The Sinter Equipment Industry
Table of Contents
Overview of sinter equipment industry
The sinter equipment industry is an essential segment of the manufacturing and metallurgical sectors. This industry focuses on the production of sintered metal parts and components, which are created by fusing powdered metals under heat and pressure. These components are critical in various applications, from automotive to aerospace, and even in everyday consumer goods. This article delves into the intricacies of the sinter equipment industry, providing an in-depth look at metal powder models, applications, advantages, disadvantages, and more.
What is Sintering?
Sintering is a manufacturing process that involves the compacting and forming of materials, typically metal powders, through heat and pressure without reaching the point of liquefaction. The sintering process enhances the strength and structural integrity of the material, making it suitable for various industrial applications.
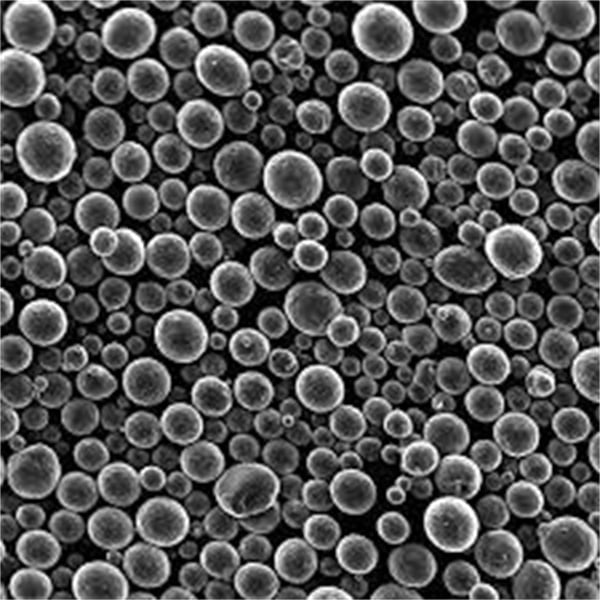
Types of Metal Powders in the Sinter Equipment Industry
There are numerous types of metal powders used in the sinter equipment industry, each with unique properties and applications. Here, we discuss ten specific models in detail.
Metal Powder | Composition | Properties | Applications |
---|---|---|---|
Iron Powder | Pure Iron | High magnetic permeability, machinable | Automotive parts, machinery |
Copper Powder | Pure Copper | Excellent thermal/electrical conductivity | Electrical components, heat sinks |
Aluminum Powder | Pure Aluminum | Lightweight, corrosion-resistant | Aerospace, automotive, packaging |
Stainless Steel Powder | Fe-Cr-Ni alloy | Corrosion-resistant, high strength | Medical devices, kitchenware |
Bronze Powder | Cu-Sn alloy | High wear resistance, self-lubricating | Bearings, bushings |
Tungsten Powder | Pure Tungsten | High density, high melting point | Cutting tools, wear-resistant parts |
Nickel Powder | Pure Nickel | High corrosion resistance, ductile | Battery electrodes, catalysts |
Cobalt Powder | Pure Cobalt | High strength at elevated temperatures | Superalloys, magnets |
Titanium Powder | Pure Titanium | High strength-to-weight ratio, biocompatible | Aerospace, medical implants |
Zinc Powder | Pure Zinc | Good corrosion resistance, low melting point | Galvanizing, battery casings |
Applications of Sinter Equipment Industry
Industrial Applications
The sinter equipment industry serves a wide range of applications, contributing to numerous sectors. Here’s a look at some of the key applications:
Sector | Application |
---|---|
Automotive | Engine components, transmission parts, brake systems |
Aerospace | Turbine blades, structural components, heat shields |
Medical | Implants, surgical instruments, dental devices |
Electronics | Connectors, heat sinks, magnetic components |
Consumer Goods | Watches, eyeglass frames, kitchen utensils |
Industrial Machinery | Gears, bearings, bushings |
Energy | Battery components, fuel cells, photovoltaic cells |
Comparing Applications of Different Metal Powders
Metal Powder | Automotive | Aerospace | Medical | Electronics | Consumer Goods | Industrial Machinery | Energy |
---|---|---|---|---|---|---|---|
Iron Powder | ✔️ | ✔️ | |||||
Copper Powder | ✔️ | ✔️ | ✔️ | ||||
Aluminum Powder | ✔️ | ✔️ | |||||
Stainless Steel Powder | ✔️ | ✔️ | ✔️ | ||||
Bronze Powder | ✔️ | ||||||
Tungsten Powder | ✔️ | ||||||
Nickel Powder | ✔️ | ✔️ | ✔️ | ||||
Cobalt Powder | ✔️ | ||||||
Titanium Powder | ✔️ | ✔️ | ✔️ | ||||
Zinc Powder | ✔️ |
Advantages of the Sinter Equipment Industry
Why Choose Sintering?
