Titanium Powder 3D printer
Table of Contents
titanium powder 3d printer, also known as additive manufacturing (AM) with titanium powders, is a revolutionary technology that has gained significant traction in various industries, including aerospace, medical, and automotive sectors. This process involves selectively fusing layers of titanium powder using a high-energy source, such as a laser or an electron beam, to create intricate, lightweight, and high-strength components.
Unlike traditional manufacturing methods, titanium powder 3d printer offers unparalleled design freedom, enabling the creation of complex geometries and internal structures that would be challenging or impossible to produce using conventional techniques. This capability has opened up new avenues for innovation, allowing engineers and designers to push the boundaries of product development.
titanium powder 3d printer Equipment Guide
Titanium 3D printers are highly specialized machines that require precise control over the printing process and a controlled environment to ensure consistent and high-quality results. The following table outlines the key components and features of a typical titanium 3D printer:
Component | Description |
---|---|
Build Chamber | An enclosed, inert environment to prevent oxidation and maintain optimal printing conditions. |
Powder Delivery System | A mechanism for precisely depositing and distributing thin layers of titanium powder onto the build plate. |
High-Energy Source | A laser or electron beam source that melts and fuses the titanium powder layer by layer. |
Optics and Beam Control | Precision optics and beam control systems to focus and direct the high-energy source accurately. |
Motion Control System | Precise motion control systems to ensure accurate positioning and movement of the build plate and energy source. |
Temperature Control | Heated build plates and environmental controls to maintain optimal printing temperatures. |
Filtration and Extraction | Filtration systems to remove potentially hazardous powders and fumes from the build chamber. |
Software and Controls | Specialized software and control systems to manage and monitor the printing process. |
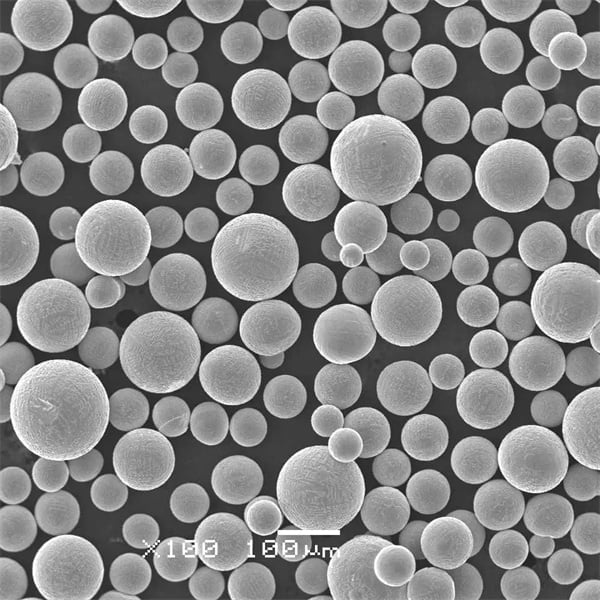
Types of titanium powder 3d printer
Titanium 3D printers can be broadly classified into two main categories based on the high-energy source used for melting the powder:
- Laser-Based Systems
- These systems use a high-powered laser to selectively melt and fuse the titanium powder layers.
- Examples: EOS M290, Renishaw AM400, and Concept Laser M2 Cusing.
- Electron Beam Melting (EBM) Systems
- These systems utilize a high-energy electron beam instead of a laser to melt the titanium powder.
- Examples: Arcam Q20plus, GE Additive Arcam EBM, and Sciaky EBAM systems.
Both laser-based and electron beam melting systems have their advantages and limitations, and the choice depends on factors such as part size, material properties, and production requirements.
The titanium powder 3d printer Process
The titanium 3D printing process typically follows these steps:
- Design and Preparation: A 3D model of the desired component is created using computer-aided design (CAD) software and then converted into a compatible file format for the 3D printer.
- Print Setup: The build chamber is prepared by preheating the build plate and creating an inert atmosphere, typically using argon or nitrogen gas.
- Powder Deposition: A thin layer of titanium powder is deposited onto the build plate using the powder delivery system.
- Melting and Fusion: The high-energy source (laser or electron beam) selectively melts and fuses the titanium powder in the desired areas, following the instructions from the CAD file.
- Layer Building: The build plate is lowered, and a new layer of powder is deposited. The process repeats, with the energy source melting and fusing the new layer to the previous one.
- Post-Processing: Once the printing is complete, the excess powder is removed, and the component may undergo additional post-processing steps, such as heat treatment, surface finishing, or machining, depending on the application requirements.
