Specific classification of 3D printed metal powders
Table of Contents
Imagine a world where complex metal parts materialize layer-by-layer, conjured from a vat of shimmering dust. This isn’t science fiction; it’s the reality of 3D printed metal powders. But not all these metallic marvels are created equal. Understanding how 3D printed metal powders are classified is crucial for unlocking their hidden potential and crafting the perfect component. Buckle up, because we’re diving deep into the fascinating world of metal powder classification!
Classifying 3D Printed Metal Powders by Chemical Composition
Think of a delicious pot of stew. Its unique flavor profile hinges on the specific ingredients tossed into the pot. Similarly, the chemical makeup of a metal powder dictates the final properties of your 3D printed part. Here’s a breakdown of the main categories:
- Stainless Steels: The workhorses of the 3D printing world, stainless steels offer a winning combination of strength, corrosion resistance, and affordability. Think of them as the Swiss Army knife of metal powders, suitable for everything from medical implants to aerospace components.
- Titanium Alloys: Imagine a featherweight champion with a heavyweight punch. That’s titanium in a nutshell. Offering exceptional strength-to-weight ratios and excellent biocompatibility, titanium alloys like Ti6Al4V are the go-to choice for applications demanding lightness and resilience, like aerospace parts and prosthetics.
- Nickel Alloys: High temperatures? Corrosive environments? Nickel alloys have your back. These robust materials boast superior heat resistance and corrosion defiance, making them ideal for jet engine components, chemical processing equipment, and even parts exposed to harsh marine environments.
- Aluminum Alloys: Lightweight, readily available, and offering good machinability, aluminum alloys are a popular choice for applications where weight reduction is paramount. Think of them as the economical option for non-critical parts like automotive components and housings.
- Other Specialty Alloys: The world of 3D printed metal powders extends beyond these common choices. Specialty alloys like cobalt-chrome (known for its wear resistance) and refractory metals (like tantalum, ideal for high-temperature applications) cater to specific needs in demanding industries.
Choosing the right chemical composition hinges on the desired properties of your final part. Need a lightweight and biocompatible bone implant? Titanium might be your champion. Building a heat exchanger for a power plant? Nickel alloys could be the key to success.
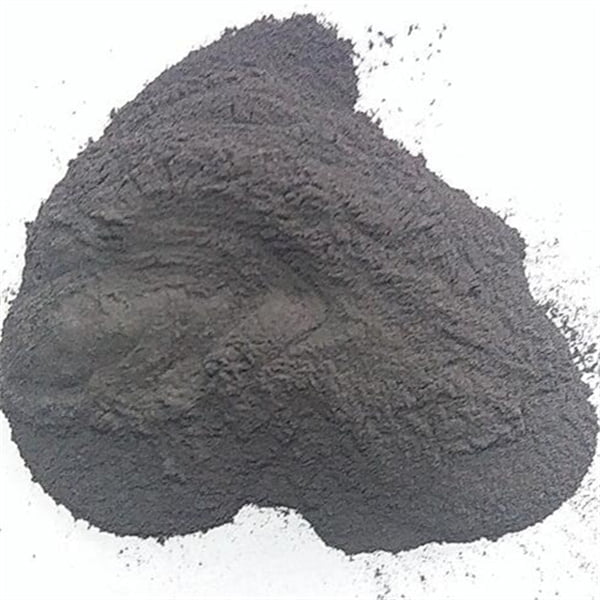
Classify 3D Printed Metal Powders According to Their Particle Size and Morphology
Imagine building a sandcastle. Fine, uniform grains create a smooth, sturdy structure. But what if your sand is a mix of pebbles and dust? The result would be a clunky, unstable mess. The same principle applies to 3D printed metal powders. Here’s how particle size and morphology (shape) influence the process:
- Particle Size Distribution: A well-distributed powder, with a range of particle sizes within a specific limit, ensures good packing density and smooth layer formation during printing. Imagine the sandcastle analogy again – a mix of different-sized grains allows for better packing and a more stable structure. Powders with excessively large particles can lead to poor flow and layer adhesion, while overly fine particles can hinder laser penetration and cause overheating.
- Particle Morphology: The shape of the powder particles also plays a critical role. Spherical particles offer the best flowability and packing density, leading to smoother surface finishes and improved mechanical properties. Elongated or irregular particles, on the other hand, can create challenges with flow and packing, potentially impacting the final quality of the printed part.
The ideal particle size and morphology depend on the specific 3D printing technology being used. For instance, Selective Laser Melting (SLM) often requires finer powders compared to Electron Beam Melting (EBM) due to the differences in energy density used for melting.
Classifying 3D Printed Metal Powders According to Manufacturing Processes
Just like baking a cake requires the right ingredients and technique, the manufacturing process used to create the metal powder influences its suitability for 3D printing. Here’s a peek into the most common methods:
- Gas Atomization: This high-pressure, high-temperature process injects molten metal into a gas stream, creating fine, spherical particles that cool rapidly. Gas-atomized powders are widely used in SLM and other 3D printing technologies due to their excellent flowability and controlled morphology.
- Water Atomization: Similar to gas atomization, but uses a water stream instead of a gas stream. This process can be more economical but often results in less spherical particles compared to gas atomization. Water-atomized powders may be suitable for some 3D printing applications, but careful selection is crucial.