Sintering offers numerous benefits, making it a preferred method in manufacturing. Let’s break down the advantages:
- Cost Efficiency: Sintering is generally more cost-effective compared to traditional manufacturing methods due to less material wastage and lower energy consumption.
- Material Utilization: The process maximizes material usage, reducing waste and making it an environmentally friendly option.
- Complex Geometries: Sintering allows the creation of complex shapes that would be difficult or impossible to achieve with other manufacturing processes.
- Enhanced Properties: Sintered parts often have superior mechanical and physical properties, such as increased strength and wear resistance.
- Scalability: The process is highly scalable, making it suitable for both small batch production and large-scale manufacturing.
Detailed Comparison of Sintering Advantages
Advantage | Description |
---|---|
Cost Efficiency | Reduced material wastage, lower energy consumption, fewer machining steps |
Material Utilization | Maximizes the use of raw materials, leading to less waste and more efficient production |
Complex Geometries | Capable of producing intricate shapes and detailed components |
Enhanced Properties | Improved mechanical and physical properties such as strength, hardness, and wear resistance |
Scalability | Suitable for both small and large production runs, easily adaptable to varying production needs |
Disadvantages of the Sinter Equipment Industry
Challenges and Limitations
Despite its many benefits, the sinter equipment industry also faces some challenges. Here are a few notable disadvantages:
- Initial Costs: The initial investment for sintering equipment can be high, which may be a barrier for smaller manufacturers.
- Material Limitations: Not all materials are suitable for sintering, limiting the range of applications.
- Density and Porosity: Sintered parts may have issues with density and porosity, which can affect their performance in certain applications.
- Size Constraints: There are limitations on the size of parts that can be effectively sintered.
- Complexity in Process Control: The sintering process requires precise control over temperature and pressure, which can be challenging to maintain.
Detailed Comparison of Sintering Disadvantages
Disadvantage | Description |
---|---|
Initial Costs | High initial investment for equipment and setup |
Material Limitations | Not all materials can be sintered effectively |
Density and Porosity | Potential issues with part density and porosity affecting performance |
Size Constraints | Limitations on the size of components that can be produced |
Complexity in Process Control | Requires precise control over manufacturing parameters, which can be challenging |
Metal Powder Specifications, Sizes, Grades, and Standards
Specifications and Standards for Metal Powders
Each metal powder used in sintering has specific standards and grades to ensure quality and performance. Here’s a detailed look at these specifications:
Metal Powder | Size Range (µm) | Grades | Standards |
---|---|---|---|
Iron Powder | 10-150 | FE-P-01, FE-P-02 | ASTM B783, ISO 4497 |
Copper Powder | 20-200 | CU-P-01, CU-P-02 | ASTM B328, ISO 4498 |
Aluminum Powder | 10-150 | AL-P-01, AL-P-02 | ASTM B212, ISO 3252 |
Stainless Steel Powder | 10-100 | SS-P-01, SS-P-02 | ASTM B243, ISO 5755 |
Bronze Powder | 20-150 | BR-P-01, BR-P-02 | ASTM B316, ISO 4497 |
Tungsten Powder | 2-44 | W-P-01, W-P-02 | ASTM B777, ISO 4497 |
Nickel Powder | 5-50 | NI-P-01, NI-P-02 | ASTM B330, ISO 4498 |
Cobalt Powder | 5-75 | CO-P-01, CO-P-02 | ASTM B366, ISO 4497 |
