Comparison between DED technology and WAAM technology
Table of Contents
Introduction
Hook: Imagine crafting complex metal objects layer by layer, with molten metal meticulously deposited to build anything from towering wind turbine components to intricate medical implants. This captivating realm belongs to Directed Energy Deposition (DED) and Wire Arc Additive Manufacturing (WAAM), two revolutionary metal additive manufacturing (AM) techniques.
Problem: Choosing between DED and WAAM can be a daunting task. Both boast impressive capabilities, but their nuances can significantly impact project outcomes.
Solution: This in-depth exploration will dissect DED and WAAM, comparing their core aspects, applications, and suitability for various scenarios.
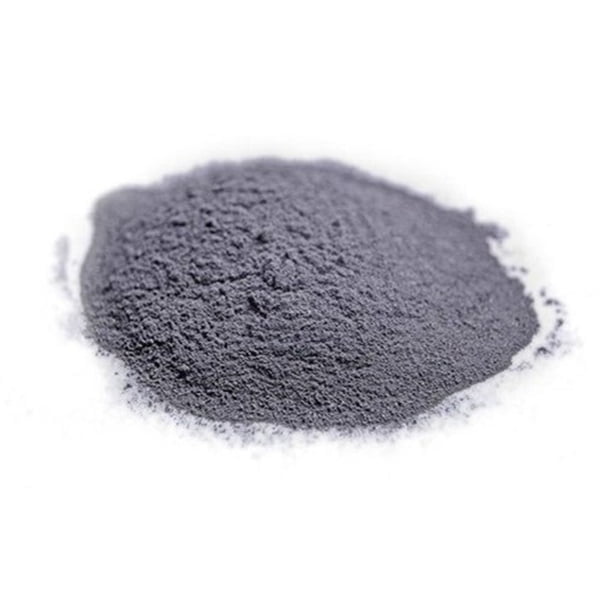
Understanding DED Technology
Definition: DED is a broad category of AM processes that utilize a concentrated energy source (laser, electron beam, plasma arc) to melt and fuse material (typically metal powder) onto a build platform, creating a 3D object layer by layer.
Heat Sources:
Laser DED: High-powered lasers offer precise control and excellent resolution, ideal for intricate geometries. Popular materials include stainless steel, titanium alloys, and Inconel.
Electron Beam DED: Generates highly focused energy beams in a vacuum chamber, enabling superior melting depth and compatibility with reactive metals like titanium.
Plasma Arc DED: Utilizes a plasma torch to melt the feedstock, offering faster deposition rates and cost-effectiveness for larger structures, often using common welding wires.
Metal Powders for DED:
Metal Powder | Description | Advantages | Limitations |
---|---|---|---|
Stainless Steel 316L | Versatile austenitic steel known for its excellent corrosion resistance, biocompatibility, and high strength. | Widely used in aerospace, medical implants, and chemical processing. | May require post-processing for optimal surface finish. |
Inconel 625 | Nickel-chromium superalloy renowned for its high-temperature strength, oxidation resistance, and creep resistance. | Employed in demanding aerospace, gas turbine, and nuclear applications. | More expensive than common steels. |
Titanium Ti-6Al-4V | Workhorse titanium alloy offering a good balance of strength, weight, and corrosion resistance. | Popular in aerospace, biomedical, and sporting goods due to its biocompatibility. | Prone to oxygen contamination during printing, requiring careful handling. |
Aluminum AlSi10Mg | Alloy combining good strength with lightweight properties and improved castability. | Used in automotive, aerospace, and marine applications for weight reduction. | Highly reactive, requiring inert gas environments for printing. |
Tool Steel H13 | Hot-work tool steel known for its excellent wear resistance and hot strength. | Employed for molds, dies, and punches used in metal forming and forging processes. | Can be challenging to print due to its high carbon content. |
Nickel Alloy 718 | High-strength, precipitation-hardening nickel alloy offering excellent mechanical properties at elevated temperatures. | Utilized in aerospace components for its strength and creep resistance. | More expensive than other options. |
Copper | Highly conductive metal with thermal and electrical applications. | Used in electrical conductors, heat exchangers, and electronic components. | Prone to oxidation during printing, requiring control measures. |
Cobalt Chrome (CoCr) | Biocompatible alloy used for wear-resistant medical implants. | Employed in hip and knee replacements due to its excellent wear resistance. | May require special handling and post-processing to optimize biocompatibility. |
Inconel 718C | Variation of Inconel 625 with improved casting characteristics and weldability. | Employed in turbine blades and other high-temperature applications. | Similar to Inconel 625 in properties and limitations. |
Applications of DED: Aerospace components, medical implants, repair of worn-out parts, tooling, and large-scale metal structures.
