Which 3D printed metal powders can be used in the mold manufacturing
Table of Contents
Mold manufacturing, the backbone of countless industries – from automotive to medical – is undergoing a revolution. Enter 3D printing, a disruptive technology that’s transforming how we design and create molds. But just like a master chef needs the perfect ingredients, successful 3D printed molds rely on the right 3D printed metal powders.
This comprehensive guide delves into the world of 3D printed metal powders, equipping you with the knowledge to choose the ideal material for your mold-making endeavors. We’ll explore a diverse range of metal powders, their properties, strengths, and applications, empowering you to craft molds that are not only functional but excel in performance.
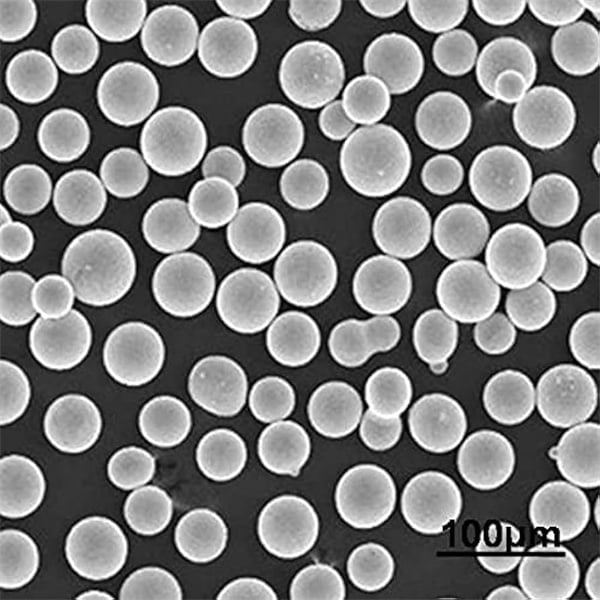
Common 3D Printing Mold Steels Include:
Metal Powder | Composition | Properties | Characteristics |
---|---|---|---|
H13 | Chromium (Cr) 5%, Molybdenum (Mo) 1.3%, Vanadium (V) 0.4% | High hot strength, good wear resistance | Excellent for injection molding applications involving high temperatures and abrasive materials |
P20 | Nickel (Ni) 1.8%, Chromium (Cr) 0.5%, Molybdenum (Mo) 0.35% | Good balance of toughness and wear resistance | A versatile choice for a wide range of molding applications, particularly for prototypes and low-volume production |
S7 | Tungsten (W) 3.25%, Chromium (Cr) 2%, Molybdenum (Mo) 1.25% | Exceptional wear resistance, high hardness | Ideal for molds subjected to extreme wear and tear, such as those used for molding abrasive materials |
Maraging Steel | Nickel (Ni) 18% – 25%, Molybdenum (Mo) 3% – 5%, Titanium (Ti) (optional) | High strength, good toughness, excellent dimensional stability | Well-suited for molds requiring intricate details and tight tolerances, often used in aerospace and medical applications |
Choosing the Right Mold Steel:
Imagine you’re picking the perfect paintbrush for your masterpiece. Selecting the ideal mold steel powder hinges on the specific demands of your project. For instance, if you’re crafting molds for high-volume production of plastic parts, H13’s superior hot strength and wear resistance might be the winning formula. Conversely, if you’re prototyping a medical device mold requiring intricate details, maraging steel’s dimensional stability could be the key to success.
Commonly Used 3D Printed Stainless Steels Include:
Metal Powder | Composition | Properties | Characteristics |
---|---|---|---|
316L | Chromium (Cr) 16% – 18%, Nickel (Ni) 10% – 13%, Molybdenum (Mo) 2% – 3% | Excellent corrosion resistance, good weldability | A popular choice for molds used with corrosive materials or requiring frequent cleaning |
17-4PH | Chromium (Cr) 15% – 17%, Nickel (Ni) 3% – 5%, Copper (Cu) 3% – 5% | High strength, good hardness, good corrosion resistance | Well-suited for molds requiring a balance of strength, corrosion resistance, and wear resistance |
Steering the Course with Stainless Steel Powders:
Stainless steel powders offer a compelling combination of corrosion resistance and printability, making them ideal for various mold-making applications. For instance, if you’re crafting molds for food-grade or medical applications where hygiene is paramount, 316L’s exceptional corrosion resistance becomes a crucial advantage. On the other hand, 17-4PH’s blend of strength and corrosion resistance might be the perfect fit for molds used with slightly abrasive materials.
