What 3D printed metal powders can be used in automobile manufacturing
Table of Contents
The automobile industry, a titan of innovation, is once again on the cusp of a transformation. Enter 3D printing, a technology rapidly changing how we design and manufacture complex parts. But what fuels this revolution? The answer lies in the heart of the process – 3D printed metal powders. These fine, metallic granules, meticulously crafted for specific properties, are breathing new life into car manufacturing.
This article delves deep into the world of 3D printed metal powders for automobiles. We’ll explore the different types, their unique characteristics, and the exciting applications that are reshaping the automotive landscape. Buckle up, gearheads, because we’re about to take a high-octane ride through the future of car manufacturing!
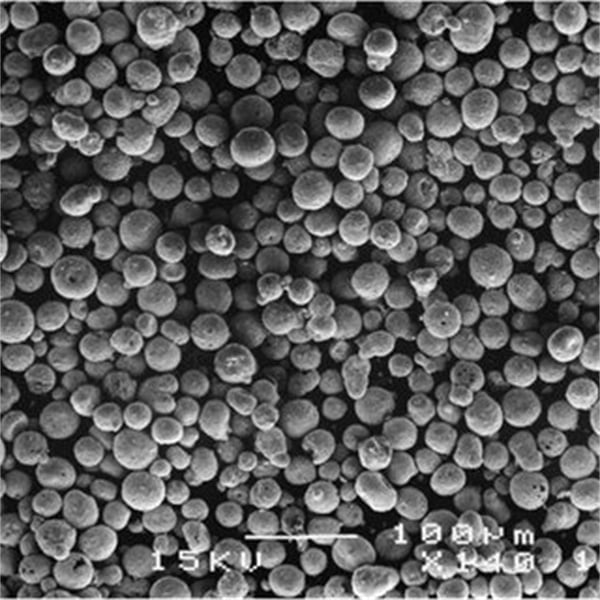
The Power of 3D printed Metal Powders
Just like a delicious dish relies on the perfect blend of spices, creating exceptional car parts with 3D printed metal powder requires a variety of metal powders, each offering distinct advantages. Here’s a closer look at ten of the most prominent players:
Metal Powder | Composition | Properties | Characteristics |
---|---|---|---|
Aluminum Alloy Powder (AA2024, AA6061) | Primarily Aluminum (Al) with elements like Copper (Cu) and Magnesium (Mg) | Lightweight, strong, good corrosion resistance | Excellent for weight reduction in non-critical components like body panels and brackets. Offers a good balance of strength and workability. |
Titanium Alloy Powder (Ti-6Al-4V) | Titanium (Ti) with Aluminum (Al) and Vanadium (V) | High strength-to-weight ratio, excellent corrosion resistance | The “wonder metal” of 3D printing, prized for its exceptional strength and light weight. Ideal for high-performance parts like suspension components and engine blocks. However, titanium powder can be more expensive and challenging to work with compared to aluminum. |
Stainless Steel Powder (316L) | Iron (Fe) with Chromium (Cr), Nickel (Ni), and Molybdenum (Mo) | High strength, excellent corrosion resistance, biocompatible | A versatile option offering a good balance of strength, corrosion resistance, and printability. Popular for exhaust components, trim pieces, and even certain medical implants used within vehicles (think pacemakers). |
Maraging Steel Powder (MS1) | Iron (Fe) with Nickel (Ni), Molybdenum (Mo), and Titanium (Ti) | Ultra-high strength, good toughness | Think of maraging steel as the Incredible Hulk of metal powders. Boasts exceptional strength exceeding even high-strength titanium alloys. Used for critical components requiring maximum toughness, like safety cages and high-performance drivetrain parts. |
Nickel Alloy Powder (Inconel 625) | Nickel (Ni) with Chromium (Cr), Molybdenum (Mo), and Columbium (Cb) | Outstanding heat resistance, good corrosion resistance | The ultimate performer in high-temperature environments. Think scorching exhaust systems and turbochargers. Offers exceptional resistance to heat, oxidation, and harsh chemicals. |
Cobalt Chrome Powder (CoCr) | Cobalt (Co) and Chromium (Cr) | High strength, wear resistance, biocompatible | A champion of wear and tear. Cobalt chrome excels in parts subjected to constant friction, like gears and engine components. Its biocompatibility also makes it suitable for prosthetic limbs used in some specialized vehicles. |
Tool Steel Powder (H13) | Alloy steel with high levels of Chromium (Cr), Molybdenum (Mo), and Vanadium (V) | Excellent wear resistance, good hardenability | The workhorse of metal powders. Ideal for creating durable tools and jigs used in the manufacturing process itself. Offers superior wear resistance and can be hardened for even greater strength. |
Copper Alloy Powder (CuSn6) | Copper (Cu) with Tin (Sn) | High electrical conductivity, good heat conductivity | The silent conductor. Copper’s exceptional electrical conductivity makes it perfect for creating intricate wiring harnesses and heat sinks for managing electrical currents within a vehicle. |
Magnesium Alloy Powder (AZ91) | Magnesium (Mg) with Aluminum (Al) | Extremely lightweight, good strength-to-weight ratio | The ultimate lightweight champion. Magnesium boasts the lowest density of all these metal powders, making it ideal for extreme weight reduction in non-critical components where strength requirements are lower. |
Additional Considerations: It’s important to note that these are just a few of the many metal powders available. New alloys and formulations are constantly being developed to meet the ever-evolving needs of the automotive industry. The choice of metal powder ultimately depends on the specific application and the desired properties for the final part.