Demystifying WAAM Technology
Definition: WAAM, or Wire Arc Additive Manufacturing, is a DED variant that utilizes a continuous wire feedstock and an electric arc (typically gas metal arc welding) to melt and deposit the material.
Advantages:
Cost-Effectiveness: WAAM leverages existing arc welding technology and readily available wire, making it a more affordable option compared to powder-based DED processes.
High Deposition Rates: WAAM offers faster deposition rates due to the continuous wire feed and higher energy density of the arc, making it suitable for large-scale projects.
Material Compatibility: WAAM offers broad material compatibility with various common welding wires, including:
Steel: Mild steel, stainless steel grades (304L, 316L), duplex stainless steel, and tool steels.
Aluminum: Aluminum alloys like AlSi10Mg and Al 6061.
Nickel Alloys: Inconel 625 and Nickel Alloy 718.
Other Metals: Copper, titanium alloys (limited use due to oxidation concerns).
Applications of WAAM: Shipbuilding, construction (bridge components, beams), large-scale pressure vessels, repair of heavy machinery, and rapid prototyping of large metal structures.
Key Considerations: DED vs. WAAM
The Printing Speed of DED Technology and WAAM Technology is Different
- DED: Offers a wider range of printing speeds depending on the heat source and powder feed rate. Laser DED provides slower speeds for high-precision work, while plasma arc DED achieves faster rates for larger builds.
- WAAM: Generally boasts the fastest deposition rates among DED processes thanks to the continuous wire feed and higher energy density of the arc.
The Material Costs of DED Technology and WAAM Technology are Different
- DED: Can be more expensive, particularly for processes using specialized metal powders like Inconel or reactive metals like titanium.
- WAAM: Typically more cost-effective due to the use of readily available and often cheaper welding wires.
The Surface Finish of DED Technology and WAAM Technology is Different
- DED: Laser DED offers the smoothest surface finishes due to the precise control over the laser beam. Electron beam DED also produces good surface finishes. Plasma arc DED, while faster, may require more post-processing to achieve a desired surface quality.
- WAAM: Generally produces rougher surface finishes compared to laser DED due to the spatter associated with the arc welding process. However, WAAM surfaces can be machined or ground for desired finishes.
The Applications Fields are Different
- DED: Well-suited for intricate, high-precision components requiring excellent surface finish, such as aerospace parts, medical implants, and molds.
- WAAM: Excels in large-scale metal structures, rapid prototyping of bulky parts, shipbuilding components, and repair of massive machinery due to its high deposition rates and cost-effectiveness.
Equipment Costs of DED Technology and WAAM Technology
- DED: DED systems, especially those using lasers or electron beams, tend to be more expensive than WAAM machines due to the complex technology involved.
- WAAM: WAAM systems often leverage existing arc welding technology, making them a more affordable DED option.
Advantages and Limitations Comparison Table
Feature | DED | WAAM |
---|---|---|
Heat Source | Laser, Electron Beam, Plasma Arc | Electric Arc (Gas Metal Arc Welding) |
Feedstock | Metal Powder | Continuous Wire |
Deposition Rate | Varies (Laser DED: Slow, Plasma Arc DED: Faster) | High |
Material Compatibility | Wider range of materials, including reactive metals | Primarily common welding wire materials |
Surface Finish | Can be very smooth (Laser DED) | Generally rougher |
Applications | Intricate components, medical implants, molds | Large-scale structures, rapid prototyping, repair |
Equipment Cost | Generally higher | Generally lower |
Material Cost | Can be higher for specialized powders | Lower for common welding wires |
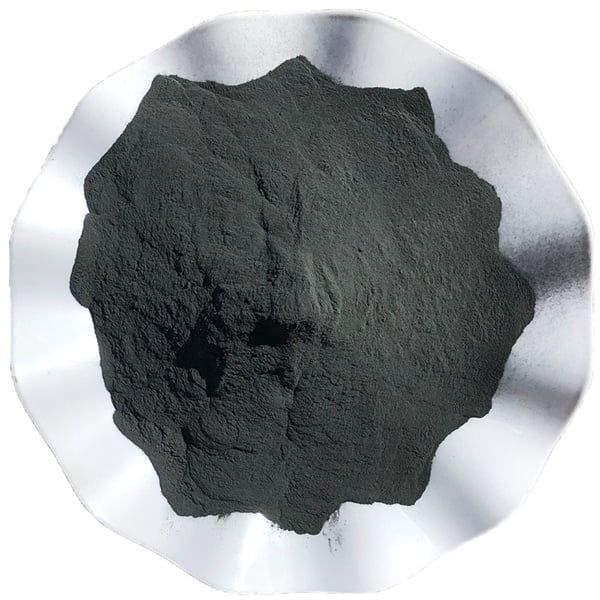
Choosing Between DED and WAAM
The optimal choice between DED and WAAM hinges on your specific project requirements:
For intricate parts with critical surface finishes and a wider material selection, DED (particularly Laser DED) is likely the better choice.
