Spherical Gas Atomized Alloy Powder
Table of Contents
Spherical gas atomized alloy powders are an integral part of many modern industrial processes. These powders, with their unique properties, find applications in various fields, from aerospace to biomedical engineering. In this comprehensive guide, we will dive into the specifics of these powders, including types, compositions, properties, applications, and much more.
Overview of Spherical Gas Atomized Alloy Powder
Spherical gas atomized alloy powder is produced by atomizing molten metal with high-pressure gas, resulting in spherical particles. This process ensures high purity, consistent particle size distribution, and excellent flowability, making these powders ideal for additive manufacturing, thermal spraying, and other high-performance applications.
Key Features of Spherical Gas Atomized Alloy Powder
- High Purity: The atomization process reduces contamination, ensuring high-purity powders.
- Spherical Shape: Enhances flowability and packing density.
- Controlled Particle Size: Allows for precise application requirements.
- Excellent Mechanical Properties: Suitable for demanding applications like aerospace and medical implants.
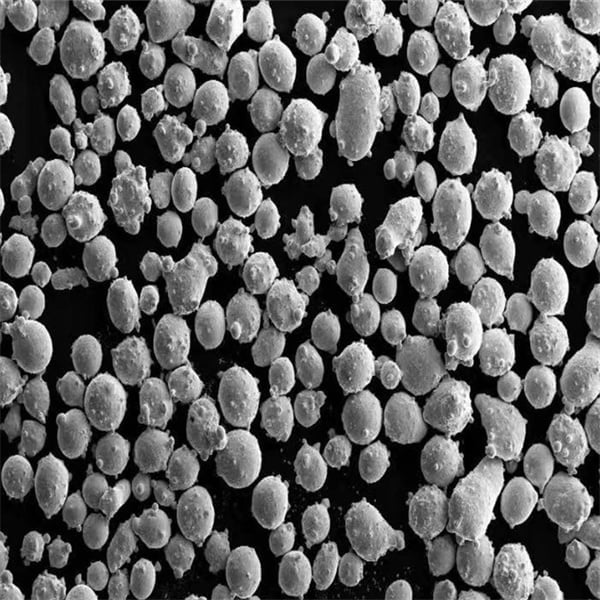
Types and Compositions of Spherical Gas Atomized Alloy Powder
Below is a detailed table of different types of spherical gas atomized alloy powders, their compositions, and properties.
Powder Type | Composition | Properties | Applications |
---|---|---|---|
Inconel 718 | Ni-Cr-Fe | High strength, corrosion resistance | Aerospace, power generation |
316L Stainless Steel | Fe-Cr-Ni-Mo | Corrosion resistance, high strength | Biomedical, food processing |
Ti-6Al-4V | Ti-Al-V | Lightweight, high strength | Aerospace, medical implants |
Cobalt-Chromium Alloy | Co-Cr | Wear resistance, biocompatibility | Dental implants, orthopedic devices |
AlSi10Mg | Al-Si-Mg | Lightweight, good thermal properties | Automotive, aerospace |
Maraging Steel | Fe-Ni-Co-Mo-Ti | Ultra-high strength, toughness | Tooling, high-performance parts |
Hastelloy X | Ni-Cr-Mo-Fe | Oxidation resistance, high temperature strength | Gas turbines, chemical processing |
Copper Alloy | Cu-Ni-Sn | Electrical conductivity, corrosion resistance | Electronics, marine applications |
Nickel Alloy 625 | Ni-Cr-Mo | High corrosion resistance, toughness | Marine, chemical industries |
Tool Steel H13 | Fe-Cr-Mo-V | High toughness, wear resistance | Tooling, die casting |
Applications of Spherical Gas Atomized Alloy Powder
Spherical gas atomized alloy powders are utilized in numerous fields due to their versatile properties. Here’s a look at some common applications:
Application | Powder Type | Details |
---|---|---|
Aerospace | Inconel 718, Ti-6Al-4V | Components like turbine blades, structural parts |
Biomedical | 316L Stainless Steel, Cobalt-Chromium Alloy | Implants, surgical instruments |
Automotive | AlSi10Mg, Maraging Steel | Lightweight components, high-strength parts |
Electronics | Copper Alloy | Conductive materials, connectors |
Tooling | Tool Steel H13, Maraging Steel | Molds, dies, high-performance tools |
Advantages of Spherical Gas Atomized Alloy Powder
- Uniformity: Spherical particles ensure uniform packing and density.
- Flowability: Smooth flow characteristics make it ideal for additive manufacturing and powder metallurgy.
- Purity: Reduced contamination leads to superior material properties.
- Customization: Particle size and composition can be tailored to specific requirements.
Disadvantages of Spherical Gas Atomized Alloy Powder
- Cost: Higher production costs compared to other powder types.
- Complexity: Requires specialized equipment and expertise.
- Availability: Not all compositions are readily available.
