selective electron beam melting
Table of Contents
Imagine crafting complex metal objects layer by layer, with unparalleled precision and the ability to handle even the most challenging materials. That’s the magic of Selective Electron Beam Melting (SEBM), a revolutionary 3D printing technology that’s transforming the way we design and manufacture metal components.
What is selective electron beam melting?
selective electron beam melting falls under the umbrella of Additive Manufacturing (AM), also known as 3D printing. It’s a powder-bed fusion technique where a high-powered electron beam selectively melts metal powder particles to create a 3D object, one layer at a time. This all happens within a high-vacuum chamber, preventing oxidation and ensuring a clean, high-quality build.
How selective electron beam melting Works
Think of SEBM as a microscopic sculptor wielding an electron beam as its chisel. Here’s a breakdown of the process:
- Preparation: A 3D model is sliced into thin layers, forming the digital blueprint for the object. The build chamber is filled with a fine layer of metallic powder specific to the desired final product.
- Electron Beam Action: A focused electron beam, generated by an electron gun, scans across the powder bed according to the sliced model data. The high energy of the beam melts the targeted powder particles, fusing them together to form the first layer of the object.
- Layer by Layer: The build platform lowers slightly, and a fresh layer of powder is deposited across the previous layer. The electron beam then scans again, selectively melting the new powder particles and bonding them to the existing structure. This process repeats meticulously, building the object layer by layer until it’s complete.
- Cooling and Removal: Once the build is finished, the chamber cools down, and the final object is carefully removed from the surrounding powder. Depending on the design, some post-processing steps like support removal and surface finishing might be necessary.
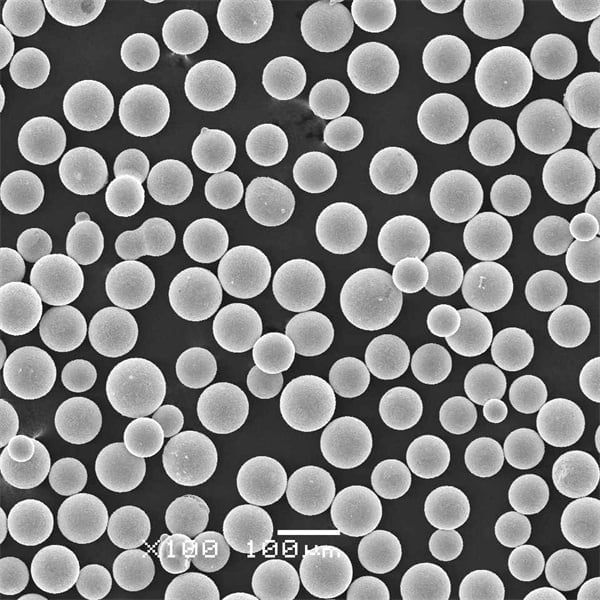
Common Metal Powders for SEBM
Metal Powder | Description | Properties | Applications |
---|---|---|---|
Titanium Alloys (Ti-6Al-4V, Ti-6Al-7Nb) | The workhorses of SEBM, offering excellent strength-to-weight ratio, biocompatibility, and high corrosion resistance. | Strong, lightweight, biocompatible, corrosion-resistant | Aerospace components, biomedical implants, dental prosthetics |
Stainless Steel (316L, 17-4PH) | Versatile and widely used, known for their excellent mechanical properties and corrosion resistance. | Strong, ductile, corrosion-resistant | Medical instruments, fluid handling components, automotive parts |
Inconel (IN625, 718) | Superalloys known for their exceptional strength and resistance to high temperatures and harsh environments. | High-temperature strength, oxidation resistance | Turbine blades, rocket engine components, heat exchangers |
Nickel Alloys (Monel 400, Hastelloy C-276) | Offer superior corrosion resistance and perform well in challenging chemical environments. | Corrosion-resistant, wear-resistant | Chemical processing equipment, valves, pumps |
Aluminum Alloys (AlSi10Mg, AlSi7Mg0.3) | Lightweight and offer good strength and machinability. | Lightweight, strong, machinable | Aerospace components, heat sinks, automotive parts (limited use due to higher cost compared to traditional methods) |
Cobalt Chrome (CoCrMo) | Biocompatible and wear-resistant, a popular choice for medical implants. | Biocompatible, wear-resistant | Hip and knee replacements, dental implants |
Copper Alloys (CuNi18Zn5Al, CuCr1Zr) | Offer high thermal and electrical conductivity, making them ideal for heat exchangers and electrical components. | High thermal conductivity, high electrical conductivity | Heat sinks, electrical connectors, brazing materials |
Tool Steels (H13, AISI M2) | Known for their high hardness and wear resistance, perfect for tooling applications. | Hard, wear-resistant | Cutting tools, dies, molds |
