Tungsten carbide powder
Table of Contents
Tungsten carbide powder, a champion of toughness and resilience, plays a critical role in shaping our world. Imagine the drill bits that burrow deep into the earth, the razor-sharp cutting tools that slice through metal with ease, or the prosthetics that endure the everyday wear and tear – all these marvels rely on the extraordinary properties of tungsten carbide powder.
But what exactly is this wonder material, and how does it achieve such remarkable feats? Dive deeper as we explore the fascinating world of tungsten carbide powder, unraveling its composition, properties, applications, and the factors that influence its selection.
the Composition and Properties of Tungsten Carbide Powder
Tungsten carbide powder, abbreviated as WC, is a ceramic compound formed by the chemical union of tungsten (W) and carbon (C). Imagine tiny, ceramic building blocks, where tungsten atoms act as the sturdy foundation, and carbon atoms fill the gaps, creating a robust and tightly packed structure. This unique arrangement bestows tungsten carbide powder with an exceptional combination of properties:
- Hardness: Tungsten carbide ranks second only to diamond in terms of hardness, making it ideal for applications that require enduring wear and tear. Think of it as the ultimate shield against abrasion, standing strong where other materials would crumble.
- Strength: Not only is tungsten carbide powder hard, but it’s also incredibly strong. It can withstand immense pressure without breaking, making it perfect for heavy-duty tasks like drilling and machining. Imagine a tiny grain of sand, but with the strength to hold a skyscraper!
- Thermal Stability: Tungsten carbide powder retains its strength and hardness even at high temperatures. In contrast to some materials that become soft and pliable when the heat is on, tungsten carbide powder keeps its cool, metaphorically and literally.
- Corrosion Resistance: Tungsten carbide powder exhibits excellent resistance to corrosion, meaning it doesn’t readily degrade in harsh environments. Imagine a material that can shrug off the challenges of acidic or caustic conditions, a true testament to its durability.
Composition and Key Properties of Tungsten Carbide Powder
Property | Description |
---|---|
Composition | Tungsten (W) and Carbon (C) |
Hardness | Second only to diamond |
Strength | High compressive strength |
Thermal Stability | Maintains properties at high temperatures |
Corrosion Resistance | Resistant to degradation in harsh environments |
These exceptional properties make tungsten carbide powder a versatile material with a wide range of applications across various industries.
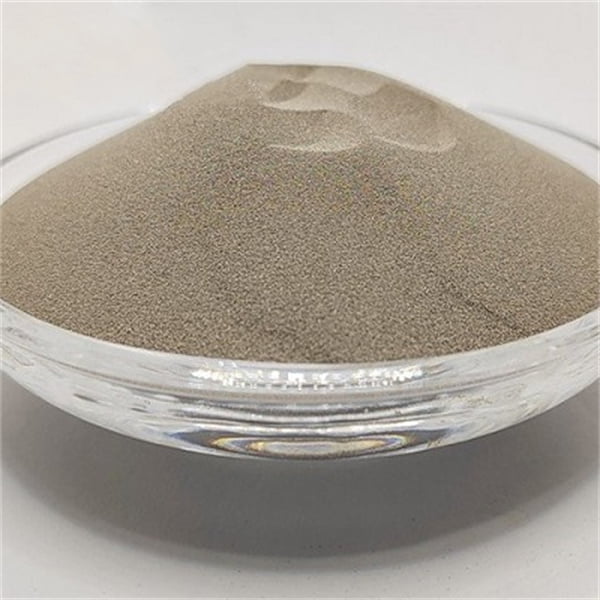
Applications of Tungsten Carbide Powder
Tungsten carbide powder isn’t just another pretty face in the material science world; it’s a workhorse that gets the job done. Here’s a glimpse into the diverse applications where tungsten carbide powder shines:
- Cutting Tools: Imagine drill bits, milling cutters, and lathe tools that can slice through tough materials like steel, concrete, and even rock. Tungsten carbide powder empowers these cutting tools to deliver exceptional performance and extended life.
- Wear Parts: Industrial equipment often faces severe wear and tear. Tungsten carbide powder comes to the rescue in the form of wear plates, bushings, and liners, protecting critical components and extending their lifespan. Think of it as a suit of armor for machinery, safeguarding it from the relentless onslaught of friction.
- Mining and Construction: Tungsten carbide powder empowers drill bits and other tools used in mining and construction to penetrate hard rock and earth with ease. Imagine carving through tough terrain with unwavering efficiency, a testament to the power of tungsten carbide.
- Aerospace: The unforgiving environment of space demands materials that can withstand extreme temperatures and harsh conditions. Tungsten carbide powder finds its place in jet engine components, rocket nozzles, and other aerospace applications.
