Stainless Steel Powder
Table of Contents
Stainless steel powder is a versatile material with applications across many industries. This comprehensive guide provides detailed information on various aspects of stainless steel powder to help you understand this material.
Overview of Stainless Steel Powder
Stainless steel powder is made from stainless steel that has been crushed into a fine powder form. It exhibits similar properties to stainless steel, including high strength, durability, corrosion resistance, and versatility. Key properties and characteristics include:
Properties:
- High strength and hardness
- Excellent corrosion resistance
- Good wear and abrasion resistance
- Versatile – can be used in various applications
- Ability to be sintered into parts
Characteristics:
- Fine powder form with particle sizes ranging from 1 micron to 150 microns
- Various grades available, including 304, 316, 410, 430
- Composition contains iron, chromium, nickel, molybdenum, manganese
- Powder can be blended with other powders like bronze, copper
Typical Applications:
- Manufacturing of industrial parts through metal injection molding and other powder metallurgy techniques
- Production of stainless steel filters
- Manufacturing of diamond tools
- 3D printing powders
- Brazing pastes and welding powders
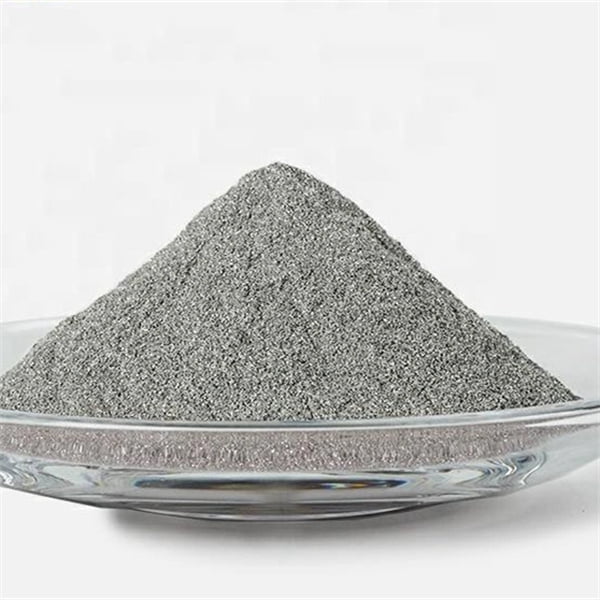
Top Stainless Steel Powder Suppliers
There are many reputable suppliers that provide quality stainless steel powders. Some of the top stainless steel powder manufacturers and vendors include:
Company | Location | Grades Offered |
---|---|---|
Sandvik | Sweden | 304L, 316L, 17-4PH, Custom Grades |
Höganäs | Sweden | 316L, 17-4PH, Custom Grades |
CNPC Powder Group | China | 304, 316L, 410, Custom Grades |
Daido Steel | Japan | 430, 304L, 316L |
ATI Powder Metals | USA | 304L, 316L, Custom Grades |
Pometon SpA | Italy | 304L, 316L, 430L |
These companies offer stainless steel powders in various common grades like 304, 316, 430, 410 as well as customized alloys. They have extensive experience and advanced production processes to ensure high quality powders.
Stainless Steel Powder Sizes
Stainless steel powders are available in a wide range of particle sizes to suit different applications. Some common size ranges include:
Size Range | Typical Uses |
---|---|
1- 10 microns | 3D printing powders, braze pastes |
10-44 microns | Metal injection molding |
44-150 microns | Conventional press and sinter powder metallurgy |
150-250 microns | Hot isostatic pressing pre-alloyed powders |
Finer powders provide better sintering, good surface finish and mechanical properties. Coarser particles sizes allow faster printing but poorer part resolution. The choice depends on balancing key application requirements.
Stainless Steel Powder Production Methods
Stainless steel powders are commercially produced using the following advanced methods that allow precise control over size and shape distributions:
Method | Description |
---|---|
Gas Atomization | Molten steel is disintegrated by high pressure gas jets to produce spherical powders |
Water Atomization | Uses water jets to breakup molten metal into irregular powders |
Mechanical Milling | Powders crushed/ground from small stainless pieces |
Electrolysis | Anodic dissolution of alloy into powders and cathode deposits |
Plasma Spheroidization | Irregular powders are remelted into spherical shape |
Gas atomized powders have the most spherical morphology ideal for additive manufacturing whereas water atomized and milled powders display more irregular shapes. Post processing like annealing, classification, and plasma treatment are done to obtain powders tailored to application needs.
