3D Printing Aluminum Alloys
Table of Contents
3d printing aluminum alloys offer several beneficial characteristics like high strength-to-weight ratio, excellent thermal conductivity, and corrosion resistance that make them suitable materials for 3D printing applications across automotive, aerospace, consumer goods, and other industries.
Selective laser melting (SLM) and direct metal laser sintering (DMLS) are the primary 3D printing processes used for aluminum alloy powders. The powders particles are fused together layer-by-layer using a high power laser to construct complex and customizable component geometries.
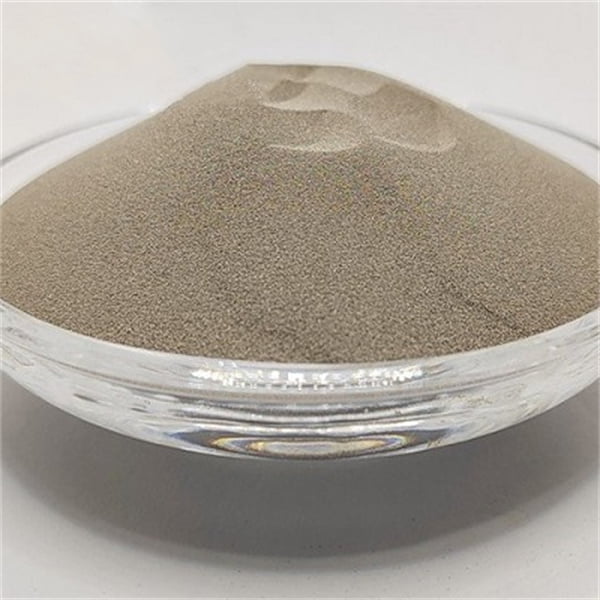
Types of 3d printing aluminum alloys
Alloy | Composition | Printing Process | Properties | Applications |
---|---|---|---|---|
AlSi10Mg | Aluminum (Al) + Silicon (Si) (10%) + Magnesium (Mg) | Laser Powder Bed Fusion (LPBF) | • Good balance of strength, ductility, and toughness • Excellent weldability • Age-hardenable for increased strength | • Aerospace components (lightweight structures) • Automotive parts (brackets, engine components) • Electronic packaging |
AlSi7Mg (F357) | Aluminum (Al) + Silicon (Si) (7%) + Magnesium (Mg) | LPBF | • Similar properties to AlSi10Mg, but slightly lower strength • Easier to print due to lower melting point | • General purpose applications requiring good strength-to-weight ratio • Fluid handling components • Brackets and housings |
Al2139 | Aluminum (Al) + Copper (Cu) (4%) + Magnesium (Mg) | LPBF | • High strength and fatigue resistance • Good machinability | • Aerospace components requiring high strength • Automotive parts (suspension components) |
6061 | Aluminum (Al) + Magnesium (Mg) (0.9%) + Silicon (Si) (0.6%) + Copper (Cu) (0.3%) | LPBF (limited), Binder Jetting (BJ) | • Excellent corrosion resistance • Good machinability and weldability • Moderate strength | • Prototypes and functional parts requiring good all-around properties • Architectural components • Heat sinks |
7075 | Aluminum (Al) + Zinc (Zn) (5.6%) + Magnesium (Mg) (2.5%) + Copper (Cu) (1.6%) | LPBF (limited), Electron Beam Melting (EBM) | • Very high strength-to-weight ratio • Excellent wear resistance • Not weldable | • Aerospace components requiring high strength and low weight • Sporting goods (bicycle frames, baseball bats) |
Scalmalloy | Aluminum (Al) + Scandium (Sc) (4%) + Magnesium (Mg) (6%) | LPBF | • Exceptional strength-to-weight ratio, exceeding 7075 • Excellent corrosion resistance • High crack resistance | • High-performance aerospace components • Defense applications requiring lightweight armor |
Composition of 3d printing aluminum alloys
Alloy Designation | Primary Alloying Elements | Additional Elements | Properties | Applications |
---|---|---|---|---|
AlSi10Mg | Silicon (10%) | Magnesium (0.3-0.5%) | * Excellent castability (adapted from casting applications) * Good weldability * High strength and toughness * Good corrosion resistance | * General purpose applications * Automotive components * Aerospace components (non-critical) * Brackets and housings * |
AlSi7Mg (F357) | Silicon (7%) | Magnesium (0.3-0.5%) | * Similar properties to AlSi10Mg, but slightly lower strength * Excellent castability * Good weldability * Good corrosion resistance | * Similar applications to AlSi10Mg, often used when a bit lower weight is desired * Engine components * Fluid handling components |
AlSi12 | Silicon (12%) | * High strength and wear resistance * Good castability * Moderate weldability * Lower corrosion resistance compared to AlSi10Mg and F357 | * Wear plates * Gears * Sand casting applications (often used as a starting point for 3D printed parts due to familiarity with the material) | |
Scalmalloy | Scandium (4.0-4.4%) | Magnesium (0.3-0.5%) | * Exceptional strength-to-weight ratio * Excellent corrosion resistance * Good weldability * Requires heat treatment for optimal properties | * Aerospace components (high-performance) * Automotive components (weight critical) * Defense applications |
EOS Aluminium Al2139 AM | Not publicly disclosed (likely Aluminum-Magnesium-Silicon) | * Developed specifically for additive manufacturing * Good strength at elevated temperatures (up to 200°C) * Improved processability compared to standard casting alloys * Requires heat treatment for optimal properties | * Aerospace components requiring high-temperature performance * Automotive components * Heat exchanger components |
Characteristics of 3D Printable Aluminum
Attribute | Details |
---|---|
Surface Finish | Powder adhesion can leave semi-rough, stepped surface profile |
