Titanium Powders Guide
Table of Contents
Titanium powders are finely divided metallic titanium particles used in various applications due to their unique properties like high strength-to-weight ratio, corrosion resistance, and biocompatibility. This guide provides a detailed overview of different types of titanium powders, their composition, properties, manufacturing methods, applications, and suppliers.
Overview of Titanium Powders
Titanium powders come in various purity levels, particle sizes, and morphologies for use in diverse applications across aerospace, automotive, chemical, medical, military, and other industries.
Key features that make titanium powders useful:
- High strength-to-weight ratio
- Excellent corrosion resistance
- Low density compared to other metallic materials
- Biocompatibility and non-toxicity
- Ability to withstand extreme temperatures
- High chemical stability across various environments
- Versatile manufacturing and processing options
With advancing technology, titanium powders with more controlled particle characteristics are being produced to meet application demands.
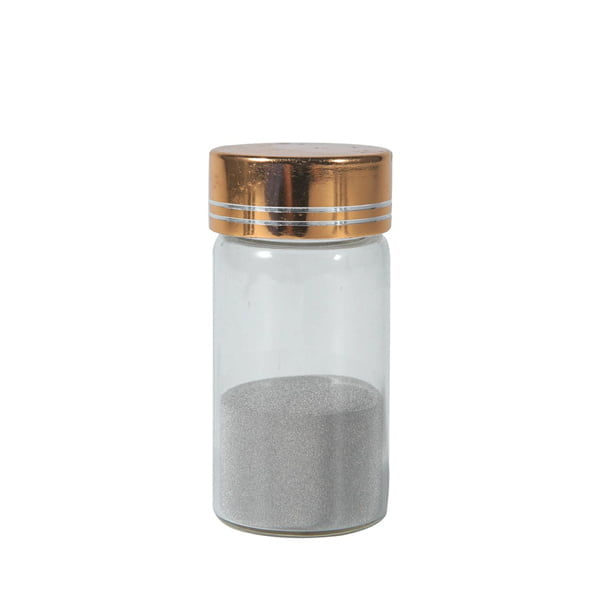
Types of Titanium Powders
Titanium powders can be categorized based on composition, production method, particle morphology, particle size distribution, and other parameters:
Titanium Powder Composition
Type | Purity | Key Elements |
---|---|---|
Commercially Pure Titanium | 99.5-99.9% Ti | Fe, C, N, O |
Ti-6Al-4V alloy | 90% Ti, 6% Al, 4% V | Al, V |
Ti-3Al-2.5V alloy | 97% Ti, 3% Al, 2.5% V | Al, V |
- Commercially pure titanium has higher corrosion resistance. Titanium alloys provide increased strength.
- Other alloying elements like molybdenum, zirconium, tin, silicon, copper, and chromium can also be present depending on required properties.
Titanium Powder Production Method
Method | Details | Particle Characteristics |
---|---|---|
Hydride-dehydride (HDH) | Ti sponge reacted with H2, then decomposed | Irregular morphology, wide size distribution |
Gas atomization | Molten Ti disintegrated by N2/Ar jets | Spherical, controlled size distribution |
Plasma atomization | Higher energy than gas atomization | Spherical, fine particles |
Electrode induction melting gas atomization (EIGA) | Combines induction skull melting with gas atomization | Spherical, controlled oxygen content |
- Gas-atomized powders have more spherical particles ideal for additive manufacturing whereas HDH powders are irregular.
- Plasma-atomized powders can produce finer particles below 15 microns.
Titanium Powder Particle Morphology
Type | Shape | Surface Texture |
---|---|---|
Irregular | Non-spherical random shapes | Rough surfaces |
Granular | Rounded with visible facets | Smooth with some pits |
Spherical | Very round overall | Very smooth |
- Particle shape influences powder flow, packing density, layer uniformity in AM processes.
- Smoother, spherical powders provide better performance in most metal AM systems.
Titanium Powder Particle Size Distribution
Titanium powders suitable for AM processes like laser powder bed fusion (L-PBF) and directed energy deposition (DED) have particle size distributions between:
- 15-45 microns
- 45-150 microns
Finer 15-45 micron powders allow higher resolution while coarser 45-150 powders minimize entrapped gases and improve flowability.
Properties of Titanium Powders
Key properties of titanium powders are:
Table: Titanium Powder Properties
Property | Details |
---|---|
Density | 4.5 g/cc |
Melting point | 1668°C |
Thermal conductivity | Low, 6.7 W/mK |
Electrical conductivity | Low, 0.4 MS/m |
Chemical reactivity | Forms stable oxide layer in air |
Mechanical strength | High strength-to-weight ratio |
Corrosion resistance | Resistant to wide variety of acids, chlorides, other chemicals |
at elevated temperatures | |
Biocompatibility | Excellent, non-toxic, non-allergenic |
- The oxide layer makes titanium resistant to corrosion and provides bio-inertness.