This layer-by-layer approach allows for the creation of intricate and complex geometries that would be challenging or impossible to produce using traditional manufacturing methods.
titanium powder 3d printer Capabilities and Customization
Capability | Description |
---|---|
Build Volume | Titanium 3D printers offer a wide range of build volumes, from compact desktop models to large-scale industrial systems. The build volume determines the maximum size of components that can be printed. |
Material Compatibility | While primarily designed for titanium alloys, some 3D printers can also process other metallic powders, such as stainless steel, aluminum, or nickel-based superalloys. |
Surface Finish | Advanced systems can achieve high-quality surface finishes, reducing or eliminating the need for post-processing operations. |
Resolution and Accuracy | High-resolution optics and precision motion control systems enable the production of components with intricate details and tight tolerances. |
Customization | Many manufacturers offer customizable solutions tailored to specific application requirements, including specialized build chambers, powder handling systems, or software integrations. |
titanium powder 3d printer Suppliers and Price Range
Titanium 3D printers are typically manufactured by specialized companies and can be a significant investment. The following table provides an overview of some leading suppliers and their approximate price ranges:
Supplier | Price Range (USD) |
---|---|
EOS GmbH | $500,000 – $1.5 million |
Renishaw plc | $500,000 – $1 million |
GE Additive | $1 million – $2 million |
Sciaky Inc. | $1 million – $3 million |
3D Systems | $500,000 – $1.5 million |
Please note that these prices are approximate and can vary based on specific configurations, additional features, and regional pricing. It’s always recommended to obtain detailed quotes from the suppliers based on your specific requirements.
Installation, Operation, and Maintenance
Aspect | Description |
---|---|
Installation | Titanium 3D printers require specialized installation, including the setup of environmental controls, power supply, and ventilation systems. Proper site preparation and compliance with safety regulations are crucial. |
Training | Comprehensive training is necessary for operators to ensure safe and efficient operation of the printer, as well as understanding the specific printing parameters and materials. |
Operation | Titanium 3D printing requires careful monitoring and control of various parameters, such as powder distribution, energy source settings, and environmental conditions, to achieve consistent and high-quality results. |
Maintenance | Regular maintenance is essential to ensure optimal performance and longevity of the printer. This includes cleaning, calibration, replacement of consumables (e.g., filters, powder handling components), and regular inspections. |
Safety | Strict safety protocols must be followed when handling titanium powders and operating the printer, including the use of personal protective equipment, proper ventilation, and adherence to safety guidelines. |
Choosing the Right Titanium 3D Printer Supplier
When selecting a titanium 3D printer supplier, consider the following factors:
Factor | Description |
---|---|
Expertise and Experience | Assess the supplier’s expertise and track record in titanium 3D printing, as well as their knowledge of specific industry applications and requirements. |
Product Range and Capabilities | Evaluate the supplier’s product portfolio and the capabilities of their titanium 3D printers to ensure they meet your specific needs and production requirements. |
Technical Support and Services | Reliable technical support, training, and maintenance services are crucial for successful implementation and ongoing operation of the printer. |
Quality and Certifications | Look for suppliers with established quality control processes, certifications (e.g., ISO 9001, AS9100), and a commitment to delivering high-quality products and services. |
Customer References | Request customer references and testimonials to gauge the supplier’s reputation, customer satisfaction, and the performance of their products in real-world applications. |
Total Cost of Ownership | Consider the initial purchase cost as well as ongoing operational costs, such as consumables, maintenance, and training, to evaluate the total cost of ownership over the printer’s lifespan. |
Pros and Cons of titanium powder 3d printer
Like any technology, titanium 3D printing has its advantages and limitations. It’s essential to weigh these factors carefully to determine if it’s the right solution for your specific application.
Advantages
- Design Freedom: Titanium 3D printing allows for the creation of complex geometries and internal structures that are difficult or impossible to manufacture using traditional methods.
- Weight Reduction: By optimizing designs and creating lightweight, lattice-like structures, titanium 3D printing can significantly reduce the weight of components, which is crucial in industries like aerospace and automotive.
- Material Efficiency: Additive manufacturing is inherently more material-efficient than subtractive processes, as it only uses the required amount of titanium powder, minimizing waste.
- Customization and Personalization: Titanium 3D printing enables the production of customized and personalized components, making it suitable for applications like medical implants and prosthetics.
- Rapid Prototyping: The ability to quickly produce functional prototypes and iterate designs can accelerate product development cycles and reduce time-to-market.