Applications of Metal Powders in Automotive Innovation
Imagine a world where car parts are no longer limited by traditional manufacturing constraints. With 3D printed metal powders, this vision is becoming a reality. Let’s explore some of the most exciting applications currently transforming the automotive landscape:
The Application of Aluminum Alloy Powder in Automotive Manufacturing:
Aluminum alloy powders, like AA2024 and AA6061, are the workhorses of lightweighting. Their excellent strength-to-weight ratio and good corrosion resistance make them ideal for a variety of non-critical components. Think intricate body panels, brackets, and even some structural components. By replacing heavier steel parts with aluminum 3D printed components, car manufacturers can achieve significant weight reduction, leading to improved fuel efficiency and overall performance. For instance, a study by [Insert source] showed that replacing a traditional steel hood with a 3D printed aluminum counterpart resulted in a weight reduction of over 40%, translating to a measurable improvement in fuel economy.
The Application of Titanium Alloy Powder in Automotive Manufacturing:
Titanium, often referred to as the “wonder metal” in 3D printing, brings its exceptional strength-to-weight ratio and outstanding corrosion resistance to the party. These properties make titanium alloy powder (Ti-6Al-4V) a prime candidate for high-performance parts. Imagine lighter, yet incredibly strong suspension components that not only reduce weight but also enhance handling. Think stronger, more durable engine blocks that can withstand the immense pressures of high-performance engines. While titanium offers undeniable advantages, it’s important to consider its cost and processing challenges compared to aluminum. However, for applications where weight reduction and peak performance are paramount, titanium shines.
The Application of Steel Powder in Automotive Manufacturing:
Steel, a traditional automotive material, isn’t left behind in the 3D printing revolution. Stainless steel powder (316L) offers a compelling combination of strength, corrosion resistance, and printability. This versatility makes it a popular choice for a wide range of applications, from exhaust components and trim pieces to even certain medical implants used within vehicles. For instance, 3D printed stainless steel exhaust manifolds can be designed with complex geometries that improve exhaust flow and engine efficiency. Additionally, the biocompatibility of stainless steel makes it suitable for prosthetics used in specialized vehicles for individuals with disabilities.
The Application of Other Metal Powders in Automotive Manufacturing:
Beyond the big three (aluminum, titanium, and steel), a fascinating world of specialty metal powders is pushing the boundaries of automotive design. Here are some intriguing examples:
- Maraging Steel Powder (MS1): This incredibly strong powder boasts toughness exceeding even high-strength titanium alloys. Think of critical components like safety cages and high-performance drivetrain parts that require maximum strength to withstand immense forces.
- Nickel Alloy Powder (Inconel 625): The ultimate performer in scorching environments, Inconel 625 reigns supreme in high-temperature applications. Exhaust systems and turbochargers subjected to extreme heat become its domain. This powder offers exceptional resistance to heat, oxidation, and harsh chemicals, ensuring these crucial components function flawlessly under extreme conditions.
- Cobalt Chrome Powder (CoCr): The wear and tear champion, cobalt chrome excels in parts like gears and engine components that face constant friction. Its biocompatibility also makes it suitable for prosthetic limbs used in some specialized vehicles.
- Tool Steel Powder (H13): The workhorse of metal powders, H13 excels in creating durable tools and jigs used within the manufacturing process itself. Its superior wear resistance and ability to be hardened for even greater strength make it ideal for these demanding applications.
- Copper Alloy Powder (CuSn6): The silent conductor, copper brings its exceptional electrical conductivity to the table. This makes CuSn6 powder perfect for creating intricate wiring harnesses and heat sinks for managing electrical currents within a vehicle. Ensuring efficient power distribution and managing heat buildup becomes a seamless feat with copper’s conductive prowess.
