3D Printed Structures for Heat Redistribution in Space Systems
Table of Contents
Introduction: Revolutionizing Satellite Thermal Management with Metal 3D Printing
The hostile environment of space presents unique and formidable challenges for spacecraft design and operation. Outside the protective blanket of Earth’s atmosphere, satellites are subjected to extreme thermal cycles, swinging between the intense heat of direct solar radiation and the frigid cold of deep space shadow. Compounding this is the vacuum of space, which eliminates the possibility of convective cooling – the primary mechanism we rely on terrestrially to dissipate heat using air or fluid flow. This leaves only conduction (heat transfer through materials) and radiation (heat emission via electromagnetic waves) as viable methods for managing the thermal loads generated by the satellite’s own electronic components and absorbed from external sources. Effective thermal management is not merely a matter of comfort; it is mission-critical. Sensitive electronic components, optical payloads, propulsion systems, and even structural elements have specific operating temperature ranges. Exceeding these limits can lead to degraded performance, reduced lifespan, malfunction, or catastrophic failure, jeopardizing multi-million or even billion-dollar missions. Procurement managers and aerospace engineers are thus constantly seeking innovative solutions to enhance satellite thermal control and ensure mission success in these demanding space systems.
Traditionally, thermal management in satellites has relied on a combination of passive and active techniques. Passive methods include deploying thermal blankets (Multi-Layer Insulation or MLI), applying specialized surface coatings with specific absorptivity and emissivity properties, and utilizing heat pipes and radiators constructed from conventional materials like aluminum and copper alloys. Active systems might involve louvers, pumped fluid loops, or cryogenic coolers, adding complexity, mass, and power consumption. While effective, these traditional approaches often face limitations, particularly as satellites become more powerful, miniaturized, and packed with high-density electronics generating significant heat fluxes. Fabricating complex heat pipe geometries or optimizing radiator fin designs using conventional methods like CNC machining, brazing, or casting can be intricate, time-consuming, costly, and often result in heavier components than desired. Assembling multiple parts also introduces thermal resistance at interfaces and potential points of failure.
This is where metal additive manufacturing (AM), commonly known as metal 3D printing, emerges as a transformative technology. By building components layer by layer directly from metal powder using energy sources like lasers or electron beams, AM unlocks unprecedented design freedom. It allows engineers to create highly complex, optimized 3D printed satellite components specifically designed for superior heat redistribution. Imagine intricate internal channels mimicking biological vascular systems, lattice structures offering high surface area with minimal mass, or heat sinks perfectly conforming to the shape of the components they need to cool. These are geometries that are often impossible or prohibitively expensive to produce using subtractive manufacturing techniques.
Metal 3D printing enables the creation of novel heat flow enhancers and heat redistribution structures – components specifically designed to efficiently collect waste heat from critical areas (like processors, power amplifiers, or batteries) and conduct it effectively to radiator surfaces where it can be safely radiated into space. These structures can be standalone components or integrated directly into the satellite’s primary structure, leading to multifunctional designs that save weight and volume – two precious commodities in spacecraft design. The ability to consolidate multiple parts into a single printed component further reduces assembly complexity, minimizes thermal contact resistance, and enhances overall reliability. Furthermore, AM facilitates the use of advanced materials, including high-thermal-conductivity alloys specifically optimized for these applications.
Companies like Met3dp are at the forefront of this revolution, providing not only advanced metal 3D printing services but also developing and manufacturing high-performance metal powders crucial for achieving the desired thermal and mechanical properties in these demanding aerospace applications. With expertise in processes like Selective Electron Beam Melting (SEBM) and advanced powder production techniques like gas atomization, Met3dp empowers aerospace engineers and manufacturers to leverage the full potential of additive manufacturing for next-generation satellite thermal control. The integration of metal additive manufacturing into the design and production workflow offers a paradigm shift, moving beyond incremental improvements towards fundamentally new ways of managing heat in space systems, ultimately enhancing satellite performance, increasing operational lifespan, and enabling more ambitious missions. This shift requires a deep understanding of the technology’s capabilities, material properties, and design principles, making collaboration with experienced partners essential for successful implementation.
Applications: Where are 3D Printed Heat Flow Enhancers Utilized in Space Systems?
The versatility of metal additive manufacturing allows for the creation of bespoke thermal management solutions tailored to the specific needs of diverse space missions and satellite architectures. The ability to optimize geometry for thermal performance while minimizing mass makes 3D printed heat flow enhancers particularly attractive across a wide spectrum of applications within space systems. These components are rapidly transitioning from research concepts to flight-proven hardware, demonstrating tangible benefits for satellite manufacturers and aerospace component suppliers.
Here are some key areas where 3D printed structures for heat redistribution are making a significant impact:
- Enhanced Cooling for High-Power Electronics: Modern satellites, especially those for communications, remote sensing, and data processing, incorporate increasingly powerful electronic components. Field-Programmable Gate Arrays (FPGAs), Application-Specific Integrated Circuits (ASICs), high-power amplifiers (SSPAs), and processors generate substantial amounts of waste heat in concentrated areas. Traditional heat sinks or thermal straps might struggle to manage these high heat fluxes efficiently or may impose unacceptable mass penalties.
- Metal 3D printing allows for the design of highly optimized heat sinks with complex fin geometries, internal microchannels, or integrated heat pipe structures (like oscillating heat pipes or vapor chambers) directly coupled to the heat source.
- These 3D printed satellite components can be conformally shaped to match the irregular surfaces of electronic packages, minimizing thermal interface resistance.
- Using materials like Copper Chromium Zirconium (CuCrZr), known for its excellent thermal conductivity, AM can produce heat spreaders that quickly draw heat away from hotspots, preventing overheating and ensuring reliable operation. For applications where weight is paramount, Aluminum Silicon Magnesium alloys (AlSi10Mg) offer a good balance of thermal performance and low density.
- Procurement managers seeking satellite electronics cooling solutions can leverage AM to source custom, high-performance components that outperform off-the-shelf options.
- Integrated Structural-Thermal Components: One of the most compelling advantages of AM is the ability to create multifunctional components. Instead of having separate structural supports and thermal pathways, engineers can design parts that serve both purposes simultaneously.
- For instance, mounting brackets for electronic boxes or payload instruments can be designed with integrated channels or optimized topologies to conduct heat away from the mounted component towards the satellite’s main radiator panels.
- This part consolidation satellite approach significantly reduces part count, assembly time, fastener mass, and potential points of thermal or mechanical failure.
- Topology optimization software, coupled with the design freedom of AM, allows engineers to remove material strategically from structural elements, leaving load-bearing paths intact while creating efficient thermal conduits within the remaining structure. This leads to significant lightweighting aerospace opportunities without compromising performance.
- Advanced Heat Pipes and Vapor Chambers: Heat pipes are highly efficient passive devices for transferring heat over distances with minimal temperature drop. Traditional heat pipes typically have simple cylindrical or flattened geometries.
- Metal AM enables the fabrication of complex heat pipe geometries, such as curved or branched pipes that can navigate around other components within the tight confines of a satellite chassis.
- It allows for the integration of the wick structure (responsible for capillary action) directly into the heat pipe wall during the printing process, potentially improving performance and reliability compared to inserting conventional wick materials.
- Flat-plate vapor chambers, which spread heat across a surface, can be printed with intricate internal support structures and optimized vapor flow paths, enhancing their heat-spreading capabilities for applications like cooling large electronic boards or interfacing with radiator panels.
- Optimized Radiator Panels and Fins: Radiators are essential for rejecting waste heat into space. Their efficiency depends on surface area, surface emissivity, and the effectiveness of heat distribution across the radiating surface.
- AM allows for the creation of radiator panels with highly complex fin geometries (e.g., lattice structures, pin fins, fractal-like designs) that maximize surface area for radiation while minimizing mass.
- Thermal straps or connections that transfer heat from internal components to the radiator can be printed with optimized cross-sections and potentially integrated directly into the radiator panel itself, improving heat transfer efficiency.
- For CubeSat thermal management, where mass and volume are extremely constrained, miniaturized, high-performance radiators enabled by AM can be crucial for mission feasibility.
- Components for Cryogenic Systems: Some specialized space missions require cryogenic cooling for sensitive detectors or instruments.
- AM can be used to create complex heat exchangers, cryocooler components, or thermal straps designed to operate efficiently at very low temperatures, leveraging materials suited for cryogenic environments.
The adoption of 3D printed heat flow enhancers spans various satellite classes, from small CubeSats and SmallSats, where mass and volume savings are paramount, to large geostationary communication satellites and complex Earth observation or scientific missions demanding sophisticated thermal control. As aerospace engineering firms and satellite manufacturing companies gain more experience and confidence in the technology, driven by reliable aerospace component suppliers like Met3dp offering high-quality materials and printing processes, the scope of applications continues to expand, pushing the boundaries of space technology.