- Medical Applications: Due to its biocompatibility and exceptional wear resistance, tungsten carbide powder is used in prosthetics, joint replacements, and surgical tools. It plays a vital role in improving the lives of patients by offering durable and long-lasting medical implants.
Applications of Tungsten Carbide Powder
Application | Description |
---|---|
Cutting Tools | Drill bits, milling cutters, lathe tools |
Wear Parts | Wear plates, bushings, liners |
Mining and Construction | Drill bits, mining tools |
Aerospace | Jet engine components, rocket nozzles |
Medical Applications | Prosthetics, joint replacements, surgical tools |
These are just a few examples, and the potential applications of tungsten carbide powder continue to expand as new technologies emerge.
the Different Types and Grades of Tungsten Carbide Powder
Not all tungsten carbide powders are created equal. Manufacturers offer various types and grades tailored to specific applications. Here’s a breakdown of some key factors that differentiate them:
- Particle Size and Distribution: The size and distribution of tungsten carbide particles significantly impact the performance of the final product. Finer particles, with a more uniform distribution, generally lead to a denser and stronger final product. Imagine building a brick wall; smaller, uniformly sized bricks create a tighter structure compared to a wall built with irregularly sized bricks. In the realm of tungsten carbide powder, finer particles act like those uniform bricks, leading to a more robust material.
- Cobalt Content: A small amount of cobalt (usually between 3% and 15%) is often added to tungsten carbide powder as a binder. This metallic binder helps hold the tungsten carbide particles together, enhancing the overall strength and toughness of the final product. Think of cobalt as the mortar that binds the bricks (tungsten carbide particles) together, creating a cohesive and robust structure. The exact amount of cobalt used depends on the desired properties of the final product. For instance, higher cobalt content generally leads to better toughness but may come at the expense of some hardness.
- Coating: Tungsten carbide powder can be coated with various materials to enhance specific properties. For example, titanium nitride coating can improve wear resistance and corrosion resistance, while a chromium carbide coating can enhance thermal stability. Imagine adding a protective layer to your armor (tungsten carbide powder); different coatings offer various benefits depending on the specific challenge faced.
Common Types and Grades of Tungsten Grade Carbide Powder
Here’s a glimpse into some of the most commonly used types and grades of tungsten carbide powder, along with their typical applications:
Type/Grade | Description | Applications |
---|---|---|
K-Type | Coarser particle size, higher cobalt content (10-15%) | Wear parts, mining tools |
F-Type | Finer particle size, lower cobalt content (6-8%) | Cutting tools, inserts |
GC Grades | Very fine particle size, various cobalt contents | High-performance cutting tools, aerospace components |
Special Grades | Tailored properties through specific additives or processes | Medical applications, electronic components |
This table provides a basic overview, and numerous other specific types and grades exist to cater to the diverse needs of various industries.
Selecting the Right Tungsten Carbide Powder
Choosing the most suitable tungsten carbide powder for a particular application requires careful consideration of several factors:
- Application Requirements: The primary function of the final product plays a crucial role. For instance, wear parts prioritize high toughness to withstand abrasion, while cutting tools demand exceptional hardness for clean cuts. Identifying the key performance requirements is the first step.
- Particle Size and Distribution: As mentioned earlier, particle size and distribution significantly impact the final product’s properties. Finer particles are generally preferred for cutting tools, while coarser particles might be suitable for wear parts.
- Cobalt Content: The amount of cobalt affects the balance between hardness and toughness. Higher cobalt content enhances toughness but might reduce hardness slightly. Finding the right balance depends on the specific application needs.
- Cost: Tungsten carbide powder can vary in cost depending on factors like particle size, grade, and cobalt content. Striking a balance between desired properties and cost is essential.
Considerations When Selecting Tungsten Carbide Powder
Factor | Description |
---|---|
Application Requirements | Function of the final product |
Particle Size and Distribution | Impact on final product properties |
Cobalt Content | Balance between hardness and toughness |
Cost | Finding the right balance between properties and budget |
By carefully considering these factors, manufacturers can select the most appropriate tungsten carbide powder to achieve optimal performance in their specific application.
Advantages and Limitations of Tungsten Carbide Powder
Tungsten carbide powder boasts numerous advantages that make it a highly sought-after material. However, it also comes with some limitations that need to be considered.
Advantages of Tungsten Carbide Powder
- Exceptional Hardness: Second only to diamond, tungsten carbide powder offers unparalleled resistance to wear and tear, making it ideal for demanding applications.
- High Strength: Not only is it hard, but tungsten carbide powder is also incredibly strong, allowing it to withstand significant pressure without breaking.
- Thermal Stability: It retains its strength and hardness even at elevated temperatures, making it suitable for high-temperature environments.