- Titanium has the highest strength-to-weight ratio among metals after beryllium.
- Alloying improves high temperature mechanical properties significantly.
Manufacturing Methods for Titanium Powders
Commonly used techniques to produce titanium powders include:
Table: Titanium Powder Manufacturing Methods
Method | Working Principle | Particle Characteristics |
---|---|---|
Hydride-dehydride (HDH) | Ti sponge is reacted with H<sub>2</sub> to form brittle TiH<sub>2</sub> which is crushed and decomposed to powder | Irregular shapes, wide size distribution |
Gas atomization | High velocity inert gas jets disintegrate molten titanium stream into droplets that solidify into powder | Spherical particles, controlled size distribution |
Plasma atomization | Similar to gas atomization but higher energy plasma arc used | Finer spherical particles, satellite formations |
Electrode Induction gas atomization (EIGA) | Combines induction melting in cold copper crucible with gas atomization | Finer particles, lower oxygen pickup |
Additional steps like sieving, deoxygenation or consolidation can further modify powders for specific applications.
Applications of Titanium Powders
Key applications taking advantage of titanium powder properties:
Table: Titanium Powder Applications
Industry | Application | Benefits |
---|---|---|
Aerospace | Forging, casting engine parts; AM of airframe, turbine components | High strength-to-weight ratio |
Chemical | Equipment like heat exchangers, tanks, pipes | Corrosion resistance |
Automotive | Valves, connecting rods, suspensions | Lightweight, durable |
Biomedical | Implants, prosthetics, devices | Biocompatibility, osseointegration |
Military | Ballistics armor plates, vehicles | High strength, low density |
Additive manufacturing | L-PBF of Ti-6Al-4V components for aerospace, automotive | Economic production of complex, lightweight parts |
- Biocompatibility allows titanium implant integration with minimal inflammatory response.
- Ability to 3D print intricate titanium components expands production flexibility.
In particular, titanium alloy Ti-6Al-4V dominates in aviation, medical implants, and metal AM applications due to its strength, workability and corrosion resistance combined with commercial availability.
Titanium Powder Specifications
Industrial titanium powders for AM and other applications need to conform to specifications for composition, particle size distribution, morphology, flow characteristics, impurity levels and other parameters.
Table: Titanium Powder Specifications
Parameter | Typical specification | Test method |
---|---|---|
Particle size | 15-45 μm; 45-150 μm | Laser diffraction, sieve |
Particle shape | Aspect ratio below 3 | Microscopy |
Apparent density | Above 2.5 g/cc | Hall flowmeter |
Tap density | Up to 4 g/cc | ASTM B527 |
Flow rate | 25-35 s/50g | Hall flowmeter |
Oxygen content | Below 0.2 wt% | Inert gas fusion |
Nitrogen content | Below 0.05 wt% | Inert gas fusion |
Hydrogen content | Below 0.0125 wt% | Inert gas fusion |
Meeting powder quality benchmarks ensures consistency, reliability and performance in AM production.
Suppliers of Titanium Powders
Key titanium powder manufacturers and suppliers globally include:
Table: Titanium Powder Suppliers
Company | Powder grades | Production methods |
---|---|---|
AP&C | Ti-6Al-4V, Ti-64 ELI, Ti Grade 2 | Plasma atomization |
TLS Technik | Ti-6Al-4V, Ti Grade 2, Ti Grade 5 | Gas atomization |
Praxair (T.I.P.) | CP Ti, Ti-6Al-4V | Multiple |
SLMP Mallory | CP Ti, Ti-6Al-4V | HDH, Gas atomization |
Carpenter Additive | Ti-6Al-4V | Gas atomization |
Sandvik | Multiple Ti alloys | Plasma atomization |
LPW Technology | CP Ti, Ti alloys | Plasma atomization |
Prices vary from $50/kg for irregular powder to over $1000/kg for highly spherical plasma atomized materials used in demanding applications like aerospace components.
Comparison of Titanium Powders
Table: Comparison of Titanium Powder Types
Parameter | HDH powder | Gas atomized | Plasma atomized |
---|---|---|---|
Particle shape | Irregular | Rounded | Highly spherical |
Size range (μm) | 50-250 | 15-150 | 5-45 |
Production cost | Low | Moderate | High |
Oxygen content | Higher | Lower | Lowest |
Uses | Press and sinter | Metal injection molding, hot isostatic pressing | AM (DED, L-PBF) |
HDH powders are less expensive but irregular particles limit use to press and sinter technologies while plasma atomized powder, despite high cost, provides excellent flow and melting properties for demanding additive manufacturing. Gas atomized powder offers a good balance for most applications.