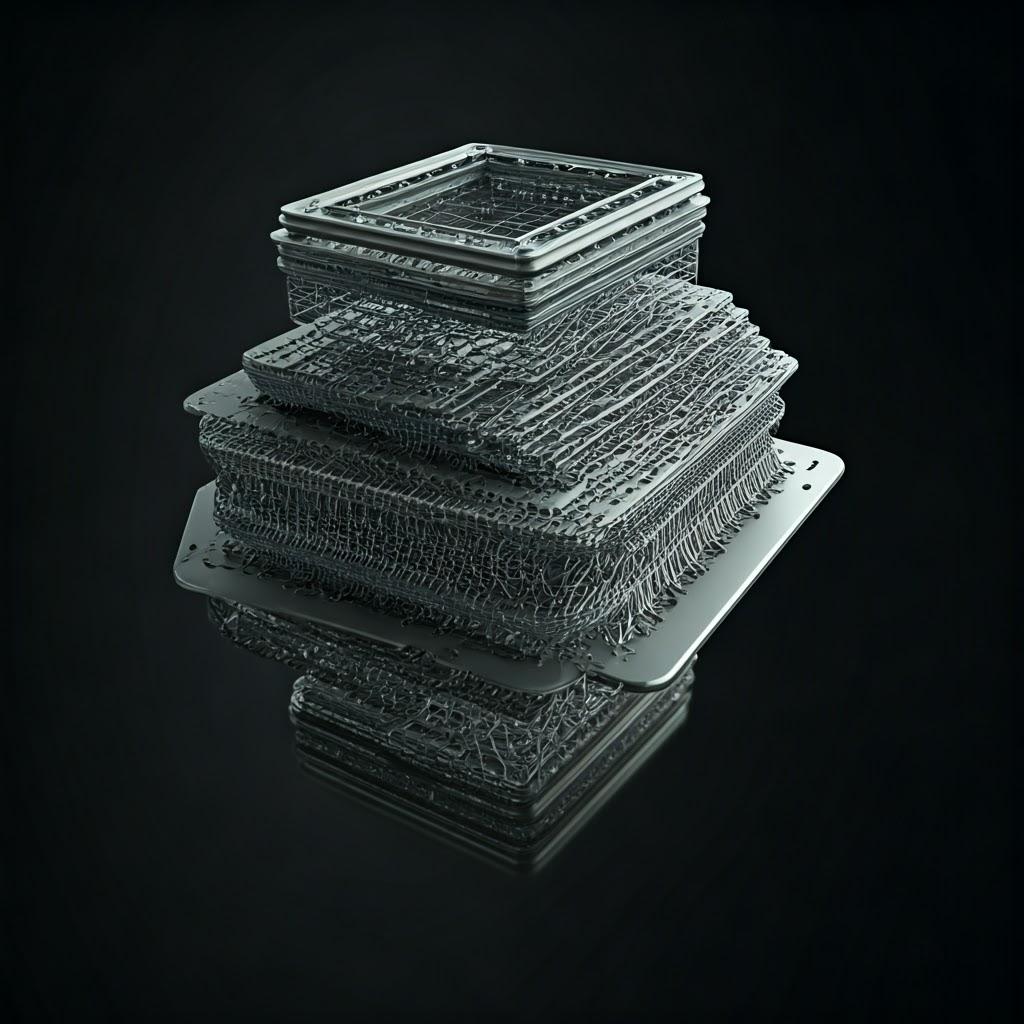
Why Metal 3D Printing for Satellite Heat Redistribution Structures?
The decision to adopt metal additive manufacturing for critical components like satellite heat flow enhancers stems from a convergence of compelling advantages over traditional manufacturing methods. While established techniques like CNC machining, casting, brazing, and sheet metal forming have served the aerospace industry well for decades, they often impose significant limitations when it comes to creating the highly optimized, complex geometries required for next-generation thermal management solutions. Engineers and procurement specialists evaluating manufacturing options for satellite components are increasingly turning to AM due to benefits that directly address the unique challenges of space systems.
Here’s a breakdown of why metal 3D printing offers a superior approach for these applications:
- Unparalleled Design Freedom (Geometric Complexity): This is arguably the most significant advantage. AM builds parts layer by layer, freeing designers from the constraints imposed by subtractive methods (material removal) or molding/casting techniques.
- Optimized Internal Channels: Engineers can design intricate internal channels and networks within a heat sink or heat exchanger, precisely controlling fluid flow (in active systems) or maximizing conductive paths and surface area in passive devices. This allows for designs that closely mimic highly efficient natural structures, like vascular networks.
- Lattice Structures: Lightweight yet strong lattice or topology-optimized structures can be created to maximize surface area for heat dissipation (e.g., in radiators or heat sinks) while minimizing material usage and mass.
- Conformal Cooling: Heat sinks and spreaders can be designed to perfectly conform to the curved or irregular surfaces of electronic components or satellite structures, minimizing thermal interface resistance and maximizing heat transfer efficiency.
- Integrated Features: Mounting points, fluid connectors, sensor housings, and other features can be directly integrated into the thermal component during the printing process.
- DfAM (Design for Additive Manufacturing): Leveraging DfAM principles allows engineers to fully exploit these geometric possibilities, leading to components that are fundamentally better suited for their thermal management task.
- Part Consolidation: Traditional thermal assemblies often involve multiple individual components (e.g., base plates, fins, heat pipes, brackets) that need to be manufactured separately and then joined together, typically through brazing, soldering, or mechanical fastening.
- AM allows multiple functional elements to be combined into a single, monolithic printed part. For instance, a mounting bracket could have integrated thermal straps and heat sink features.
- Benefits of Part Consolidation Satellite:
- Reduced Weight: Eliminates fasteners, interfaces, and overlapping material.
- Improved Reliability: Fewer joints mean fewer potential leak paths (for fluid systems) or points of mechanical/thermal failure.
- Lower Assembly Costs & Time: Simplifies the satellite integration process.
- Enhanced Thermal Performance: Eliminates thermal resistance associated with joints and interfaces.
- Material Efficiency and Lightweighting: Aerospace applications place a premium on minimizing mass due to the high cost of launching payloads into orbit (often tens of thousands of dollars per kilogram).
- Near-Net Shape Production: AM builds parts close to their final dimensions, using only the material necessary for the component itself and required support structures (which are often minimized through design). This contrasts sharply with subtractive manufacturing (like CNC machining), where a significant portion of an initial billet of material is machined away and becomes waste. This improves the “buy-to-fly” ratio, a critical metric in aerospace component supplier chains.
- Topology Optimization: Combined with design freedom, AM enables the practical application of topology optimization algorithms. These tools mathematically determine the most efficient distribution of material within a defined design space to meet specific performance requirements (e.g., stiffness, thermal conductivity) under given loads, resulting in highly organic-looking, lightweight structures impossible to make conventionally. This is a key driver for lightweighting aerospace components.
- Rapid Prototyping and Accelerated Development: The space hardware development cycle is notoriously long and expensive. AM offers significant advantages in speeding up this process.
- Fast Iteration: New design iterations for thermal components can be printed and tested in a matter of days or weeks, compared to months often required for traditional tooling and manufacturing setups. This allows engineers to quickly validate thermal models, explore different design concepts, and converge on an optimal solution much faster.
- Tooling Elimination: AM typically does not require the expensive and time-consuming creation of molds, dies, or fixtures associated with casting, forging, or complex machining setups. This drastically reduces upfront costs and lead times, especially for low-volume production runs typical of satellite hardware.
- On-Demand Manufacturing: Parts can be printed as needed, facilitating agile development and potentially supporting concepts like in-space manufacturing in the future.
- Material Flexibility: While this post focuses on AlSi10Mg and CuCrZr, AM processes are compatible with a growing range of metals and alloys relevant to aerospace, including various titanium alloys, nickel superalloys, and stainless steels. This allows engineers to select the optimal material based on the specific thermal, structural, and environmental requirements of the application. Access to high-quality powders, such as those produced by Met3dp using advanced gas atomization techniques, is crucial for achieving consistent and reliable material properties in the final printed part.
In summary, the comparison of metal 3D printing vs CNC machining and other traditional methods reveals compelling reasons for adopting AM for satellite heat redistribution structures. The ability to create highly complex, lightweight, consolidated parts optimized for thermal performance, coupled with accelerated development cycles, provides a significant competitive edge for satellite manufacturers and thermal solutions providers in the demanding aerospace market. Partnering with knowledgeable metal AM service providers ensures access to the necessary expertise in design, materials, and process control to fully realize these benefits.
Recommended Materials: AlSi10Mg and CuCrZr for Optimal Thermal Performance
Selecting the right material is paramount when designing any satellite component, but it takes on heightened importance for heat flow enhancers where thermal properties are the primary performance driver, balanced against stringent mass and structural requirements. For 3D printed satellite thermal management structures, two metallic powders have emerged as leading candidates, offering distinct advantages depending on the specific application needs: Aluminum Silicon Magnesium (AlSi10Mg) and Copper Chromium Zirconium (CuCrZr). Understanding their properties and why they are favored in aerospace metal powders selection is crucial for engineers and procurement managers.
Aluminum Silicon Magnesium (AlSi10Mg): The Lightweight All-Rounder
AlSi10Mg is one of the most widely used aluminum alloys in metal additive manufacturing, particularly Laser Powder Bed Fusion (L-PBF). It’s essentially an aluminum casting alloy adapted for AM processes.
- Key Properties & Benefits:
- Low Density: With a density of approximately 2.67 g/cm³, it is significantly lighter than copper alloys, steels, or titanium alloys, making it highly attractive for lightweighting aerospace components where mass is critical.
- Good Thermal Conductivity: While not as high as pure aluminum or copper, AlSi10Mg offers good thermal conductivity (typically in the range of 100-130 W/m·K after appropriate heat treatment), sufficient for many heat sink and heat spreader applications.
- Good Strength-to-Weight Ratio: It exhibits good mechanical properties, including decent tensile strength and hardness, especially after stress relief or T6-like heat treatments. This allows components made from AlSi10Mg to serve both structural and thermal functions.
- Excellent Processability: AlSi10Mg is known for its relatively good behavior during the L-PBF process, allowing for the reliable printing of complex geometries with fine features.
- Corrosion Resistance: Offers good resistance to corrosion.
- Typical Applications: Ideal for applications where a balance between low weight, reasonable thermal performance, and structural integrity is needed. Examples include:
- Integrated structural brackets with thermal pathways.
- Larger, complex heat sinks where the mass savings compared to copper are significant.
- Radiator panels with optimized fin structures.
- Housings for electronics requiring moderate heat dissipation.
Copper Chromium Zirconium (CuCrZr): The High-Conductivity Champion
CuCrZr (typically UNS C18150) is a precipitation-hardenable copper alloy known for its exceptional combination of high thermal and electrical conductivity and good mechanical strength, which is retained relatively well at elevated temperatures.
- Key Properties & Benefits:
- Excellent Thermal Conductivity: This is the standout feature. CuCrZr thermal conductivity is very high, often exceeding 300 W/m·K after suitable heat treatment (aging). This is significantly higher than AlSi10Mg and approaches that of pure copper, making it ideal for managing high heat fluxes.
- High Electrical Conductivity: Also possesses excellent electrical conductivity, which can be advantageous in some integrated applications.
- Good High-Temperature Strength: Retains its strength better at elevated temperatures compared to pure copper or some aluminum alloys.
- Good Wear Resistance: Offers reasonable wear resistance.
- Typical Applications: Primarily used where maximizing heat transfer is the absolute priority, even at the expense of higher density compared to aluminum. Examples include:
- High-performance heat sinks for densely packed, high-power electronics (e.g., amplifiers, processors).
- Heat spreaders designed to rapidly draw heat away from localized hotspots.
- Components in heat pipes or vapor chambers requiring maximum thermal throughput.
- Induction coils or components requiring both thermal and electrical conductivity.
