Which 3D printed aluminum alloy powder can be used in aerospace
Table of Contents
The aerospace industry has always been a pioneer in pushing the boundaries of design and technology. Imagine a world where complex aircraft parts are crafted not through traditional subtractive manufacturing, but through a layer-by-layer additive process. This is the magic of 3D printing, and 3D printed aluminum alloy powders are playing a starring role in this aerial revolution.
But with a vast array of aluminum alloy powders available, selecting the right one for your next aerospace project can feel like navigating a starry night sky. Fear not, intrepid innovator! This guide will illuminate the most popular 3D printed aluminum alloy powders, their strengths, weaknesses, and ideal applications within the aerospace realm.
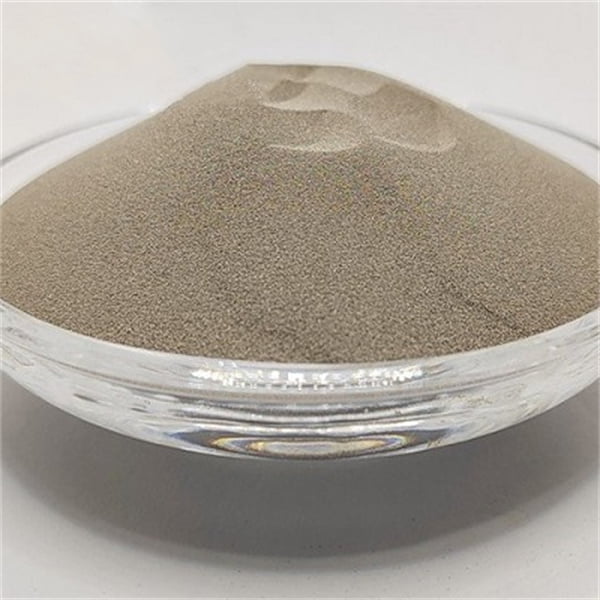
3D printed aluminum alloy powders:AlSi10Mg
Commonly used in the manufacturing of:
- Aircraft structural components
- Engine components
- Gas turbine components
Imagine the powerful heart of an aircraft – the engine. Now, picture its intricate components built layer by layer with a reliable, weldable material. Enter AlSi10Mg, a versatile aluminum-silicon-magnesium alloy powder. This champion offers a compelling combination of:
- Excellent strength-to-weight ratio: AlSi10Mg boasts a respectable balance between being lightweight and possessing the muscle needed for aerospace applications. Think of it as a weightlifter who defies gravity with their impressive feats.
- Superior castability: Just like pouring molten metal into a mold, the 3D printing process requires good flow characteristics. AlSi10Mg excels in this area, ensuring smooth layer formation during printing.
- Weldability: Aerospace parts often require joining together. AlSi10Mg’s exceptional weldability makes this process seamless, crucial for creating robust and reliable structures.
However, AlSi10Mg isn’t without its limitations. Its moderate strength compared to some other options might not be ideal for highly stressed components. Additionally, its corrosion resistance leaves room for improvement in applications exposed to harsh environments.
The Verdict: AlSi10Mg is a fantastic all-rounder, perfect for a wide range of aerospace applications where a good balance of printability, strength, and weight is desired.
Al6061: The Lightweight Champion
Commonly used in the manufacturing of:
- Aircraft fuselage
- Wings
- Landing gear components
Ever wondered how massive airplanes manage to stay airborne? Part of the answer lies in their lightweight construction. Al6061, an aluminum-magnesium-silicon alloy powder, is a champion in this regard. Think of it as a featherweight boxer packing a surprising punch. Here’s what makes it so special:
- Unmatched lightness: Al6061 shines in its exceptional weight-to-strength ratio. Every gram saved translates to improved fuel efficiency and overall aircraft performance. Imagine an airplane shedding pounds without sacrificing its ability to handle the demands of flight.
- Excellent machinability: Sometimes, 3D printed parts require further shaping and finishing. Al6061’s superior machinability allows for precise post-processing, ensuring a flawless final product.
However, there’s always a trade-off. While lightweight, Al6061 falls short in the strength department compared to some other options. Additionally, its corrosion resistance is considered moderate, requiring additional protection for applications exposed to saltwater or harsh environments.
The Verdict: Al6061 is the go-to choice for applications where weight reduction is paramount. Think of it as the ideal material for aircraft parts that don’t require the most extreme strength but benefit greatly from being as light as possible.
Al7075: The Strongman of the Skies
Commonly used in the manufacturing of:
- Aircraft structural components
- Engine components
- Spacecraft components
When it comes to raw strength, Al7075, an aluminum-zinc alloy powder, takes the crown. Imagine a material that can withstand the immense pressures and stresses of high-performance flight. Al7075 is that material, boasting:
- Unmatched strength: This alloy reigns supreme in terms of tensile strength and yield strength. Think of it as the weightlifter who can hoist incredible amounts of weight. This makes it ideal for applications demanding exceptional strength-to-weight ratios.
- Excellent fatigue resistance: Aircraft components are constantly under stress. Al7075’s exceptional fatigue resistance ensures they can withstand these repetitive forces without succumbing to failure.
Al7075 can be more challenging to print compared to other options. Additionally, its corrosion resistance is lower, necessitating proper surface treatments for aerospace applications
While printing complexities and lower corrosion resistance require extra considerations, Al7075 remains a top choice for aerospace parts that demand the utmost strength and fatigue resistance. Think of it as the perfect material for highly stressed components like landing gear or critical engine parts.