Commonly Used 3D Printed Titanium Alloys Include:
Metal Powder | Composition | Properties | Characteristics |
---|---|---|---|
Ti6Al4V (Grade 23) | Aluminum (Al) 6%, Vanadium (V) 4% | High strength-to-weight ratio, good corrosion resistance | A go-to choice for lightweight, high-performance molds in aerospace and medical applications |
Ti5Al2.5Sn | Aluminum (Al) 5.5%, Tin (Sn) 2.5% | Good ductility, high strength-to-weight ratio | A valuable option for molds requiring a combination of strength, formability, and weight reduction |
Commonly Used 3D Printed Aluminum Alloys Include:
Metal Powder | Composition | Properties | Characteristics |
---|---|---|---|
AlSi10Mg | Silicon (Si) 10%, Magnesium (Mg) 0.3% | Good castability, excellent machinability | A cost-effective option for prototypes and low-volume mold applications |
Al6061 | Magnesium (Mg) 0.6%, Silicon (Si) 0.6%, Copper (Cu) 0.2% | Good strength, good corrosion resistance | A versatile choice for a wide range of mold applications, offering a balance of affordability and performance |
Aluminum Alloys: The Affordable All-Stars
Aluminum alloys are the budget-friendly champions of the 3D printed mold material world. Their affordability and excellent machinability make them a popular choice for prototyping and low-volume production runs. For instance, if you’re creating a prototype mold for a new consumer product design, AlSi10Mg’s cost-effectiveness might be the ideal solution. On the other hand, if you require a balance of affordability and performance for a low-volume mold, Al6061’s blend of strength and corrosion resistance could be a winning combination.
Specialty Metal Powders
While the aforementioned metal powders are industry staples, the world of 3D printable mold-making materials extends far beyond these workhorses. Here’s a glimpse into some specialty options:
- Nickel Alloys: Offering exceptional high-temperature strength and corrosion resistance, nickel alloys are the go-to choice for molds used in harsh environments, such as those encountered in the chemical processing industry.
- Copper Alloys: Renowned for their excellent thermal conductivity, copper alloys excel in applications where heat transfer is critical, such as molds for injection molding of thermoplastics.
- Tool Steels: Boasting exceptional wear resistance and dimensional stability, tool steels are a valuable option for molds subjected to extreme pressure and wear, such as those used in die casting.
Considering the Special Metal Powders
Think of specialty metal powders as the elite forces of the 3D printed metal powders. Each possesses unique properties that excel in specific scenarios. For instance, if you’re crafting a mold for a chemical processing application where extreme temperatures and corrosive materials are present, nickel alloys’ resilience becomes a game-changer. Similarly, if you’re designing a mold for a high-volume injection molding operation, copper alloys’ superior thermal conductivity could significantly improve production efficiency.
Choosing a 3D printed metal powders
Now that you’ve explored the diverse landscape of 3D printable metal powders, it’s time to equip yourself for the crucial task of selecting the perfect material for your mold-making project. Here are some key factors to consider:
- Application: What will the mold be used for? The specific demands of the application will heavily influence your material selection. For example, if you’re crafting a mold for a high-volume production run, factors like wear resistance and thermal stability become paramount.
- Part Geometry: The intricacy of the mold’s design plays a role. For molds with intricate details, metal powders known for their good dimensional stability, such as maraging steel, might be the preferred choice.
- Post-Processing Requirements: Different metal powders necessitate varying degrees of post-processing, such as heat treatment. Consider the available post-processing capabilities and choose a powder compatible with your setup.
- Cost: Metal powders vary significantly in price. While affordability is a consideration, remember that the upfront cost of a superior material might be offset by factors like extended mold life and improved production efficiency.
A Guide to Metal Powder Properties
When selecting a 3D printed metal powders, understanding its key properties is essential. Here’s a breakdown of some crucial characteristics to keep in mind:
- Strength: The ability of the material to withstand stress without breaking. For molds subjected to high pressure, superior strength is a must.
