Stainless Steel Powders for Additive Manufacturing
Table of Contents
Stainless steel powders enable complex geometry printing using additive techniques unmatched by conventional metal manufacturing. This guide covers alloy variants, particle specifications, properties data, pricing insights and comparisons to inform stainless powder procurement.
Introduction to Stainless Steel Powders
Key capabilities offered by stainless steel powders:
- Fabricate complex, lightweight components
- Achieve superior corrosion resistance
- Enable rapid prototyping and customization
Common alloys used include:
- 304L – Cost effective with excellent corrosion resistance
- 316L – Superb corrosion resistance with molybdenum addition
- 17-4PH – High strength, hardest stainless powder
This guide provides considerations when selecting stainless powders:
- Alloy Compositions and Production Methods
- Mechanical Properties Test Data
- Particle Size Distribution Recommendations
- Morphology, Flow Rate and Apparent Density
- Supplier Price Ranges Based on Volumes
- Corrosion Resistance Comparisons
- Pros vs Cons Relative to Solid Barstock
- FAQs on Printing Parameter Optimization
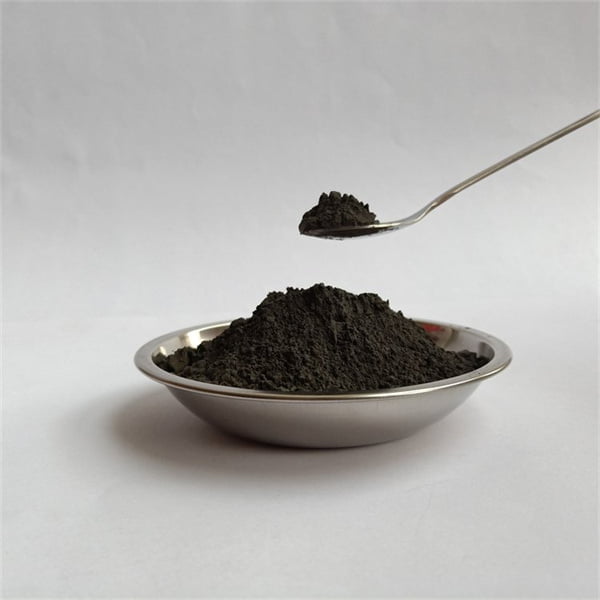
Stainless Steel Powder Compositions
Table 1 shows stainless steel powder alloy compositions by primary elemental additions with some variation across powder manufacturers:
Alloy | Major Alloying Elements |
---|---|
304L | Cr, Ni |
316L | Cr, Ni, Mo |
17-4PH | Cr, Ni, Cu |
Carbon is restricted (≤0.03%) in 304L and 316L to prevent carbide precipitation and maintain corrosion resistance and weldability.
Higher carbon in 17-4PH increases strength through martensitic hardening heat treatments.
Mechanical Properties and Test Methods
Property | Description | Test Method (Standard) | Importance for Additive Manufacturing (AM) |
---|---|---|---|
Apparent Density | Mass of powder per unit volume in its loose, uncompacted state | ASTM B922 | Influences powder flowability and ease of handling in AM processes |
Flowability | Ease with which powder particles flow under gravity | ASTM B2132 | Affects packing density and powder layer uniformity in AM builds |
Tap Density | Density of powder after a standardized tapping routine | ASTM B854 | Provides a basic assessment of powder packing efficiency |
Green Density | Density of a compacted powder body before sintering | ASTM B970 | влияет (vliyaniyet) on final density and dimensional accuracy of AM parts (influyats na final’nuyu plotnost’ i razmernuyu tochnost’ detaley AM) |
Sintered Density | Density of a powder body after sintering | ASTM B962 | Critical for achieving desired mechanical properties and corrosion resistance in AM parts |
Particle Size Distribution | Range of sizes present in a powder population | ASTM B822 | Impacts powder flowability, packing behavior, and final microstructure of AM parts |
Particle Shape | Morphological characteristics of individual powder particles (spherical, angular, etc.) | Scanning Electron Microscopy (SEM) | влияет (vliyaniyet) on packing density, inter-particle bonding, and flowability (influyats na plotnost’ upakovki, mezhchastichnoe svyazyvanie i tekuchest’) |
Surface Roughness | Microscopic variations on the surface of a powder particle | Atomic Force Microscopy (AFM) | Can influence inter-particle bonding and sintering behavior |
Chemical Composition | Elemental makeup of the powder material | X-Ray Fluorescence (XRF) | Determines final material properties, corrosion resistance, and suitability for specific applications |
Tensile Strength | Maximum stress a powder metallurgy (PM) specimen can withstand before pulling apart | ASTM E8 | Crucial for applications requiring high load-bearing capacity |
Yield Strength | Stress level at which a PM specimen exhibits plastic deformation | ASTM E8 | Important for understanding material’s elastic limit and predicting permanent deformation |
Elongation | Percentage increase in length a PM specimen experiences before fracture in a tensile test | ASTM E8 | Indicates material’s ductility and ability to deform without breaking |
Compressive Strength | Maximum stress a PM specimen can withstand before crushing under compressive load | ASTM E9 | Essential for applications experiencing compressive forces |
Hardness | Resistance of a material to indentation by a harder object | ASTM E384 | Relates to wear resistance and surface properties |
Fatigue Strength | Maximum stress a PM specimen can endure under repeated loading and unloading cycles without failure | ASTM E466 | Critical for components subjected to cyclic stresses |
Fracture Toughness | Material’s ability to resist crack propagation | ASTM E399 | Important for safety-critical applications where sudden failure cannot be tolerated |
