Spherical Titanium Powder
Table of Contents
Overview
Spherical titanium powder is a form of titanium metal powder that has been processed to have a spherical morphology. It is characterized by its high sphericity, smooth surface, controlled particle size distribution, and good flowability.
Some key properties and details of spherical titanium powder include:
Types
- Pure titanium powder
- Titanium alloy powders (Ti-6Al-4V, Ti-6Al-7Nb, etc.)
Production Methods
- Gas atomization
- Plasma rotating electrode process (PREP)
- Electrode induction melting gas atomization (EIGA)
Particle Size Range
- 15-45 microns
- 45-100 microns
- 106-250 microns
Typical Uses
- 3D printing powder
- Metal injection molding
- Thermal spraying
- Production of titanium parts
Key Characteristics
- High sphericity (>90%)
- Controlled particle size distribution
- Good flowability
- High purity
- Lower surface area compared to irregular powders
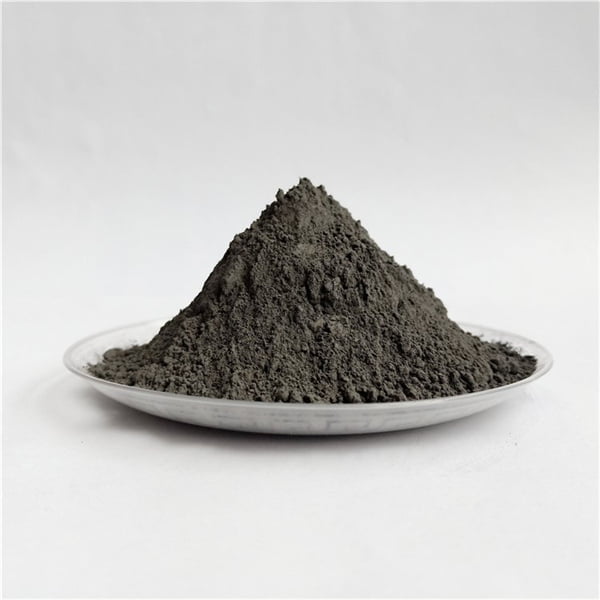
Types of Spherical Titanium Powder
There are two main categories of spherical titanium powder based on composition:
Table 1: Types of spherical titanium powder
Type | Description |
---|---|
Pure Titanium | 99.5% titanium with low oxygen and iron levels |
Titanium Alloys | Titanium combined with aluminum + vanadium, niobium, etc. |
Pure Titanium Powder
Pure spherical titanium powder contains at least 99.5% titanium with maximum limits on the levels of oxygen and iron. It has the highest titanium content compared to titanium alloys.
Typical composition:
- Titanium: 99.5% minimum
- Oxygen: 2000 ppm maximum
- Iron: 3000 ppm maximum
It offers properties close to pure titanium metal – high strength, low density, corrosion resistance. It is used when high chemical purity is needed.
Titanium Alloy Powders
The most common titanium alloy powders are Ti-6Al-4V and Ti-6Al-7Nb containing aluminum and vanadium or niobium additions. Other alloys are also produced with elements like molybdenum, zirconium and tin.
Benefits of alloys:
- Increased strength
- Higher temperature capability
- Enhanced corrosion resistance
Alloy powders expand the application range beyond pure titanium powders.
Production Methods for Spherical Powder
Various gas atomization techniques are used commercially to make spherical titanium powder with controlled particle sizes:
Table 2: Production processes for spherical titanium powder
Method | Principle | Particle Size* |
---|---|---|
Gas Atomization | Molten stream disintegration by gas jets | 15-106 μm |
Plasma Rotating Electrode (PREP) | Centrifugal disintegration of molten metal | 15-45 μm |
Electrode Induction Gas Atomization (EIGA) | Induction melting + gas atomization | 15-250 μm |
Typical size ranges produced
Gas atomization uses high velocity inert gas jets like argon or nitrogen to break up a molten stream of titanium metal into fine droplets, which solidify into powder. This produces spherical particles with smooth surfaces a result of surface tension effects.
PREP and EIGA are variants that offer increased control, narrower size distributions and shape optimization.
Specifications
Spherical titanium powder is available in various size cuts classified according to particle diameter. Common mesh-based size ranges include:
Table 3: Particle size specifications
Size Classification | Mesh Range | Particle Diameter |
---|---|---|
Small | -325 mesh | <45 μm |
Medium | 140-325 mesh | 45-100 μm |
Large | +100 mesh | >106 μm |
Other parameters used to specify powders:
- Sphericity: >90% indicates how spherical the particles are
- Tap density: 2.2-3.5 g/cm3 indicates packing density
- Hausner ratio: <1.25 indicates flowability
- Apparent density: range based on composition
- Flow rate: measurement of mass flow through a funnel
Standards used for specifying powders include ASTM B819, ASTM F3049, EN 10204/3.1.