Comparison and Considerations for Space Applications:
The choice between AlSi10Mg and CuCrZr often involves trade-offs:
Property | AlSi10Mg (Typical, Heat Treated) | CuCrZr (Typical, Heat Treated) | Traditional Al 6061-T6 | Traditional Copper (ETP) | Notes |
---|---|---|---|---|---|
Density (g/cm³) | ~2.67 | ~8.89 | ~2.70 | ~8.96 | CuCrZr is >3x denser than AlSi10Mg. |
Thermal Conductivity (W/m·K) | ~100 – 130 | ~300 – 320 | ~167 | ~390 – 400 | CuCrZr offers significantly higher K. |
Tensile Strength (MPa) | ~300 – 450 | ~450 – 550 | ~310 | ~220 (Annealed) | Both AM materials offer good strength. |
Coefficient of Thermal Expansion (CTE) (µm/m·°C) | ~21 – 22 | ~17 – 18 | ~23 | ~17 | Important for thermal stress & interfaces. |
Relative Cost | Moderate | Higher | Lower | Moderate | AM powders add cost premium. |
Printability | Generally Good | More Challenging | N/A | N/A | Reflectivity/conductivity impact AM process. |
Export to Sheets
Why these powders for Space?
Beyond the core thermal and mechanical properties, materials destined for space must meet other criteria:
- Outgassing: Materials must have low outgassing characteristics in a vacuum environment to prevent contamination of sensitive optical surfaces or electronics. Both AlSi10Mg and CuCrZr, when properly processed and cleaned, can meet typical space requirements.
- Radiation Resistance: While metals are generally less susceptible to radiation damage than polymers, the long-term effects in the space radiation environment need consideration, although typically less critical for these alloys compared to electronics.
- Process Reliability: Consistent and predictable material properties are essential for mission-critical hardware. This relies heavily on the quality of the input powder feedstock.
Met3dp’s Role in Material Excellence:
Achieving the optimal properties listed above in a finished 3D printed part depends critically on the quality and consistency of the metal powder used. Met3dp specializes in manufacturing high-quality metal powders optimized for additive manufacturing processes like L-PBF and SEBM. Utilizing advanced techniques such as vacuum gas atomization and Plasma Rotating Electrode Process (PREP), Met3dp produces powders with:
- High Sphericity: Ensures good powder flowability and dense packing in the powder bed, leading to higher density parts with fewer voids.
- Low Porosity: Minimizes internal powder porosity for better final part integrity.
- Controlled Particle Size Distribution (PSD): Optimized PSD for specific AM machines and processes, ensuring consistent melting and layer formation.
- High Purity: Minimizing impurities that could negatively impact mechanical or thermal properties.
By utilizing high-quality AlSi10Mg and CuCrZr powders from a reputable aerospace metal powders supplier like Met3dp, satellite manufacturers can have greater confidence in achieving the desired performance, reliability, and consistency required for demanding satellite material selection in thermal management applications. Consulting with material and AM experts is key to making the optimal choice for each unique mission requirement.
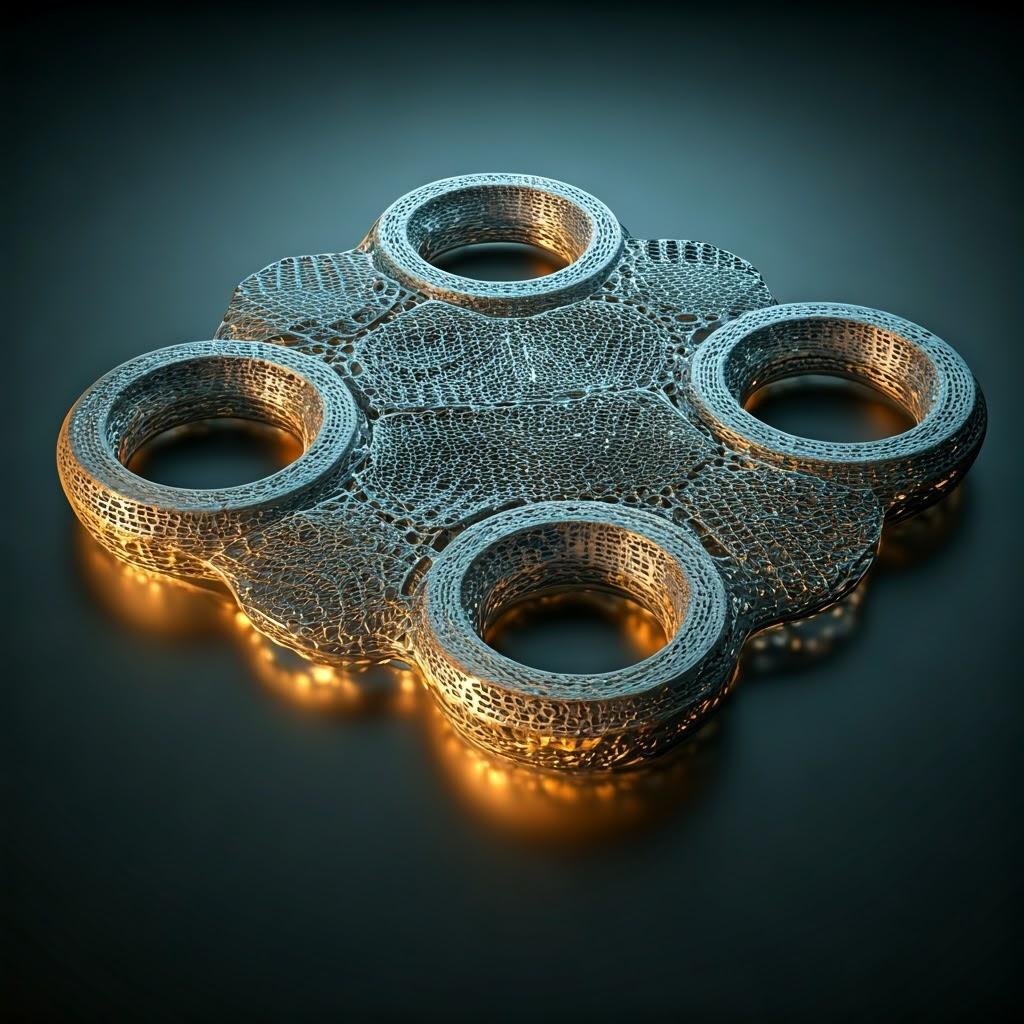
Design Considerations for Additively Manufactured Heat Flow Enhancers
The true power of metal additive manufacturing lies in the ability to translate complex, performance-driven designs into physical reality. However, simply replicating a design intended for traditional manufacturing often fails to leverage the full potential of AM and can even lead to suboptimal results or manufacturing difficulties. Designing successful 3D printed heat flow enhancers for space systems requires embracing Design for Additive Manufacturing (DfAM) principles. This approach considers the unique capabilities and constraints of the layer-by-layer building process right from the conceptual stage, ensuring thermal performance, structural integrity, and manufacturability are optimized simultaneously. Engineers designing satellite components, particularly thermal hardware, must think differently when AM is the chosen production route.
Here are key DfAM thermal management considerations for satellite heat enhancers:
- Leveraging Geometric Freedom for Thermal Performance:
- Optimized Internal Channels: Unlike drilling or casting, AM allows for smoothly curved, variable cross-section internal channels that minimize pressure drop (for fluid-based systems) or maximize convective surface area. Channels can follow complex paths to target specific heat sources directly. Thin, conformal channels can spread heat efficiently across surfaces.
- Advanced Fin Geometries: Move beyond simple extruded fins. AM enables complex fin structures like pin fins, tapered fins, wavy fins, or lattice-based fins (e.g., gyroids, octet trusses). These structures can significantly increase the surface-area-to-volume ratio, enhancing heat dissipation through convection (if applicable in ground testing or specific environments) or radiation, while simultaneously reducing mass. Lattice structures, in particular, offer excellent stiffness-to-weight ratios alongside enhanced surface area.
- Surface Area Maximization: Techniques like adding textured surfaces or incorporating micro-features within channels or on external surfaces can further enhance heat transfer, although the impact and practicality depend heavily on the specific heat transfer mechanism (conduction, radiation) and the surrounding environment (vacuum).
- Conformal Design: Design heat sinks, spreaders, or cold plates to perfectly match the contours of the heat-generating components (e.g., curved surfaces of circuit boards, non-planar device packages). This minimizes thermal interface material (TIM) thickness and contact resistance, leading to more efficient heat transfer compared to flat sinks on non-flat surfaces.
- Minimum Feature Sizes and Wall Thickness: AM processes, such as Laser Powder Bed Fusion (L-PBF), have limitations on the smallest features and thinnest walls they can reliably produce.
- Typical Limits: Depending on the machine, material (AlSi10Mg and CuCrZr have different processing characteristics), and parameters used, minimum wall thicknesses might range from 0.3 mm to 0.8 mm, and minimum feature sizes (like channel diameters or strut thicknesses in lattices) are often in a similar range. Exceeding these limits can lead to incomplete formation, poor surface finish, or structural weakness.
- Design Rule Adherence: Designers must work within the established L-PBF design rules provided by the AM service provider (like Met3dp). These rules, based on empirical data and process knowledge, guide achievable feature sizes, aspect ratios for unsupported walls or overhangs, and minimum hole diameters. Early consultation with the manufacturing partner is crucial.
- Support Structure Strategy: AM parts are built layer by layer, and overhanging features or surfaces oriented below a certain angle (typically < 45 degrees from the horizontal build plane) require temporary support structures during the printing process. These supports prevent distortion due to thermal stress, anchor the part to the build plate, and ensure geometric accuracy.
- Minimize Supports: Design parts with self-supporting angles wherever possible to reduce the need for supports, which consume extra material, add print time, and require post-processing for removal.
- Design for Removal: When supports are unavoidable, design them for easy access and removal without damaging the final part surface. Avoid placing supports on critical functional surfaces or within complex internal channels where removal is difficult or impossible. Consider break-off points or features that facilitate clean separation.
- Impact on Surface Finish: Surfaces where supports are attached will generally have a rougher finish after removal compared to self-supporting or upward-facing surfaces. This needs consideration if surface finish is critical in those areas. Specialized support strategies (e.g., easily removable or soluble supports, though less common in metal AM) might be explored with the provider.
- Topology Optimization and Lightweighting: This computational design technique is ideally suited for AM.