Stainless Steel Powder Particle Size Recommendations
Application | Median Particle Size (D₅₀) | Particle Size Distribution (PSD) | Shape | Key Considerations |
---|---|---|---|---|
Metal Additive Manufacturing (Laser Melting, Electron Beam Melting) | 15-45 microns | Narrow (Tight distribution around D₅₀) | Spherical | – Flowability: Spherical particles flow more easily, enabling consistent layer formation. – Packing Density: Smaller particles can pack more tightly, reducing porosity in the final product. – Surface Finish: Extremely fine particles (<10 microns) can cause surface roughness. – Laser Absorption: Particle size can influence laser absorption efficiency, impacting melting behavior. |
Metal Injection Molding (MIM) | 10-100 microns | Broad (Wider distribution for packing and sintering) | Irregular | – Powder Flow: Irregular shapes can interlock, improving powder flow during injection molding. – Packing Density: A broader size distribution allows for better packing, reducing shrinkage during sintering. – Sintering Efficiency: Larger particles can hinder complete sintering, affecting mechanical properties. – Debinding: Large particles and broad distributions can trap debinding agents, leading to residual porosity. |
Plasma Spraying | 45-150 microns | Broad (Similar to MIM) | Irregular | – Impact Resistance: Larger particles improve impact resistance in the final coating. – Deposition Efficiency: Irregular shapes can enhance mechanical interlocking, improving coating adhesion. – Splat Morphology: Particle size influences splat formation during spraying, impacting coating microstructure. – Recoatability: Broader distributions may improve the ability to create smooth, layered coatings. |
Thermal Spraying (High Velocity Oxygen Fuel, Detonation Gun) | 45-250 microns | Broad (Similar to MIM) | Irregular | – Deposition Rate: Larger particles allow for faster deposition rates. – Particle Velocity: High-velocity processes require robust particles to minimize in-flight fracturing. – Coating Density: Broader distributions can promote denser coatings, but particle size can also affect packing efficiency. – Oxidation Resistance: Larger particle sizes can reduce surface area, potentially improving oxidation resistance. |
Additive Manufacturing (Binder Jetting) | 10-50 microns | Narrow (Similar to Laser Melting) | Spherical | – Resolution: Smaller particles enable finer feature details in the printed part. – Green Strength: Particle size and distribution can influence the strength of the unfired part. – Binder Compatibility: Particle surface area can affect binder adhesion and printability. – Moisture Sensitivity: Extremely fine powders may be more susceptible to moisture absorption, impacting handling. |
Powder Morphology, Flow Rate and Density
Property | Description | Importance in Powder Processing |
---|---|---|
Powder Morphology | The size, shape, and surface characteristics of individual powder particles. | Morphology significantly impacts packing density, flowability, and laser absorptivity in Additive Manufacturing (AM). Ideally, spherical particles with smooth surfaces offer the best packing density and flow characteristics. However, atomization processes can introduce variations. Gas-atomized powders tend to be more spherical, while water-atomized powders exhibit a more irregular, splattered morphology. Additionally, surface features like satellites (small particles attached to larger ones) and satellites can hinder flow and affect laser melting behavior in AM. |
Particle Size Distribution (PSD) | A statistical representation of the variation in particle sizes within a powder batch. It is typically expressed as a cumulative distribution curve or by reporting specific percentiles (e.g., d10 – 10% of particles are smaller than this size, d50 – median particle size). | PSD plays a crucial role in powder bed packing and influences the final density and mechanical properties of AM parts. A narrow PSD with a well-defined median size (d50) is preferred for consistent packing and laser melting depth. Conversely, a broad distribution can lead to segregation (larger particles separating from finer ones) during handling and uneven melting in the AM process. |
Apparent Density & Tap Density | * Apparent density: The mass of powder per unit volume when poured freely into a container. * Tap density: The density achieved after a standardized tapping or vibration protocol. | These properties reflect the packing behavior of the powder and are crucial for efficient powder handling and storage. Apparent density represents the loose packing state, while tap density indicates a denser packing achieved through mechanical agitation. The difference between these values, known as the Carr angle, is an indirect measure of flowability. Powders with a lower Carr angle (higher tap density closer to apparent density) exhibit better flow characteristics. |
