application of different Titanium Based Alloy Powder in Medical field
Table of Contents
Imagine a material that’s as strong as steel yet surprisingly light, like a featherweight champion. Imagine it being gentle on your body, like a soft touch. That’s the magic of Titanium Based Alloy Powder in the medical field.
They’re revolutionizing how doctors repair and replace damaged parts, offering patients a new lease on life. But with different types of titanium alloy powders available, understanding their properties is crucial. So, buckle up as we delve into the fascinating world of these medical marvels!
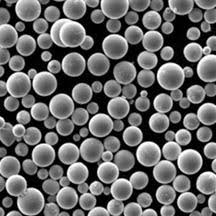
Classification of Titanium Alloy Powders by Chemical Composition
Titanium Based Alloy Powder aren’t created equal. Just like spices in a chef’s kitchen, adding different elements creates a spectrum of properties. Here’s a breakdown of some key classifications:
- Commercially Pure Titanium (CP Ti): This is the base metal, boasting excellent biocompatibility (meaning your body tolerates it well) and corrosion resistance. Think of it as the all-rounder, used for applications where strength isn’t the top priority.
- Titanium-Aluminum Alloys (Ti-Al): Here’s where things get interesting. Aluminum strengthens the titanium, making it ideal for load-bearing applications like artificial joints. The most common ones include:
- TA1 (Ti-0.8Al-0.4Mn): A good balance between strength and ductility (ability to bend without breaking). Imagine it as a flexible yet sturdy bridge.
- TA2 (Ti-2.5Al-1.6Fe): Even stronger than TA1, offering enhanced wear resistance. Think of it as a robust shield protecting your bones.
- TA4 (Ti-6Al): The heavyweight champion of the Ti-Al family, boasting the highest strength in this group. Imagine it as the dependable workhorse for demanding applications.
- Titanium-Aluminum-Vanadium Alloys (Ti-Al-V): Vanadium joins the party, further boosting strength and fatigue resistance (ability to withstand repeated stress). This makes them perfect for implants subjected to constant wear and tear, like:
- Ti6Al4V (Grade 23): The most widely used titanium alloy powder in medicine. It’s like the “gold standard” for its excellent combination of properties.
- Ti5Al2.5Sn (Grade 2): A good alternative to Ti6Al4V, offering slightly better corrosion resistance. Imagine it as the adaptable cousin, performing well in various medical scenarios.
- Other Specialized Alloys: The world of titanium alloy powders doesn’t stop there. Researchers are constantly innovating, developing alloys like:
- Ti6Al2Sn4Zr2Mo (Grade 24): This alloy offers superior creep resistance (ability to withstand deformation under stress at high temperatures). Think of it as the high-performance athlete, ideal for implants in hot environments (like near the heart).
- Ti10V2Fe3Al (Grade 7): This alloy boasts exceptional biocompatibility and good strength, making it suitable for bone screws and plates. Imagine it as the gentle giant, providing support without irritation.
- Shape Memory Alloys (SMAs): These are a whole new level of cool. Alloys like NiTi (Nickel-Titanium) can “remember” their original shape even after significant deformation. This makes them perfect for applications like self-expanding stents that open up blocked arteries.
Remember: This is just a glimpse into the vast world of titanium alloy powders. Each type offers unique advantages and applications, making them a versatile tool in the medical professional’s arsenal.
Typical Applications of TA1, TA2, and TA4 in Medical Device Manufacturing
Now that we’ve met the key players, let’s see them in action! TA1, TA2, and TA4, with their good balance of strength and biocompatibility, are commonly used for:
- Cranioplasty Plates and Mesh: These are used to repair skull fractures or correct cranial defects. Imagine TA1 as a gentle patch, providing support without weighing down the head.
- Maxillofacial Implants: Following facial injuries or surgeries, TA2’s strength comes into play, offering a reliable framework for facial reconstruction.
- Dental Implants: These tiny screws provide a foundation for artificial teeth. TA4’s strength ensures they can withstand the stress of chewing.
- Fracture Fixation Devices: These include bone screws and plates that hold fractured bones in place while they heal. TA1, TA2, and TA4, depending on the severity of the fracture, offer the necessary support for proper bone healing.