- Process: Engineers define a design space, apply expected thermal and structural loads, set performance targets (e.g., maximum temperature, minimum stiffness), and specify constraints (e.g., keep-out zones, manufacturing constraints). The software then iteratively removes material from non-critical areas, resulting in an optimized, often organic-looking structure that meets requirements with minimum mass.
- Application: Widely used for topology optimization aerospace brackets and structural elements, it’s equally powerful for thermal components. It can identify the most efficient paths for heat conduction while ensuring the part withstands operational stresses (e.g., launch vibrations). The resulting complex geometries are often only manufacturable via AM.
- Integration of Features: Reduce part count and assembly complexity by integrating features directly into the AM design.
- Mounting Interfaces: Design screw holes, bosses, locating pins, or complex mating surfaces directly into the heat enhancer. Ensure tolerances and surface finishes meet assembly requirements (potentially requiring post-machining).
- Fluid Connectors: For liquid-cooled systems or heat pipes, integrate threaded ports, pipe stubs, or manifold connections.
- Sensor Housing: Embed locations or mounts for temperature sensors (thermistors, thermocouples) for monitoring thermal performance.
- Thermal Modeling and Simulation: Given the complex geometries enabled by AM, accurate thermal modeling and simulation become even more critical during the design phase.
- Performance Prediction: Use Finite Element Analysis (FEA) or Computational Fluid Dynamics (CFD) tools to predict temperature distributions, heat flow paths, pressure drops (if applicable), and overall thermal resistance of the designed component under operational conditions.
- Design Iteration: Simulation allows for rapid virtual iteration and optimization of channel layouts, fin designs, and material choices before committing to expensive and time-consuming physical prototypes. Validate different DfAM thermal management strategies computationally.
- Correlation: Post-manufacturing thermal testing should be used to validate and refine the simulation models for future designs.
Successful satellite component design using AM requires a collaborative approach between design engineers, thermal specialists, and manufacturing experts. Engaging with experienced AM service providers like Met3dp early in the design cycle allows access to crucial manufacturing insights, material expertise, and guidance on L-PBF design rules, ensuring that the final 3D printed structure for heat redistribution is not only innovative but also manufacturable, reliable, and performs optimally within the demanding environment of space systems.
Achievable Tolerance, Surface Finish, and Dimensional Accuracy
While metal additive manufacturing unlocks incredible design freedom, it’s essential for engineers and procurement managers sourcing 3D printed satellite components to have realistic expectations regarding the achievable levels of precision. Tolerance, surface finish, and dimensional accuracy are critical factors, especially for components that must interface precisely with other parts of the satellite assembly or meet stringent performance criteria. Understanding the capabilities and limitations of processes like Laser Powder Bed Fusion (L-PBF) for materials such as AlSi10Mg and CuCrZr is key to successful implementation.
Tolerances in Metal AM:
- General Achievable Tolerances: As a rule of thumb, the typical dimensional accuracy for L-PBF metal parts falls within the range of ±0.1 mm to ±0.2 mm for smaller dimensions (e.g., up to 100 mm), or ±0.1% to ±0.2% for larger dimensions. These values can be influenced by several factors:
- Part Size and Geometry: Larger parts or complex geometries with thin walls or overhangs may exhibit greater deviation due to accumulated thermal stress and potential warpage during the build.
- Material: Different materials behave differently under the intense, localized heating and cooling cycles of L-PBF. AlSi10Mg and CuCrZr have distinct thermal properties that affect residual stress buildup and potential distortion.
- Machine Calibration: The accuracy and calibration of the specific AM machine play a significant role. High-end industrial machines, like those utilized by quality-focused providers such as Met3dp, generally offer better precision and repeatability.
- Build Orientation: The orientation of the part on the build platform affects thermal history, support requirements, and potential shrinkage anisotropies, influencing final dimensions.
- Post-Processing: Stress relief heat treatments can cause minor dimensional changes that need to be accounted for.
- ISO Standards: Often, achievable tolerances are related to general tolerance standards like ISO 2768 (medium ‘m’ or coarse ‘c’ classes). However, achieving tighter tolerances (e.g., ISO 2768-fine ‘f’) typically requires secondary machining operations.
- Critical Dimensions: For interfaces, mounting holes, or features requiring high precision, it’s standard practice to design the AM part slightly oversized (adding machining stock) and then use CNC machining in a post-processing step to achieve the required tight tolerances (e.g., down to ±0.01 mm or better, depending on the feature).
Surface Finish (Roughness):
The surface finish of as-built metal AM parts is inherently rougher than that achieved by conventional machining or polishing.
- Typical As-Built Roughness (Ra): Surface roughness (Ra value) typically ranges from 5 µm to 25 µm (micrometers), depending heavily on:
- Orientation: Upward-facing surfaces and vertical walls generally have the best finish. Downward-facing surfaces (supported surfaces) tend to be the roughest due to the interaction with support structures. Angled surfaces fall somewhere in between.
- Layer Thickness: Thinner layers generally result in a smoother finish but increase build time and cost. Typical layer thicknesses range from 20 µm to 60 µm.
- Process Parameters: Laser power, scan speed, and hatch spacing influence the melt pool characteristics and resulting surface texture.
- Powder Quality: The size distribution and sphericity of the metal powder (like the high-quality powders from Met3dp’s advanced atomization) can impact powder bed density and melt pool stability, influencing the final surface quality.
- Improving Surface Finish: If a smoother surface is required for thermal contact, fluid flow, sealing, or aesthetic reasons, various post-processing techniques can be employed:
- Bead Blasting/Sand Blasting: Provides a uniform matte finish, typically improving Ra slightly and removing partially melted particles.
- Tumbling/Vibratory Finishing: Can smooth external surfaces and deburr edges, particularly effective for batches of smaller parts.
- Electropolishing/Chemical Polishing: Can achieve very smooth, mirror-like finishes but may slightly round sharp edges. Effectiveness varies by material.
- CNC Machining/Grinding: Offers precise control over surface finish for specific areas.
- Micro-machining/Laser Polishing: Advanced techniques for achieving very high surface finishes on targeted areas.
Dimensional Accuracy and Verification:
Ensuring the final 3D printed structure for heat redistribution meets all dimensional specifications is critical for its function and integration within the satellite.
- Importance: Correct dimensions ensure proper fit with mating components, accurate alignment of thermal interfaces, and correct flow paths in internal channels. Deviations can lead to assembly issues, reduced thermal performance, or even structural problems.
- Metrology and Inspection: Reputable aerospace 3D printing services employ rigorous quality control and inspection procedures. Common techniques include:
- Coordinate Measuring Machines (CMM): Provide highly accurate 3D measurements of critical features and overall geometry.
- 3D Scanning (Laser or Structured Light): Capture the full geometry of the part, allowing comparison to the original CAD model to identify deviations across the entire surface (heat mapping).
- Traditional Metrology Tools: Calipers, micrometers, height gauges for specific feature measurements.
- Non-Destructive Testing (NDT): Techniques like X-ray or CT scanning can be used not only to check internal dimensional accuracy (e.g., channel diameters) but also to inspect for internal defects like porosity.
- Quality Management Systems: Look for suppliers with robust Quality Management Systems (QMS), potentially certified to standards like ISO 9001 or, ideally for aerospace, AS9100. This ensures documented processes for quality control, traceability, and continuous improvement. Met3dp, for instance, emphasizes its commitment to industry-leading print volume, accuracy, and reliability, backed by stringent quality protocols essential for mission-critical satellite components.
In conclusion, while engineers should leverage the design freedom of AM, they must also design with achievable metal 3D printing tolerances and surface finish L-PBF capabilities in mind. Specify critical tolerances clearly on drawings and discuss requirements with the AM provider early on. Plan for necessary post-processing steps, like machining, where as-built precision is insufficient. Partnering with a provider experienced in aerospace quality control and equipped with advanced metrology ensures that the final heat enhancer meets the exacting demands of space systems.
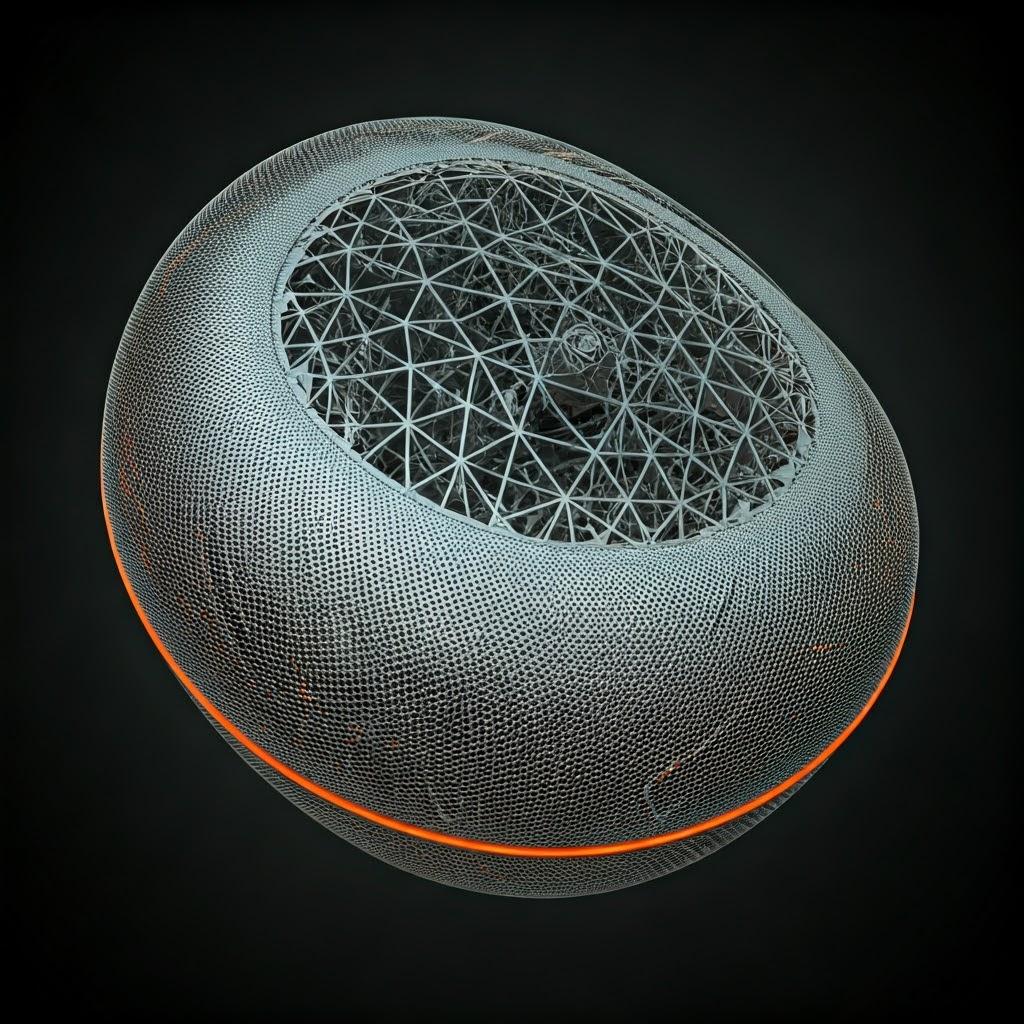
Post-Processing Requirements for 3D Printed Thermal Components
Producing a satellite heat flow enhancer using metal additive manufacturing doesn’t end when the part comes off the build plate. A series of essential post-processing steps are typically required to transform the as-built component into a functional, flight-ready piece of hardware. These steps are crucial for relieving internal stresses, achieving the desired material properties (including optimal thermal conductivity), removing temporary support structures, meeting dimensional and surface finish specifications, and ensuring the component is clean and ready for integration. Understanding these post-processing requirements is vital for project planning, cost estimation, and ensuring the final component meets the stringent demands of space systems.
