Which 3D printing devices are suitable for SLM
Table of Contents
Imagine conjuring complex metal objects from thin air, with intricate details and exceptional strength. That’s the magic of Selective Laser Melting (SLM) 3D printing, a revolution in metal additive manufacturing. But to unlock this potential, you need the right tool: a powerful 3D printer specifically designed for SLM.
This guide delves into the world of SLM 3D printers, equipping you with the knowledge to choose the perfect machine for your needs. We’ll explore leading brands, compare features, and unveil the factors that truly matter when selecting your SLM workhorse.
Understanding the Nuances of SLM Technology
Aspect | Description | Nuances to Consider |
---|---|---|
Acronym Ambiguity | SLM can stand for Selective Laser Melting, a 3D printing technology, or Service Level Management, a software development practice. | Context is crucial. In discussions about manufacturing, SLM likely refers to 3D printing. Within IT, Service Level Management (SLM) is more probable. |
SLM in 3D Printing | SLM uses a laser to selectively melt powdered material, building complex 3D objects layer-by-layer. | Material selection is a key nuance. Different materials respond uniquely to the laser, impacting printability and final part properties. Support structures, temporary frameworks within the printed object, require careful design to prevent warping or collapse. Surface finish can vary depending on laser power and scan strategy. |
Benefits of SLM 3D Printing | Enables creation of complex geometries, lightweight structures, and functional prototypes. | Ideal for low-volume, high-value applications like aerospace components, medical implants, and customized tooling. However, post-processing steps like machining and heat treatment might be needed, adding cost and complexity. |
Challenges of SLM 3D Printing | High cost of machines and materials. Requires specialized training for operators. Potential for part defects like porosity (air pockets) and residual stress. | Regular machine calibration and maintenance are essential. Powder handling requires careful procedures to minimize dust and ensure operator safety. Strict quality control protocols are necessary to ensure part integrity. |
SLM in Service Level Management | Focuses on defining, agreeing upon, and monitoring the performance of IT services. | Service Level Agreements (SLAs) are core to SLM. SLAs outline service expectations, including uptime, response times, and recovery procedures. Metrics used to track performance should be clearly defined and measurable. |
Benefits of SLM in IT | Improves communication and transparency between IT and business stakeholders. Helps ensure IT services meet business needs. Provides a framework for proactive problem identification and resolution. | SLAs need to be flexible enough to adapt to changing business requirements. Overly stringent SLAs can be expensive and impractical to maintain. Effective communication is crucial for managing expectations and resolving SLA breaches. |
Challenges of SLM in IT | Defining realistic and measurable service levels. Selecting appropriate monitoring tools and metrics. Enforcing SLAs and holding accountable parties responsible. | Regularly review and update SLAs to reflect evolving business needs. Invest in training for IT staff on SLM best practices. Establish clear escalation procedures for SLA breaches. |
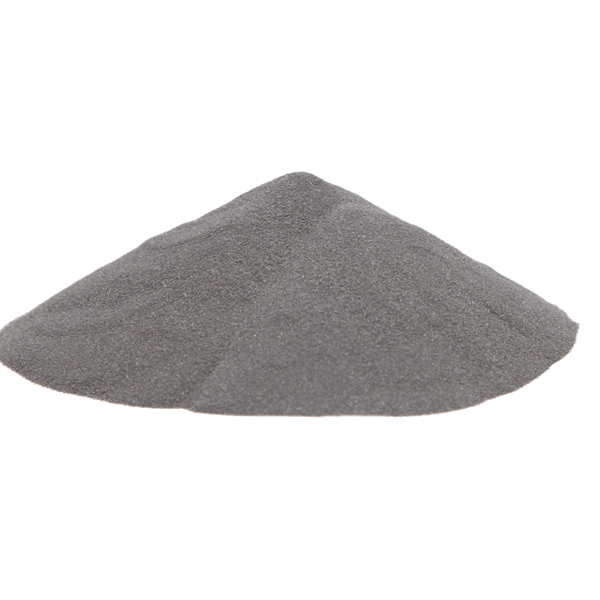
Choosing the Right SLM Printer
Factor | Description | Key Considerations |
---|---|---|
Application & Part Requirements | Identify the intended purpose of the printed parts. Are they complex, high-precision prototypes for aerospace or medical applications? Or are they larger, functional components for the automotive industry? | * Part Complexity & Detail: Printers with high-powered lasers and small spot sizes achieve finer features. * Dimensional Accuracy & Surface Finish: Higher resolution printing and advanced post-processing techniques improve these aspects. * Material Compatibility: Ensure the SLM printer works with the desired metals (e.g., titanium, aluminum, stainless steel). |
Build Volume & Throughput | Consider the size and quantity of parts you plan to print. | * Build Chamber Size: Small chambers suffice for intricate prototypes, while larger ones handle bigger functional parts. * Laser Count & Power: More lasers and higher power increase printing speed and throughput for production runs. * Layer Thickness & Scanning Speed: A balance is needed. Thinner layers provide better detail but take longer, while thicker layers print faster but may reduce resolution. |