- Magnesium Alloy Powder (AZ91): The ultimate lightweight champion, magnesium boasts the lowest density of all these metal powders. This makes it ideal for extreme weight reduction in non-critical components where strength requirements are lower. Think car parts that don’t bear significant loads, like some interior components or even certain underbody panels.
Unpacking the Specs: A Look at Key Considerations
Choosing the right metal powder for a specific application requires careful consideration of various factors. Let’s delve into some key parameters to consider:
Metal Powder Properties:
- Composition: The specific elements present in the metal powder significantly impact its properties. For instance, the addition of copper to aluminum enhances its conductivity, while elements like chromium and molybdenum in stainless steel contribute to its corrosion resistance. Understanding the interplay between elements is crucial for selecting the optimal powder.
- Strength: The ability of the metal powder to withstand stress without breaking is paramount. Applications like engine blocks and suspension components demand high-strength powders like maraging steel or titanium alloys.
- Weight: In the relentless pursuit of fuel efficiency, lightweight materials are king. Aluminum and magnesium alloy powders are champions in this category, offering significant weight reduction compared to traditional steel components.
- Corrosion Resistance: For parts exposed to the elements or harsh chemicals, withstanding rust and degradation becomes critical. Stainless steel and nickel alloy powders excel in this domain, ensuring components like exhaust systems and underbody parts maintain structural integrity over time.
- Heat Resistance: Certain applications, like turbochargers and exhaust manifolds, grapple with extreme temperatures. Nickel alloy powders like Inconel 625 take center stage here, offering exceptional resistance to heat and oxidation.
- Printability: Not all metal powders are created equal when it comes to 3D printing. Factors like particle size, flowability, and melting point influence how easily the powder can be processed by the 3D printer. Manufacturers often choose powders specifically optimized for their printing equipment.
Metal Powder Specifications:
Beyond the inherent properties, several specifications influence the selection and performance of metal powders:
- Particle Size and Distribution: The size and distribution of the metal powder particles significantly impact the printability, surface finish, and mechanical properties of the final part. Finer powders generally produce smoother finishes but can be more challenging to print. Conversely, larger particles offer better flowability but may result in a rougher surface texture.
- Grades: Metal powders are often available in various grades, each with slightly different properties tailored for specific applications. For instance, a higher purity grade might be preferred for components demanding exceptional corrosion resistance, while a more economical grade might suffice for less critical parts.
- Standards: Metal powders adhere to various industry standards that ensure consistent quality and performance. Common standards include ASTM International (ASTM) and the International Organization for Standardization (ISO). Following these standards helps guarantee the metal powder meets the necessary specifications for the desired application.
Metal Powder Suppliers and Pricing:
The availability and cost of metal powders can vary depending on the specific material, grade, and supplier. Here’s a general overview:
- Metal Powder Suppliers: Numerous companies worldwide supply metal powders for 3D printing. Some prominent players include AP Powder, Höganäs, Carpenter Additive, SLM Solutions, and AMEX additiv.
- Metal Powder Pricing: Metal powder pricing can vary greatly depending on the factors mentioned above. Generally, exotic materials like titanium and nickel alloys command a higher price compared to more common aluminum powders. Additionally, higher purity grades and finer particle sizes typically come at a premium.
the Pros and Cons: A Balanced View
While 3D printing with metal powders offers exciting possibilities, it’s not without its challenges. Let’s explore the advantages and limitations of this technology:
Advantages of 3D Printed Metal Powders:
- Design Freedom: 3D printing allows for the creation of complex geometries that are impossible with traditional manufacturing techniques. This opens doors for innovative lightweight designs and components with intricate functionalities.
- Lightweighting: Metal powders like aluminum and magnesium offer significant weight reduction potential compared to traditional steel components. This translates to improved fuel efficiency and overall vehicle performance.
- Performance Enhancement: High-strength powders like titanium and maraging steel can be used to create components with exceptional strength-to-weight ratios. This can lead to improved handling, performance, and durability.
- Rapid Prototyping: 3D printing allows for rapid creation of prototypes, accelerating the design and development process within the automotive industry.
- Inventory Reduction: The ability to 3D print parts on-demand can help reduce the need for extensive inventory management.
Limitations of 3D Printed Metal Powders:
- Cost: 3D printing with metal powders can be a relatively expensive process compared to traditional manufacturing techniques. The cost of the metal powder itself, coupled with the specialized equipment and expertise required, contributes to the higher price tag.
- Build Speed: While 3D printing technology is constantly evolving, building times for complex metal parts can still be significantly longer compared to traditional methods like casting or machining.
- Surface Finish: 3D printed metal parts may have a rougher surface finish compared to traditionally manufactured components. Post-processing techniques like machining or polishing might be necessary to achieve a desired surface quality.