- Hardness: The material’s resistance to indentation or permanent deformation. Molds encountering abrasive materials benefit from increased hardness.
- Wear Resistance: The material’s ability to resist wear and tear. Molds used for high-volume production require high wear resistance.
- Thermal Conductivity: The material’s ability to transfer heat. For applications involving heat transfer, such as injection molding, optimal thermal conductivity is crucial.
- Corrosion Resistance: The material’s ability to resist rust and degradation. Molds used with corrosive materials or requiring frequent cleaning demand excellent corrosion resistance.
- Dimensional Stability: The material’s ability to maintain its original shape during and after the printing process. Molds requiring precise dimensions benefit from high dimensional stability.
- Printability: How well the powder flows and fuses during the 3D printing process. Good printability ensures smooth operation and minimizes printing defects.
Understanding the Symphony: How Metal Powder Properties Work Together
Imagine a well-rehearsed orchestra. Each instrument possesses unique qualities, but it’s their harmonious interplay that creates beautiful music. Similarly, the properties of a metal powder don’t exist in isolation. Their interplay determines the material’s overall suitability for a specific mold-making application.
For instance, a mold for a high-pressure die-casting application might require a material with exceptional strength and wear resistance. In this scenario, tool steel powder with its inherent toughness and resilience becomes a strong contender. Conversely, a mold for a medical device requiring intricate details and tight tolerances might prioritize dimensional stability and printability, making maraging steel powder a potential frontrunner.
Specifications, Sizes, Grades, and Standards
Choosing the right 3D printed metal powder goes beyond just the material itself. Several additional factors influence your selection, and understanding these nuances is essential for making an informed decision. Here’s a breakdown of some key considerations:
- Specifications: Metal powders adhere to specific industry standards that define their chemical composition, mechanical properties, and particle size distribution. Knowing the relevant specifications ensures you’re selecting a powder that meets the performance requirements of your application.
- Sizes: Metal powders come in various particle sizes, each with its own advantages and limitations. Finer powders generally produce smoother surface finishes but might be more challenging to print. Conversely, coarser powders offer better flow characteristics but might result in a rougher surface finish.
- Grades: Many metal powders come in multiple grades, each offering slight variations in properties to cater to specific needs. For example, a mold steel powder might be available in a variety of grades, with each offering a different balance of strength, toughness, and wear resistance.
- Standards: Metal powders are often manufactured according to industry standards set by organizations like ASTM International (ASTM) or the American Powder Metallurgy Institute (APMI). Understanding these standards helps ensure the quality and consistency of the powder you choose.
Metal Powder Suppliers and Considerations
With a plethora of metal powder manufacturers and suppliers vying for your attention, selecting a reliable source is crucial. Here are some factors to consider when choosing a supplier:
- Reputation: Look for a supplier with a proven track record of providing high-quality metal powders. Research online reviews and industry feedback to gauge the supplier’s reputation.
- Material Selection: Opt for a supplier offering a diverse range of metal powders to cater to your specific needs. A wider selection allows you to find the perfect material for your mold-making project.
- Technical Expertise: A knowledgeable supplier can provide valuable guidance on material selection and answer your technical questions. Choose a supplier with a team that possesses in-depth knowledge of 3D printable metal powders.
- Pricing and Availability: Compare prices from different suppliers while ensuring the quoted price includes any additional costs like shipping and handling. Also, consider the supplier’s lead times and ensure they can meet your project’s timeline.
Pros and Cons of 3D printed metal powders
While 3D printable metal powders offer a revolutionary approach to mold manufacturing, it’s essential to acknowledge both the advantages and limitations of this technology.
Pros:
- Design Freedom: 3D printing allows for the creation of complex mold geometries that were previously impossible with traditional manufacturing methods.
- Faster Lead Times: Compared to traditional mold-making techniques, 3D printing enables faster turnaround times, accelerating product development cycles.
- Cost-Effectiveness: For low-volume production runs or prototypes, 3D printed molds can be a more cost-effective option compared to traditional methods.
- Lightweight Molds: 3D printed metal molds can be lighter than their traditionally manufactured counterparts, offering ergonomic benefits and potentially reducing production costs.
