Stainless Steel 316L Powder
Table of Contents
stainless steel 316l powder is widely used across industries owing to its excellent corrosion resistance and mechanical properties. This guide provides an overview of 316L powder composition, attributes, processing, applications, and suppliers for additive manufacturing.
Introduction to Stainless Steel 316L Powder
Property | Description | Benefits for Additive Manufacturing |
---|---|---|
Alloy Composition | Stainless steel 316L powder is a chromium-nickel molybdenum (Moly) austenitic stainless steel. The key elements include: Chromium (Cr): 16-18% Nickel (Ni): 10-14% Molybdenum (Mo): 2-3% Iron (Fe): Balance Silicon (Si) and Manganese (Mn) are also present in small quantities. | Excellent corrosion resistance Good high-temperature strength Improved weldability |
Corrosion Resistance | The presence of chromium provides inherent corrosion resistance. Molybdenum further enhances resistance to pitting corrosion, particularly in chloride-rich environments like seawater. | Suitable for applications exposed to harsh environments or corrosive media * Ideal for components in marine, chemical processing, and food & beverage industries |
High-Temperature Strength | Compared to standard 304 stainless steel, 316L powder offers improved strength at elevated temperatures. | * Enables the creation of parts for applications involving high operating temperatures, such as heat exchangers or jet engine components. |
Weldability | The low carbon content in 316L powder minimizes the risk of weld sensitization, a phenomenon that can lead to embrittlement in the heat-affected zone of welds. | * Facilitates the creation of complex parts through welding of additively manufactured components or integration with traditionally fabricated elements. |
Powder Characteristics | 316L stainless steel powder is typically available in a range of particle sizes, with spherical or near-spherical morphologies for optimal flowability in additive manufacturing processes. | * Ensures consistent powder flow during printing, leading to good dimensional accuracy and repeatability in the final parts. |
Applications | Stainless steel 316L powder is a versatile material used in various 3D printing applications, including: * Marine components (impellers, valves) * Chemical processing equipment (reactors, pumps) * Food & beverage machinery * Medical implants (joint replacements) * Aerospace parts (heat exchangers, ducting) | * Offers a combination of printability, corrosion resistance, and mechanical properties for diverse industrial applications. |
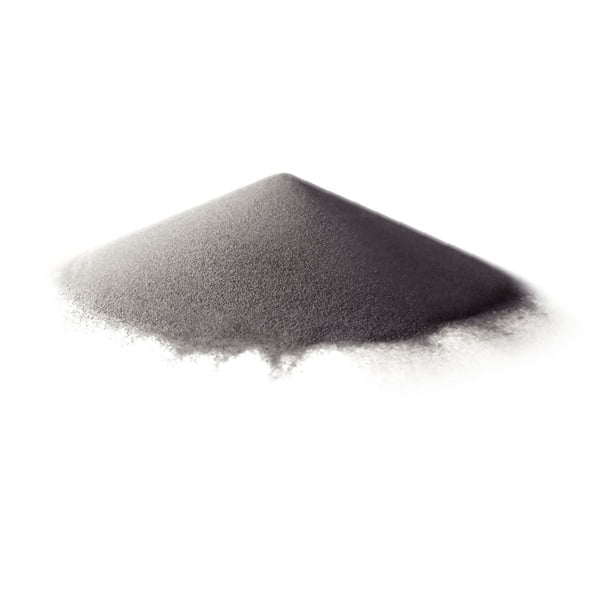
Chemical Composition
The composition of stainless steel 316l powder is:
Table 2: 316L stainless steel powder chemical composition
Element | Weight % | Role |
---|---|---|
Iron (Fe) | Balance | Base metal |
Chromium (Cr) | 16-18% | Corrosion resistance |
Nickel (Ni) | 10-14% | Corrosion resistance |
Molybdenum (Mo) | 2-3% | Pitting resistance |
Manganese (Mn) | ≤ 2% | Deoxidizer |
Silicon (Si) | ≤ 1% | Deoxidizer |
Phosphorus (P) | ≤ 0.045% | Impurity limit |
Sulfur (S) | ≤ 0.03% | Impurity limit |
Carbon (C) | ≤ 0.03% | Impurity limit |
Nitrogen (N) | ≤ 0.1% | Impurity limit |
The optimized composition of chromium, nickel and molybdenum boosts corrosion resistance. Let’s explore the properties next.