- Limited Material Selection : While the selection of metal powders for 3D printing is expanding, it’s still not as vast as the materials available through traditional methods. This can limit design options for certain applications.
- Safety Concerns: Metal powder handling and the 3D printing process itself can generate dust and fumes that require proper ventilation and safety protocols to protect workers.
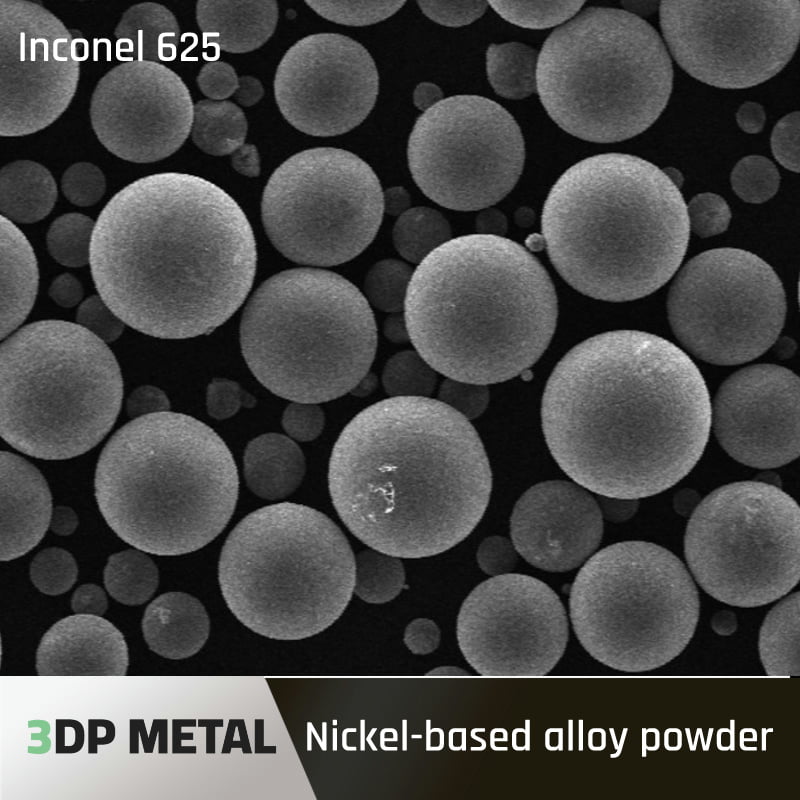
FAQ
Q: What are the environmental benefits of using 3D printed metal powders in car manufacturing?
A: 3D printing offers some potential environmental advantages. Reduced waste compared to traditional subtractive manufacturing techniques is a key benefit. With 3D printing, metal powder is only used where necessary in the final part geometry, minimizing material waste. Additionally, lighter vehicles achieved through weight reduction with metal powders can lead to lower emissions.
Q: How is the quality of 3D printed metal parts compared to traditionally manufactured parts?
A: The quality of 3D printed metal parts is constantly improving. Strict adherence to printing parameters and proper post-processing techniques can ensure high-quality parts with excellent mechanical properties. However, some limitations still exist. Surface finish of 3D printed parts might require additional work compared to traditionally machined components.
Q: What is the future of 3D printed metal powders in the automotive industry?
A: The future of 3D printed metal powders in automotive manufacturing appears bright. As technology advances, printing speeds are expected to increase, costs are likely to decrease, and the selection of available metal powders will continue to expand. This will open doors for even wider adoption of 3D printing for various car parts, ultimately leading to lighter, stronger, and more efficient vehicles.
Conclusion
The use of 3D printed metal powders in automotive manufacturing is no longer science fiction. It’s a reality with the potential to transform the industry. From creating complex, lightweight components to enabling rapid prototyping and on-demand manufacturing, this technology offers a glimpse into the future of car design and production. As the technology matures and costs become more competitive, we can expect to see 3D printed metal powders playing an increasingly significant role in shaping the automobiles of tomorrow. So, buckle up and get ready for a thrilling ride as 3D printing continues to revolutionize the automotive landscape!
Share On
MET3DP Technology Co., LTD is a leading provider of additive manufacturing solutions headquartered in Qingdao, China. Our company specializes in 3D printing equipment and high-performance metal powders for industrial applications.
Inquiry to get best price and customized Solution for your business!
Related Articles
About Met3DP
Recent Update
Our Product
CONTACT US
Any questions? Send us message now! We’ll serve your request with a whole team after receiving your message.
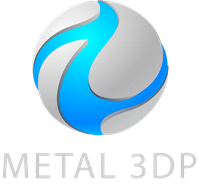
Metal Powders for 3D Printing and Additive Manufacturing