Flow Rate | The rate at which powder flows under gravity through an orifice or hopper. | Flow rate is critical for consistent material feed in various powder processing techniques like AM and metal injection molding (MIM). Good flowability ensures smooth powder layer formation and avoids disruptions during the build process. Irregular particle shapes, presence of satellites, and moisture content can hinder flow rate. Manufacturers often employ flowability additives like lubricants to improve powder flow. |
Powder Density | The mass of powder per unit volume of the solid particles themselves, excluding voids between particles. | Powder density is a material property inherent to the specific stainless steel composition. It influences the final density achievable in the finished product after sintering or melting. Higher powder density typically translates to higher final product density and improved mechanical properties. |
Stainless Steel Powder Pricing
Factor | Description | Impact on Price |
---|---|---|
Grade | The specific type of stainless steel, designated by a three-digit number (e.g., 304, 316L, 17-4PH). Different grades offer varying degrees of corrosion resistance, strength, and formability. | Higher-grade stainless steel powders, like 316L with molybdenum for enhanced corrosion resistance, typically command a premium price compared to basic grades like 304. |
Particle Size and Distribution | The size and uniformity of the powder particles. Measured in microns (μm) or mesh size (number of openings per linear inch in a sieve), particle size significantly influences the final product’s properties and manufacturing process. | Finer powders (smaller microns/higher mesh size) generally cost more due to the additional processing required to achieve a narrower particle size distribution. However, finer powders can enable intricate details and smoother surface finishes in 3D printed parts. |
Surface Area | Closely linked to particle size, the total surface area of the powder particles per unit weight. Powders with higher surface areas tend to be more reactive and require stricter handling protocols. | Powders with high surface areas may incur additional costs due to specialized handling and storage requirements to prevent contamination or moisture absorption. |
Manufacturing Process | The method used to produce the stainless steel powder. Common techniques include atomization (gas or water) and chemical vapor deposition (CVD). | Atomization processes are generally more established and cost-effective, while CVD yields finer and purer powders but at a higher price point. |
Purity | The chemical composition of the powder, with minimal presence of unwanted elements. | Higher purity powders, with lower levels of oxygen, nitrogen, and other impurities, often come at a higher cost due to stricter manufacturing controls. |
Spherical Morphology | The shape of the powder particles. Spherical particles offer superior flow characteristics and packing density, leading to improved printability and material utilization. | Spherical stainless steel powders are generally more expensive compared to irregular-shaped particles due to the additional processing steps involved. |
Quantity | The amount of stainless steel powder purchased. | Bulk purchases typically benefit from significant price reductions due to economies of scale offered by suppliers. |
Market Fluctuations | The global supply and demand dynamics for raw materials like chromium and nickel, which significantly impact the base price of stainless steel feedstock. | Periods of high demand or supply chain disruptions can cause price increases for stainless steel powders. |
Supplier | The reputation and expertise of the powder manufacturer. Established brands with rigorous quality control procedures may command a slightly higher price compared to lesser-known suppliers. | Reputable suppliers often provide additional services like technical support and material certifications, which can justify a slight price premium. |
Stainless Steel Powder Corrosion Resistance
Property | Description | Impact on Corrosion Resistance |
---|---|---|
Chromium Content | The key element in stainless steel’s corrosion resistance. It forms a thin, invisible layer of chromium oxide on the surface when exposed to oxygen, acting as a barrier against further oxidation (rust). | Higher chromium content (typically above 10.5%) translates to better corrosion resistance. Different grades of stainless steel powder have varying chromium levels, catering to specific environments. |