Here’s a breakdown of common post-processing steps for AM parts made from AlSi10Mg and CuCrZr:
- Stress Relief / Heat Treatment: This is arguably one of the most critical steps, especially for metal AM parts. The rapid heating and cooling cycles inherent in L-PBF create significant residual stresses within the printed component.
- Purpose:
- Reduce Residual Stress: High internal stresses can cause distortion during or after the build (especially after removal from the build plate) and can negatively impact the part’s mechanical performance and fatigue life. Stress relief heat treatment significantly reduces these internal stresses.
- Optimize Microstructure & Properties: For alloys like AlSi10Mg and CuCrZr, specific heat treatment cycles are necessary to achieve the desired microstructure and, consequently, the optimal balance of mechanical properties (strength, ductility) and, importantly, thermal conductivity. The as-built microstructure is often non-equilibrium and may not exhibit the best thermal performance.
- Process: The specific temperature, time, and atmosphere (e.g., vacuum, argon) for heat treatment AlSi10Mg and post-processing CuCrZr AM parts depend on the alloy and the targeted properties. AlSi10Mg often undergoes a stress relief cycle followed potentially by a T6-like solutionizing and aging treatment for enhanced strength. CuCrZr typically requires solution treatment followed by aging to achieve its high conductivity and strength through precipitation hardening.
- Considerations: Heat treatment can cause minor dimensional changes (shrinkage or growth), which must be anticipated or compensated for, potentially by performing rough machining before heat treatment and final machining afterward.
- Purpose:
- Part Removal from Build Plate: The component is initially fused to a metal build plate. Separation is typically done using:
- Wire EDM (Electrical Discharge Machining): Offers a precise cut with minimal force exerted on the part, ideal for delicate structures.
- Sawing/Bandsawing: A more common and faster method for robust parts.
- Machining: Milling the base of the part away from the plate.
- Support Structure Removal: As discussed in the design section, temporary supports are often necessary.
- Methods: Support removal is often manual, using pliers, grinders, or hand tools. For complex or internal supports, CNC machining or potentially EDM might be required.
- Challenges: This can be labor-intensive and requires careful execution to avoid damaging the part surface. Difficulty in accessing internal supports highlights the importance of DfAM and support removal challenges mitigation through design. The areas where supports were attached will typically have a rougher surface finish.
- Surface Finishing: Depending on the application requirements, various surface treatments may be applied after support removal.
- Cleaning/De-powdering: Thorough removal of any loose or semi-sintered powder, often using compressed air, bead blasting, or ultrasonic cleaning. This is critical for preventing contamination in space systems.
- Bead Blasting / Sand Blasting: Creates a uniform, matte surface finish, removes minor imperfections, and can help close near-surface porosity. Different media (glass beads, ceramic, aluminum oxide) produce different finishes.
- Tumbling / Vibratory Finishing: Uses abrasive media in a rotating or vibrating drum to smooth external surfaces and edges. Best suited for batches of smaller, robust parts.
- Polishing (Manual or Automated): For achieving very smooth surfaces (low Ra) required for specific interfaces or sometimes for aesthetic reasons. Electropolishing can be effective for certain alloys like CuCrZr, providing a bright, smooth finish.
- Machining: As discussed below, used for achieving smooth, flat surfaces on critical areas.
- CNC Machining: Often essential for achieving tight tolerances and specific surface finishes on critical features.
- Applications: Machining mating surfaces, interfaces, sealing grooves, bearing bores, threaded holes, or any feature requiring precision beyond as-built AM capabilities. Achieving CNC machining 3D parts accuracy is common practice.
- Considerations: Requires careful fixture design to hold the potentially complex AM part without distortion. Machining stock must be included in the AM design for features requiring machining.
- Thermal Control Coatings: Satellite thermal management heavily relies on surface radiative properties (absorptivity and emissivity). Specialized thermal control coatings satellite applications are often required.
- Purpose: To tailor how the heat enhancer absorbs solar radiation and radiates waste heat to space.
- Types: Common coatings include specialized paints (e.g., white paints like AZ-93, black paints like Z-306), anodizing (especially for aluminum alloys like AlSi10Mg, which can be dyed black or left clear), or deposition coatings (e.g., silvered Teflon, Optical Solar Reflectors – OSRs, though typically applied to radiator panels rather than complex heat sinks).
- Surface Preparation: The effectiveness and adhesion of these coatings depend critically on proper surface preparation (cleaning, potentially specific roughness profiles).
- Cleaning and Inspection: Final cleaning is paramount for space hardware to meet stringent outgassing and contamination control requirements.
- Cleaning Procedures: May involve multi-stage processes using specific solvents, ultrasonic baths, and cleanroom environments following established aerospace cleaning standards.
- Final Inspection: Includes dimensional verification (CMM, scanning), surface finish checks, visual inspection, and potentially NDT (e.g., CT scanning for internal integrity checks) as required by the project specifications.
The extent and sequence of these post-processing steps depend heavily on the specific design, material, and application requirements. They contribute significantly to the overall cost and lead time of producing AM components. Therefore, understanding and planning for post-processing requirements is crucial for successfully implementing metal additive manufacturing for demanding applications like satellite heat flow enhancers. Working with a full-service provider like Met3dp, offering expertise across the entire workflow from powder to finished part, including necessary post-processing, streamlines the production process and ensures components meet all specifications. You can explore the different printing methods and associated post-processing implications further on the Met3dp website.
Common Challenges in 3D Printing Heat Enhancers and Mitigation Strategies
While metal additive manufacturing offers significant advantages for creating complex satellite thermal components, the process is not without its challenges. Understanding potential issues and implementing effective mitigation strategies during design, simulation, printing, and post-processing is crucial for ensuring the production of high-quality, reliable parts. Awareness of these metal AM defects and hurdles helps engineers and procurement managers set realistic expectations and work collaboratively with AM service providers to overcome them.
Here are some common challenges encountered when 3D printing heat flow enhancers from AlSi10Mg and CuCrZr, along with mitigation approaches:
- Residual Stress and Warpage:
- Challenge: The rapid, localized heating and cooling inherent in L-PBF generate significant thermal gradients, leading to the buildup of internal residual stresses within the part and the supporting structures. If these stresses exceed the material’s yield strength at elevated temperatures, they can cause distortion (warpage) during the build, detachment from supports, or cracking. Warpage can also occur after the part is removed from the build plate if stresses are not adequately relieved.
- Mitigation Strategies:
- Optimized Part Orientation: Orienting the part on the build platform to minimize large flat surfaces parallel to the recoater, reduce overhangs, and manage thermal mass distribution can help mitigate stress.
- Robust Support Structures: Designing sufficient, well-placed support structures is critical to anchor the part firmly to the build plate and resist warping forces. Finite element simulation can help optimize support placement and design.
- Process Parameter Optimization: Fine-tuning laser power, scan speed, and scan strategy (e.g., checkerboard patterns) can help manage thermal gradients. Using advanced systems with precise process control is beneficial.
- Platform Heating: Preheating the build platform reduces the thermal gradient between the melted material and the surrounding environment, lowering residual stress (more common in EBM, but also used in some L-PBF systems).
- Mandatory Stress Relief: Performing a stress relief heat treatment cycle immediately after printing and before removing the part from the build plate is the most effective way for residual stress mitigation.
- Porosity:
- Challenge: The presence of small voids or pores within the printed material can negatively impact both mechanical properties (especially fatigue strength) and thermal conductivity. Porosity can arise from gas entrapment (e.g., dissolved gases in the powder or shielding gas) or incomplete fusion between layers or scan tracks (lack-of-fusion porosity).
- Mitigation Strategies:
- High-Quality Powder: Using high-purity, spherical metal powders with low internal porosity and controlled particle size distribution, such as those produced via Met3dp’s advanced atomization, is fundamental for porosity control 3D printing. Poor quality powder is a common source of defects. See Met3dp’s product page for examples of high-grade powders.
- Optimized Process Parameters: Developing and using validated process parameters (laser power, speed, hatch distance, layer thickness) specific to the material (AlSi10Mg and CuCrZr behave differently) and machine is crucial to ensure complete melting and fusion.
- Inert Atmosphere Control: Maintaining a high-purity inert gas atmosphere (e.g., Argon, Nitrogen) in the build chamber minimizes oxidation and gas pickup during melting.
- Hot Isostatic Pressing (HIP): For critical applications requiring maximum density (>99.9%), HIP post-processing can be used to close internal pores through high pressure and temperature. However, it adds cost and lead time and can affect dimensions.
- NDT Inspection: CT scanning can detect internal porosity non-destructively.
- Support Structure Removal Issues:
- Challenge: While necessary, support structures can be difficult and time-consuming to remove, especially from complex internal channels or delicate features. Improper removal can damage the part surface or leave remnants that impede function (e.g., blocking channels). These support removal challenges are a common bottleneck.