Beyond Strength: The Importance of Biocompatibility
It’s not just about being strong; when it comes to medical implants, your body’s happy acceptance is paramount. That’s where biocompatibility shines. Imagine placing a foreign object inside your body – ideally, it should feel like a welcome guest, not a hostile intruder. Titanium and its alloys excel in this department. Their surface chemistry closely resembles bone, minimizing the risk of rejection and inflammation. This translates to faster healing times and a reduced risk of complications for patients.
However, even within the biocompatible world of titanium alloys, there can be subtle differences. Here’s a breakdown:
- Commercially Pure Titanium (CP Ti): This champion of biocompatibility is the go-to choice for applications where minimizing tissue irritation is a top priority. Think of it as the ultimate peacemaker, fostering a harmonious relationship between implant and body.
- Titanium-Aluminum Alloys (Ti-Al): While generally biocompatible, the presence of aluminum can introduce a slight increase in the risk of periprosthetic osteolysis (bone loss around the implant). However, advancements in surface modification techniques are mitigating this concern. Imagine them as friendly neighbors, sometimes needing a little extra effort to get along perfectly.
- Titanium-Aluminum-Vanadium Alloys (Ti-Al-V): These workhorses offer a good balance between strength, biocompatibility, and cost-effectiveness. Ti6Al4V, the most widely used alloy, strikes a sweet spot between these factors. Think of it as the reliable friend, always there to support without causing major issues.
- Other Specialized Alloys: As research progresses, new alloys with enhanced biocompatibility are emerging. For example, Ti10V2Fe3Al boasts exceptional biocompatibility, making it ideal for applications like bone screws and plates that are in direct contact with bone. Imagine it as the considerate guest, taking extra care not to disturb its host.
The Importance of Osseointegration
Beyond biocompatibility lies a concept called osseointegration. This refers to the implant’s ability to form a direct bond with bone tissue. This strong connection is crucial for the long-term success of implants, particularly in load-bearing applications like artificial joints. The closer the implant mimics bone’s mechanical properties (like elasticity), the better the osseointegration. Here’s where the lower modulus of elasticity (MOE) of titanium alloys becomes a star player. Compared to stiffer materials like stainless steel, titanium’s MOE is closer to that of bone. This reduces stress shielding, a phenomenon where the implant takes on all the stress, leading to bone resorption (loss) around it. Imagine titanium as a supportive dance partner, moving in sync with the bone, not dominating it.
Choosing the Right Titanium Based Alloy Powder
Selecting the right titanium alloy powder for a medical device is a delicate balancing act. Factors like:
- Required Strength: For load-bearing applications like hip replacements, stronger alloys like Ti6Al4V are preferred.
- Biocompatibility Needs: For implants in sensitive areas like the jaw or near nerves, CP Ti or alloys with minimal aluminum content might be chosen.
- Corrosion Resistance: In some environments, like dental implants exposed to saliva, alloys with enhanced corrosion resistance like Ti5Al2.5Sn might be preferred.
- Fatigue Resistance: For implants subjected to constant wear and tear, like knee replacements, alloys with good fatigue resistance like Ti6Al4V are crucial.
The Future of Titanium Alloy Powders in Medicine
The story of titanium alloy powders in medicine is far from over. Here’s a glimpse into the exciting future:
- 3D Printing Revolution: Additive manufacturing (3D printing) is transforming how implants are made. Titanium alloy powders are perfectly suited for this technology, allowing for the creation of complex, customized implants that perfectly match a patient’s anatomy. Imagine 3D-printed implants as bespoke suits, tailor-made for each patient’s unique needs.
- Bioactive Surfaces: Researchers are developing surface treatments that enhance the interaction between implants and bone. This can promote faster osseointegration and potentially reduce the risk of infection. Imagine bioactive surfaces as a welcoming handshake between implant and bone, accelerating a strong connection.
- New Alloys for New Possibilities: The quest for even better biocompatible, stronger, and more versatile alloys continues. This opens doors for new medical applications, pushing the boundaries of what’s possible. Imagine new alloys as the next generation of superheroes in the medical field, offering even greater healing potential.
In conclusion, titanium alloy powders are revolutionizing the medical field. Their unique combination of strength, biocompatibility, and versatility is making a world of difference for patients. As technology advances, we can expect even more exciting developments in this field, paving the way for a healthier future for all.