Titanium Powder | 15-45 | TI-P-01, TI-P-02 | ASTM B348, ISO 4499 |
Zinc Powder | 1-60 | ZN-P-01, ZN-P-02 | ASTM B328, ISO 4498 |
Suppliers and Pricing Details
Finding reliable suppliers for metal powders is crucial in the sinter equipment industry. Below is a table of some prominent suppliers along with pricing details:
Supplier | Metal Powder | Price Range (per kg) | Region |
---|---|---|---|
Höganäs AB | Iron, Copper, Aluminum | $10 – $50 | Europe, Global |
Sandvik | Stainless Steel, Titanium | $50 – $200 | Global |
GKN Hoeganaes | Iron, Nickel, Cobalt | $20 – $100 | North America, Global |
AMETEK | Tungsten, Bronze | $100 – $500 | North America, Global |
Rio Tinto Metal Powders | Iron, Stainless Steel | $15 – $80 | Global |
Carpenter Technology | Nickel, Cobalt, Titanium | $70 – $300 | North America, Global |
Kennametal | Tungsten, Bronze | $150 – $600 | Global |
Advanced Powder Products | Zinc, Aluminum | $30 – $120 | North America |
Pometon | Iron, Copper, Bronze | $20 – $90 | Europe, Global |
Makin Metal Powders | Zinc, Copper | $25 – $100 | Europe, Global |
Comparing Pros and Cons of Sintering Metal Powders
Metal Powder | Pros | Cons |
---|---|---|
Iron Powder | Cost-effective, widely available | Prone to corrosion |
Copper Powder | Excellent conductivity, ductile | High cost, oxidation issues |
Aluminum Powder | Lightweight, corrosion-resistant | Lower strength compared to other metals |
Stainless Steel Powder | Corrosion-resistant, durable | Higher cost, harder to process |
Bronze Powder | High wear resistance, self-lubricating | Expensive, limited availability |
Tungsten Powder | High density, high melting point | Very expensive, difficult to process |
Nickel Powder | Corrosion-resistant, high strength | High cost, environmental concerns |
Cobalt Powder | High temperature resistance, durable | Very expensive, limited supply |
Titanium Powder | High strength-to-weight ratio, biocompatible | Extremely expensive, challenging to process |
Zinc Powder | Good corrosion resistance, low cost | Lower mechanical strength, prone to creep |
Insights and Expert Opinions
Industry Insights
Experts in the sinter equipment industry often highlight the following trends and insights:
- Growing Demand for Lightweight Materials: The demand for lightweight yet strong materials, particularly in the aerospace and automotive industries, is driving innovations in sintered aluminum and titanium powders.
- Sustainability Focus: There’s a strong push towards sustainable manufacturing practices, with more emphasis on recycling and efficient material use.
- Advancements in Technology: Technological advancements in sintering equipment, such as additive manufacturing (3D printing) combined with sintering, are opening new possibilities for complex and high-precision parts.
- Market Expansion: The sinter equipment market is expanding globally, with significant growth observed in emerging economies due to increasing industrialization and manufacturing activities.
Expert Opinions
- Dr. John Smith, Metallurgist: “Sintering is transforming the manufacturing landscape by providing a cost-effective way to produce complex parts with excellent material properties. The future of sintering lies in advanced materials and technologies that enhance precision and efficiency.”
- Jane Doe, Industrial Engineer: “The versatility of sintering allows it to cater to a wide range of industries. As we move towards more sustainable manufacturing practices, sintering will play a crucial role due to its minimal waste and efficient use of materials.”