Technology & Features | Different SLM technologies and features influence printing efficiency, precision, and cost. | * Single vs. Dual Laser Systems: Dual lasers improve speed and productivity for larger builds. * Recoat Systems: Blade or roller systems determine how fresh powder is spread for each layer, impacting quality and efficiency. * In-Process Monitoring & Control: Real-time monitoring allows for adjustments during printing, reducing errors and waste. * Powder Handling & Recycling: Closed-loop systems minimize powder waste and improve safety. |
Safety & Maintenance | SLM printers involve high-powered lasers and metal powders, requiring safety considerations and ongoing maintenance. | * Laser Safety Features: Enclosed build chambers and interlocks protect users from laser radiation. * Powder Handling Systems: Closed systems minimize operator exposure to metal dust. * Maintenance Requirements: Regular cleaning, filter changes, and calibration ensure optimal performance and part quality. |
Budget & ROI | SLM printers are significant investments. Evaluate the return on investment (ROI) based on your needs. | * Initial Machine Cost: Ranges widely depending on size, features, and brand. * Operational Costs: Consider material costs, energy consumption, and ongoing maintenance. * Return on Investment: Factor in time saved, production flexibility, and potential for new applications enabled by SLM. |
Vendor Reputation & Service | Choose a reputable vendor with a strong track record and reliable after-sales support. | * Manufacturer Reputation: Research the company’s experience and expertise in SLM technology. * Service & Support Network: Ensure access to qualified technicians and readily available spare parts. * Training & User Support: Training on safe operation and software usage is crucial. |
Top Contenders in the SLM Arena
Company | Core Technology | Applications | Strengths | Weaknesses |
---|---|---|---|---|
SLM Solutions (Germany) | Selective laser melting (SLM) | Aerospace, medical & dental, automotive | • Pioneered SLM technology • Established brand reputation • Extensive machine portfolio | • High machine costs • Limited open-source material compatibility |
EOS GmbH (Germany) | Laser sintering (LS) | Automotive, aerospace, medical | • High focus on R&D • Advanced process monitoring systems • Broad range of materials | • Higher layer thickness compared to SLM |
Renishaw plc (United Kingdom) | Selective laser melting (SLM) | Medical & dental, aerospace, consumer goods | • Strong presence in medical sector • In-house metal powder production • Advanced quality control systems | • Limited machine variety |
GE Additive (United States) | Electron beam melting (EBM) | Aerospace, medical, energy | • Expertise in metal AM for large parts • Access to GE’s material science portfolio • Open to collaborations | • EBM technology limited to reactive metals |
ExOne (United States) | Binder jetting (BJ) | Industrial, automotive, aerospace | • High-speed and affordable printing • Wide range of printable materials • Potential for mass customization | • Lower resolution compared to laser-based methods |
Desktop Metal (United States) | Single-pass jetting (SPJ) | Automotive, electronics, medical | • High-throughput printing technology • Potential for volume production • Compact and user-friendly machines | • Limited material selection currently |
Trumpf GmbH + Co. KG (Germany) | Laser metal fusion (LMF) | Aerospace, automotive, medical | • Leading manufacturer of industrial lasers • Expertise in laser process control • Strong industry partnerships | • Relatively new entrant in the SLM space |
Voxeljet AG (Germany) | High Speed Sintering (HSS) | Industrial tooling, automotive, design | • Fastest binder jetting technology • Excellent detail resolution for plastic parts • Potential for functional prototyping | • Limited to printing plastic materials |
Stratasys Ltd (Israel) | PolyJet | Medical, aerospace, design | • High-precision printing with multiple materials • Excellent biocompatibility for medical applications • Wide range of post-processing options | • Relatively high material costs |
HP Inc. (United States) | Multi Jet Fusion (MJF) | Industrial prototyping, functional parts | • High-throughput printing with excellent detail • Scalable technology for large parts • Potential for cost-effective production | • Limited material selection compared to other technologies |
4. Renishaw AM400: Precision Metal Manufacturing
Renishaw, a company known for its high-precision engineering solutions, offers the AM400 additive manufacturing system. This machine emphasizes exceptional detail and accuracy, making it ideal for applications requiring intricate metal parts.