Specifications, Sizes, and Standards
Understanding the specifications, sizes, and standards is crucial for selecting the right powder for your application. Below is a table summarizing these aspects for some common powders:
Powder Type | Particle Size Range (µm) | Standards | Typical Uses |
---|---|---|---|
Inconel 718 | 15-45, 45-105 | ASTM B637 | Aerospace components |
316L Stainless Steel | 15-45, 45-105 | ASTM F138 | Medical implants |
Ti-6Al-4V | 20-63, 45-105 | ASTM F2924 | Aerospace, medical |
Cobalt-Chromium Alloy | 15-45, 45-105 | ASTM F75 | Biomedical devices |
AlSi10Mg | 20-63, 45-105 | EN 1706 | Automotive parts |
Maraging Steel | 15-45, 45-105 | ASTM A579 | High-strength tools |
Hastelloy X | 15-45, 45-105 | ASTM B572 | High-temperature components |
Copper Alloy | 15-45, 45-105 | ASTM B505 | Electronics |
Nickel Alloy 625 | 15-45, 45-105 | ASTM B446 | Corrosive environments |
Tool Steel H13 | 15-45, 45-105 | ASTM A681 | Tooling applications |
Suppliers and Pricing Details
Here is a list of some suppliers and the typical pricing for these powders:
Supplier | Powder Type | Price per kg (USD) | Notes |
---|---|---|---|
Höganäs | 316L Stainless Steel | $50-$70 | Bulk discounts available |
Carpenter Technology | Ti-6Al-4V | $150-$200 | Custom particle sizes |
Praxair Surface Technologies | Inconel 718 | $80-$120 | High purity grades |
Kennametal | Cobalt-Chromium Alloy | $200-$250 | Medical grade |
LPW Technology | AlSi10Mg | $40-$60 | Consistent quality |
Sandvik | Maraging Steel | $90-$130 | High performance |
AMETEK | Hastelloy X | $100-$150 | Various grades available |
GKN Hoeganaes | Copper Alloy | $30-$50 | Electrical applications |
Arcam AB | Nickel Alloy 625 | $100-$140 | Aerospace grade |
QuesTek Innovations | Tool Steel H13 | $70-$100 | Tooling applications |
Comparing Pros and Cons of Different Powders
Choosing the right powder depends on understanding the pros and cons of each option. Here’s a comparative look:
Powder Type | Advantages | Disadvantages |
---|---|---|
Inconel 718 | High strength, corrosion resistance | High cost |
316L Stainless Steel | Corrosion resistance, biocompatibility | Moderate strength |
Ti-6Al-4V | Lightweight, high strength | Expensive |
Cobalt-Chromium Alloy | Biocompatibility, wear resistance | High cost |
AlSi10Mg | Lightweight, good thermal properties | Lower strength |
Maraging Steel | Ultra-high strength, toughness | Expensive, limited availability |
Hastelloy X | High temperature strength, oxidation resistance | High cost |
Copper Alloy | Electrical conductivity, corrosion resistance | Lower mechanical strength |
Nickel Alloy 625 | Corrosion resistance, toughness | High cost |
Tool Steel H13 | High toughness, wear resistance | Moderate cost |
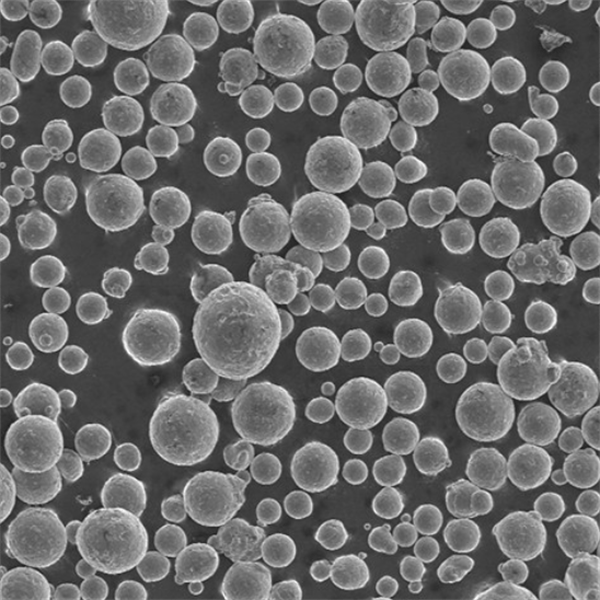
FAQ
What is spherical gas atomized alloy powder?
Spherical gas atomized alloy powder is a type of metal powder created by atomizing molten metal with high-pressure gas, resulting in spherical particles with high purity, consistent size, and excellent flowability.
What are the common applications of these powders?
These powders are used in aerospace, biomedical implants, automotive parts, electronics, tooling, and high-performance industrial components.
Why choose spherical gas atomized powders over other types?
Their uniform shape, high purity, and excellent flowability make them ideal for precise manufacturing processes like additive manufacturing and powder metallurgy.
How are these powders priced?
Pricing varies by composition and supplier, typically ranging from $30 to $250 per kilogram depending on the material and grade.
What are the limitations of using spherical gas atomized powders?
They are generally more expensive to produce and require specialized equipment and expertise. Availability can also be an issue for some specific compositions.
Can particle size be customized?
Yes, particle size can be tailored to meet specific application requirements, which is one of the advantages of using spherical gas atomized powders.
How does the production process ensure high purity?
The atomization process minimizes contamination by using high-pressure gas, which helps to create powders with fewer impurities compared to other methods.
Which industries benefit the most from these powders?
Aerospace and biomedical industries benefit significantly due to the stringent material performance requirements that these powders can meet.
Share On
MET3DP Technology Co., LTD is a leading provider of additive manufacturing solutions headquartered in Qingdao, China. Our company specializes in 3D printing equipment and high-performance metal powders for industrial applications.
Inquiry to get best price and customized Solution for your business!
Related Articles
About Met3DP
Recent Update
Our Product
CONTACT US
Any questions? Send us message now! We’ll serve your request with a whole team after receiving your message.
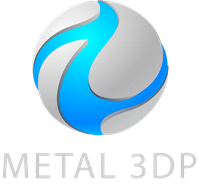
Metal Powders for 3D Printing and Additive Manufacturing