Spherical Aluminum Powder
Table of Contents
Spherical aluminum powder is a specialty aluminum powder with particles that are spherical in shape. This powder has several beneficial properties and applications compared to standard aluminum powders.
Overview of spherical aluminum powder
Spherical aluminum powder offers superior flowability, packing density, and other characteristics that make it well-suited to various industrial uses. Some key details:
- Made up of small aluminum particles in a spherical shape rather than irregular flakes
- Particle sizes typically range from 1 μm to 150 μm
- Produced through atomization process of molten aluminum
- Properties can be customized based on atomization parameters
- Used in explosives, pyrotechnics, welding, metal 3D printing, and more
Benefits: excellent flowability, higher bulk density, lower surface area, uniform particle size distribution, low porosity, reduced oxide content, controlled chemistry.
Drawbacks: more expensive than standard aluminum powders.
Types of spherical aluminum powder
There are a few key types of spherical aluminum powder categorized by production method and properties:
Type | Description |
Atomized | Made by inert gas or water atomization; most common type with tight distribution. Used for explosive sensitivity reduction, improved powder flow and packing. |
Spheroidized | Irregular aluminum powder transformed into spheres using processes like hot isostatic pressing. Lower cost but wider distribution. |
Plasma Atomized | Produced using plasma instead of gas/water. Very small, uniform powder down to 1 μm for advanced applications. |
Aluminum Shot | Low porosity and precise diameters. Used for blasting/surface profiling. Typically larger than powders. |
These various spherical aluminum powder types have specific composition, sizes, production methods and applications they are most suitable for.
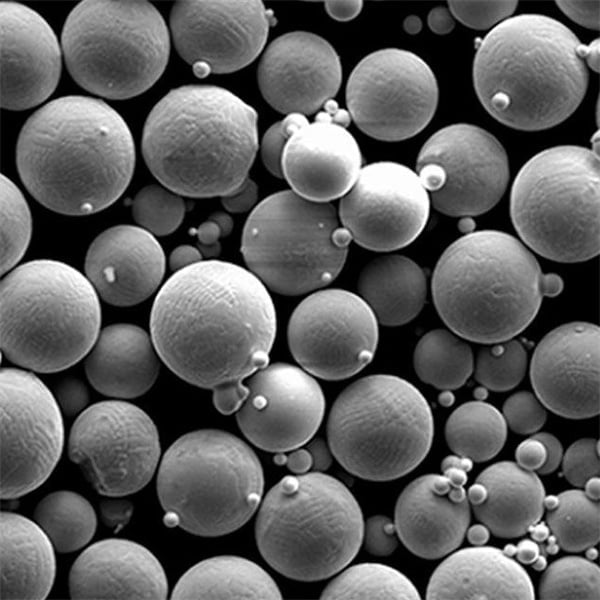
Composition of spherical aluminum powder
Spherical aluminum powder can be composed of pure aluminum or various aluminum alloys customized to impart particular properties. Some examples:
Type | Alloying Elements | Characteristics |
Pure Al | – | Soft, lower strength; easily formed and welded. |
6061 | Mg, Si | Medium strength; moderate corrosion resistance. |
7075 | Zn, Mg, Cu | High strength; often used for aerospace applications. |
Specific impurity limits in chemistry and tight particle distributions are maintained to achieve reliable performance. Custom alloys are possible for specialized mechanical, thermal, or chemical properties.