Accuracy | Generally high dimensional accuracy up to ±0.1% is possible |
Anisotropy | Directionally weaker mechanical properties observed |
Porosity | <1% porosity achieved under optimized SLM parameters |
Alloy Flexibility | Many 2xxx, 5xxx, 6xxx, and 7xxx grades printable |
Applications of 3d printing aluminum alloys
Industry | Typical Applications |
---|---|
Aerospace | Aircraft ductwork, heat exchangers, structural brackets |
Automotive | Custom brackets, supports, heat sinks, tooling |
Architecture | Lightweight panels, decorative lattices, small sculptures |
Medical | Firmware like surgical instruments, implants |
Electronics | Heat dissipation devices like heat sinks |
Defense | Low volume parts with reduced lead times |
Aluminum Powder Specifications for Additive Manufacturing
Parameter | Type/Range |
---|---|
Materials | AlSi10Mg, AlSi7Mg0.6, AlSi12, AlSi9Cu3 |
Particle size | 25 to 65 microns |
Particle shape | Mostly spherical, some satellites allowed |
Apparent density | Around 2.67 g/cc |
Flow rate | <30 s/50 g per ASTM B964 |
Residual oxygen | <0.4% for high tensile strength |
Leading Suppliers of 3d printing aluminum alloys
Supplier | Specialty | Key Products | Applications | Additional Services |
---|---|---|---|---|
Elementum 3D | Innovative Powders | Gas-atomized aluminum alloy powders, including traditional and dispersion-strengthened variants | Aerospace, automotive, defense | Material development, application engineering, printing parameter optimization |
APWorks | High-Performance Alloys | Scalable Aluminum Silicon Magnesium (AlSiMg) alloy for Laser Beam Melting (LBM) | Automotive components, robotics, industrial machinery | Design for Additive Manufacturing (DFAM) consulting, post-processing services |
SLM Solutions | Established Manufacturer | Aluminum alloys optimized for Selective Laser Melting (SLM) process, including AlSi10Mg and Scalmalloy | Medical implants, aerospace components, heat exchangers | Machine sales and support, parameter development for specific alloys |
EOS GmbH | Multi-Process Compatibility | Aluminum alloys compatible with both Laser Beam Melting (LBM) and Electron Beam Melting (EBM) technologies | Aerospace parts, consumer electronics, medical devices | Consulting on machine selection and process optimization, training programs |
Höganäs | Metal Powder Expertise | Gas-atomized aluminum powders with tight size and morphology control | Heat exchangers, automotive components, electronics enclosures | Powder characterization and testing, collaboration on new alloy development |
Royal Alloy | Diverse Alloy Portfolio | Wide range of aluminum alloy powders, including scandium and lithium additions for enhanced performance | Aerospace components, defense applications, high-performance heat sinks | Material selection guidance, printability testing, custom powder development |
Norsk Hydro | Sustainable Production | Aluminum alloy powders produced with a focus on minimal environmental impact | Automotive parts, architectural components, consumer electronics | Life cycle assessment (LCA) data for materials, support for sustainable manufacturing practices |
ExOne | Binder Jetting Technology | Aluminum alloys specifically formulated for binder jetting additive manufacturing (BJAM) | Automotive prototypes, sand casting molds, industrial tooling | Design for Additive Manufacturing (DFAM) services, post-processing expertise for BJAM parts |
DMG Mori Seiki | Integrated Solutions | Aluminum alloy powders alongside compatible metal 3D printers | Tooling and molds, medical implants, aerospace components | Machine sales and service, training on metal additive manufacturing workflows |
Carpenter Additive Manufacturing | Specialty Alloys | Aluminum alloys with high strength-to-weight ratios and improved corrosion resistance | Marine components, oil and gas equipment, chemical processing applications | Material selection support, application engineering services, prototyping assistance |
Pros and Cons of 3D Printed Aluminum
Feature | Pros | Cons |
---|---|---|
Design Freedom | Unmatched Complexity: Allows for intricate lattice structures, internal channels, and lightweighting features impossible with traditional methods. Enables designers to push boundaries and create high-performance parts. Rapid Prototyping: Enables quick iteration and testing of designs, reducing development time and cost. | Support Structures: Complex geometries often require intricate support structures, adding post-processing time and potentially creating unwanted surface textures. |