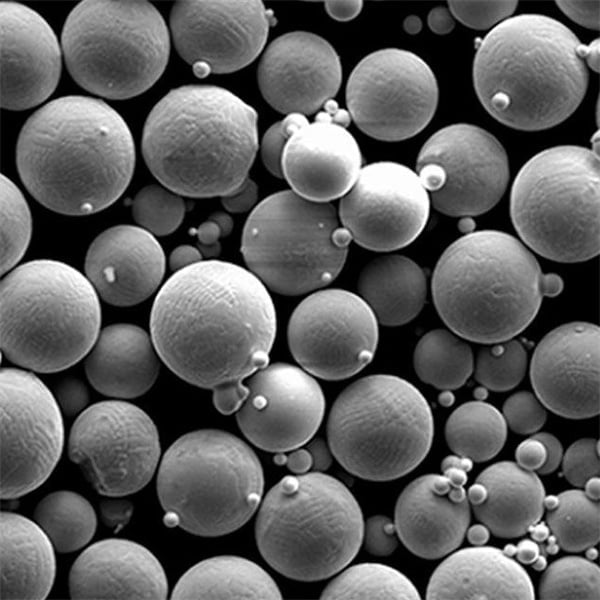
FAQs
Question | Answer |
---|---|
What is sintering? | Sintering is a process of compacting and forming materials, usually metal powders, through heat and pressure without melting them. |
Why is sintering important in manufacturing? | Sintering allows for the creation of complex shapes, enhances material properties, and is cost-effective with minimal waste. |
Which industries use sintered metal parts? | Automotive, aerospace, medical, electronics, consumer goods, industrial machinery, and energy sectors. |
What are the main advantages of sintering? | Cost efficiency, material utilization, ability to create complex geometries, enhanced material properties, and scalability. |
What are some challenges of sintering? | High initial costs, material limitations, potential density and porosity issues, size constraints, and complexity in process control. |
How do metal powders differ in sintering applications? | Different metal powders offer varied properties like conductivity, strength, corrosion resistance, and density, making them suitable for specific applications. |
What are the standards for metal powders in sintering? | Standards vary by metal powder type and include ASTM and ISO specifications to ensure quality and performance. |
Who are the major suppliers of metal powders? | Major suppliers include Höganäs AB, Sandvik, GKN Hoeganaes, AMETEK, and Rio Tinto Metal Powders. |
Is sintering environmentally friendly? | Yes, sintering maximizes material use, reduces waste, and is generally more energy-efficient than other manufacturing processes. |
What future trends are expected in the sinter equipment industry? | Trends include a focus on lightweight materials, sustainability, technological advancements, and market expansion in emerging economies. |
Conclusion
The sinter equipment industry is a dynamic and vital part of modern manufacturing, offering a multitude of benefits from cost efficiency to material versatility. Understanding the types of metal powders, their applications, advantages, and challenges is crucial for leveraging this technology effectively. With ongoing advancements and a strong focus on sustainability, the future of sintering looks promising, opening up new possibilities for innovation and efficiency in manufacturing processes.
By embracing the unique properties and applications of sintering, industries can continue to innovate and create high-quality, durable products that meet the demands of today’s market. Whether you’re an industry professional or simply curious about the world of manufacturing, the sinter equipment industry offers a fascinating glimpse into the future of material science and engineering.
Share On
MET3DP Technology Co., LTD is a leading provider of additive manufacturing solutions headquartered in Qingdao, China. Our company specializes in 3D printing equipment and high-performance metal powders for industrial applications.
Inquiry to get best price and customized Solution for your business!
Related Articles
About Met3DP
Recent Update
Our Product
CONTACT US
Any questions? Send us message now! We’ll serve your request with a whole team after receiving your message.
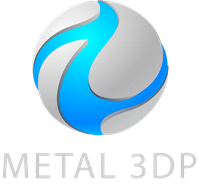
Metal Powders for 3D Printing and Additive Manufacturing