Limitations
- High Initial Investment: Titanium 3D printers and the associated equipment and infrastructure can be expensive, making it a significant capital investment for many organizations.
- Limited Build Size: While larger build volumes are available, most titanium 3D printers have a relatively small build area compared to traditional manufacturing methods, limiting the size of components that can be produced.
- Post-Processing Requirements: Printed components may require additional post-processing steps, such as heat treatment, surface finishing, or machining, which can add time and cost to the production process.
- Material and Process Restrictions: Titanium 3D printing is primarily suitable for titanium alloys and a limited range of other metallic powders, limiting material choices and applications.
- Skilled Workforce: Operating and maintaining titanium 3D printers requires specialized training and expertise, which can be challenging to acquire and retain.
It’s important to carefully evaluate your specific requirements, production volumes, and budget to determine if the advantages of titanium 3D printing outweigh the limitations and costs associated with the technology.
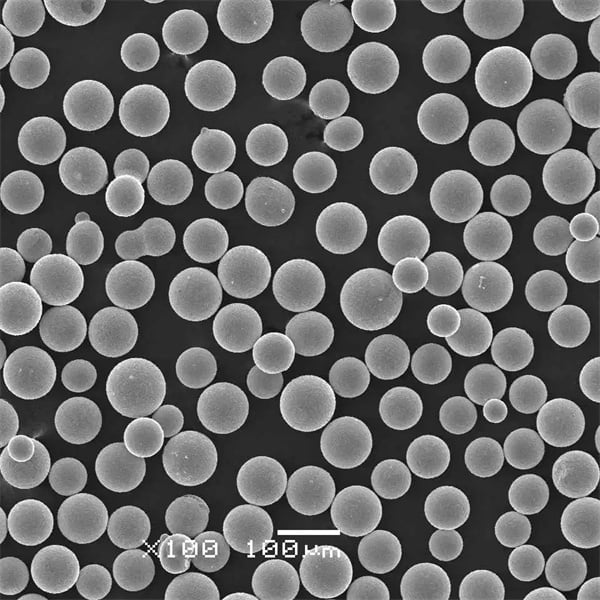
FAQ
Question | Answer |
---|---|
What are the typical applications of titanium 3D printing? | Titanium 3D printing is widely used in industries such as aerospace, medical, automotive, and energy sectors for producing lightweight, high-strength components, implants, and prototypes. |
What are the advantages of titanium over other metals in 3D printing? | Titanium offers excellent strength-to-weight ratio, corrosion resistance, and biocompatibility, making it suitable for demanding applications where these properties are crucial. |
How does the cost of titanium 3D printing compare to traditional manufacturing methods? | While the initial investment in titanium 3D printing can be high, it can be more cost-effective for producing complex geometries, small batch sizes, or customized components compared to traditional methods like machining or casting. |
What are the challenges associated with titanium 3D printing? | Challenges include managing the high temperatures required for melting titanium, preventing oxidation and contamination, ensuring consistent powder distribution, and achieving desired material properties in the printed components. |
How does the surface finish and mechanical properties of 3D printed titanium components compare to traditionally manufactured parts? | With proper process control and post-processing, 3D printed titanium components can achieve comparable or superior surface finish and mechanical properties to conventionally manufactured parts. |
What are the safety considerations when working with titanium powders and 3D printing? | Proper ventilation, personal protective equipment, and handling protocols are necessary due to the potential hazards associated with fine metal powders and the high-energy sources used in the printing process. |
How is the quality and consistency of 3D printed titanium components ensured? | Quality control measures include strict process monitoring, material testing, non-destructive evaluation techniques, and adherence to industry standards and certifications. |
What are the ongoing developments and future trends in titanium 3D printing? | Ongoing research and development focus on improving print speeds, achieving better material properties, expanding material compatibility, increasing build volumes, and integrating advanced process monitoring and control systems. |
Share On
MET3DP Technology Co., LTD is a leading provider of additive manufacturing solutions headquartered in Qingdao, China. Our company specializes in 3D printing equipment and high-performance metal powders for industrial applications.
Inquiry to get best price and customized Solution for your business!
Related Articles
About Met3DP
Recent Update
Our Product
CONTACT US
Any questions? Send us message now! We’ll serve your request with a whole team after receiving your message.
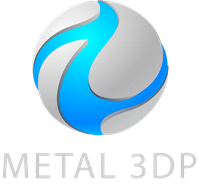
Metal Powders for 3D Printing and Additive Manufacturing