- Mitigation Strategies:
- DfAM for Support Reduction: Design parts to be as self-supporting as possible (using angles > 45 degrees).
- Optimized Support Design: Use support types that are easier to remove (e.g., thinner contact points, perforated structures). Simulation tools can help optimize support placement for both stability and removability.
- Access Planning: Ensure adequate physical access for tools to reach support structures during the design phase. Avoid internal supports in channels unless absolutely necessary and designed for flushability or dissolution (rare in metals).
- Post-Processing Expertise: Skilled technicians with appropriate tools are needed for careful support removal.
- Achieving Desired Thermal Conductivity:
- Challenge: The final thermal conductivity AM parts achieve can sometimes be lower than the theoretical maximum for the wrought or cast alloy. This can be due to factors like residual porosity, non-equilibrium microstructures in the as-built state, or impurities.
- Mitigation Strategies:
- Maximize Density: Implementing strategies for porosity control (high-quality powder, optimized parameters, potentially HIP).
- Optimized Heat Treatment: Applying the correct stress relief and aging/solutionizing heat treatments is essential to develop the equilibrium microstructure that maximizes thermal conductivity, especially for CuCrZr.
- Material Certification & Testing: Sourcing powder with certified chemistry and potentially performing thermal conductivity testing on sample coupons printed with the final part parameters can verify performance.
- Powder Handling and Reuse:
- Challenge: Metal powders can degrade over time through handling and exposure to atmosphere (oxidation, moisture absorption). Reusing unsintered powder from previous builds is common practice to improve economics, but it must be done carefully to maintain quality. Improper powder management additive manufacturing can lead to inconsistent part quality.
- Mitigation Strategies:
- Controlled Environment: Store and handle powders in controlled, low-humidity environments.
- Sieving and Analysis: Sieve reused powder to remove any agglomerates or contaminants. Regularly analyze reused powder (e.g., chemistry, particle size distribution, flowability) to ensure it remains within specification.
- Blending Strategy: Implement a clear strategy for blending virgin and reused powder lots.
- Supplier Quality: Relying on suppliers like Met3dp who maintain strict quality control over their powder production ensures a high-quality starting material.
Addressing these challenges requires a combination of careful design, process simulation, high-quality materials, precise process control during printing, diligent post-processing, and rigorous quality inspection. Collaboration between designers and experienced AM providers is key to navigating these potential pitfalls and successfully producing robust and reliable heat flow enhancers for critical satellite thermal management applications.
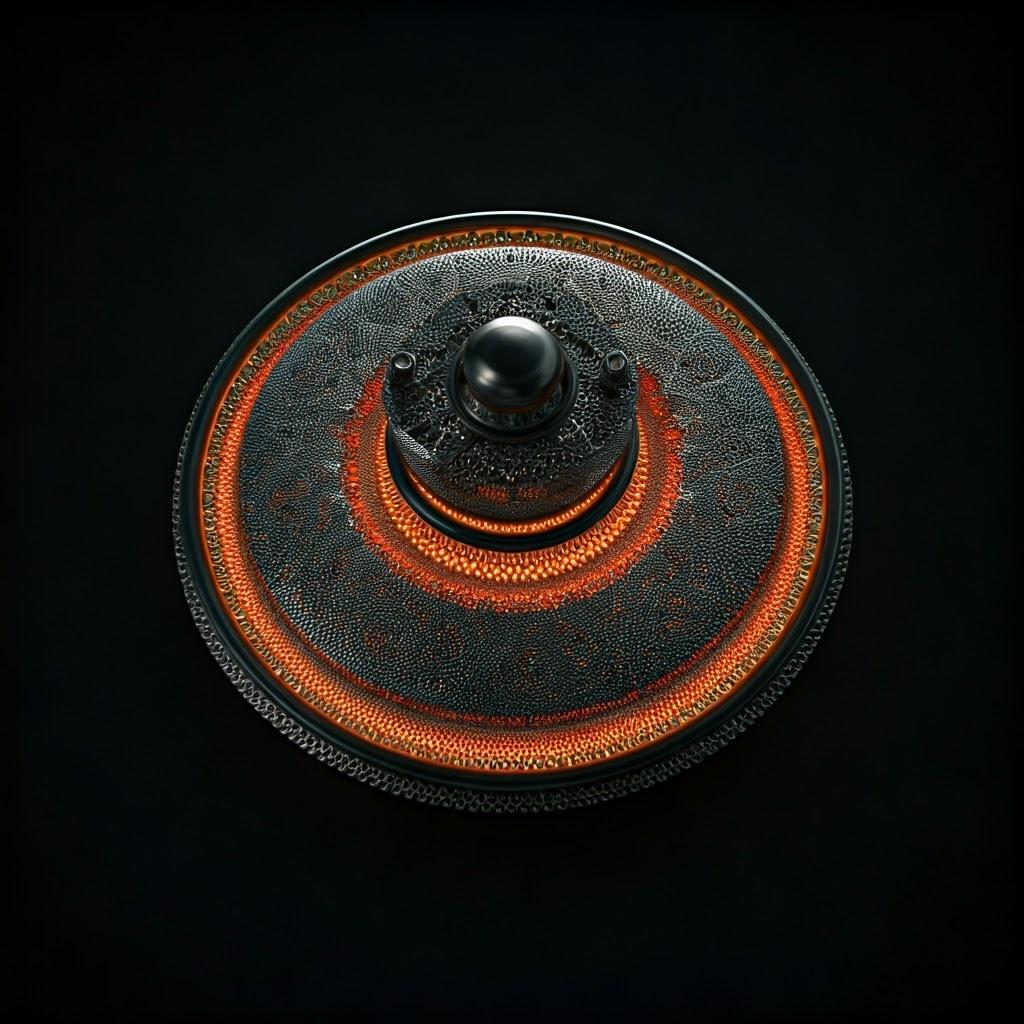
Choosing the Right Metal 3D Printing Service Provider for Aerospace Components
Selecting the appropriate manufacturing partner is a critical decision when sourcing high-performance components like satellite heat flow enhancers produced via metal additive manufacturing. The aerospace industry demands exceptional quality, reliability, and traceability, and not all AM service providers possess the necessary expertise, equipment, and certifications to meet these stringent requirements. Procurement managers and engineering teams must conduct thorough due diligence to identify a supplier capable of delivering flight-ready hardware consistently. Making the right choice ensures access to cutting-edge technology, material expertise, and process control necessary for mission success in demanding space systems.
Here are key criteria to consider when evaluating potential aerospace 3D printing services partners:
- Aerospace Experience and Certifications:
- Proven Track Record: Look for providers with demonstrable experience in producing components for aerospace and defense applications. Ask for case studies, references, or examples of similar projects (subject to confidentiality agreements). Understanding the specific challenges and quality expectations of the sector is crucial.
- Relevant Certifications: The AS9100 certification is the internationally recognized Quality Management System (QMS) standard for the aviation, space, and defense industries. AS9100 certified additive manufacturing providers demonstrate a commitment to rigorous process control, traceability, risk management, and continuous improvement aligned with aerospace requirements. While ISO 9001 is a good baseline, AS9100 provides a higher level of assurance specific to the sector. Other certifications related to specific processes (e.g., Nadcap for heat treatment or NDT) may also be relevant depending on the required post-processing steps.
- Material Expertise and Portfolio:
- Specialization in Relevant Alloys: Ensure the provider has proven, validated processes for the specific materials required, such as AlSi10Mg and CuCrZr for thermal applications. Don’t just look for listing the material; ask about their experience level, developed parameter sets, typical achieved properties (mechanical and thermal), and familiarity with aerospace specifications for these alloys.
- Powder Quality Control: Inquire about their powder sourcing and management protocols. Do they source from reputable suppliers? What are their procedures for powder handling, storage, testing (chemistry, PSD, flowability), and reuse to ensure consistency and prevent contamination? Companies like Met3dp, which manufacture their own high-quality metal powders using advanced gas atomization and PREP technologies, offer an advantage through vertical integration and direct control over this critical input material. This ensures traceability right from the raw material source.
- Material Development Capabilities: For cutting-edge applications, providers with R&D capabilities and experience in qualifying new or specialized alloys (like TiNi, TiTa, TiAl, TiNbZr, CoCrMo mentioned in Met3dp’s portfolio) can be valuable partners.
- Equipment Capabilities and Technology:
- Appropriate AM Technology: For high-resolution metal parts like heat enhancers, Laser Powder Bed Fusion (L-PBF) is commonly used. Some providers might also offer Electron Beam Melting (EBM), which has advantages for certain materials like titanium alloys (less residual stress) but typically produces rougher surfaces. Understand the specific machines the provider operates (manufacturer, model, age, maintenance status).
- Build Volume and Capacity: Ensure the provider’s machines have a build envelope large enough for your component dimensions and sufficient capacity to meet your required lead times, whether for prototypes or potential production volumes.
- Process Monitoring and Control: Advanced AM systems incorporate in-situ monitoring capabilities (e.g., melt pool monitoring, thermal imaging). Providers utilizing these tools demonstrate a higher level of process control and quality assurance. Ask about their process validation and parameter development methodologies.
- Comprehensive Post-Processing Capabilities:
- In-House vs. Partnered Services: As discussed previously, post-processing is critical. Determine which steps (stress relief/heat treatment, support removal, machining, surface finishing, coating, cleaning) the provider performs in-house versus outsourcing. In-house capabilities generally offer better control over lead times, quality, and communication.
- Expertise in Required Steps: Ensure the provider (or their qualified partners) has specific expertise in the necessary post-processing for your chosen material and application (e.g., vacuum heat treatment for aerospace alloys, precision CNC machining for tight tolerances, application of specific thermal control coatings satellite standards).
- Robust Quality Management System (QMS) and Inspection:
- Documentation and Traceability: Aerospace requires meticulous documentation. The provider’s QMS should ensure full traceability of materials (powder batches), process parameters, operator actions, post-processing steps, and inspection results for each part.
- Metrology Equipment: Verify they possess the necessary calibrated inspection equipment (CMM, 3D scanners, surface profilometers, NDT equipment like CT scanners if required) to validate that parts meet all dimensional, surface finish, and internal integrity requirements.
- Reporting: Understand the level of detail provided in quality reports and certificates of conformance.