Mechanical Properties
Table 3: stainless steel 316l powder properties
Property | Value |
---|---|
Density | 8.0 g/cm3 |
Elastic modulus | 193 GPa |
Melting point | 1375°C |
Thermal conductivity | 16.3 W/m-K |
Electrical resistivity | 0.074 μΩ-cm |
Yield strength | 205 MPa |
Tensile strength | 515 MPa |
Elongation | ≥40% |
Hardness | 96 HB |
The combination of corrosion resistance, weldability, bio-compatibility, strength and ductility make 316L versatile for engineering across industries.
Production Process for stainless steel 316l powder
Common 316L powder production methods:
Table 4: 316L powder manufacturing processes
Method | Description | Characteristics |
---|---|---|
Gas atomization | Molten metal stream atomized by inert gas jets | Spherical particles ideal for AM |
Water atomization | Disintegration of molten stream by high pressure water | Irregular powder at lower cost |
Plasma atomization | Electrode vaporization in water-cooled copper crucible by plasma | Controlled particle size distribution |
Rotating electrode process | Centrifugal disintegration of spinning molten metal by electric arcs | Tight particle distribution |
Gas atomization with auxiliary pulse laser technology allows tuning the stainless steel powder shape, size, surface chemistry and defects.
Applications of stainless steel 316l powder
Thanks to excellent fabrication properties combined with strength and corrosion resistance, common applications of 316L powder include:
Table 5: 316L powder applications
Industry | Application | Components |
---|---|---|
Aerospace | Structural brackets, hydraulic systems, engines | Air/spacecraft fuel tanks, valves, fittings, nozzles |
Automotive | Corrosive fluid handling systems | Fuel cells, pumps, valves, pipes |
Architecture | Decorative/functional structures, signage | Railings, panels, letters |
Medical | Implants, prosthetics, devices | Cranial plates, hip joints, surgical tools |
Chemical processing | Tanks, vessels, valves | Mixers, reactors, heat exchangers |
Food/beverage | Pipework, vessels, utensils | Mixing blades, conveyors, molds |
Marine | Desalination, propulsion, environmental | Pumps, valves, heat exchangers |
3D printing enables relatively fast and affordable small batch production of end-use 316L parts. Let’s look at critical powder specifications next.
316L Powder Specifications for 3D Printing
Table 6: 316L powder specifications
Parameter | Specification |
---|---|
Particle size | 15-45 microns |
Apparent density | Typically > 4 g/cm3 |
Flow rate | Hall flowmeter > 15 s/50g |
Morphology | Spherical |
Phases | Austenitic |
Impurities | Low oxygen/nitrogen/sulfur |
Manufacturing method | Gas atomization |
Careful powder production tailored to additive manufacturing achieves defect-free printing and mechanical performance surpassing cast and wrought 316L steel.
Global Suppliers
Specialist manufacturers of 316L stainless steel powder include:
Table 7: 316L powder suppliers
Company | Location |
---|---|
Sandvik Osprey | Sweden |
LPW Technology | United Kingdom |
Carpenter Additive | United States |
Erasteel | France |
Aubert & Duval | France |
Praxair | United States |
These premium suppliers offer argon atomized 316L powder optimized for demanding additive manufacturing applications across industries.
stainless steel 316l powder Pricing
Factor | Description | Impact on Price |
---|---|---|
Market Fluctuations | The global market for metal powders, including stainless steel 316L, can be subject to fluctuations in raw material prices (nickel, chromium, molybdenum). | Sudden increases in the cost of these base metals can translate to higher powder prices. Staying informed about market trends can be helpful for budgeting and planning purposes. |
Supplier Choice | Selecting a reputable supplier can influence the price of stainless steel 316L powder. | Negotiating bulk purchase agreements with established suppliers can lead to more competitive pricing. Additionally, some suppliers may offer tiered pricing structures based on order volume. |
Powder Characteristics | The specific properties of the powder can affect its cost. | Finer powders with narrow particle size distributions or those with special surface treatments for improved flowability may command a premium price. Similarly, powders with specific certifications for medical or aerospace applications may be more expensive. |
