different 3D printed metal powders:different application scenarios
Table of Contents
Imagine a world where complex metal objects, once limited by traditional manufacturing constraints, can be conjured from thin air. Well, that world is already here, thanks to the revolutionary power of 3D printing. But what fuels this metallic alchemy? The answer lies in a seemingly unremarkable substance – 3D printed metal powders. These fine, granular particles hold the key to unlocking a universe of possibilities in various industries.
This comprehensive guide delves into the fascinating realm of 3D printed metal powders, exploring their classification, properties, and how they shape the future of manufacturing.
Classification by Raw Material Morphology
Just like snowflakes, no two metal powder particles are exactly alike. Their morphology, or physical shape, plays a crucial role in the 3D printing process. Here’s a breakdown of the two main categories:
- Spherical Powders: Picture tiny metal marbles. These near-perfect spheres offer exceptional flowability, meaning they move smoothly and evenly during the printing process. This translates to better layer formation, smoother surface finishes, and minimal waste. Think of them as the well-oiled gears that keep the printing process running efficiently.
- Irregular Powders: Unlike their spherical counterparts, these powders possess a more haphazard, angular shape. While this might seem like a disadvantage, it can actually be beneficial in certain situations. The irregular shapes can interlock more tightly, potentially leading to stronger final parts. Imagine them as puzzle pieces that fit together snugly, creating a more robust structure.
The choice between spherical and irregular powders depends on the desired outcome. Spherical powders are generally preferred for intricate designs and smooth finishes, while irregular powders might be chosen for applications where strength is paramount.
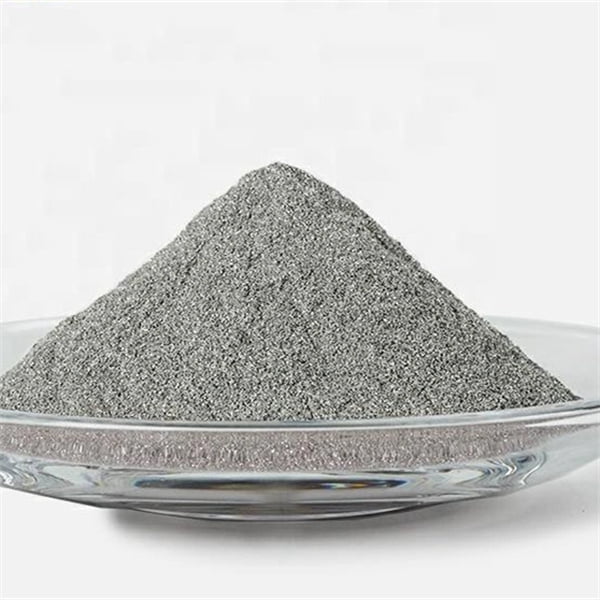
Classification by Material Type
The world of 3D printed metal powders boasts a diverse range of materials, each with its own unique set of properties:
- Stainless Steel Powders: The workhorse of the metal powder family, stainless steel offers a compelling combination of strength, corrosion resistance, and affordability. It’s a popular choice for applications across various industries, from medical implants to aerospace components. Think of it as the adaptable chameleon, readily conforming to diverse needs.
- Titanium Powders: Renowned for their exceptional strength-to-weight ratio and biocompatibility, titanium powders are the go-to choice for demanding applications. From lightweight aircraft parts to life-saving orthopedic implants, titanium’s strength and affinity for the human body make it a true champion.
- Aluminum Powders: When lightness is the ultimate goal, aluminum powders take center stage. Offering a beautiful silver finish and excellent machinability, aluminum is ideal for applications where weight reduction is critical, such as automotive components and aerospace parts. Imagine it as the featherweight champion, providing exceptional performance without the extra bulk.
- Nickel-Based Alloys: For high-temperature environments where things get hot and heavy, nickel-based alloys step up to the plate. These robust powders boast exceptional heat resistance and resistance to corrosion, making them perfect for applications like jet engine components and downhole oil drilling tools. Think of them as the fireproof warriors, standing strong even in the face of extreme heat.
This is just a glimpse into the vast array of 3D printed metal powders available. From exotic options like cobalt chrome to custom-designed alloys, the possibilities are constantly expanding, pushing the boundaries of what’s possible in manufacturing.