Properties of spherical aluminum powder
Property | Description | Benefit in Additive Manufacturing & Other Applications |
---|---|---|
High Flowability | Spherical aluminum powder particles move freely with minimal friction due to their smooth, rounded shape. This allows for even distribution within a hopper or feeder system, critical for consistent material deposition in Additive Manufacturing (AM) processes like Selective Laser Melting (SLM) or Electron Beam Melting (EBM). In traditional techniques like pyrotechnics or metal injection molding (MIM), good flowability ensures uniform packing during mold filling, leading to predictable product quality. | * Consistent Layer Formation in AM: Even powder flow enables precise material placement during each layer in AM, resulting in accurate part geometries and minimized defects. * Reduced Segregation: Spherical particles are less prone to segregation, where larger or denser particles settle out during transport. This maintains a homogeneous powder mixture for consistent material properties throughout the build. * Improved Efficiency: High flowability allows for faster powder dispensing and minimizes waste, leading to efficient production processes. |
High Packing Density | Spherical particles pack together more efficiently than irregularly shaped powders. This translates to a higher density of aluminum particles per unit volume, maximizing material utilization in AM and achieving a denser final product. | * Stronger Parts in AM: Higher packing density in the powder bed allows for a greater amount of aluminum to be melted during AM, leading to parts with enhanced mechanical strength and improved load-bearing capabilities. * Reduced Porosity: Dense packing minimizes voids or air gaps within the powder bed, resulting in a more compact final product with less porosity. This translates to better structural integrity, corrosion resistance, and overall performance. * Material Optimization: High packing density allows manufacturers to use less powder to achieve the desired final part density, leading to material cost savings. |
Uniform Particle Size Distribution | Spherical aluminum powder is typically produced with a narrow range of particle sizes. This consistency ensures predictable material behavior during processing. | * Improved Process Control: Consistent particle size allows for optimized laser or electron beam parameters in AM, leading to more uniform melting and better control over the final microstructure of the part. * Reduced Surface Area: A narrower particle size distribution minimizes the overall surface area of the powder, leading to potentially lower oxidation rates during storage and improved flow characteristics. * Minimized Segregation: Similar-sized particles are less prone to segregation within the powder bed, ensuring consistent material properties throughout the build. |
Low Surface Area | Compared to irregular powders with a high surface area, spherical aluminum powder has a smaller total surface area per unit volume. This characteristic offers advantages in various applications. | * Reduced Oxidation: A lower surface area minimizes the exposure of aluminum particles to oxygen, leading to less oxidation during storage and handling. This helps maintain powder quality and material properties. * Improved Flowability: Lower surface area contributes to smoother interactions between particles, enhancing flowability and enabling efficient powder handling. * Enhanced Thermal Conductivity: The spherical shape minimizes internal resistance to heat flow, potentially leading to improved thermal conductivity in the final product. |
Tailored Properties | Spherical aluminum powder can be produced with various alloying elements to achieve specific properties for different applications. | * Broad Range of Applications: By incorporating specific elements like silicon (Si), magnesium (Mg), or copper (Cu), manufacturers can tailor the powder’s properties like strength, ductility, or electrical conductivity to suit diverse AM and industrial needs. * Functional Parts: Alloyed spherical aluminum powder allows for the creation of functional parts in AM with properties exceeding those of pure aluminum, opening doors for advanced applications. * Lightweight Performance: Aluminum alloys maintain the inherent lightness of aluminum while offering enhanced mechanical properties, making them ideal for weight-critical applications in aerospace, automotive, and other industries. |
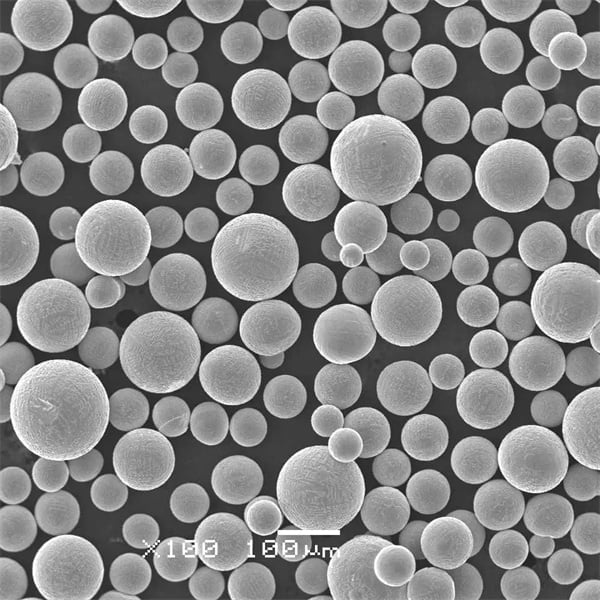
Characteristics of spherical aluminum powder
In order to function optimally in applications, spherical aluminum powders have strict standards for characteristics like:
Characteristic | Typical Range |
Particle shape | Spherical; Minimal satellites |
Particle size | 1 – 150 μm |
Size distribution | D10: D50 ratio > 0.7 |
Oxide content | < 3.0% by weight |
Apparent density | 0.85 – 2.0 g/cm3 |
Tap density | > 75% solid density |
Hausner ratio | 1.25 maximum |
Flow rate | 25-35 sec, 50g sample |
Maintaining this consistency allows reliable and repeatable performance. Specifications can be customized based on application requirements.