- Technical Support and Engineering Expertise:
- DfAM Consultation: The ideal partner acts as more than just a print bureau. Look for providers offering Design for Additive Manufacturing (DfAM) consultation services. Their engineers can provide valuable feedback on your design to optimize it for printability, thermal performance, cost-effectiveness, and support minimization.
- Problem Solving: Experienced providers can help troubleshoot issues related to design, material selection, or manufacturing challenges.
- Location, Communication, and Logistics:
- Proximity: While not always the deciding factor, proximity can simplify logistics, facilitate site visits/audits, and potentially reduce shipping times.
- Responsiveness and Communication: Evaluate the provider’s responsiveness to inquiries, clarity of communication, and project management approach. A strong working relationship is essential.
Why Consider Met3dp?
Met3dp, headquartered in Qingdao, China, positions itself as a leading provider of comprehensive additive manufacturing solutions, aligning well with many of these critical selection criteria. Key strengths include:
- Integrated Solutions: Offering both industry-leading print volume, accuracy and reliability in their metal 3D printing equipment (including SEBM printers) and high-performance Met3dp metal powders.
- Advanced Powder Production: Utilizing state-of-the-art gas atomization and PREP technologies ensures high-quality, spherical powders crucial for demanding applications.
- Material Portfolio: Expertise across a range of materials including standard aerospace alloys and innovative compositions.
- Decades of Expertise: Collective experience in metal AM provides a strong foundation for technical support and application development.
- Commitment to Quality: Emphasis on accuracy, reliability, and enabling mission-critical parts for industries like aerospace.
By carefully evaluating potential suppliers against these criteria, focusing on aerospace-specific needs, and considering the integrated capabilities offered by companies like Met3dp, organizations can confidently select a metal AM supplier evaluation partner capable of delivering high-quality, reliable satellite heat flow enhancers that contribute to overall mission success.
Cost Factors and Lead Time for 3D Printed Satellite Heat Enhancers
While metal additive manufacturing enables the creation of highly optimized and complex satellite components, understanding the associated cost structure and typical lead times is essential for effective project planning, budgeting, and procurement. Both metal 3D printing cost and turnaround time can differ significantly from traditional manufacturing methods and are influenced by a multitude of factors specific to the AM process and the component itself. Communicating clear requirements and obtaining detailed quotes from qualified suppliers is key to managing expectations.
Key Cost Drivers for AM Satellite Heat Enhancers:
- Part Volume and Complexity:
- Material Consumption: The sheer volume of the part directly impacts the amount of expensive, high-quality metal powder (e.g., AlSi10Mg, CuCrZr) consumed. This is often a primary cost driver.
- Geometric Complexity: While AM excels at complexity, highly intricate designs with fine features, thin walls, or extensive internal channeling can increase print time and potentially lead to higher failure rates during printing or post-processing, influencing cost. Designs requiring extensive support structures also add to material usage and print time.
- Build Time (Machine Time):
- Part Height (Z-Height): Since AM builds layer by layer, the height of the part in the build orientation is a major determinant of the total print time. Taller parts take longer.
- Part Volume & Density: Larger volume parts require more scanning by the laser/electron beam per layer.
- Number of Parts per Build: Machine time cost can be amortized if multiple parts (yours or other customers’) can be nested efficiently onto a single build platform. Print-on-demand for single complex prototypes will carry a higher machine-time cost per part compared to a small batch run.
- Layer Thickness: Thinner layers improve surface finish but significantly increase the number of layers and thus the build time.
- Material Type:
- Powder Cost: The raw material powder cost varies significantly between alloys. Aerospace-grade powders like CuCrZr or specialized titanium alloys are generally more expensive than more common AlSi10Mg or stainless steels due to raw material costs and processing complexity. The quality (sphericity, purity, PSD control) demanded for aerospace applications also commands a premium.
- Processing Difficulty: Some materials (like highly reflective copper alloys) are more challenging to process reliably via L-PBF, potentially requiring specialized equipment or parameters, which can influence cost.
- Support Structure Requirements:
- Volume: Supports consume material and add to the overall volume being printed, increasing print time.
- Removal Effort: Complex or difficult-to-access supports significantly increase the labor time and cost associated with post-processing. Designs optimized to minimize supports (DfAM) can yield substantial cost savings.
- Post-Processing Intensity:
- Heat Treatment: Required cycles (stress relief, aging, etc.) add time, utilize specialized equipment (vacuum furnaces), and consume energy.
- Machining: The extent of CNC machining needed for tolerances or features significantly impacts cost (machine time, tooling, programming, setup).
- Surface Finishing: Steps like bead blasting, polishing, or coating application add labor and potentially specialized processing costs.
- Cleaning & Inspection: Rigorous aerospace quality control requirements, including detailed inspection (CMM, NDT) and documentation, contribute significantly to the final cost compared to less critical industrial parts.
- Quality Requirements and Qualification:
- Testing: Destructive testing of witness coupons (for mechanical or thermal properties) or extensive NDT on the final part adds cost.
- Documentation: Generating comprehensive traceability and quality documentation packages required for flight hardware takes time and resources.
- Process Qualification: If specific process qualification or validation runs are required for a new component or supplier, these upfront costs must be factored in.
- Order Volume (Quantity):
- Economies of Scale: While AM is often touted for low-volume production, some economies of scale still apply. Setup costs (build preparation, programming) can be amortized over larger batches. Optimized nesting on build plates becomes more efficient. However, the cost reduction per part is generally less dramatic than with traditional mass production techniques like casting or injection molding.
Understanding Quoting Models:
Providers may use different models for additive manufacturing pricing:
- Cost per Part: A fixed price for each successfully produced and inspected component.
- Cost per Build: Price based on occupying the build platform, regardless of success, plus post-processing. More common in R&D settings.
- Time and Materials: Charging based on actual machine time used and material consumed. Less common for production parts.
It’s crucial to get detailed quotes outlining what is included (material, printing, standard post-processing, inspection) and what might be additional (complex machining, specialized coatings, extensive NDT, qualification efforts). Requesting a B2B 3D printing quote from qualified suppliers like Met3dp, providing a clear 3D model and technical drawing with all requirements, is the best way to get accurate pricing.
Lead Time Factors:
Satellite hardware lead time for AM components is influenced by:
- Design Complexity: Complex parts take longer to print and post-process.
- Printing Queue: The service provider’s machine availability and backlog. Urgent orders may incur expedite fees.
- Build Time: As discussed, primarily driven by part height and volume. Can range from hours to several days or even weeks for very large/complex builds.
- Post-Processing Steps: Each step (heat treatment, machining, finishing, inspection) adds time. Heat treatment cycles can take hours to days; complex machining can take days. Support removal can be a bottleneck.
- Testing and Qualification: If extensive testing or qualification is needed, this adds significant time.
- Shipping: Logistics time to get the part from the provider to your facility.
Typical Lead Times:
- Prototypes: Simple prototypes might be delivered in 1-3 weeks.
- Complex Prototypes/Low Volume: Parts requiring significant post-processing or made from challenging materials could take 4-8 weeks or longer.
- Production Parts: Depends heavily on volume, complexity, and required qualification/documentation, potentially extending to several months for initial production runs requiring process stabilization and full qualification.
Cost-Effectiveness vs. Traditional Methods:
AM is most cost-effective compared to traditional methods (like CNC machining from billet) in scenarios involving:
- High Geometric Complexity: Where machining would be extremely difficult or impossible.
- Low-to-Medium Volume Production: Where tooling costs for casting/molding are prohibitive.
- Part Consolidation: Where assembly savings and improved reliability offset higher per-part AM cost.
- Lightweighting: Where the value of mass savings (especially launch cost reduction) outweighs the manufacturing cost premium.
- Rapid Prototyping: Where speed is paramount.
For simple geometries produced in high volumes, traditional methods often remain more economical. However, for the intricate, optimized designs needed for advanced satellite heat flow enhancers, AM frequently offers the best combination of performance, lead time, and overall value, especially when considering the total lifecycle and mission impact.
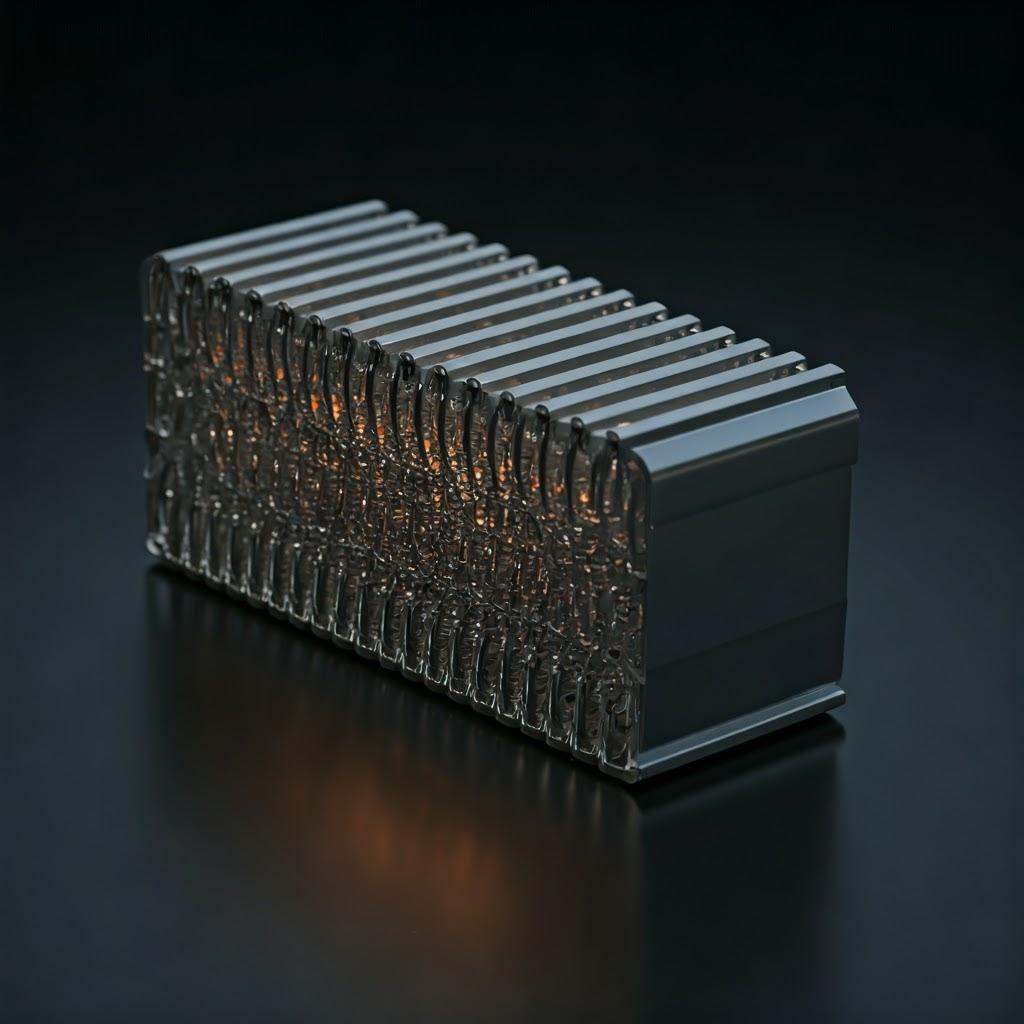
Frequently Asked Questions (FAQ)
Here are answers to some common questions regarding 3D printed satellite heat flow enhancers using AlSi10Mg and CuCrZr:
Q1: What is the typical thermal conductivity achievable for 3D printed AlSi10Mg and CuCrZr?