Application Scenarios of Different Types of 3D Printed Metal Powders
Now that we’ve explored the different types of metal powders, let’s see how they translate into real-world applications:
- Aerospace Industry: Here, weight is a critical factor. Aluminum and titanium powders shine, enabling the creation of lightweight yet incredibly strong aircraft parts, leading to improved fuel efficiency and overall performance.
- Medical Industry: Biocompatible materials like titanium and cobalt chrome are revolutionizing the field of medical implants. 3D printed prosthetics can be customized to perfectly fit individual patients, offering a new level of comfort and functionality.
- Automotive Industry: From lightweight aluminum engine components to intricate stainless steel fuel injectors, 3D printed metal powders are driving innovation in the automotive sector. They enable the creation of complex, high-performance parts that would be difficult or impossible to manufacture using traditional methods.
- Consumer Goods: The possibilities extend beyond the industrial realm. 3D printed metal powders are opening doors for creating unique and personalized jewelry pieces, decorative art objects, and even custom-designed hardware. Imagine a world where you can design and print your own door handles or unique metal sculptures – the future is brimming with creative potential.
Choosing the right metal powder for a specific application requires careful consideration of factors like the desired strength, weight, corrosion resistance, biocompatibility, and of course, cost.
Advantages and Considerations of Using 3D Printed Metal Powders
While 3D printed metal powders offer a treasure trove of benefits, it’s important to acknowledge some considerations before diving headfirst into this innovative technology.
Advantages:
- Design Freedom: Unlike traditional manufacturing techniques that are limited by rigid tooling, 3D printing with metal powders unlocks a world of design freedom. Complex geometries, intricate lattice structures, and even internal channels can be printed with relative ease. Imagine being able to design a component with internal pathways for fluids or intricate cooling systems – a feat that would be near impossible with traditional methods.
- Lightweighting: As we saw earlier, certain metal powders like aluminum and titanium excel in creating lightweight yet robust parts. This translates to significant advantages in industries like aerospace and automotive, where every gram saved can contribute to improved fuel efficiency and performance.
- Rapid Prototyping: Gone are the days of lengthy and expensive prototyping processes. 3D printing with metal powders allows for rapid creation of functional prototypes, enabling designers and engineers to iterate quickly and test their ideas efficiently. This significantly reduces development timelines and costs.
- Mass Customization: 3D printing empowers a shift towards mass customization. Imagine being able to produce customized metal parts in small batches, catering to specific needs or niche applications. This opens doors for personalized medical implants, one-of-a-kind jewelry pieces, and even custom tools tailored to individual tasks.
- Reduced Waste: Traditional manufacturing processes often generate significant scrap material. 3D printing with metal powders offers a more sustainable approach. Unused powder can often be recycled and reused, minimizing waste and environmental impact.
Considerations:
- Cost: While costs are steadily decreasing, 3D printing metal powders can still be a relatively expensive proposition compared to traditional manufacturing techniques, particularly for high-volume production runs. The cost of the metal powder itself, coupled with the specialized equipment and expertise required, can be significant factors to consider.
- Surface Finish: While advancements are being made, surface finishes achievable with 3D printed metal powders may not always match the smoothness attainable with traditional methods like machining. In some cases, post-processing techniques like polishing or sandblasting might be necessary to achieve the desired finish.
- Material Limitations: While the material palette for 3D printed metal powders is expanding, it’s not as vast as traditional manufacturing options. Certain specialty metals or alloys might not yet be readily available in a printable powder form.
- Post-Processing: Depending on the specific application and desired outcome, 3D printed metal parts might require post-processing steps like heat treatment or support structure removal. This can add to the overall processing time and complexity.
Choosing the Right Metal Powder
With a diverse range of metal powders available, selecting the right one for your project requires careful consideration of several key factors:
- Desired Properties: The first step is to identify the essential properties your final part needs to possess. Is strength paramount? Does it need to be lightweight? Corrosion resistance or biocompatibility a factor? Understanding these needs will guide your material selection process.
- Application Requirements: The intended use of the part plays a crucial role. For instance, a lightweight component for the aerospace industry might call for aluminum powder, while a high-temperature application like a jet engine component might necessitate a nickel-based alloy.
- 3D Printing Process: Different 3D printing processes have varying compatibility with specific metal powders. Understanding the limitations and capabilities of your chosen printing method is crucial for selecting a compatible powder material.
