harsh chemicals or corrosive environments? Some Rocket Powder models excel in corrosion resistance.
- Processing Method: Is the Rocket Powder intended for traditional techniques like casting or forging, or is it optimized for additive manufacturing processes? Particle size and flowability become crucial factors.
- Cost Constraints: Rocket Powder can be expensive, so finding the right balance between performance and affordability is essential.
Consulting with a Material Specialist
Given the complexity of factors involved, consulting with a material specialist can be invaluable in selecting the most suitable Rocket Powder for your needs. These experts can guide you through the various options, considering your specific application requirements and budgetary constraints.
Specifications of RocketPowder
Once you’ve chosen a promising Rocket Powder model, it’s crucial to delve into its technical specifications.
Parameter | Description | Importance |
---|---|---|
Chemical Composition | The exact weight percentages of each element present in the Rocket Powder blend. | Knowing the precise composition allows for a deeper understanding of the material’s properties and performance. |
Particle Size Distribution | This refers to the variation in size of the individual metal particles within the Rocket Powder. | Particle size distribution significantly impacts factors like flowability, packing density, and printability in additive manufacturing. |
Apparent Density | The weight of Rocket Powder per unit volume in its loose, uncompacted state. | Apparent density influences how much powder is needed to fill a specific mold or container. |
Tap Density | The density of Rocket Powder after a standardized tapping procedure. | Tap density provides a more realistic picture of how much powder can be packed into a given volume. |
Flowability | A measure of how easily the Rocket Powder powder flows. | Good flowability is essential for efficient processing in techniques like powder bed fusion and cold spray deposition. |
Melting Point | The temperature at which the Rocket Powder transitions from a solid to a liquid state. | The melting point is a crucial consideration for selecting the appropriate processing techniques. |
Standards and Certifications
For many applications, adhering to specific industry standards and certifications is essential. Rocket Powder manufacturers typically provide information on relevant standards their products comply with. Some common standards for metal powders include:
- ASTM International (ASTM): A globally recognized organization that sets standards for various materials, including metal powders.
- Additive Manufacturing Standards (AMS): A collection of industry standards specifically developed for additive manufacturing processes.
- Mil-Spec (Military Specifications): For applications in the aerospace and defense sector, meeting relevant Mil-Specs might be mandatory.
Obtaining the Right Information
Consulting the technical datasheet provided by the Rocket Powder manufacturer is the best way to obtain detailed information on all the above-mentioned specifications. Reputable manufacturers will provide comprehensive datasheets that outline the key properties, processing recommendations, and adherence to relevant standards.
Suppliers and Pricing
Having identified the ideal Rocket Powder model based on application and specifications, the next step is finding a reliable supplier. Several factors come into play when choosing a supplier:
- Product Availability: Does the supplier offer the specific Rocket Powder model you require?
- Minimum Order Quantity: Some suppliers might have minimum order quantities that might not be suitable for smaller projects.
- Pricing and Payment Terms: Comparing prices from different suppliers can help you secure the best deal. Payment terms like credit options can also influence your decision.
- Delivery Timeframes: Consider the lead time for obtaining the Rocket Powder and factor it into your project timeline.
- Supplier Reputation: Researching the supplier’s reputation for quality, customer service, and technical expertise can provide valuable insights.
Beyond Price: The Value Proposition
While price is certainly a consideration, focusing solely on the cheapest option might not be the wisest move in the long run. A reliable supplier with a proven track record of quality and excellent customer service can offer significant value beyond just the initial cost.
For instance, a reputable supplier might offer technical support and guidance throughout the selection and processing stages. They might also provide access to additional resources like case studies and application examples, proving the Rocket Powder‘s effectiveness in similar scenarios.
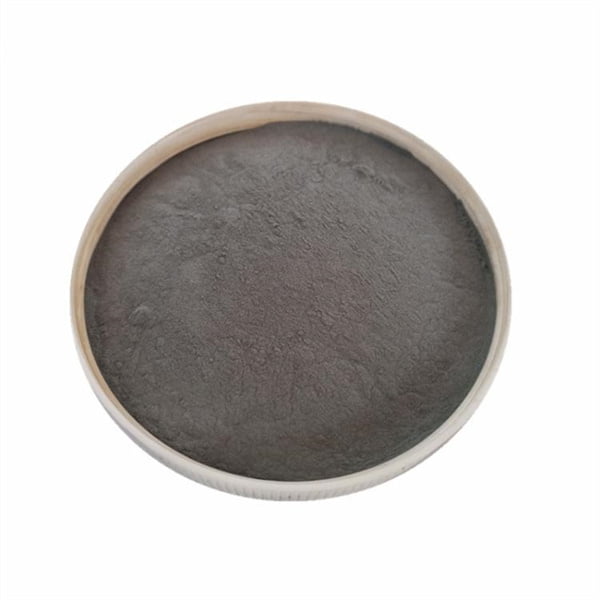
FAQ
In a world brimming with technical jargon, navigating the complexities of Rocket Powder can be daunting. Here’s a table addressing some frequently asked questions to shed some light on this innovative material:
Question | Answer |
---|---|
What are the advantages of Rocket Powder? | Rocket Powder boasts exceptional high-temperature strength, superior creep resistance, lightweight properties, and outstanding mechanical properties. It also offers excellent corrosion resistance for specific models. |
What are the disadvantages of Rocket Powder? | Compared to traditional materials, Rocket Powder can be more expensive due to the inclusion of rare earth elements. Additionally, it might have a lack of extensive long-term data in certain applications compared to well-established materials. Machinability of some models can also be a challenge. |
What are some applications of Rocket Powder? | Rocket Powder finds applications in high-temperature environments like turbine blades and rocket engine components. It excels in the aerospace and defense sector due to its lightweight nature and exceptional mechanical properties. The chemical and petrochemical processing industry also leverages Rocket Powder’s corrosion resistance and high-temperature stability. |
Share On
MET3DP Technology Co., LTD is a leading provider of additive manufacturing solutions headquartered in Qingdao, China. Our company specializes in 3D printing equipment and high-performance metal powders for industrial applications.
Inquiry to get best price and customized Solution for your business!
Related Articles
About Met3DP
Recent Update
Our Product
CONTACT US
Any questions? Send us message now! We’ll serve your request with a whole team after receiving your message.
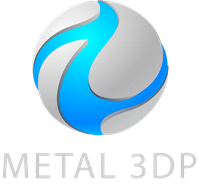
Metal Powders for 3D Printing and Additive Manufacturing