- A1: The achievable thermal conductivity depends heavily on the alloy, the printing process parameters, the resulting part density, and, most importantly, the post-print heat treatment.
- AlSi10Mg: In the as-built state, thermal conductivity might be relatively low (e.g., 90-110 W/m·K). After appropriate stress relief and potentially a T6-like heat treatment (optimized for thermal properties, which might differ slightly from treatments optimized solely for strength), thermal conductivity typically increases significantly, reaching values in the range of 100-130 W/m·K, sometimes higher depending on the specific process and treatment. Achieving >99.5% density is crucial.
- CuCrZr: This alloy relies on precipitation hardening via heat treatment (solutionizing and aging) to achieve both high strength and high conductivity. In the as-built state, conductivity is lower. After optimized heat treatment, CuCrZr printed via L-PBF can achieve excellent thermal conductivity, typically in the range of 300-320 W/m·K, approaching values close to wrought C18150 alloy. Again, achieving near-full density and applying the correct heat treatment validated for the AM process are critical. It’s essential to discuss target thermal conductivity requirements with the AM provider, as they should have data based on their validated processes and heat treatments for these specific aerospace metal powders.
Q2: How does the weight of 3D printed heat enhancers compare to traditionally manufactured ones?
- A2: Metal 3D printing offers significant potential for lightweighting aerospace components, including heat enhancers, compared to traditional methods, primarily through two mechanisms:
- Topology Optimization and Complex Geometries: AM allows the creation of highly optimized shapes (like lattice structures or topology-optimized designs) that place material only where it’s needed for structural support or thermal function. This can drastically reduce volume and mass compared to subtractively manufacturing from a solid block or assembling simpler shapes. A heat sink designed using DfAM principles can often perform the same or better thermally while being 20-50% lighter (or even more in some cases) than a traditionally designed and manufactured counterpart.
- Part Consolidation: By integrating multiple functions (e.g., structure, thermal path, mounting) into a single printed part, AM eliminates the need for fasteners, brackets, and interface materials, further reducing overall assembly weight.
- Material Choice: While CuCrZr is dense, the ability to create highly efficient, complex structures means less material volume might be needed compared to a simpler, bulkier copper part made traditionally. When using AlSi10Mg, the inherent low density combined with topology optimization can lead to extremely lightweight thermal solutions. Therefore, 3D printed heat enhancers are often significantly lighter than traditionally manufactured equivalents offering similar thermal performance.
Q3: Are 3D printed metal parts suitable for the vacuum and radiation environment of space?
- A3: Yes, metal components produced via additive manufacturing using alloys like AlSi10Mg and CuCrZr are generally well-suited for the space environment, provided they are properly processed and cleaned.
- Vacuum Compatibility: Metals inherently have very low vapor pressures and, when properly cleaned to remove organic residues and contaminants, exhibit low outgassing rates compatible with space vacuum requirements (typically defined by standards like NASA-STD-6016 or ECSS-Q-ST-70-02C). Ensuring high density (>99.5%) minimizes virtual leaks from internal porosity. Thorough post-processing cleaning procedures are crucial.
- Radiation Resistance: Metallic alloys are generally robust against the types and levels of radiation encountered in most Earth orbits (protons, electrons, gamma rays). Unlike polymers or some electronic components, the structural and thermal properties of AlSi10Mg and CuCrZr are not significantly degraded by typical space radiation doses over common mission lifetimes. Shielding effects of the metal itself also offer some protection to internal components.
- Thermal Cycling: The wide temperature swings in space require materials with stable properties across the operating range and resistance to thermal fatigue. While residual stress from AM needs careful management (via heat treatment), the base metals themselves handle thermal cycling well. The Coefficient of Thermal Expansion (CTE) matching with interfacing components is an important design consideration.
Q4: What quality certifications should I look for in a supplier for aerospace parts?
- A4: When selecting a metal AM supplier evaluation partner for critical aerospace components, specific quality certifications provide assurance of robust processes and controls:
- AS9100: This is the gold standard QMS for the aerospace industry. Certification to AS9100 indicates the supplier has implemented rigorous controls for configuration management, traceability, risk management, process validation, and defect prevention specific to aerospace requirements. It’s highly recommended for flight hardware.
- ISO 9001: A general QMS certification, forming the foundation for AS9100. While good, it lacks the specific aerospace focus of AS9100.
- Nadcap: While AS9100 covers the overall system, Nadcap provides accreditation for specific special processes. If your component requires critical post-processing like heat treatment, welding, or non-destructive testing performed by the AM provider or their subcontractors, look for relevant Nadcap accreditations for those specific processes.
- ITAR Registration (if applicable): For defense-related projects subject to US International Traffic in Arms Regulations, ensure the provider is ITAR registered and compliant.
- Specific Customer Approvals: Major aerospace OEMs often have their own supplier approval processes and requirements that may go beyond standard certifications.
Q5: Can Met3dp handle both prototyping and production volumes for these components?
- A5: Based on Met3dp’s stated capabilities, they appear positioned to support both phases. They highlight:
- Industry-leading print volume, accuracy, and reliability: Suggests equipment suitable for repeatable production.
- Comprehensive solutions: Spanning printers, advanced metal powders, and application development implies support throughout the product lifecycle from concept to manufacturing.
- Partnership approach: Willingness to partner with organizations to implement 3D printing and accelerate digital manufacturing transformations indicates readiness for ongoing production relationships.
- Expertise: Decades of collective expertise enables them to support initial DfAM for prototypes through to process optimization for scaled production. While specific capacity details would require direct inquiry, their focus on industrial applications in aerospace, medical, and automotive sectors suggests they are equipped to handle the quality demands and potentially the volumes required for series production of critical components, moving beyond just one-off prototypes. Discussing specific volume requirements and production roadmaps directly with Met3dp would clarify their capacity and scaling capabilities for your project.
Conclusion: Enhancing Space Mission Success with Advanced Additive Manufacturing
The relentless pursuit of higher performance, increased efficiency, and greater reliability in satellite technology necessitates continuous innovation in every aspect of spacecraft design, particularly in critical areas like thermal management. As we’ve explored, metal additive manufacturing represents a paradigm shift, offering unprecedented capabilities to address the complex challenges of dissipating heat in the harsh environment of space. By leveraging the design freedom inherent in AM, engineers can create 3D printed structures for heat redistribution using advanced materials like AlSi10Mg and CuCrZr that outperform conventionally manufactured components in terms of thermal efficiency, weight, and integration.
The ability to produce highly complex internal channels, topology-optimized geometries, conformal surfaces, and integrated multifunctional components allows for significant improvements in satellite thermal control. This translates directly into tangible benefits: electronic components can operate reliably at higher power levels, sensitive instruments maintain stable operating temperatures, and overall satellite mass can be reduced, freeing up capacity for more payload or enabling launches on smaller, less expensive vehicles. The advantages extend beyond performance; AM facilitates part consolidation satellite designs, reducing assembly complexity and potential failure points, while rapid prototyping space hardware capabilities accelerate development cycles, allowing faster iteration and validation of novel thermal solutions.
Materials like lightweight AlSi10Mg provide excellent thermal performance where mass is paramount, while high-conductivity CuCrZr tackles extreme heat flux challenges. The key to unlocking the full potential of these materials lies in utilizing high-quality, specifically engineered aerospace metal powders and partnering with expert AM providers who possess validated processes, rigorous quality control, and comprehensive post-processing capabilities. From DfAM thermal management consultation through meticulous inspection and finishing, the entire manufacturing chain must be geared towards the exacting standards of the aerospace industry.
Choosing the right manufacturing partner, one with proven aerospace experience, relevant certifications like AS9100, deep material knowledge, and advanced technological capabilities, is paramount. Companies like Met3dp, offering end-to-end solutions from advanced Powder Making System technology delivering superior Met3dp metal powders to state-of-the-art printing equipment and application expertise, are enabling the future of satellite thermal management. Their commitment to accuracy, reliability, and partnership helps organizations navigate the complexities of adopting AM for mission-critical applications.
In conclusion, metal AM is no longer just a prototyping tool; it is a mature manufacturing technology driving additive manufacturing aerospace innovation. For satellite heat flow enhancers and redistribution structures, it offers a compelling value proposition, enabling lighter, more efficient, and more reliable thermal management solutions that directly contribute to space mission success. As the technology continues to evolve, its role in enabling next-generation space systems will only grow. We encourage engineers and procurement managers facing thermal challenges in satellite design to explore the possibilities offered by metal additive manufacturing and engage with knowledgeable partners to turn innovative concepts into flight-ready reality. Visit the Met3dp homepage to learn more about their comprehensive solutions and how they can power your organization’s additive manufacturing goals.
Share On
MET3DP Technology Co., LTD is a leading provider of additive manufacturing solutions headquartered in Qingdao, China. Our company specializes in 3D printing equipment and high-performance metal powders for industrial applications.
Inquiry to get best price and customized Solution for your business!
Related Articles
About Met3DP
Recent Update
Our Product
CONTACT US
Any questions? Send us message now! We’ll serve your request with a whole team after receiving your message.
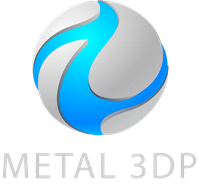
Metal Powders for 3D Printing and Additive Manufacturing