Precious Metals (Gold, Silver, Platinum) | High value and unique properties, used for specialized applications in jewelry, electronics, and aerospace. | High value, good electrical conductivity, biocompatible (for specific alloys) | Jewelry, electrical contacts, biomedical applications (limited) |
Refractory Metals (Tantalum, Tungsten) | Offer extremely high melting points and are ideal for high-temperature applications. | High melting point, high strength at |
Advantages of Selective Electron Beam Melting
SEBM boasts a range of advantages that make it a compelling choice for various metal 3D printing applications. Let’s delve into some of its key benefits:
- Unparalleled Design Freedom: SEBM allows for the creation of highly complex geometries with intricate features and internal channels, which would be near impossible or incredibly expensive to achieve with traditional manufacturing methods. This opens doors for innovative and lightweight designs that push the boundaries of functionality.
- Exceptional Material Properties: The high-vacuum environment and precise melting process in SEBM lead to parts with excellent mechanical properties, including high strength, good ductility, and outstanding fatigue resistance. These properties are often comparable or even superior to those achieved through traditional techniques like casting or forging.
- Superior Accuracy and Precision: The electron beam in SEBM offers exceptional control and precision, resulting in parts with tight tolerances and smooth surface finishes. This reduces the need for extensive post-processing and minimizes material waste.
- Material Efficiency: SEBM utilizes a powder-bed approach, meaning unused powder can be recovered and reused for subsequent builds. This minimizes material waste and offers a more sustainable production method compared to traditional subtractive manufacturing techniques.
- Reduced Lead Times: SEBM allows for the rapid prototyping and production of complex metal parts, eliminating the need for complex tooling and lengthy fabrication processes. This can significantly reduce lead times and accelerate product development cycles.
- Freedom of Material Choice: SEBM offers a wider range of compatible metal powders compared to other metal 3D printing technologies. This allows for the creation of parts from a diverse selection of materials with unique properties, catering to specific application demands.
Disadvantages of Selective Electron Beam Melting
While SEBM offers a plethora of advantages, it’s not without its limitations. Here’s a look at some of the drawbacks to consider:
- High Cost: SEBM machines and the associated materials tend to be expensive compared to traditional manufacturing methods. This can be a barrier for entry for smaller companies or those with limited budgets.
- Build Size Limitations: Current SEBM machines have limitations on build volume, restricting the size of parts that can be produced. However, advancements are continuously expanding these capabilities.
- Surface Roughness: While SEBM offers good surface finishes, they might not be as smooth as those achievable with some traditional machining techniques. Additional post-processing steps might be needed for applications requiring a highly polished surface finish.
- Support Structures: Similar to other 3D printing technologies, SEBM often requires the use of support structures for overhanging features. These supports need to be removed after the build, which can be a time-consuming and potentially delicate process.
- Limited Color Options: Unlike some other 3D printing technologies, SEBM is primarily focused on functional applications and doesn’t offer a wide range of color options for the finished parts.
Applications of Selective Electron Beam Melting
SEBM’s unique capabilities make it a valuable tool for various industries. Here are some prominent applications:
- Aerospace: The lightweight and high-strength properties of SEBM-produced parts make them ideal for aerospace applications. Components like landing gear parts, missile fins, and lightweight brackets can be created with intricate designs to optimize performance and weight reduction.