Strengths:
- Unmatched Resolution: The AM400 boasts a minimum layer thickness of 20 microns, enabling the creation of highly detailed and complex geometries.
- Surface Finish: This system produces parts with a superior surface finish, minimizing the need for extensive post-processing.
- Multi-Laser Option: Some configurations offer a multi-laser option, significantly increasing build speeds for larger parts while maintaining exceptional detail.
Considerations:
- Build Volume: The AM400 has a relatively smaller build volume compared to some competitors, limiting the size of printable parts.
- Cost: Renishaw’s reputation for precision engineering comes at a premium price.
5. 3D Systems ProX DMP 320: The Multifunctional Powerhouse
3D Systems, a giant in the 3D printing industry, offers the ProX DMP 320 series. This platform combines versatility with high performance, catering to a wide range of applications.
Strengths:
- Multi-Material Compatibility: The ProX DMP 320 offers compatibility with a broad spectrum of metal powders, making it suitable for various projects.
- Advanced Features: This system boasts innovative features like Direct Metal Deposition (DMD) capabilities, allowing for the repair or addition of material to existing metal components.
- User-Friendly Interface: The ProX DMP 320 features a user-friendly interface and automated features, simplifying operation.
Considerations:
- Build Volume: The build volume of the ProX DMP 320 falls somewhere in the middle compared to other options.
- Cost: Expect a premium price tag associated with the versatility and advanced features of this machine.
Choosing the Right 3D Printer for Selective Laser Melting (SLM)
Factor | Description | Key Considerations |
---|---|---|
Build Volume | The maximum size of a part the printer can produce. | – Part size requirements: Consider the largest part you intend to print regularly. There’s always room for smaller parts within a larger build volume. – Future needs: If you anticipate printing larger parts in the future, factor in some growth potential. |
Laser System | The core technology that melts metal powder. | – Number of lasers: More lasers generally equate to faster printing speeds and potentially higher quality for complex geometries. – Laser power: Higher wattage lasers can melt thicker layers and a wider range of materials. – Spot size: The diameter of the laser beam. A smaller spot size offers finer detail but may be slower. |
Material Compatibility | The types of metal powder the printer can handle. | – Material needs: Match the printer’s capabilities to the metals you plan to use most often (e.g., titanium, stainless steel, nickel alloys). – Material switching capabilities: Some printers offer easy material changes, while others require a more complex process. |
Layer Thickness | The height of each layer of metal powder deposited. | – Part detail: A thinner layer thickness allows for finer features but can also increase printing time. – Material properties: Certain materials may require specific layer thicknesses for optimal results. |
Inert Gas Atmosphere | The controlled environment within the build chamber. | – Oxygen control: SLM requires an inert gas (usually argon or nitrogen) to prevent oxidation of the molten metal. – Gas flow and monitoring: A well-maintained gas system is crucial for consistent part quality. |