Applications of spherical aluminum powder
Application | Description | Advantages of Spherical Aluminum Powder | Industries |
---|---|---|---|
Additive Manufacturing (3D Printing) | Spherical aluminum powder is a key material in 3D printing processes like Selective Laser Melting (SLM) and Powder Bed Fusion. These techniques use lasers to selectively melt layers of powder, building complex, near-net shape components. | * Flowability: Spherical particles flow freely, enabling smooth and consistent deposition during the printing process. * Packing Density: Spherical shapes pack tightly, minimizing voids and creating strong, dense final parts. * Laser Absorption: The smooth surface of spheres reflects less laser energy, leading to more efficient melting and improved material properties. * Surface Finish: Spherical aluminum powder results in smoother surface finishes on printed parts, reducing the need for post-processing. | Aerospace, Automotive, Medical, Dental |
Metal Injection Molding (MIM) | MIM is a manufacturing technique that combines metal powder with a binder to create a feedstock that can be injection molded. The binder is then removed through a debinding process, leaving a near-finished metal part. Spherical aluminum powder is well-suited for MIM due to its: * Flowability: Similar to 3D printing, good flowability is crucial for even distribution in the mold cavity. * Packing Density: High packing density leads to parts with minimal shrinkage and good dimensional accuracy. * Sinterability: Spherical particles promote better sintering (bonding) during the debinding process, resulting in stronger parts. | * Complex Geometries: MIM allows for the production of intricate metal parts with high precision. * Mass Production: MIM is suitable for high-volume production of consistent parts. * Material Variety: Spherical aluminum powder can be combined with various alloying elements to achieve specific properties. | Consumer Electronics, Automotive, Medical Devices, Firearms |
Thermal Spraying | Thermal spraying involves melting metal powder and propelling it at high velocity towards a substrate. The molten particles impact and adhere to the surface, creating a coating that can improve properties like wear resistance, corrosion resistance, and thermal conductivity. Spherical aluminum powder offers advantages in thermal spraying, including: * Splat Morphology: Spherical particles flatten into splats with a larger contact area, enhancing adhesion to the substrate. * Reduced Rebound: Due to their shape, spherical particles experience less rebound compared to irregular shapes, leading to higher deposition efficiency. * Controllable Coating Properties: Particle size and distribution can be precisely controlled to achieve desired coating characteristics. | * Refurbishment: Thermal spraying can restore worn or damaged components, extending their service life. * Functional Coatings: Aluminum coatings can improve heat dissipation, electrical conductivity, and reflectivity. * Lightweighting: Aluminum offers a lightweight alternative to heavier materials used in thermal spraying. | Aerospace, Automotive, Power Generation, Oil & Gas |
Pyrotechnics | Spherical aluminum powder is a fuel source in some pyrotechnic compositions. Its advantages include: * High Burning Rate: The spherical shape promotes efficient and uniform burning, leading to brighter and more predictable pyrotechnic effects. * Controllable Particle Size: Particle size can be tailored to influence the burning rate and color effects in the pyrotechnic display. * Safety: Spherical aluminum powder can be safer to handle compared to irregularly shaped aluminum powders due to reduced dust generation. | Fireworks Manufacturing |
