3D printed metal powders:different classification methods
Table of Contents
The world of 3D printing has unveiled a treasure trove of possibilities, revolutionizing the way we design and manufacture objects. But have you ever stopped to wonder about the tiny metallic building blocks that breathe life into these intricate creations? We’re talking about 3D printed metal powders, the unsung heroes behind the scenes.
Just like snowflakes, no two metal powder particles are exactly alike. Their characteristics – size, shape, composition – play a critical role in determining the final properties and success of your 3D printed masterpiece. So, buckle up as we delve into the fascinating world of metal powder classification, exploring the various methods that categorize these metallic marvels.
3D printed metal powders:Classified by Raw Materials
The foundation of any good story starts with its characters, and in the world of metal powders, the characters are the raw materials themselves. Here’s a breakdown of the two main categories:
- Ferrous Powders: Imagine the ironclad knights of yore. Ferrous powders, dominated by iron, are the sturdy warriors of the 3D printing realm. They offer excellent strength and are often used for applications like tools, machine parts, and even structural components. Think of them as the workhorses of the industry, getting the job done with unwavering reliability. Some popular examples include steel powders, stainless steel powders, and low-alloy steel powders.
- Non-Ferrous Powders: Now, picture the dazzling diversity of a medieval marketplace. Non-ferrous powders, encompassing a wider range of elements like aluminum, titanium, and nickel, bring a touch of variety to the party. They offer a lighter weight, superior corrosion resistance, and sometimes even unique properties like high conductivity. These versatile performers cater to a broader spectrum of applications, from aerospace components to biomedical implants.
The choice between ferrous and non-ferrous powders hinges on the desired properties of the final product. Do you need the robust strength of steel or the lightweight agility of aluminum? Understanding the strengths and limitations of each material is key to selecting the perfect powder for your project.
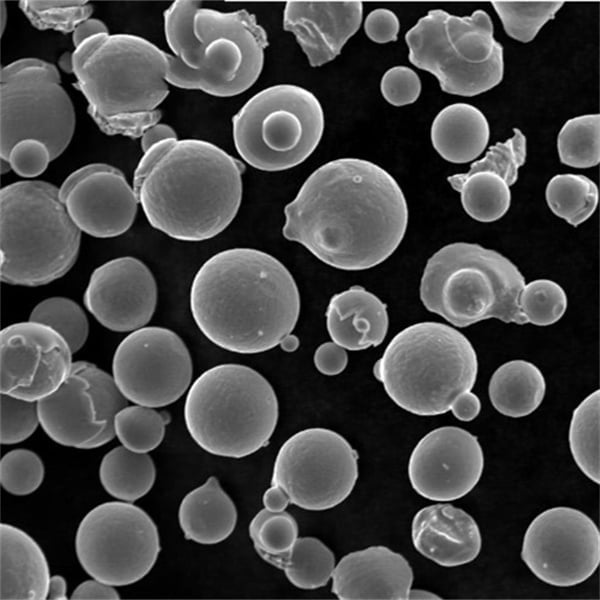
Classified by Granularity
Imagine a sandbox overflowing with grains of different sizes. Similarly, metal powders come in a variety of particle sizes, measured in micrometers (µm). This granularity, as it’s called, significantly impacts the printing process and final product:
- Fine Powders (less than 20 µm): Think of these as the tiny ballerinas of the powder world. Their small size allows for intricate details and smooth surface finishes. However, they can be challenging to handle due to their flowability and potential for agglomeration (clumping). Fine powders are often used for applications requiring high precision, like jewelry or medical implants.
- Medium Powders (20-100 µm): These are the workhorses, offering a good balance between detail and handling ease. They flow well and are suitable for a wide range of applications, including automotive parts and prototypes.
- Coarse Powders (greater than 100 µm): Imagine them as the burly bodybuilders of the group. Coarse powders offer superior strength and are often used for applications requiring high load-bearing capacity, such as structural components and tools.
The ideal particle size depends on the specific 3D printing technology being used. For instance, Selective Laser Melting (SLM) generally works best with finer powders, while Binder Jetting can handle a wider range of granularity.
Classified by Production Process
Metal powders don’t magically appear – they undergo a series of transformations before reaching your 3D printer. Here are some of the common production methods:
- Atomization: Imagine molten metal raining down and solidifying into tiny droplets. This technique, called atomization, uses various methods like gas atomization or water atomization to create spherical powders with good flowability.
- Mechanical Milling: Think of a tireless chef pounding spices in a mortar and pestle. Mechanical milling utilizes high-energy grinding processes to break down larger metal pieces into fine powders. This method offers more control over particle shape but may result in less spherical morphologies.
- Electrolysis: This process is like a magic trick where electricity transforms metal ions in a solution into a metallic powder on the cathode. Electrolytic powders are known for their high purity and can be well-suited for specific applications like biomedical implants.
The choice of production process depends on factors like the desired powder characteristics, material type, and cost considerations.
Classification by Application Field
Metal powders aren’t one-size-fits-all solutions. Different applications demand specific properties from the powder. Here’s a glimpse into some popular application fields and their ideal powder matches:
- Aerospace: Soaring to new heights requires materials that are lightweight yet incredibly strong. Here, aluminum and titanium powders shine, offering the perfect blend of these properties. Additionally, their excellent corrosion resistance makes them ideal for withstanding harsh weather conditions.
- Medical: Biocompatible and high-precision are the watchwords in the medical field. For applications like implants and prosthetics, powders like titanium and cobalt-chromium alloys are preferred due to their biocompatibility and exceptional strength. Fine-grained powders ensure a smooth surface finish, crucial for osseointegration (fusion with bone) in implants.
