Spherical Powder
Table of Contents
Overview
Spherical powder, also known as spherical metal powder, is a type of finely granulated material characterized by its spherical shape. These powders are essential in various industrial applications, including additive manufacturing, coatings, and metal injection molding. The uniform shape of the particles ensures high packing density and flowability, making them ideal for precision applications.
In this article, we’ll delve into the specifics of spherical powder, exploring different models, compositions, properties, and uses. We’ll also compare various options, discuss their advantages and limitations, and provide insights into suppliers and pricing.
What is Spherical Powder?
Spherical powders are metallic powders composed of tiny, uniform spherical particles. The shape of these particles significantly enhances the material’s properties, such as flowability and packing density, which are crucial for applications like 3D printing and coatings.
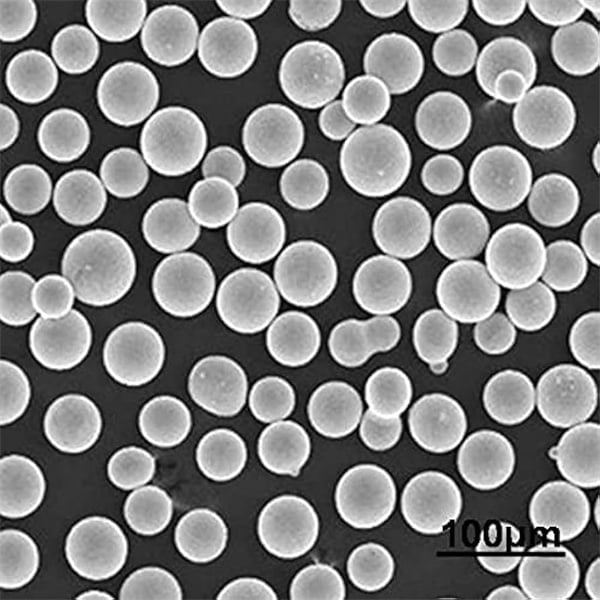
Types of Spherical Powder
Here’s a detailed look at some of the most common types of spherical metal powders:
Type | Composition | Properties | Characteristics |
---|---|---|---|
Spherical Titanium Powder (Ti-6Al-4V) | Titanium alloyed with 6% Aluminum, 4% Vanadium | High strength, lightweight, corrosion resistance | Ideal for aerospace and biomedical applications |
Spherical Aluminum Powder (AlSi10Mg) | Aluminum alloyed with Silicon and Magnesium | Good thermal properties, lightweight | Used in automotive and aerospace sectors |
Spherical Stainless Steel Powder (316L) | Iron, Chromium, Nickel, Molybdenum | High corrosion resistance, good mechanical properties | Common in medical and food industries |
Spherical Copper Powder (Cu-OFHC) | Pure Copper | Excellent electrical and thermal conductivity | Used in electronics and conductive inks |
Spherical Nickel Alloy Powder (Inconel 718) | Nickel, Chromium, Iron, Molybdenum, Niobium | High temperature resistance, corrosion resistance | Suitable for aerospace and gas turbines |
Spherical Cobalt-Chrome Powder (CoCrMo) | Cobalt, Chromium, Molybdenum | High wear resistance, biocompatibility | Widely used in medical implants |
Spherical Iron Powder (Fe) | Pure Iron | Good magnetic properties, ductility | Used in powder metallurgy and magnetic applications |
Spherical Tungsten Powder (W) | Pure Tungsten | High density, high melting point | Utilized in radiation shielding and heavy metal alloys |
Spherical Molybdenum Powder (Mo) | Pure Molybdenum | High strength at high temperatures | Used in high-temperature applications and electronics |
Spherical Zinc Powder (Zn) | Pure Zinc | Good corrosion resistance, sacrificial anode | Common in galvanization and battery applications |
Applications of Spherical Powder
Spherical powders find use in a wide array of industries due to their unique properties. Here’s a table that shows where these powders are commonly applied:
Application | Industry | Specific Use |