- Medical Devices: The biocompatibility of certain metal powders, coupled with the precision of SEBM, allows for the creation of customized medical implants, such as hip and knee replacements, dental prosthetics, and cranial implants. These implants offer excellent biocompatibility and can be tailored to individual patient needs.
- Automotive: SEBM is increasingly used in the automotive industry to produce high-performance components like lightweight pistons, complex cooling channels in engine blocks, and custom gears and shafts. This allows for weight reduction, improved efficiency, and enhanced performance.
- Energy Sector: SEBM is used to create highly resistant components for turbine blades and heat exchangers used in power generation due to the ability to utilize high-temperature alloys with excellent mechanical properties.
- Tooling: SEBM can produce complex cutting tools and dies with intricate geometries and high wear resistance. This allows for the creation of specialized tooling for specific applications and reduces production lead times.
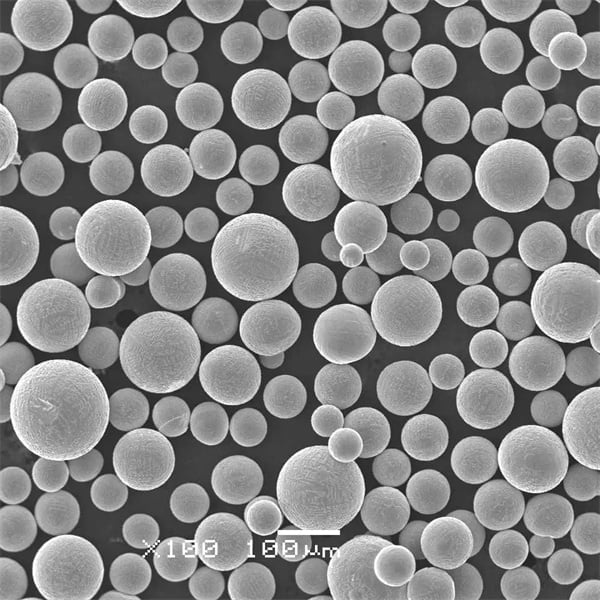
SEBM Metal Powders
We’ve explored the common metal powders used in SEBM, but let’s delve a bit deeper into some key factors to consider when choosing the right powder for your specific application:
- Particle Size and Distribution: The size and distribution of the powder particles significantly impact the final properties of the printed part. Finer powders generally result in smoother surface finishes but can be more challenging to work with due to flowability issues. Conversely, coarser powders offer better flowability but might lead to a rougher surface finish.
- Powder Purity: The purity of the metal powder directly affects the mechanical properties of the finished part. Impurities can weaken the material and lead to cracks or other defects. High-purity powders are essential for critical applications requiring optimal performance.
- Sphericity and Flowability: Ideally, metal powders for SEBM should be spherical in shape to ensure good flowability within the build chamber. Good flowability allows for even powder distribution and consistent melting during the build process.
- Chemical Composition: The specific chemical composition of the powder determines the final properties of the printed part. Consider factors like alloying elements, trace elements, and oxygen content when selecting a powder for your desired application.
Here’s a table summarizing some key considerations for SEBM metal powders:
Factor | Description | Impact |
---|---|---|
Particle Size and Distribution | The size and spread of powder particles. | Affects surface finish, density, and mechanical properties. |
Powder Purity | The absence of impurities in the metal powder. | Influences mechanical strength and reduces the risk of defects. |
Sphericity and Flowability | The roundness and ease with which powder flows. | Impacts layer quality, density, and overall build success. |
Chemical Composition | The specific elements and their proportions within the powder. | Determines final material properties like strength, corrosion resistance, and high-temperature performance. |
Specifications, Sizes, Grades, and Standards for SEBM Metal Powders
Metal powders for SEBM adhere to specific industry standards to ensure consistent quality and printability. Here’s an overview of some key aspects:
- ASTM International (ASTM): ASTM publishes various standards for metal powders used in additive manufacturing, including ASTM F3049 for metal powders for AM and ASTM B294 for titanium and titanium alloy powders.