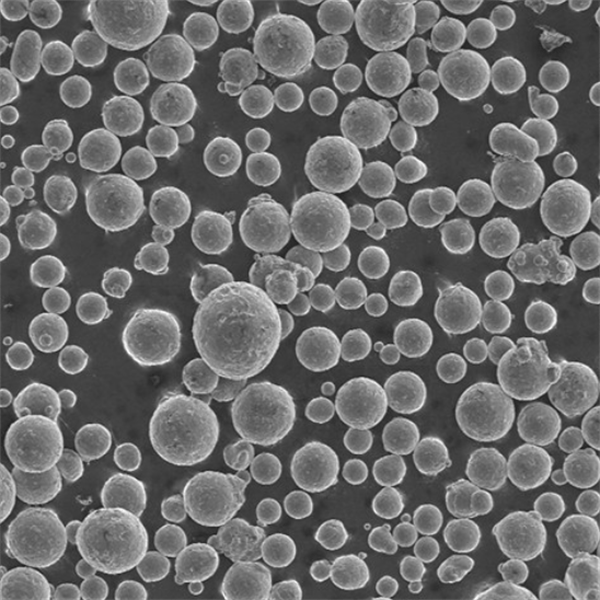
Specifications of spherical aluminum powder
Spherical aluminum powder is available under various standard designations and specifications per industry, process requirements and final applications:
Standard | Grades | Particle Size | Common Applications |
ASTM B801 | Atomized Aluminum; Grade A | 10-150 μm | Thermal spray coatings; printing wires |
AMS 4376 | Class 1A; Class 3 | 10-53 μm; 38-106 μm | Solid rocket propellants; explosives |
AMS 4377 | Class 1-3 | 5-15 μm | Pyrotechnics; ignition mixes |
Alcan MD-202 | MD-202SD; MD-202HD | 20-180 μm | Thermal spray powders |
Labels clearly identify relevant grade, size range, lot number, date of manufacture and other details.
spherical aluminum powder Suppliers
Some leading global suppliers of spherical aluminum powder include:
Company | Location |
Atlantic Equipment Engineers | Bergen, NJ; USA |
Luxfer Magtech | Manchester; UK |
Nippon Atomized Metal Powders Corp | Japan |
Hoganas | Sweden |
Makin Metal Powders | UK |
Supply chain logistics, minimum order quantity (MOQ), and pricing varies among suppliers based on geographic region, production capacity, customization options, and other factors.
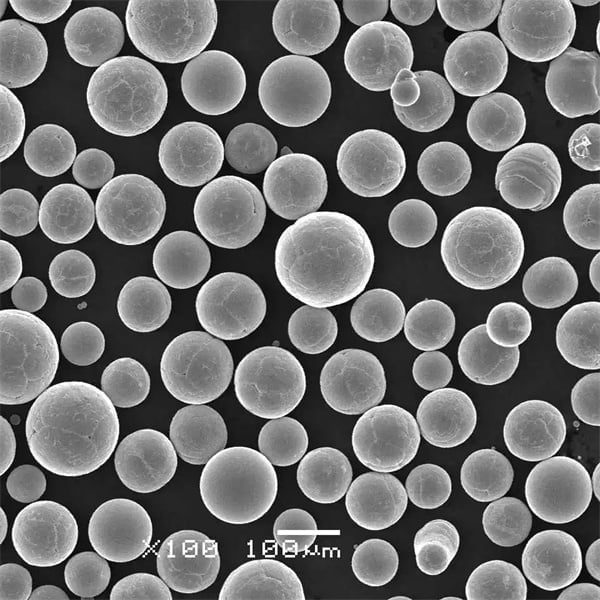
spherical aluminum powder Pricing
Factor | Description | Impact on Price | Example |
---|---|---|---|
Purity | The percentage of aluminum metal present in the powder. Higher purity grades are more expensive. | Directly proportional | – 99.5% pure spherical aluminum powder: Lower cost. – 99.9+% pure spherical aluminum powder: Higher cost. |
Particle Size | The diameter of the individual spherical particles. Finer powders are generally more expensive. | Directly proportional | – 10-45 microns: More affordable, commonly used in pyrotechnics and metal injection molding. – 1-3 microns: More expensive, used in 3D printing and high-performance coatings. |
Surface Area | Relates to particle size. Finer powders have a larger total surface area, potentially increasing cost due to processing requirements. | Directly proportional | – Larger surface area powders may require additional treatment to prevent agglomeration (clumping), impacting price. |
Sphericity | How perfectly spherical the particles are. A more spherical shape is generally more desirable and expensive. | Directly proportional | – Highly spherical particles flow more easily, pack more densely, and offer superior performance in some applications, leading to a higher price. |
Quantity | The amount of spherical aluminum powder purchased. Bulk purchases typically offer a lower price per unit weight. | Indirectly proportional | – Smaller quantities (grams or kilograms) are typically more expensive per unit weight than larger quantities (tonnes). |
Manufacturer | The reputation and production methods of the supplier can influence price. | Varies | – Reputable manufacturers with high-quality control processes may charge more than lesser-known suppliers. – Manufacturers using specialized atomization techniques to achieve specific particle size or sphericity may have a price premium. |
Demand & Availability | Market forces of supply and demand can affect price. | Varies | – Periods of high demand or limited supply can drive prices up. – Conversely, excess supply may lead to lower prices. |
Pros vs Cons of spherical aluminum powder
Feature | Pros | Cons |