- Plasma Atomization: This cutting-edge technique utilizes an ionized gas stream (plasma) to melt and atomize the metal. Plasma atomization offers tight control over particle size and morphology, making it ideal for producing high-performance powders for demanding applications. However, this process can be more expensive compared to gas or water atomization.
- Electrode Induction-Gas Atomization (EIGA): This hybrid technique combines electric induction melting with gas atomization. EIGA offers precise control over chemistry and minimizes oxygen content in the powder, resulting in high-purity powders suitable for printing critical aerospace components.
Understanding the manufacturing process behind a metal powder provides valuable insights into its suitability for your specific 3D printing needs.
Advantages and Disadvantages of Different Metal Powders
We’ve explored the key classification factors, but the plot thickens! Each type of metal powder offers unique advantages and disadvantages to consider:
Stainless Steel Powders
- Pros: Affordable, good corrosion resistance, readily available in various grades
- Cons: Relatively high density compared to titanium or aluminum, may require post-processing for optimal mechanical properties
Titanium Alloy Powders
- Pros: Excellent strength-to-weight ratio, biocompatible, good corrosion resistance
- Cons: Higher cost compared to stainless steel, more challenging to print due to its higher melting point
Nickel Alloy Powders
- Pros: Exceptional heat and corrosion resistance, suitable for demanding environments
- Cons: High cost, some nickel alloys can be challenging to print due to their crack-prone nature
Aluminum Alloy Powders
- Pros: Lightweight, affordable, good machinability
- Cons: Relatively lower strength compared to other options, not suitable for high-temperature applications
Specialty Alloy Powders
- Pros: Offer unique properties like wear resistance or high-temperature performance
- Cons: Can be very expensive and limited in availability, may require specialized printing expertise
Choosing the right metal powder boils down to a careful evaluation of your project requirements. Consider factors like the part’s desired properties (strength, weight, corrosion resistance), printing technology limitations, and of course, budget.
Finding the Perfect Match: Selecting the Right Metal Powder
Finding the perfect metal powder for your 3D printing project is akin to Goldilocks searching for the “just right” bed – not too coarse, not too fine, but just the right fit. Here are some key questions to ask yourself:
- What are the functional requirements of the final part? Does it need to be lightweight, super strong, or resistant to corrosion?
- What 3D printing technology will you be using? Different technologies may have specific requirements for particle size and morphology.
- What is your budget? Specialty alloys can be significantly more expensive than common materials like stainless steel.
Here’s a helpful analogy: Imagine you’re building a high-performance racing bike. You wouldn’t use the same materials you would for a leisurely cruiser bike. Similarly, the metal powder selection for a jet engine component will differ vastly from the powder chosen for a decorative figurine.
Beyond the technical specifications, consider the aesthetics and post-processing requirements as well. For instance, some metal powders may require extensive post-processing steps to achieve a desired surface finish.
Working with Metal Powders: Safety Precautions are Paramount
Metal powders, while fascinating, can pose health and safety risks if not handled properly. Here are some crucial precautions to remember:
- Metal powders can be flammable or explosive. Always store them in designated containers and maintain a clean work environment free of ignition sources.
- Fine metal powders can be inhaled and irritate the lungs. Wear proper personal protective equipment (PPE) like respirators and gloves when handling powders.
- Metal powders can also irritate the skin and eyes. Wear safety glasses and protective clothing to minimize exposure.
By following these safety protocols, you can ensure a safe and enjoyable 3D printing experience.
FAQ
Q: What is the most common metal powder used in 3D printing?
A: Stainless steel is the most widely used metal powder in 3D printing due to its affordability, good properties, and wide range of available grades.
Q: Are there any eco-friendly options for metal powders?
A: Yes, some manufacturers are exploring the use of recycled metal powders to reduce environmental impact. However, these options may still be limited in availability.
Q: Are there any eco-friendly options for metal powders?
A: Yes, some manufacturers are exploring the use of recycled metal powders to reduce environmental impact. However, these options might still be limited in availability and may not offer the same level of performance as virgin powders.
Q: Can any metal powder be used in a 3D printer?
A: No, it’s generally not recommended to use metal powders from traditional manufacturing processes in 3D printers. These powders are often not optimized for 3D printing and can lead to flow issues, laser/electron beam issues, surface quality problems, and even safety concerns.
Q: What are some resources for learning more about specific metal powders?
- Metal powder manufacturers often provide detailed datasheets with information on composition, particle size distribution, morphology, and recommended applications for their powders.
- Industry associations and research institutions may publish reports and studies on the latest advancements in metal powders for 3D printing.
Share On
MET3DP Technology Co., LTD is a leading provider of additive manufacturing solutions headquartered in Qingdao, China. Our company specializes in 3D printing equipment and high-performance metal powders for industrial applications.
Inquiry to get best price and customized Solution for your business!
Related Articles
About Met3DP
Recent Update
Our Product
CONTACT US
Any questions? Send us message now! We’ll serve your request with a whole team after receiving your message.
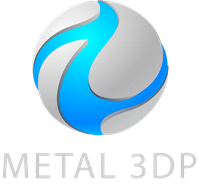
Metal Powders for 3D Printing and Additive Manufacturing
COMPANY
PRODUCT
cONTACT INFO
- Qingdao City, Shandong, China
- [email protected]
- [email protected]
- +86 19116340731