Applications and Uses of Stainless Steel Powder
Stainless steel powder has gained immense use across industries owing to its excellent properties. Major application areas include:
Industry | Applications |
---|---|
Automotive | Engine & transmission components, pumps, valves |
Aerospace | Turbine blades, landing gear parts |
Medical | Surgical instruments, implants |
Marine | Pumps, propeller shafts |
Oil & Gas | Valves, wellhead components |
Industrial | Pipes, fittings, filters, bearings |
The automotive sector utilizes stainless steel powder the most for small intricate parts followed by aerospace and medical devices. Industries demand corrosion resistant, high strength parts which stainless steel powder can provide through modern manufacturing approaches.
Manufacturing Processes Using Stainless Steel Powder
- Metal Injection Molding (MIM): Most common powder metallurgy process where stainless steel powder is mixed with binders, molded and then sintered to produce small, complex parts like gears at high volumes.
- Additive Manufacturing: Selective laser melting, electron beam melting and binder jetting 3D print parts from stainless steel powder by fusing particles layer-by-layer. Allows complex geometries.
- Hot Isostatic Pressing (HIP): Heat and pressure are applied to consolidate and densify stainless steel powder preforms into fully dense functional parts. Filters, bearings employ this process.
- Cold/Warm Compaction: Simple powder pressing to shape followed by sintering to manufacture filters, magnets, and structural parts.
Stainless Steel Powder Part Manufacturing Guide
Manufacturing high quality stainless steel parts from powder requires systematic planning and execution. A general framework is provided below:
I. Requirements Finalization
- Part dimensions, tolerance, surface finish specifications
- Mechanical performance expectations – hardness, strength, toughness
- Production quantity
- Budget assessment
II. Design and Simulation
- CAD model optimized for manufacturability
- FEA, CFD analysis of models under working loads using actual material data
- Design tweaks based on analysis feedback
III. Prototype Production
- Produce prototype parts through same process as final parts
- Allows validation of CAD models, analysis data and process performance
IV. Powder Material Procurement
- Grade selection – 304 vs 316 vs 17-4PH based on corrosion resistance, temperature needs
- Desired powder characteristics – particle size range, morphology, purity levels
- Sourcing reputed manufacturers like Sandvik, Höganäs
V. Part Fabrication
- Parameter selection – compaction pressure, temperature profiles, build layout
- Precision equipment used – CNC presses, 3D printers, vacuum sintering furnaces
- Post processing – heat treatment, surface finishing
VI. Part Testing and Validation
- Measurement – dimensions, surface roughness, porosity
- Mechanical testing – tensile, hardness, impact toughness, fatigue
- Corrosion testing – salt spray, chemical exposure
- Revision of process based on results
VII. Full Scale Manufacturing
- Volume production after process capability and control confirmed
- Continual inspection and testing for quality assurance
- Consider automation to reduce costs at higher quantities
How to Choose A Reliable Stainless Steel Powder Supplier
Choosing a high quality stainless steel powder supplier is vital to part production success. Key selection criteria include:
1. Grade Options: Offer wide range – 304, 316L, 17-4PH, 420, Custom Alloys
2. Quality Standards: ISO 9001 certification, Strict chemical, grain size control
3. Sampling: Provide free testing samples to gauge quality
4. Consistency: Ensure batch-to-batch uniformity over years
5. Technical Support: Powder experts for advise on application requirements
6. Customer Service: Responsiveness to queries and timely delivery
7. Fair Pricing: Reasonable price relative to value offered
8. Heritage: Years in business signals reliability and good practices
Shortlist suppliers based on metals served, sampling policy, responsiveness and lead times. Prioritize ISO certified companies with strict quality control and metallography. Favor larger, reputable manufacturers like Sandvik, Höganäs over unreliable Agents or Traders.
Stainless Steel Powder Cost Breakdown
Like other alloys, cost depends on factors below:
Cost Drivers | Details |
---|---|
1. Grade | 316L > 17-4PH > 304. More nickel/chromium means higher cost |
2. Particle Size | Ultrafine Powders < 10 μm most expensive |
3. Morphology | Spherical > Irregular. Gas Atomization priciest |
4. Purity Levels | Higher purity powders used in medical devices cost more |
5. Order Quantity | Unit price reduces at 500+ kg quantities due to economy of scale |
6. Auxiliary Processing | Additional annealing, sieving etc. increases powder price |
Price Range: $5/kg – $60/kg
For prototyping, ordering smaller 5-10 kg samples for testing is recommended before bulk purchase. Payment terms are also quite flexible – secured LC, TT, Paypal.