---|---|---|
Flowability | Spherical aluminum powder excels in flowability due to its smooth, round particles. This allows for easier and more consistent movement within processing equipment, reducing issues like segregation and jamming. Improved flowability translates to faster production times, better packing in molds, and ultimately, more uniform finished products. | While superior to irregular powders, spherical aluminum powder may still exhibit some limitations in flowability, particularly for very fine particle sizes. Additionally, factors like moisture content and surface oxidation can slightly hinder flow characteristics. |
Packing Density | The spherical shape of the powder particles enables them to pack together more tightly, resulting in higher packing density compared to irregular powders. This translates to a greater amount of aluminum powder being packed into a specific volume, leading to components with higher density and improved mechanical properties. | Spherical aluminum powder may have a slightly lower apparent density compared to irregular shapes due to the presence of air gaps between the spheres. However, this is often outweighed by the benefits of higher packing efficiency. |
Uniform Melting & Densification | The consistent size and shape of spherical aluminum powder contribute to more uniform melting behavior during sintering or additive manufacturing processes. This allows for better control over the final microstructure of the component, minimizing internal defects and promoting a more even distribution of porosity. | While offering advantages, spherical aluminum powder might require slightly adjusted processing parameters compared to irregular powders to achieve optimal results. This highlights the importance of tailoring the manufacturing process to the specific powder characteristics. |
Porosity & Mechanical Properties | The improved packing density and uniform melting behavior of spherical aluminum powder lead to reduced porosity within the final product. This translates to improved mechanical properties like tensile strength, fatigue resistance, and ductility. Components with less porosity are generally stronger, more durable, and less prone to cracking or failure. | The presence of even minimal residual porosity, though significantly reduced compared to irregular powders, can still have an impact on the overall mechanical properties. Careful selection of processing parameters and potential post-processing techniques can further minimize porosity. |
Surface Finish | Due to the smooth, spherical nature of the powder particles, components fabricated using spherical aluminum powder often exhibit a superior surface finish. This reduces the need for extensive post-processing steps like grinding or polishing, leading to improved aesthetics and potentially enhanced functional performance in tribological applications. | The surface finish achievable with spherical aluminum powder can be influenced by factors like particle size distribution and the chosen manufacturing process. However, compared to irregular powders, a smoother surface finish is generally a notable advantage. |
Production Cost | Spherical aluminum powder production methods like gas or water atomization tend to be more complex and energy-intensive compared to simpler techniques used for irregular powders. This translates to a higher cost for the spherical powder itself. | The increased cost of spherical aluminum powder needs to be weighed against the benefits it offers in terms of improved product quality, processing efficiency, and potentially reduced waste due to lower rejection rates. |