Advantages and Limitations of Titanium Powders
Table: Advantages and Limitations of Titanium Powders
Advantages | Limitations |
---|---|
High strength-to-weight ratio | Expensive compared to steel |
Retains properties at elevated temperatures | Requires controlled atmosphere processing |
Resistant to wide range of chemicals | Low thermal conductivity |
Completely recyclable | Susceptible to contamination like oxygen pick-up |
Non-magnetic and non-sparking | Difficult to machine in certain alloy forms |
Readily fabricated into complex shapes | Limited supplier base especially for high grade powder |
Titanium’s merits make it suitable for specialized applications despite drawbacks like high cost and sensitivity to contamination during reuse or recycling.
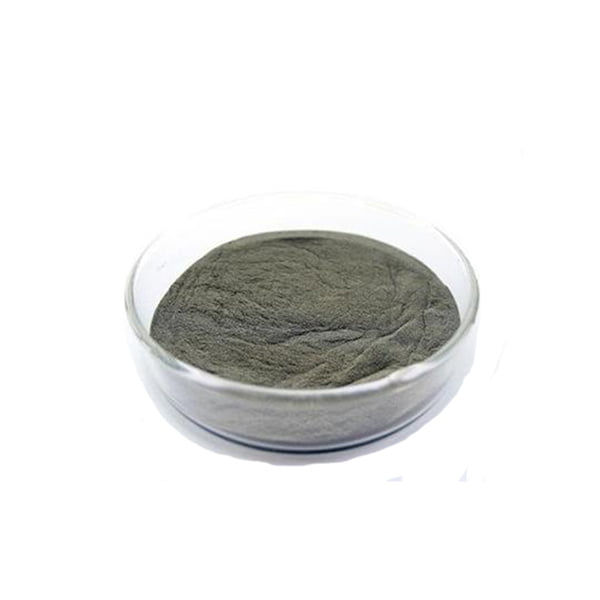
Frequently Asked Questions
1. Why is high purity important for titanium powders meant for medical or aerospace applications?
High purity minimize adverse biological responses and ensure reliable performance under demanding service conditions over product lifetimes spanning decades. Trace elements can negatively impact mechanical properties or corrosion resistance.
2. What is the benefit of spheroidal titanium powders for AM?
Spherical powders with smooth surface texture provide excellent flowability, spreadability, packing density and layer uniformity during laser or e-beam melting processes, resulting in higher quality 3D printed components.
3. Which titanium powder production method yields finest particle sizes?
Plasma atomization of titanium can yield extremely fine particles down to 5-15 micron range owing to higher energy input, allowing very high resolution AM processing. However, productivity is lower than gas atomization.
4. Why is gas atomization the most popular titanium powder making method?
Gas atomized powders offer a good balance of particle size distribution, spherical morphology, bulk density and moderate oxygen pickup during production at reasonable cost. This allows great flexibility in meeting specifications for pressing, AM, thermal spray or other powder metallurgy technologies.
5. What is meant by ‘satellite particles’ in plasma atomized titanium powder?
Satellites refer to very fine undersized particles that adhere to the surface of coarser particles during the rapid solidification. These satellites can get entrapped in layers, negatively impacting consolidation and density.
Summary
With their high strength, low density, temperature resistance, corrosion performance and biocompatibility, titanium powders serve critical applications across aerospace, medical, automotive, chemical and military sectors.
Modern gas, plasma and induction melting atomization methods can produce titanium powders with tailored particle characteristics to maximize performance in powder bed AM processes as well as metal injection molding, pressing and sintering, thermal spray, and more.
Leading titanium powder producers offer various grades including commercially pure titanium along with workhorse alloys like Ti-6Al-4V meeting key benchmarks for size distribution, shape and purity.
Despite higher costs versus steel, titanium powders provide the requisite combination of mechanical and chemical properties to justify use in mission-critical rotating parts, armor protection systems, biomedical implants and 3D printed components where performance, life span and reliability are vital.
Continuing R&D focused on powder manufacturing, post-processing, alloy development and qualification aims to expand adoption across aerospace, defense, motorsports and medical sectors where titanium’s capabilities can enable next generation transportation and health technologies.
Share On
MET3DP Technology Co., LTD is a leading provider of additive manufacturing solutions headquartered in Qingdao, China. Our company specializes in 3D printing equipment and high-performance metal powders for industrial applications.
Inquiry to get best price and customized Solution for your business!
Related Articles
About Met3DP
Recent Update
Our Product
CONTACT US
Any questions? Send us message now! We’ll serve your request with a whole team after receiving your message.
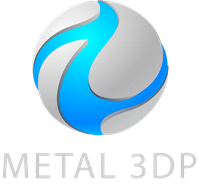
Metal Powders for 3D Printing and Additive Manufacturing