- Material Data Sheets (MDS): Metal powder suppliers typically provide Material Data Sheets (MDS) that detail the specific properties and characteristics of their powders, such as chemical composition, particle size distribution, apparent density, and flowability.
- Powder Grades: Metal powders for SEBM are available in various grades depending on the application requirements. Higher purity grades might be necessary for critical applications demanding exceptional mechanical properties.
- Powder Size Availability: The size of metal powders for SEBM typically ranges from 15 to 150 microns. The specific size chosen depends on the desired surface finish, packing density, and mechanical properties of the final part.
Suppliers and Pricing of SEBM Metal Powders
The availability and pricing of SEBM metal powders can vary depending on the specific material, powder grade, and order quantity. Here’s a general breakdown:
- Metal Powder Suppliers: Several companies specialize in supplying metal powders for additive manufacturing, including Höganäs AB, AP Powder Company, AMPO LLC, LPW Technology, and Sandvik Hyperion.
- Pricing: The cost of metal powders for SEBM can range from $50 to $500 per kilogram depending on the material, powder grade, and supplier. Generally, higher purity powders and exotic materials command a premium price.
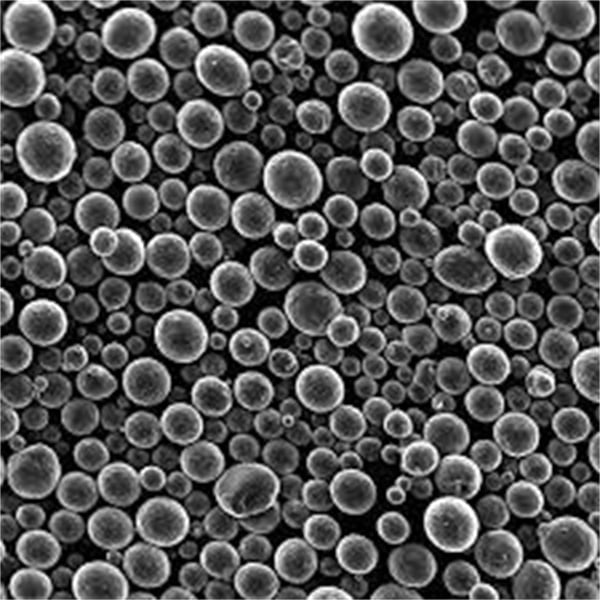
FAQ
Here are some frequently asked questions (FAQ) about Selective Electron Beam Melting (SEBM):
Question | Answer |
---|---|
What are the benefits of SEBM over other metal 3D printing technologies? | SEBM offers superior design freedom, exceptional material properties, high accuracy and precision, material efficiency, and freedom of material choice compared to some other metal 3D printing methods. |
What are the limitations of SEBM? | SEBM can be expensive due to machine and material costs, has limitations on build size, might require additional post-processing for surface finishes, needs support structures for some designs, and offers limited color options. |
What industries use SEBM? | SEBM is used in various industries, including aerospace, medical devices, automotive, energy, and tooling. |
What are some common metal powders used in SEBM? | Common metal powders for SEBM include titanium alloys, stainless steel, Inconel, nickel alloys, aluminum alloys, cobalt |
Share On
MET3DP Technology Co., LTD is a leading provider of additive manufacturing solutions headquartered in Qingdao, China. Our company specializes in 3D printing equipment and high-performance metal powders for industrial applications.
Inquiry to get best price and customized Solution for your business!
Related Articles
About Met3DP
Recent Update
Our Product
CONTACT US
Any questions? Send us message now! We’ll serve your request with a whole team after receiving your message.
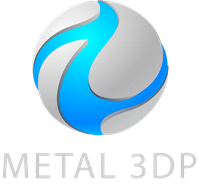
Metal Powders for 3D Printing and Additive Manufacturing
COMPANY
PRODUCT
cONTACT INFO
- Qingdao City, Shandong, China
- [email protected]
- [email protected]
- +86 19116340731