Minimum Order Quantity | Some suppliers may have minimum order quantities (MOQ) for stainless steel 316L powder. | This can be a cost consideration, particularly for small projects or initial prototyping phases. Exploring alternative suppliers with lower MOQs or collaborating with other users for shared purchases can be cost-saving strategies. |
Geographic Location | The geographic location of the supplier and the buyer can influence the final price due to factors like transportation costs and import duties. | Sourcing powder from a local supplier can minimize transportation costs. However, depending on regional availability and market dynamics, it may be more cost-effective to purchase from a supplier in another location. |
Pros vs. Cons of Stainless Steel 316L Powder
Pros | Cons |
---|---|
Excellent Corrosion Resistance: Stainless steel 316L powder boasts exceptional resistance to corrosion, particularly in environments with chlorides like seawater. This makes it ideal for applications in marine, chemical processing, and food & beverage industries. | Limited Strength Compared to Some Alloys: While offering good mechanical properties, 316L may not be the strongest option for all applications. For parts requiring extremely high strength-to-weight ratios, other metal alloys like titanium alloys might be better suited. |
High-Temperature Strength: Compared to standard 304 stainless steel, 316L powder offers improved strength at elevated temperatures. This allows for the creation of parts used in high-temperature environments like heat exchangers or jet engine components. | Post-Processing Requirements: Parts printed with 316L powder may require post-processing steps like hot isostatic pressing (HIP) to achieve optimal mechanical properties. This adds complexity and cost to the manufacturing process. |
Weldability: The low carbon content in 316L powder minimizes the risk of weld sensitization during welding. This facilitates the creation of complex parts through welding of additively manufactured components or integration with traditionally fabricated elements. | Surface Roughness: Metal parts printed with 316L powder can exhibit a rougher surface finish compared to machined or cast components. Additional post-processing techniques like polishing or machining may be necessary to achieve a desired surface quality. |
Biocompatible Grade Available: A specific variant of 316L powder with even lower carbon content (316LVM) is biocompatible and suitable for use in medical implants. | Potential Safety Hazards: Handling metal powders, including 316L, can pose safety hazards due to flammability, inhalation risks, and skin irritation. Proper personal protective equipment and adherence to safety protocols are essential. |
Versatility: 316L stainless steel powder offers a good balance between printability, corrosion resistance, and mechanical properties. This makes it a versatile material for various 3D printing applications across multiple industries. | Higher Cost: Compared to some other metal powders like aluminum, 316L can be more expensive due to the presence of additional alloying elements and the potential need for specialized post-processing. |
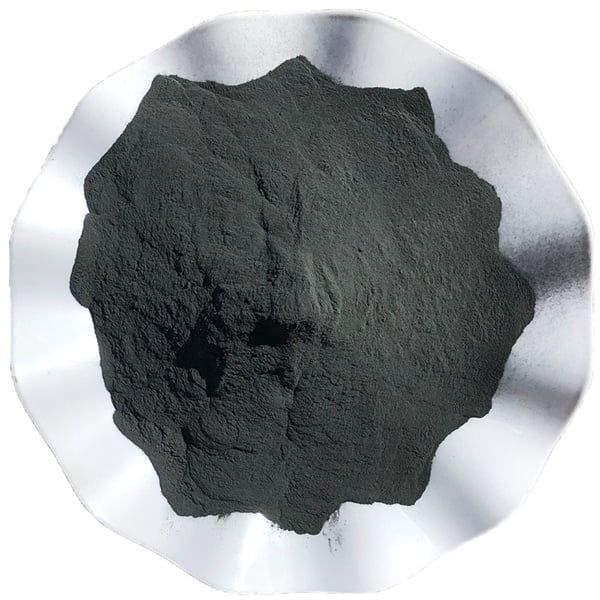
FAQ
Q: Is 316L powder printable for additive manufacturing?
A: Yes, with optimized production methods for AM to control particle shape and defects, 316L prints very well across binder jetting, DED and PBF processes for low to mid volumes applications.
Q: What particle size is ideal for printing 316L powder?
A: An ideal 316L powder particle size distribution ranges from 15-45 microns, avoiding ultrafine or coarse fractions, to enable high packing density and limit porosity.
Q: What post-processing is recommended for as-printed 316L parts?
A: Stress relieving heat treatment, hot isostatic pressing, and surface finishing like media blasting, grinding or electropolishing help improve as-printed 316L microstructure and aesthetics.
Share On
MET3DP Technology Co., LTD is a leading provider of additive manufacturing solutions headquartered in Qingdao, China. Our company specializes in 3D printing equipment and high-performance metal powders for industrial applications.
Inquiry to get best price and customized Solution for your business!
Related Articles
About Met3DP
Recent Update
Our Product
CONTACT US
Any questions? Send us message now! We’ll serve your request with a whole team after receiving your message.
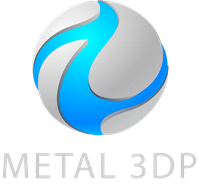
Metal Powders for 3D Printing and Additive Manufacturing