Cons:
- Limited Material Selection: While the range of available 3D printed metal powders is growing, it’s still not as extensive as the options available for traditional mold-making methods.
- Post-Processing Requirements: Some 3D printed metal powders necessitate additional post-processing steps, such as heat treatment, which can add to the overall production time and cost.
- Surface Finish: The surface finish of 3D printed metal molds might not be as smooth as those produced with traditional methods, potentially impacting the quality of the final product.
- Printer Compatibility: Not all 3D printers are compatible with all metal powders. Ensure your chosen powder is compatible with your specific 3D printing equipment.
- Higher Upfront Costs: While 3D printed molds can be cost-effective for low-volume applications, the upfront investment in a 3D printer and metal powder can be significant.
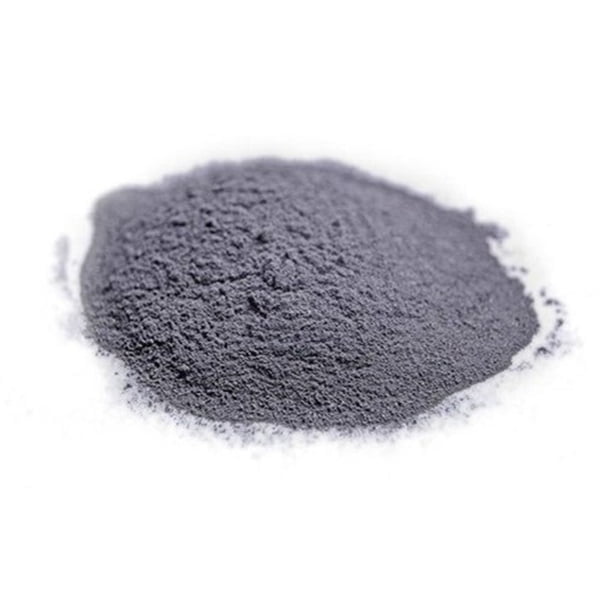
FAQs
Here, we tackle some frequently asked questions to solidify your understanding of 3D printable metal powders and their role in mold manufacturing:
Q: Are 3D printed metal molds as strong as traditionally manufactured molds?
A: The strength of a 3D printed metal mold depends on the chosen metal powder and its processing parameters. However, many 3D printable metal powders offer excellent strength properties, making them suitable for various mold-making applications.
Q: Can I use 3D printed metal molds for high-volume production runs?
A: While 3D printed metal molds can be used for low-volume production runs, their suitability for high-volume applications depends on the specific material and the mold design. Some metal powders offer superior wear resistance, making them potentially viable for high-volume production. However, factors like post-processing requirements and potential limitations in surface finish need to be considered.
Q: How much does it cost to 3D print a metal mold?
A: The cost of 3D printing a metal mold depends on several factors, including the size and complexity of the mold, the chosen metal powder, and the post-processing requirements. The cost of the metal powder itself can vary significantly depending on the material.
Q: What are the environmental benefits of using 3D printed metal molds?
A: Compared to traditional mold-making methods, 3D printing can offer some environmental benefits. The ability to create molds with minimal material waste and the potential for lighter weight molds can contribute to a more sustainable manufacturing process.
The Future of Metal Muscles
The realm of 3D printable metal powders for mold manufacturing is brimming with exciting possibilities. As research and development continue, we can expect to see:
- An even wider range of metal powders with properties tailored to specific mold-making applications.
- Advancements in 3D printing technology leading to faster printing speeds, improved surface finishes, and broader printer compatibility with various metal powders.
- Development of new post-processing techniques that streamline the workflow and reduce the overall production time and cost of 3D printed metal molds.
Share On
MET3DP Technology Co., LTD is a leading provider of additive manufacturing solutions headquartered in Qingdao, China. Our company specializes in 3D printing equipment and high-performance metal powders for industrial applications.
Inquiry to get best price and customized Solution for your business!
Related Articles
About Met3DP
Recent Update
Our Product
CONTACT US
Any questions? Send us message now! We’ll serve your request with a whole team after receiving your message.
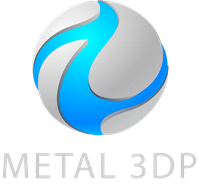
Metal Powders for 3D Printing and Additive Manufacturing