- Cost Considerations: As discussed earlier, cost can be a significant factor. While some metal powders like stainless steel offer affordability, exotic options or custom alloys might come with a higher price tag. Balance your desired properties with budgetary constraints.
Expert Tip: Consulting with a qualified 3D printing service provider can be invaluable in navigating the selection process. Their expertise can help you identify the most suitable metal powder for your specific needs and application.
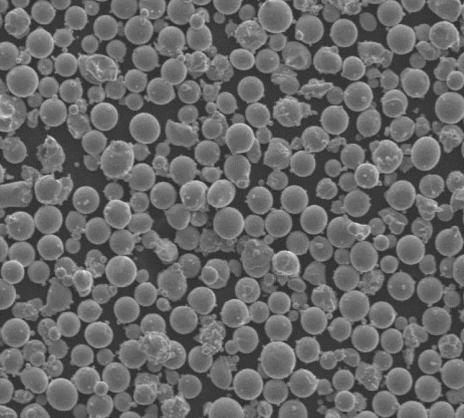
FAQ
Here are some frequently asked questions regarding 3D printed metal powders, answered in a clear and concise format:
Question | Answer |
---|---|
What are the benefits of using 3D printed metal powders compared to traditional manufacturing techniques? | 3D printing offers design freedom, enables lightweighting, facilitates rapid prototyping, allows for mass customization, and reduces waste. |
What are some of the limitations of using 3D printed metal powders? | Cost, surface finish limitations, material availability, and the need for post-processing can be considerations. |
What are some of the most common types of 3D printed metal powders? | Stainless steel, titanium, aluminum, and nickel-based alloys are popular choices. |
The Future of 3D Printed Metal Powders
The world of 3D printed metal powders is a dynamic and ever-evolving landscape. Here’s a peek into some of the exciting advancements shaping the future of this technology:
- Multi-Material Printing: Imagine being able to print a single object using a combination of different metal powders. This opens doors for creating parts with unique properties in localized areas. For instance, a lightweight core structure could be combined with a high-strength outer shell, all within the same printed piece.
- Nanopowders: The introduction of even finer metal powders, venturing into the realm of nanoparticles, holds immense potential. These miniscule particles could enable the creation of incredibly detailed and intricate structures, pushing the boundaries of design complexity and functionality.
- Advanced Alloys: Researchers are constantly developing new and improved metal alloys specifically designed for 3D printing. These custom-designed materials could offer superior properties like exceptional strength, enhanced heat resistance, or even tailored biocompatibility for medical applications.
- Sustainable Powders: Environmental consciousness is at the forefront of many industries. The development of metal powders derived from recycled materials or utilizing more eco-friendly production processes is a promising area of exploration.
- Reduced Printing Costs: As 3D printing technology matures and production scales up, the cost of metal powders and printing processes is anticipated to decrease. This will make this technology more accessible to a wider range of industries and applications.
Conclusion
3D printed metal powders represent a transformative technology with the power to revolutionize various industries. From enabling the creation of lightweight and high-performance aerospace components to facilitating the development of customized medical implants, the possibilities are truly boundless. As the technology continues to evolve, with advancements in material science, printing processes, and cost reduction, we can expect to see even more groundbreaking applications emerge in the years to come.
The future of manufacturing is undoubtedly intertwined with the continued development of 3D printed metal powders. This exciting technology holds the key to unlocking a new era of design freedom, innovation, and efficiency, shaping the way we create objects and pushing the boundaries of what’s possible.
Share On
MET3DP Technology Co., LTD is a leading provider of additive manufacturing solutions headquartered in Qingdao, China. Our company specializes in 3D printing equipment and high-performance metal powders for industrial applications.
Inquiry to get best price and customized Solution for your business!
Related Articles
About Met3DP
Recent Update
Our Product
CONTACT US
Any questions? Send us message now! We’ll serve your request with a whole team after receiving your message.
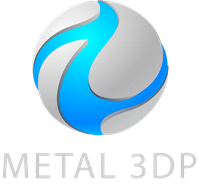
Metal Powders for 3D Printing and Additive Manufacturing
COMPANY
PRODUCT
cONTACT INFO
- Qingdao City, Shandong, China
- [email protected]
- [email protected]
- +86 19116340731