Advantages & Limitations of Stainless Steel Powder
Advantages
- Excellent corrosion resistance
- High strength to weight ratio
- Good wear resistance
- Manufacture complex, net-shape parts
- Custom alloy grades possible
- Suitable for extreme environments
Limitations
- High material cost vs regular steel
- Lower ductility than wrought alloys
- Special handling to prevent oxidation
- Qualified personnel and costly equipment needed for part processing
With continual metallurgical advancements, stainless steel powder will open up novel applications in future.
Stainless Steel Powder Industry Trends and Outlook
Key trends shaping stainless steel powder demand:
- Surging use in 3D printing across aerospace, medical sectors
- Automotive lightweighting driving adoption of MIM components
- Demand for better performing alloys from oil and gas sector
- S. Korea, China markets growing over 12% annually
Industry forecasts indicate healthy 6-8% CAGR led by rising adoption in metal additive manufacturing. Top metal powder manufacturers are investing to expand capacities to meet sales volumes going forward.
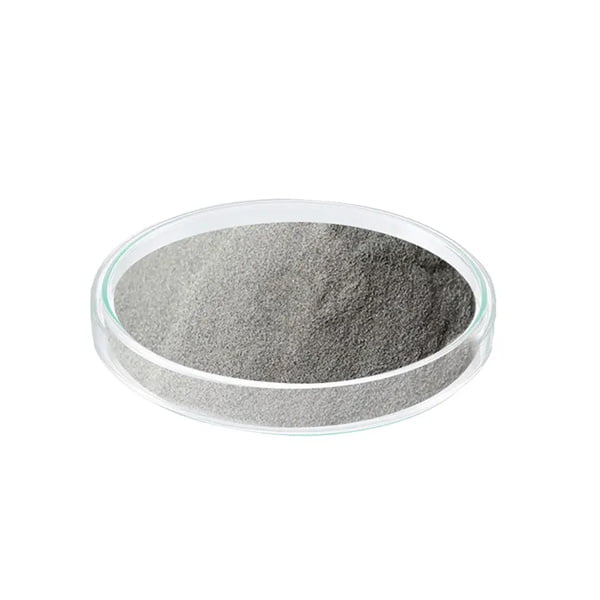
FAQ
Q: What particle size range works best for metal injection molding stainless steel powder?
A: 10-25 micron powders offer a good compromise between sinterability, moldability and reasonable cost for stainless steel metal injection molding applications.
Q: Does stainless steel powder get affected by moisture or storage conditions?
A: Yes, stainless steel readily oxidizes when exposed to atmospheric moisture at elevated temperatures. Proper dry inert gas sealed containers must be used for packaging and storing powders in climate-controlled warehouses below 30 C temperatures for preventing deterioration.
Q: What is the typical density achieved after sintering stainless steel 316L powder?
A: 316L powder compacts can attain over 92% theoretical density when vacuum sintered at high temperatures around 1350 C. Higher pre-sinter densities above 65% produce better final densities after pore elimination.
Q: Can stainless steel powders be blended with other powders?
A: Yes, to modify physical, functional or economic performance, stainless steel powders can be combined with other powders like bronze, cobalt alloys, hard phases like tungsten carbide in varied percentages using high energy mixing systems.
Q: Does stainless steel powder require any post processing after sintering?
A: For certain applications, post sinter heat treatments like solution annealing or aging may be done to modify hardness, toughness and other mechanical properties as per part specifications. Additionally surface operations like grinding or machining can enhance precision, surface finish and dimensional accuracy.
Share On
MET3DP Technology Co., LTD is a leading provider of additive manufacturing solutions headquartered in Qingdao, China. Our company specializes in 3D printing equipment and high-performance metal powders for industrial applications.
Inquiry to get best price and customized Solution for your business!
Related Articles
About Met3DP
Recent Update
Our Product
CONTACT US
Any questions? Send us message now! We’ll serve your request with a whole team after receiving your message.
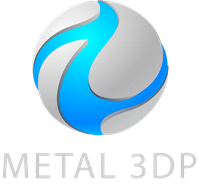
Metal Powders for 3D Printing and Additive Manufacturing