Particle Size Range | While spherical aluminum powder is available in a wide range of particle sizes, there may be limitations compared to irregular powders. Producing very fine spherical particles can be more challenging and expensive. | The selection of the optimal particle size for a specific application is crucial. While a wider range with finer options might be desirable, the available options for spherical aluminum powder are still quite comprehensive for most applications. |
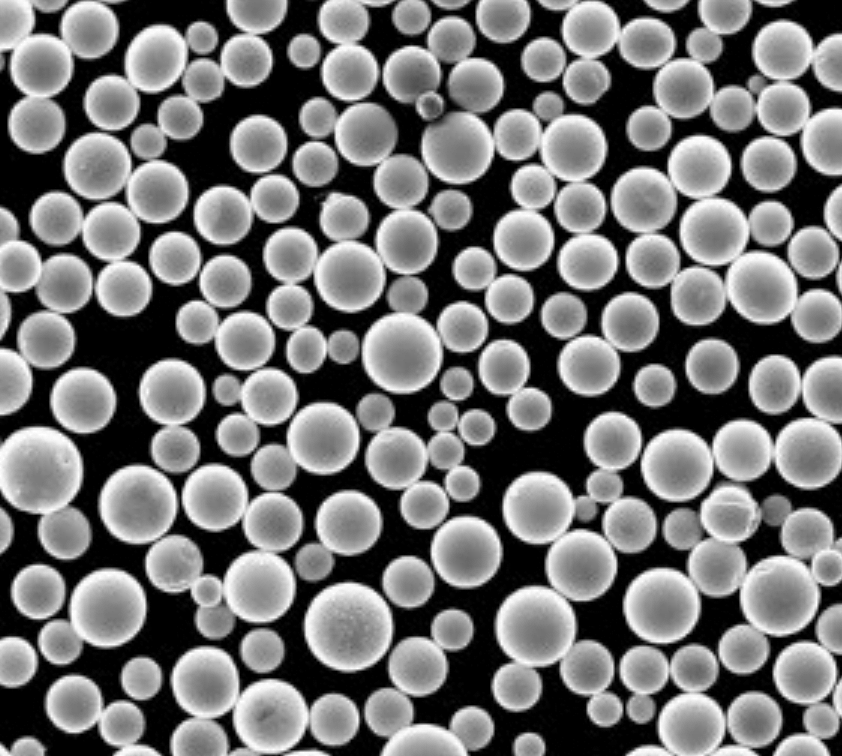
FAQs
Q: What is the difference between spherical and atomized aluminum powder?
A: Atomized aluminum powder can have slightly irregular shapes though the particle size distribution is still tightly controlled. Spherical aluminum powder particles have a precise spherical shape made through specialized atomization processes.
Q: Is spherical aluminum powder dangerous or hazardous?
A: Some types may be pyrophoric, requiring special handling in inert atmospheres. Otherwise it is generally safe, with health hazards similar to other aluminum powders requiring masks to prevent inhalation. Always check SDS.
Q: What is the typical bulk density of spherical aluminum powder?
A: Bulk densities range between 0.4-1.2 g/cm3 depending on exact composition and powder characteristics. Values exceeding 1 g/cm3 are common for manyspherical aluminum powder specifications.
Q: How do I choose the right size spherical aluminum powder?
A: Consider factors like: manufacturing method constraints, density requirements, surface finishing needs, reactivity, final part properties and alloy options available. Discussing application details with suppliers gives the best recommendation.
Q: Can these spherical powders be used in food/medical applications?
A: Spherical aluminum is generally not used in food or medical applications itself, though aluminum alloys conforming to strict standards regarding impurities and processing may be tailored for select scenarios requiring non-toxicity. Special compliance considerations would be required.
Conclusion
Spherical aluminum powder provides superior powder flow behavior, density, reactivity control, surface finish and other properties compared to standard aluminum powders. Customization through specialized atomization processes allows tailoring to demanding applications across aerospace, defense, additive manufacturing and advanced ceramics industries. Partnering with expert suppliers enables dialing in the right specifications. Despite higher costs, the enhanced consistency and component performance demonstrates excellent value for critical applications. Ongoing developments focus on improved size distributions, lower oxide content and better control of alloying additions.
Share On
MET3DP Technology Co., LTD is a leading provider of additive manufacturing solutions headquartered in Qingdao, China. Our company specializes in 3D printing equipment and high-performance metal powders for industrial applications.
Inquiry to get best price and customized Solution for your business!
Related Articles
About Met3DP
Recent Update
Our Product
CONTACT US
Any questions? Send us message now! We’ll serve your request with a whole team after receiving your message.
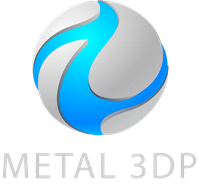
Metal Powders for 3D Printing and Additive Manufacturing
COMPANY
PRODUCT
cONTACT INFO
- Qingdao City, Shandong, China
- [email protected]
- [email protected]
- +86 19116340731