Al2219: The All-Around Performer
Commonly used to manufacture:
- Aircraft skins
- Fuel tanks
- Pipelines
Imagine the sleek, smooth skin of an aircraft. Al2219, an aluminum-copper alloy powder, is a popular choice for creating these intricate shapes. Here’s why:
- Good balance of properties: Al2219 offers a well-rounded combination of strength, weldability, and formability. Think of it as a multi-talented athlete excelling in various disciplines.
- Excellent corrosion resistance: Unlike some other options, Al2219 boasts superior resistance to corrosion, making it ideal for applications exposed to harsh environments or saltwater. Imagine an aircraft part that can withstand the elements without succumbing to rust.
However, Al2219 falls short in the peak strength department compared to Al7075. Additionally, it can be slightly more challenging to machine compared to Al6061.
The Verdict: Al2219 is a versatile choice for applications requiring a good balance of strength, corrosion resistance, and formability. Think of it as the ideal material for aircraft skins, fuel tanks, and pipelines that need to be both strong and resistant to the elements.
Exploring Cutting-Edge Alloys
The world of 3D printed aluminum alloy powders is constantly evolving. Here’s a glimpse into some exciting newcomers:
- Scalmalloy: Developed specifically for additive manufacturing, Scalmalloy boasts exceptional strength that rivals even Al7075. Think of it as a game-changer for applications demanding the absolute peak in strength-to-weight ratio.
- Aluminum MMCs (Metal Matrix Composites): These innovative powders combine aluminum with ceramic or other reinforcing materials. Imagine an aluminum alloy infused with the strength of ceramics, creating a composite material with unmatched properties. While still under development, MMCs hold immense promise for pushing the boundaries of what’s possible with 3D printed aluminum alloy powders in aerospace.
Choosing the Right Alloy
Selecting the perfect 3D printed aluminum alloy powder for your aerospace project requires careful consideration of various factors. Here’s a handy checklist to guide your decision:
- Application requirements: What specific properties are most crucial for your part? Is it raw strength, lightweight construction, or exceptional corrosion resistance?
- Printing considerations: Some alloys might be more challenging to print than others. Evaluate your printing capabilities and choose an alloy that aligns with your expertise.
- Post-processing needs: Will your part require extensive machining or surface treatments? Factor in the machinability and corrosion resistance of the chosen alloy.
- Cost considerations: While some alloys offer superior performance, they might come at a higher price point. Balance performance needs with your budget constraints.
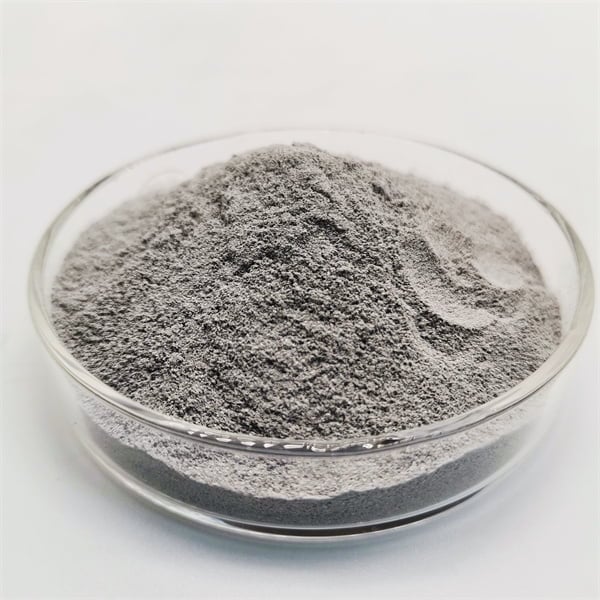
FAQ
Q: What are the benefits of using 3D printed aluminum alloy powders in aerospace applications?
A: 3D printing offers several advantages over traditional subtractive manufacturing techniques in aerospace:
- Design freedom: Complex geometries and lightweight structures become possible with 3D printing.
- Reduced waste: 3D printing utilizes a near net-shape manufacturing process, minimizing material waste.
- Faster turnaround times: Prototyping and production cycles can be significantly accelerated with 3D printing.
Q: What are the key challenges associated with 3D printing aluminum alloy powders?
A: Here are some hurdles to consider:
- Powder quality: Inconsistent powder flow or impurities can impact the printing process and final part quality.
- Surface roughness: 3D printed parts might require additional post-processing to achieve a smooth surface finish.
- Limited part size: Current 3D printing technology has limitations on the size of parts that can be produced.
Q: What’s the future of 3D printed aluminum alloy powders in aerospace?
A: The future is bright! Advancements in powder quality, printing technology, and innovative alloy development will continue to push the boundaries of what’s possible. Expect to see even stronger, lighter, and more versatile aluminum alloys specifically designed for the demanding world of aerospace.
This guide has hopefully provided you with a clear understanding of the most popular 3D printed aluminum alloy powders and their applications within the aerospace industry. Remember, choosing the ideal alloy hinges on your specific project requirements. By carefully considering the factors outlined in the pilot’s checklist, you can make an informed decision that ensures the success of your next aerial endeavor.
Share On
MET3DP Technology Co., LTD is a leading provider of additive manufacturing solutions headquartered in Qingdao, China. Our company specializes in 3D printing equipment and high-performance metal powders for industrial applications.
Inquiry to get best price and customized Solution for your business!
Related Articles
About Met3DP
Recent Update
Our Product
CONTACT US
Any questions? Send us message now! We’ll serve your request with a whole team after receiving your message.
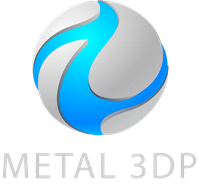
Metal Powders for 3D Printing and Additive Manufacturing
COMPANY
PRODUCT
cONTACT INFO
- Qingdao City, Shandong, China
- [email protected]
- [email protected]
- +86 19116340731