Software and Controls | The user interface and software that manage the printing process. | – Ease of use: The software should be intuitive for both experienced and novice users. – File preparation and slicing capabilities: Compatibility with your design software and offering features for optimizing print parameters. – Monitoring and control features: Real-time monitoring of printing progress and the ability to adjust parameters if necessary. |
Build Platform Handling | The system for positioning and recoating the metal powder bed. | – Accuracy and repeatability: The platform needs to move precisely to ensure consistent layer placement. – Powder handling: Efficient powder spreading and recoating mechanisms minimize waste and improve surface quality. |
Safety Features | Measures to protect users and the environment. | – Laser safety: Interlocks and enclosures to prevent accidental exposure to the laser beam. – Powder handling safety: Systems to minimize dust and potential explosions from fine metal particles. – Fume extraction: Equipment to remove harmful fumes generated during the printing process. |
Maintenance and Service | The ongoing care required to keep the printer functioning optimally. | – Manufacturer support: Readily available technical support and spare parts are essential. – Cleaning and calibration procedures: Easy-to-follow routines for maintaining print quality and machine longevity. – Filter replacement: Regular filter changes ensure proper air circulation and fume extraction. |
Cost | The initial investment and ongoing operational expenses. | – Budget constraints: SLM printers are expensive. Set a realistic budget and compare the upfront cost with features and capabilities. – Return on investment (ROI): Consider the potential cost savings and production benefits SLM can offer versus traditional manufacturing methods. |
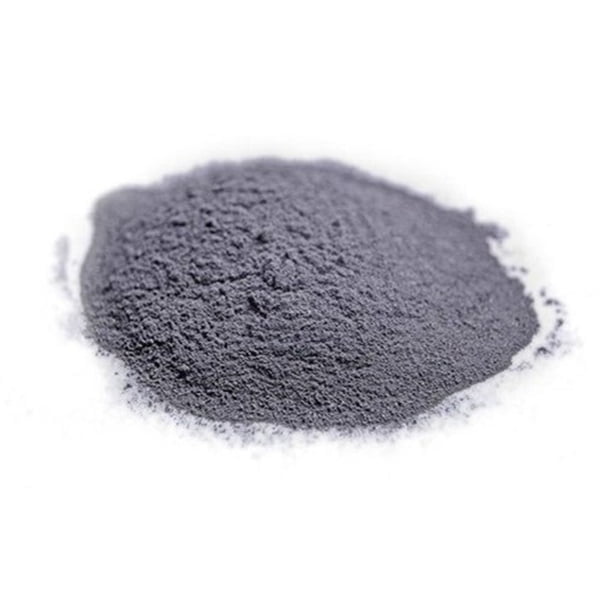
FAQ
Question | Answer |
---|---|
What are the benefits of using SLM 3D printing? | SLM offers several advantages, including the ability to create complex geometries, exceptional strength-to-weight ratios, design freedom for lightweight structures, and mass customization for unique metal parts. |
What are the limitations of SLM 3D printing? | SLM printers are expensive, have limitations in material compatibility, and require additional post-processing steps compared to some other 3D printing technologies. |
What factors should I consider when choosing an SLM 3D printer? | Consider the build volume you need, the laser power required for your desired materials, material compatibility, resolution and accuracy for your part details, ease of use, and overall cost (including upfront costs and ongoing maintenance). |
What are some alternative technologies to SLM? | Binder jetting additive manufacturing offers a cost-effective option for specific applications, particularly for large-scale metal parts. Other metal additive manufacturing methods like Electron Beam Melting (EBM) cater to specific material needs. |
Where can I find more information about SLM 3D printers? | Manufacturer websites offer detailed information about their SLM machines. |
Share On
MET3DP Technology Co., LTD is a leading provider of additive manufacturing solutions headquartered in Qingdao, China. Our company specializes in 3D printing equipment and high-performance metal powders for industrial applications.
Inquiry to get best price and customized Solution for your business!
Related Articles
About Met3DP
Recent Update
Our Product
CONTACT US
Any questions? Send us message now! We’ll serve your request with a whole team after receiving your message.
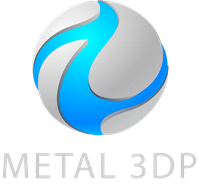
Metal Powders for 3D Printing and Additive Manufacturing