- Corrosion Resistance: Tungsten carbide powder exhibits excellent resistance to corrosion, ensuring long-lasting performance in harsh conditions.
- Versatility: With various types and grades available, tungsten carbide powder can be tailored to meet the specific needs of a wide range of applications.
Limitations of Tungsten Carbide Powder
- Brittleness: While incredibly hard, tungsten carbide powder can be brittle under certain circumstances, meaning it may chip or fracture if subjected to a sudden impact. Imagine a very strong, but slightly inflexible piece of armor; it might provide exceptional protection against scratches and abrasions but could crack under a forceful blow.
- Machinability: Tungsten carbide powder can be challenging to machine due to its extreme hardness. Special tooling and techniques are required to work with it, which can increase production costs. Think of shaping a very hard stone; it requires specialized tools and techniques compared to working with softer materials.
- Cost: Tungsten carbide powder can be more expensive than some other materials, particularly when considering the specialized processing required. This cost factor needs to be weighed against the performance benefits it offers for the specific application.
Advantages vs. Limitations of Tungsten Carbide Powder
Advantage | Description | Limitation | Description |
---|---|---|---|
Exceptional Hardness | Resists wear and tear | Brittleness | May chip or fracture under impact |
High Strength | Withstands significant pressure | Machinability | Challenging to machine |
Thermal Stability | Maintains properties at high temperatures | Cost | More expensive than some materials |
Corrosion Resistance | Long-lasting performance in harsh conditions | ||
Versatility | Tailored for diverse applications |
Despite these limitations, the exceptional properties of tungsten carbide powder often outweigh the drawbacks. By carefully considering the application requirements and selecting the most appropriate type and grade, manufacturers can leverage the unique strengths of tungsten carbide powder to achieve superior performance in their products.
Suppliers and Pricing of Tungsten Carbide Powder
Tungsten carbide powder is readily available from a wide range of global and regional suppliers. Here are some key factors to consider when selecting a supplier:
- Reputation and Experience: Choose a reputable supplier with a proven track record of providing high-quality tungsten carbide powder. Look for a company with experience in your specific industry to ensure they understand your needs.
- Product Variety: The supplier should offer a variety of types and grades of tungsten carbide powder to cater to your specific application requirements.
- Quality Control: Ensure the supplier has robust quality control procedures in place to guarantee the consistency and properties of the tungsten carbide powder.
- Pricing and Lead Times: Compare prices from multiple suppliers and factor in lead times for delivery to ensure it aligns with your production schedule.
Pricing of Tungsten Carbide Powder
The cost of tungsten carbide powder can vary depending on several factors, including:
- Particle size and distribution: Finer particles generally command a higher price.
- Grade: Powders with higher cobalt content or special additives typically cost more.
- Quantity: Bulk purchases often come with discounted pricing.
As a general estimate, the price of tungsten carbide powder can range from $10 to $100 per kilogram, depending on the aforementioned factors.
Finding the Right Tungsten Carbide Powder Supplier
Here’s a table summarizing the key factors to consider when selecting a tungsten carbide powder supplier:
Factor | Description |
---|---|
Reputation and Experience | Proven track record, industry expertise |
Product Variety | Caters to specific application needs |
Quality Control | Ensures consistency and properties |
Pricing and Lead Times | Competitive pricing, aligns with production schedule |
By carefully evaluating these factors, manufacturers can identify a reliable supplier that provides high-quality tungsten carbide powder at a competitive price.
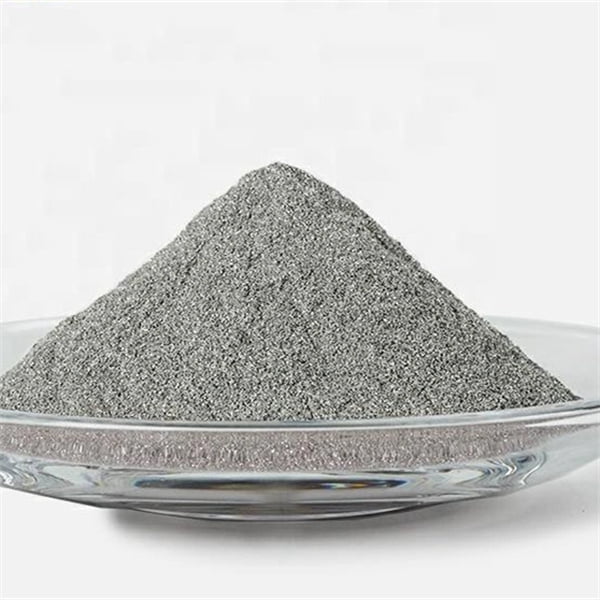
The Future of Tungsten Carbide Powder
Tungsten carbide powder has been a cornerstone of industrial applications for decades, and its future looks bright. Here are some exciting trends shaping the future of this remarkable material:
- Development of New Grades: Researchers are continuously developing new grades of tungsten carbide powder with even better properties, such as enhanced wear resistance, higher thermal stability, and improved toughness.