Molybdenum | Often added to improve resistance to pitting corrosion, a localized form of attack that creates deep holes in the metal. Molybdenum enhances the stability of the chromium oxide layer, particularly in environments containing chlorides (e.g., seawater). | Stainless steel powders with molybdenum are ideal for marine applications, chemical processing involving chlorides, and high-salinity environments. |
Nickel | Contributes to overall corrosion resistance, particularly in high-temperature settings. Nickel helps maintain the stability of the passive oxide layer and improves resistance to reducing acids. | Nickel-containing stainless steel powders are well-suited for applications involving hot acidic environments or high-pressure steam. |
Powder Manufacturing Method | The process used to create the powder can influence its microstructure and, consequently, corrosion resistance. Gas atomization, a common method, can trap oxygen within the particles, potentially leading to localized corrosion. | Choosing powders produced with methods minimizing internal oxidation, like water atomization, can enhance corrosion performance. |
Porosity | Sintering, the process of bonding powder particles, can leave behind tiny pores within the final product. These pores can act as initiation sites for corrosion if they trap contaminants or moisture. | Selecting powders with optimized particle size distribution and proper sintering parameters minimizes porosity, leading to improved corrosion resistance. |
Surface Finish | The surface topography of the finished component can influence how readily it interacts with the environment. Rougher surfaces offer more area for contaminants and moisture to adhere, increasing the risk of corrosion. | Smoother surface finishes, achievable through polishing or specific manufacturing techniques, enhance corrosion resistance by minimizing these potential sites. |
Grain Size | The size of individual metal grains within the sintered component can affect corrosion behavior. Finer grain sizes generally offer better corrosion resistance as they present a less permeable barrier to corrosive agents. | Selecting powders optimized for achieving fine grain structures during sintering can enhance the component’s ability to resist corrosion. |
Pros vs Cons: Powder vs Solid Barstock
Table 7
Advantages | Disadvantages | |
---|---|---|
Stainless Steel Powder | Complex shapes | Higher cost |
Great corrosion resistance properties | Post-processing | |
Lightweighting | Print parameter optimization | |
Stainless Steel Solid Bar | Cost effective | Shape limits |
Availability | Much heavier | |
Machinability | Material waste |
In general, stainless steel powder justifies higher prices for low volume complex components where corrosion resistance and weight reduction are vital. Bar forms offer affordability for simple shapes in high production use cases.
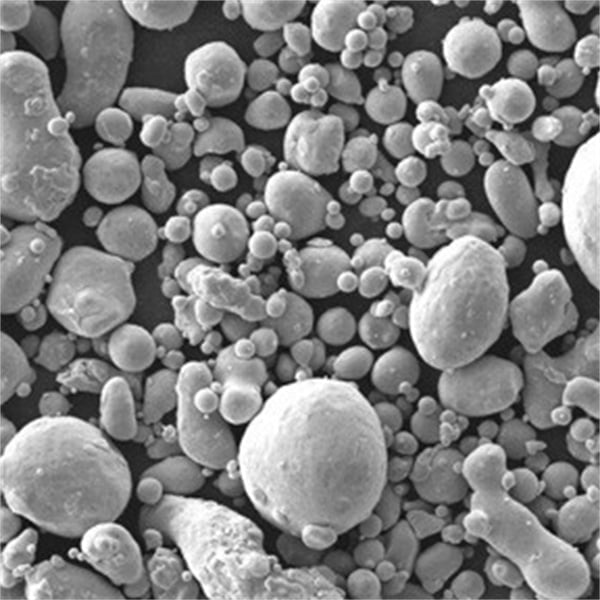
FAQs
Table 8 – Common questions:
FAQ | Answer |
---|---|
Should I review test reports? | Yes, scrutinize powder certification data thoroughly |
What size powder particles should I start with? | 25-45 micron for robust printing |
What factors impact consistency? | Raw powder production technique affects variability |
How much powder should I buy initially? | Start small scale to validate print process |
Table 9 – Application-focused advice:
FAQ | Answer |
---|---|
How should I adjust parameters for printing food-grade stainless equipment? | Optimize for low surface roughness and eliminate crevices |
What post-processing can reduce porosity for marine parts? | Consider hot isostatic pressing to maximize corrosion resistance |
Which alloy maximizes yield strength for load-bearing components? | 17-4PH precipitation-hardened stainless |
What stainless powder is optimal for high-temperature furnace parts? | 316L powder offers excellent oxidation resistance |
Share On
MET3DP Technology Co., LTD is a leading provider of additive manufacturing solutions headquartered in Qingdao, China. Our company specializes in 3D printing equipment and high-performance metal powders for industrial applications.
Inquiry to get best price and customized Solution for your business!
Related Articles
About Met3DP
Recent Update
Our Product
CONTACT US
Any questions? Send us message now! We’ll serve your request with a whole team after receiving your message.
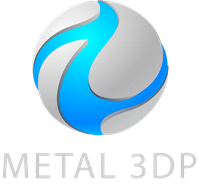
Metal Powders for 3D Printing and Additive Manufacturing