Applications of Spherical Titanium Powder
The controlled particle size distribution and spherical morphology provides certain benefits that expand the uses of titanium powder:
Table 4: Typical applications of spherical titanium powder
Area | Benefits |
---|---|
3D Printing | Excellent flowability, packing density for additive manufacturing |
Metal Injection Molding | Allows complex net-shape part fabrication |
Thermal Spraying | Improves coating density and deposition efficiency |
Powder Metallurgy | Facilitates manufacture of titanium parts like fasteners, gears |
Biomedical | Enhances properties of surface coatings for implants |
Aerospace | Used to repair jet engine parts via hot isostatic pressing |
The main advantage of spherical powder is it facilitates automated material handling better than irregular powder. This allows fabrication of titanium components to near net shape.
Suppliers and Pricing
Spherical titanium metal powder is sold by various leading manufacturers:
Table 5: Major spherical titanium powder suppliers
Company | Production Methods |
---|---|
AP&C | Gas atomization |
Carpenter Technology | Electrode induction melting |
Sandvik | Plasma atomization |
TLS Technik | Gas atomization |
Tekna | Plasma induction |
Pricing estimate:
- Pure titanium: $50-100 per kg
- Titanium alloys: $70-150 per kg
Pricing varies based on quantity ordered, powder grade, particle size range as well as market demand and supply economics.
Pros vs Cons of Spherical Titanium Powder
Table 6: Comparison of advantages and disadvantages
Advantages | Disadvantages |
---|---|
Excellent flowability for automation | Higher cost than other forms |
High packing density | Limited very large size availability |
Controlled particle size distribution | Requires controlled inert atmosphere |
Near net-shape fabrication capability | Reactive at high temperatures |
Good blending with other powders | Dust explosion hazard must be managed |
Achieves material properties closer to bulk |
While spherical titanium powder enables greater process flexibility, it also requires handling precautions against ignition or explosion. Cost is higher than other forms like sponge fines.
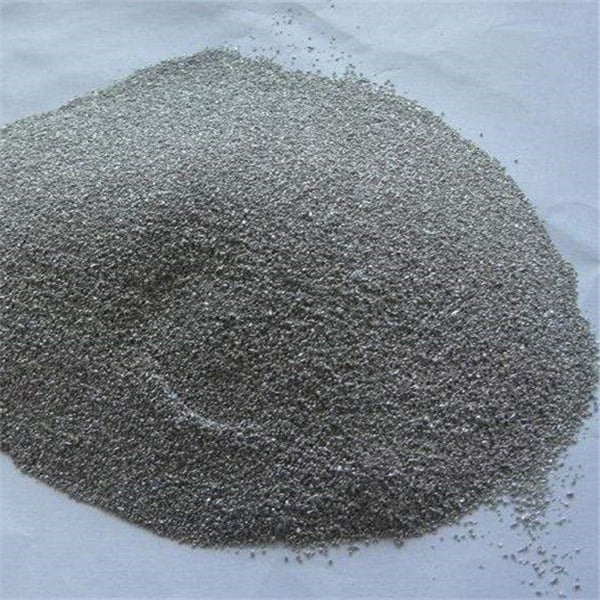
FAQs
What is the typical purity level of spherical titanium powder?
For pure titanium powders, the purity level is 99.5% minimum titanium content as per ASTM standards. For alloys like Ti-6Al-4V, the titanium level is over 90% with specific ranges for other elements.
What size range is best suited for additive manufacturing?
For most titanium powder bed fusion processes, the ideal particle size range is 45-100 microns. Smaller sizes have poor flow while larger sizes affect resolution. Standards like ASTM F3049 provide specifications.
Does spherical shape affect the properties of printed parts?
Yes, spherical particles result in higher density prints with better interparticle bonding leading to improved mechanical properties. Parts can achieve properties closer to bulk titanium.
What is the typical production capacity for spherical titanium powder?
Leading manufacturers of spherical titanium powder have capacities ranging from a few hundred tons per year to over 2000 tons per year currently. Capacities are expected to expand significantly to match growth in metal AM.
How is pricing of spherical titanium powder determined?
Pricing depends on powder composition, particle size range, production method, order volume, and market conditions. Smaller sizes (<45 μm) are typically 20-30% higher priced than larger sizes due to greater processing difficulty and demand.
Conclusion
Spherical titanium powder has distinct advantages over other forms of titanium powders in terms of flowability, packing density, and repeatability in automated powder processing. This enables fabrication of near net-shape components with superior properties.
Various gas atomization techniques allow tailored production of titanium alloys and particle size distributions for manufacturing methods like metal 3D printing which rely on powder bed fusion technology.
Despite higher prices, the benefits of spherical morphology drive increasing adoption across industries to expand the applications of titanium metal beyond conventional processing. Advancements continue, improving size distributions and alloy compositions to enhance properties further.
Share On
MET3DP Technology Co., LTD is a leading provider of additive manufacturing solutions headquartered in Qingdao, China. Our company specializes in 3D printing equipment and high-performance metal powders for industrial applications.
Inquiry to get best price and customized Solution for your business!
Related Articles
About Met3DP
Recent Update
Our Product
CONTACT US
Any questions? Send us message now! We’ll serve your request with a whole team after receiving your message.