---|---|---|
Additive Manufacturing (3D Printing) | Aerospace, Medical, Automotive | Fabrication of complex geometries, prototyping |
Metal Injection Molding (MIM) | Medical, Consumer Goods | Production of small, intricate parts |
Coatings | Aerospace, Automotive, Electronics | Thermal barrier coatings, conductive coatings |
Powder Metallurgy | Automotive, Industrial | Manufacturing of high-performance parts |
Electronics | Electronics Manufacturing | Production of conductive inks, components |
Battery Production | Energy Storage | Fabrication of electrodes, battery components |
Catalysts | Chemical Processing | Used in catalytic converters, industrial catalysts |
Sintering | Industrial Manufacturing | Fabrication of dense, durable parts |
Thermal Spraying | Aerospace, Industrial | Surface enhancement and protection |
Filtration | Water Treatment, Air Purification | Fabrication of porous filters |
Specifications, Sizes, Grades, and Standards
The specifications and standards for spherical powders vary depending on the application and material. Below is a table outlining these aspects:
Material | Size Range (µm) | Grade | Standards |
---|---|---|---|
Ti-6Al-4V | 15-45, 45-75 | Grade 23, Grade 5 | ASTM F2924, ISO 5832-3 |
AlSi10Mg | 20-63 | Grade 1 | EN AC-43000 |
316L Stainless Steel | 15-45, 45-100 | Grade 316L | ASTM F138, ISO 5832-1 |
Cu-OFHC | 10-45 | Grade 1 | ASTM F68 |
Inconel 718 | 15-53 | Grade 718 | AMS 5662, ASTM B637 |
CoCrMo | 15-45 | F75, F1537 | ASTM F75, ISO 5832-4 |
Iron | 20-150 | High Purity | ASTM A131 |
Tungsten | 5-45 | High Purity | ASTM B777, AMS 7725 |
Molybdenum | 10-45 | High Purity | ASTM B387 |
Zinc | 20-150 | High Purity | ASTM B6 |
Advantages of Spherical Powder
Spherical powders offer several advantages over irregular-shaped powders, making them preferred for many high-precision applications.
High Flowability
Due to their uniform shape, spherical powders exhibit superior flowability, which is crucial for processes like 3D printing and metal injection molding.
High Packing Density
The spherical shape allows for a higher packing density compared to irregular powders, which improves the mechanical properties of the finished products.
Uniformity and Consistency
Spherical powders ensure a more consistent and uniform layer application, which is essential for producing high-quality parts with intricate details.
Reduced Porosity
Parts manufactured using spherical powders generally have reduced porosity, enhancing their mechanical strength and durability.
Improved Thermal Conductivity
For materials like copper and aluminum, the spherical shape enhances thermal conductivity, making them ideal for applications in electronics and heat exchangers.
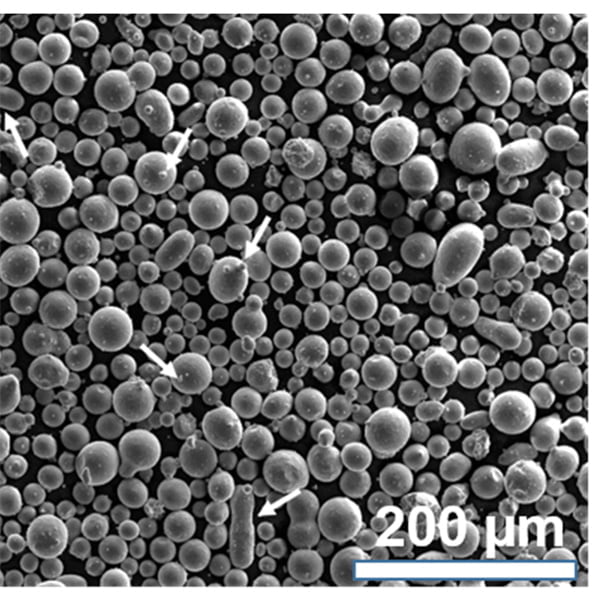
Disadvantages of Spherical Powder
While spherical powders have many advantages, there are some limitations to consider:
Higher Cost
The production of spherical powders can be more expensive due to the specialized processes required to achieve the uniform shape.