- Nanotechnology Applications: Nanotechnology offers exciting possibilities for creating tungsten carbide powder with unique properties at the atomic level. Imagine even more precise control over the material’s structure and performance.
- Composite Materials: Tungsten carbide powder can be combined with other materials to create composites with even more desirable properties. This opens doors for innovative applications in various fields.
- Additive Manufacturing: The rise of additive manufacturing techniques like 3D printing paves the way for the creation of complex shapes and structures using tungsten carbide powder. This opens doors for entirely new design possibilities.
The future of tungsten carbide powder is brimming with potential. As technology advances and research delves deeper, we can expect to see even more groundbreaking applications for this versatile and remarkable material.
FAQ
Q: What are some specific examples of different tungsten carbide powder models?
As tungsten carbide powder isn’t a pre-defined model like a car or phone, it’s categorized by its properties and composition. However, to give you a better understanding, here are some examples with descriptions based on common classifications:
- K10: This is a coarse-grained type with a high cobalt content (around 10%). Due to its excellent toughness and wear resistance, it’s commonly used in wear parts like grinding balls, crusher liners, and drill bits for abrasive materials.
- F20: A finer-grained type with a lower cobalt content (around 6-8%). This combination provides a good balance between hardness and toughness, making it ideal for various cutting tools like inserts for milling and turning operations.
- GC10: An ultra-fine grained type with a medium cobalt content (around 10%). This combination offers exceptional hardness and wear resistance, making it suitable for high-performance cutting tools used in machining difficult materials like titanium alloys and superalloys.
- Special Grade (Biocompatible): This type incorporates specific additives or undergoes additional processing to achieve biocompatibility. Used in medical implants like joint replacements and surgical tools, it offers excellent wear resistance and resists corrosion within the body.
Note: These are just a few examples, and numerous other specific types and grades exist with varying properties and applications.
Q: How is tungsten carbide powder manufactured?
Tungsten carbide powder production involves a multi-step process:
- Raw Material Preparation: Tungsten ore is crushed, milled, and purified to obtain tungsten oxide (WO3). Similarly, carbon sources like graphite are processed into a desired form.
- Carburization: Tungsten oxide and carbon are mixed and heated in a controlled atmosphere, typically a hydrogen furnace. This high-temperature process triggers a chemical reaction, converting the tungsten oxide to tungsten carbide (WC).
- Grinding and Classification: The resulting tungsten carbide cake is crushed and milled into a fine powder. Classification techniques are used to achieve the desired particle size distribution.
- Coating (Optional): For specific applications, the powder may be coated with additional materials like titanium nitride or chromium carbide to enhance specific properties.
- Quality Control: Rigorous quality control procedures ensure the powder meets the desired specifications for particle size, distribution, chemical composition, and other critical parameters.
Q: Can tungsten carbide powder be recycled?
Yes, tungsten carbide powder can be recycled to a certain extent. The recycling process involves collecting scrap tungsten carbide materials, crushing and grinding them into a usable powder form. However, the recycled powder may not possess the same properties as virgin powder due to potential contamination and changes in particle size distribution. Recycled powder is often used in less demanding applications.
Q: What are some safety considerations when handling tungsten carbide powder?
Tungsten carbide powder is generally considered safe for handling when following proper precautions. However, inhaling fine dust particles can irritate the lungs. Here are some safety tips:
- Wear appropriate personal protective equipment (PPE): Use a respirator to prevent inhalation of dust particles. Safety glasses and gloves are also recommended.
- Minimize dust generation: Use wet methods whenever possible to suppress dust formation during handling and processing.
- Maintain good ventilation: Ensure adequate ventilation in the workspace to remove airborne dust particles.
- Proper disposal: Dispose of tungsten carbide powder waste according to local regulations.
Share On
MET3DP Technology Co., LTD is a leading provider of additive manufacturing solutions headquartered in Qingdao, China. Our company specializes in 3D printing equipment and high-performance metal powders for industrial applications.
Inquiry to get best price and customized Solution for your business!
Related Articles
About Met3DP
Recent Update
Our Product
CONTACT US
Any questions? Send us message now! We’ll serve your request with a whole team after receiving your message.
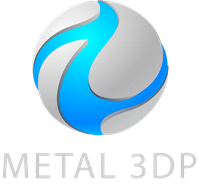
Metal Powders for 3D Printing and Additive Manufacturing