Material Properties | Excellent Strength-to-Weight Ratio: Aluminum offers a good balance between weight and strength, making it ideal for applications like aerospace and automotive where weight reduction is crucial. Corrosion Resistance: Many aluminum alloys boast excellent resistance to corrosion, particularly valuable for parts exposed to harsh environments. | Anisotropy: The layered nature of 3D printing can lead to anisotropic properties, meaning the strength of the material can vary depending on the printing direction. This may require design adjustments for certain applications. Porosity: Depending on the printing process, small voids or pores can be present within the material, potentially impacting mechanical properties. Post-processing techniques like hot isostatic pressing (HIP) can mitigate this. |
Manufacturing | Reduced Lead Time: 3D printing allows for on-demand production, eliminating the need for complex tooling and minimizing lead times for prototypes or low-volume parts. Minimal Material Waste: The additive nature of 3D printing significantly reduces material waste compared to traditional subtractive manufacturing methods. | High Cost: The technology and equipment for 3D printing aluminum are still relatively expensive, making it less cost-effective for high-volume production compared to traditional methods. Build Time: Printing complex metal parts can be time-consuming, impacting overall production speed. |
Post-Processing | Surface Finish: While some 3D printing technologies offer good surface finishes, roughness is a common concern. Post-processing techniques like machining, polishing, or sandblasting may be necessary for certain applications. Heat Treatment: Specific aluminum alloys may require heat treatment after printing to achieve optimal mechanical properties. | Additional Cost and Time: Post-processing adds to the overall production time and cost of the part. |
Applications | Aerospace: The ability to create lightweight, high-strength components with complex geometries makes 3D printed aluminum ideal for aerospace applications like heat exchangers, brackets, and structural components. Automotive: Weight reduction is a major concern in the automotive industry. 3D printed aluminum components can be used for parts like wheels, engine components, and lightweight chassis structures. Medical: Biocompatible aluminum alloys can be used to create custom prosthetics and implants. | Limited Applications for High-Stress Components: Due to potential anisotropy and porosity, 3D printed aluminum may not be suitable for all high-stress applications. Careful design and material selection are crucial. |
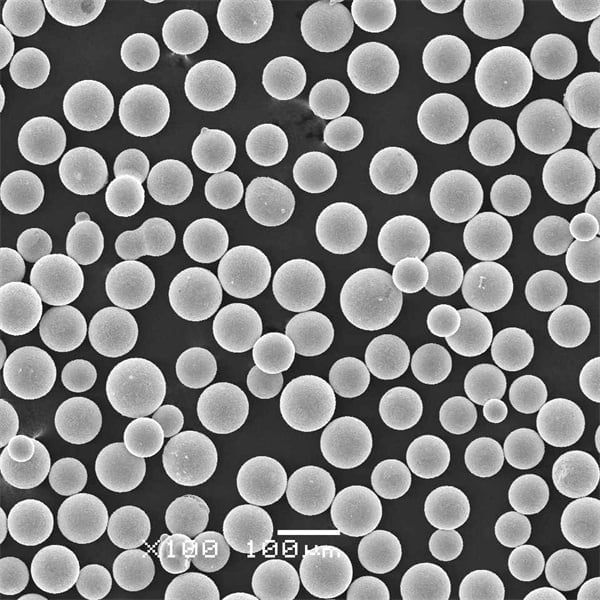
FAQ
Q: Which aluminum alloy is best suited for additive manufacturing?
A: AlSi10Mg is the most widely adopted aluminum alloy offering a good combination of fluidity, strength, hardness and corrosion resistance combined with compatibility across various printers.
Q: Does build orientation affect properties of 3D printed aluminum components?
A: Yes, building vertically can exhibit 20-30% lower tensile and yield strengths versus horizontally built parts due to layer-by-layer construction. Mechanical performance also varies depending on loading parallel or perpendicular to layers.
Q: What solution heat treatments can enhance aluminum properties?
A: T6 heat treatment (solubilize then artificially age harden) of some additively manufactured alloys like AlSi10Mg can significantly increase tensile strength, hardness and ductility compared to as-built state.
Q: How are surface finishes improved for additively made aluminum parts?
A: Various finishing procedures like sand blasting, bead blasting, laser polishing, CNC machining, grinding or linishing can help smooth out the stepped contours typically observed on as-built aluminum surfaces from powder-based printing.
Q: Does aluminum powder reuse affect 3D printed part properties?
A: Recycling aluminum build powder upto 10-20 times typically does not impact mechanical performance. But beyond around 25 reuse cycles, declining powder flowability, lower density, and higher oxygen/nitride impurities can start deteriorating material quality and strengths.
Share On
MET3DP Technology Co., LTD is a leading provider of additive manufacturing solutions headquartered in Qingdao, China. Our company specializes in 3D printing equipment and high-performance metal powders for industrial applications.
Inquiry to get best price and customized Solution for your business!
Related Articles
About Met3DP
Recent Update
Our Product
CONTACT US
Any questions? Send us message now! We’ll serve your request with a whole team after receiving your message.