For large-scale, cost-sensitive applications where deposition speed and readily available materials are priorities, WAAM shines.
Additional Considerations:
- Project complexity: DED excels in intricate geometries.
- Material requirements: DED offers broader material options, including reactive metals.
- Production volume: WAAM’s speed is advantageous for high-volume projects.
- Budget: WAAM is generally more cost-effective.
Future of DED and WAAM
Both DED and WAAM technologies are rapidly evolving. We can expect advancements in:
- Multi-material capabilities: DED and WAAM may integrate functionalities to deposit different materials within the same build for composite structures.
- Hybrid DED/WAAM systems: Combining DED and WAAM in a single machine could offer more flexibility in material selection and deposition rates.
- Improved control and automation: Enhanced software and sensor integration will lead to more precise control over the printing process.
FAQ
Q: Which technology is faster, DED or WAAM?
A: WAAM generally boasts the fastest deposition rates among DED processes. The continuous wire feed and higher energy density of the arc in WAAM allow for quicker material deposition compared to DED, particularly powder-based DED methods. However, laser DED can achieve moderate speeds for intricate work requiring high precision.
Q: Is DED or WAAM more expensive?
A: WAAM is typically the more cost-effective option. Here’s a breakdown:
- Equipment: WAAM systems leverage existing arc welding technology, making them more affordable than DED machines, especially those using lasers or electron beams.
- Material: DED can be more expensive if you require specialized metal powders like Inconel or reactive metals like titanium. WAAM utilizes readily available and often cheaper welding wires.
Q: Which technology offers a better surface finish?
A: DED, particularly laser DED, excels in producing smooth surface finishes due to the precise control over the laser beam. Electron beam DED also yields good results. Plasma arc DED, while faster, may require more post-processing for a desired surface quality. WAAM generally produces rougher finishes compared to laser DED because of the spatter associated with the arc welding process. However, WAAM surfaces can be machined or ground for a smoother finish.
Q: What kind of parts are DED and WAAM suitable for?
A: DED and WAAM cater to different application areas:
- DED: Ideal for intricate, high-precision components requiring excellent surface finish, such as:
- Aerospace parts (turbine blades, engine components)
- Medical implants (hip replacements, dental prosthetics)
- Molds and tooling inserts
- WAAM: Excels in large-scale metal structures and applications where:
- High deposition rates are crucial (shipbuilding components, bridge beams)
- Rapid prototyping of bulky parts is needed
- Cost-effectiveness is a major consideration (repair of massive machinery)
Q: Is DED or WAAM more environmentally friendly?
A: Both DED and WAAM can be considered environmentally friendly compared to traditional subtractive manufacturing techniques like machining. Here’s why:
- Reduced Material Waste: DED and WAAM utilize additive processes, building parts layer by layer with minimal material wastage compared to machining, which removes excess material.
- Potential for Recycling: Metal powders used in DED can potentially be recycled and reused in future builds, minimizing environmental impact.
In conclusion, DED and WAAM are powerful metal additive manufacturing technologies with distinct strengths and applications. By understanding their core principles, material compatibility, and suitability for various project requirements, you can make an informed decision on which technology best aligns with your needs. As these technologies continue to evolve, we can expect even greater capabilities and wider adoption in diverse industries.
Share On
MET3DP Technology Co., LTD is a leading provider of additive manufacturing solutions headquartered in Qingdao, China. Our company specializes in 3D printing equipment and high-performance metal powders for industrial applications.
Inquiry to get best price and customized Solution for your business!
Related Articles
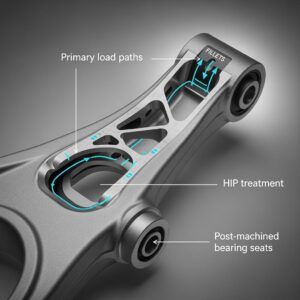
Metal 3D Printing for U.S. Automotive Lightweight Structural Brackets and Suspension Components
Read More »About Met3DP
Recent Update
Our Product
CONTACT US
Any questions? Send us message now! We’ll serve your request with a whole team after receiving your message.