- Automotive: The automotive industry demands a balance of strength, weight reduction, and affordability. Nickel alloys and stainless steel powders offer a compelling combination of these characteristics. They’re strong enough for critical components like engine parts, yet lighter than traditional materials, contributing to improved fuel efficiency.
- Tooling: Durability is paramount when it comes to tools. Steel powders, particularly tool steels, take center stage here. Their exceptional wear resistance ensures tools can withstand repeated use and maintain their cutting edge.
Understanding these application-specific needs is crucial for selecting the optimal metal powder.
Classify by Shape
Not all metal powder particles are created equal. Beyond size, their shape also plays a role:
- Spherical Powders: Imagine tiny marbles – these are the ideal shapes for most 3D printing processes. Their smooth, round form ensures good flowability, allowing for even distribution during printing. This translates to better packing density and potentially stronger finished parts.
- Irregular Powders: Think of a handful of crushed crystals. These irregular-shaped powders can be produced during mechanical milling. While they may not flow as well as spherical powders, they can offer advantages in certain situations. For instance, their faceted surfaces can sometimes improve inter-particle bonding, leading to a stronger final product.
The choice between spherical and irregular powders depends on the specific printing technology and desired properties of the final part.
Putting the Pieces Together
Now that you’ve explored the fascinating world of metal powder classification, you’re well on your way to becoming a 3D metal printing aficionado! Here are some key takeaways to remember:
- Consider the application: What properties do you need in the final product – strength, weight, corrosion resistance, or biocompatibility? Choose a powder that aligns with those needs.
- Material matters: Ferrous or non-ferrous? Understanding the base material’s characteristics is crucial for selecting the right powder.
- Size it up: Granularity plays a significant role in detail, handling ease, and the printing process itself. Match the particle size to your specific needs and printing technology.
- Shape it right: Spherical or irregular? Consider the flowability and potential benefits of each shape for your application.
Remember, selecting the optimal metal powder is just the first step in the exciting journey of 3D metal printing. By understanding these classification methods, you’ll be well-equipped to navigate this dynamic realm and unlock the power of 3D printed metal marvels!
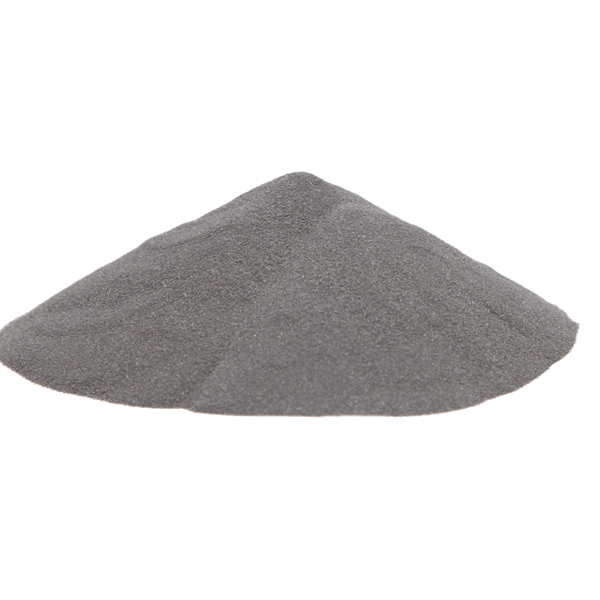
FAQ
What are the advantages and disadvantages of 3D printed metal compared to traditional manufacturing methods?
Feature | 3D Printed Metal | Traditional Manufacturing |
---|---|---|
Design complexity | High – Can create intricate geometries | Limited – Complex designs can be challenging and expensive |
Waste reduction | Potentially lower waste compared to subtractive techniques | Can generate significant scrap material |
Lead time | Can be faster for prototypes and low-volume production | May be slower for high-volume production |
Cost | Currently higher for some metals compared to traditional methods | Costs can be lower for high-complexity parts |
What are some of the limitations of 3D printed metal?
- Cost: While costs are coming down, 3D printed metal can still be expensive compared to some traditional methods for high-volume production.
- Surface finish: Surface roughness can be a challenge, depending on the printing technology and powder characteristics. Post-processing techniques may be needed to achieve a desired finish.
- Material limitations: Not all metals are readily available as powders for 3D printing. The selection of materials is still evolving.
Conclusion
The future of 3D printed metal is brimming with possibilities. From a wider material palette and faster printing speeds to increased customization and sustainability benefits, this technology has the potential to transform how we design, manufacture, and interact with metal objects. By addressing the existing challenges and fostering collaboration between researchers, engineers, and industry leaders, we can unlock the true potential of 3D printed metal and usher in a new era of innovation and creation.
Share On
MET3DP Technology Co., LTD is a leading provider of additive manufacturing solutions headquartered in Qingdao, China. Our company specializes in 3D printing equipment and high-performance metal powders for industrial applications.
Inquiry to get best price and customized Solution for your business!
Related Articles
About Met3DP
Recent Update
Our Product
CONTACT US
Any questions? Send us message now! We’ll serve your request with a whole team after receiving your message.
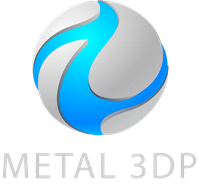
Metal Powders for 3D Printing and Additive Manufacturing
COMPANY
PRODUCT
cONTACT INFO
- Qingdao City, Shandong, China
- [email protected]
- [email protected]
- +86 19116340731