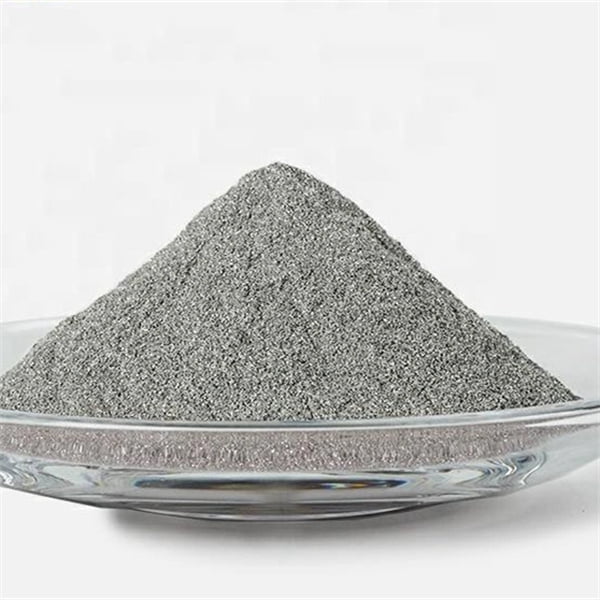
FAQ
Here’s a breakdown of some frequently asked questions regarding titanium alloy powders in medical applications, presented in a clear table format for easy reference:
Question | Answer |
---|---|
What are the advantages of using titanium alloy powders in medical devices? | Excellent biocompatibility: Minimizes rejection and inflammation, promoting faster healing. High strength-to-weight ratio: Strong yet lightweight, ideal for implants that need to withstand stress without adding bulk. Corrosion resistance: Resists corrosion in the body’s environment, ensuring long implant life. Fatigue resistance: Withstands repeated stress without breaking, crucial for long-term performance. Versatility: Different alloys offer a range of properties to suit specific needs. |
Are there any disadvantages to using titanium alloy powders in medical devices? | Cost: Titanium and its alloys can be more expensive than some other implant materials. Stiffness: While an advantage for strength, the stiffness of some alloys can lead to stress shielding, requiring careful selection. Brittleness: Certain alloys can be brittle, making them less suitable for applications requiring high impact resistance. |
How are titanium alloy powders used to create medical devices? | Titanium alloy powders are primarily used in a process called Additive Manufacturing (AM), also known as 3D printing. The powder is deposited layer-by-layer to create a three-dimensional object with a specific design. This allows for the creation of complex, customized implants that perfectly match a patient’s anatomy. |
What are some examples of medical devices made from titanium alloy powders? | Artificial joints (hips, knees, shoulders) Bone screws and plates for fracture fixation Cranioplasty plates and mesh for skull repair Maxillofacial implants for facial reconstruction Dental implants Spinal correctors and fusion cages Vascular stents to open blocked arteries Artificial heart valves |
How long do titanium alloy implants typically last? | With proper care, titanium alloy implants can last for many years, often exceeding 15-20 years. Factors like the type of implant, location in the body, and activity level can influence lifespan. |
What are some future advancements expected in the use of titanium alloy powders in medicine? | Development of new alloys: Alloys with even better biocompatibility, strength, and corrosion resistance are being explored. Bioactive surface treatments: Surface modifications that enhance osseointegration and reduce infection risk are being investigated. Advancements in 3D printing technology: More precise and efficient 3D printing techniques will enable the creation of even more complex and customized implants. Personalized medicine: Tailoring implants to individual patient needs based on their genetic makeup and anatomy. |
Share On
MET3DP Technology Co., LTD is a leading provider of additive manufacturing solutions headquartered in Qingdao, China. Our company specializes in 3D printing equipment and high-performance metal powders for industrial applications.
Inquiry to get best price and customized Solution for your business!
Related Articles
About Met3DP
Recent Update
Our Product
CONTACT US
Any questions? Send us message now! We’ll serve your request with a whole team after receiving your message.
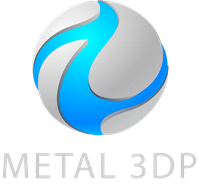
Metal Powders for 3D Printing and Additive Manufacturing