Limited Material Availability
Not all materials are available in spherical form, which can limit options for specific applications.
Specialized Equipment Required
Handling and processing spherical powders often require specialized equipment, which can add to the overall cost and complexity of the manufacturing process.
Potential for Segregation
In some applications, the uniform shape can lead to segregation issues, where different sizes of particles separate, affecting the consistency of the final product.
Comparative Analysis of Spherical Powder Types
Here’s a comparison of different spherical powders, highlighting their pros and cons:
Material | Advantages | Disadvantages |
Ti-6Al-4V | High strength, lightweight, excellent corrosion resistance | Expensive, requires specialized equipment for processing |
AlSi10Mg | Good thermal properties, lightweight, cost-effective | Limited high-temperature performance |
316L Stainless Steel | Corrosion resistance, good mechanical properties | Higher cost compared to other steels |
Cu-OFHC | Excellent electrical and thermal conductivity | Soft, prone to wear and tear |
Inconel 718 | High temperature resistance, corrosion resistance | Very expensive, difficult to machine |
CoCrMo | High wear resistance, biocompatibility | Expensive, limited to specialized applications |
Iron | Good magnetic properties, cost-effective | Prone to rust and corrosion |
Tungsten | High density, high melting point | Very heavy, difficult to process |
Molybdenum | High strength at high temperatures | Brittle, difficult to machine |
Zinc | Good corrosion resistance, cost-effective | Lower mechanical strength, limited structural applications |
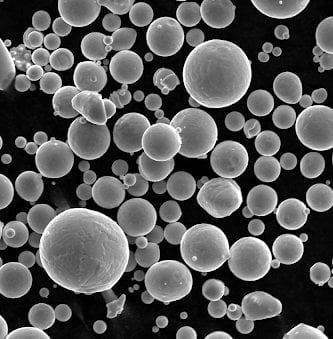
FAQ
What is spherical powder?
Spherical powder is a type of metal powder with particles shaped like spheres, offering high flowability and packing density for precision applications.
What are the common types of spherical powder?
Common types include Ti-6Al-4V, AlSi10Mg, 316L Stainless Steel, Cu-OFHC, Inconel 718, CoCrMo, Iron, Tungsten, Molybdenum, and Zinc.
Where is spherical powder used?
It is used in additive manufacturing, metal injection molding, coatings, powder metallurgy, electronics, battery production, catalysts, sintering, thermal spraying, and filtration.
What are the advantages of spherical powder?
Advantages include high flowability, high packing density, uniformity and consistency, reduced porosity, and improved thermal conductivity.
What are the disadvantages of spherical powder?
Disadvantages include higher cost, limited material availability, specialized equipment requirements, and potential for segregation in some applications.
Who are the main suppliers of spherical powder?
Main suppliers include Höganäs, LPW Technology, Carpenter Technology, Valimet, AP&C, Sandvik Osprey, Praxair Surface Technologies, Tekna, Kennametal, and Arcam AB.
How is spherical powder priced?
Pricing varies based on material and supplier, typically ranging from $20 to $600 per kilogram.
Share On
MET3DP Technology Co., LTD is a leading provider of additive manufacturing solutions headquartered in Qingdao, China. Our company specializes in 3D printing equipment and high-performance metal powders for industrial applications.
Inquiry to get best price and customized Solution for your business!
Related Articles
About Met3DP
Recent Update
Our Product
CONTACT US
Any questions? Send us message now! We’ll serve your request with a whole team after receiving your message.
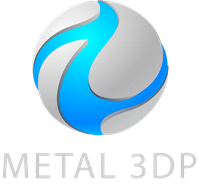
Metal Powders for 3D Printing and Additive Manufacturing