The advantages of Plasma atomization for 3D Printing Metal Powder
Table of Contents
Imagine holding the future in your hands – a future where complex metal objects are precisely crafted layer by layer, not through conventional methods like welding or machining, but through the magic of 3D Printing Metal Powder. But what about the building blocks of this future? Enter the world of metal powders, the heart and soul of 3D Printing Metal Powder, and specifically, plasma atomized metal powders, renowned for their superior qualities.
Highly Spherical Particles: The Key to Flawless Printing
One of the most crucial advantages of plasma atomization lies in the highly spherical particles it produces. Unlike other methods that might create irregular shapes, plasma atomization utilizes an intricate dance of heat and pressure. Imagine a molten metal stream encountering a searing plasma torch, disintegrating into tiny droplets that solidify rapidly in mid-air. This rapid cooling process prevents the formation of unwanted crystal structures, resulting in near-perfect spheres.
The significance of these spherical particles cannot be overstated. They flow more smoothly during the printing process, leading to consistent layer formation and minimized printing defects. Think of it like building a house with uniform, perfectly shaped bricks; the final structure will be stronger, more precise, and visually appealing compared to one built with irregular bricks.
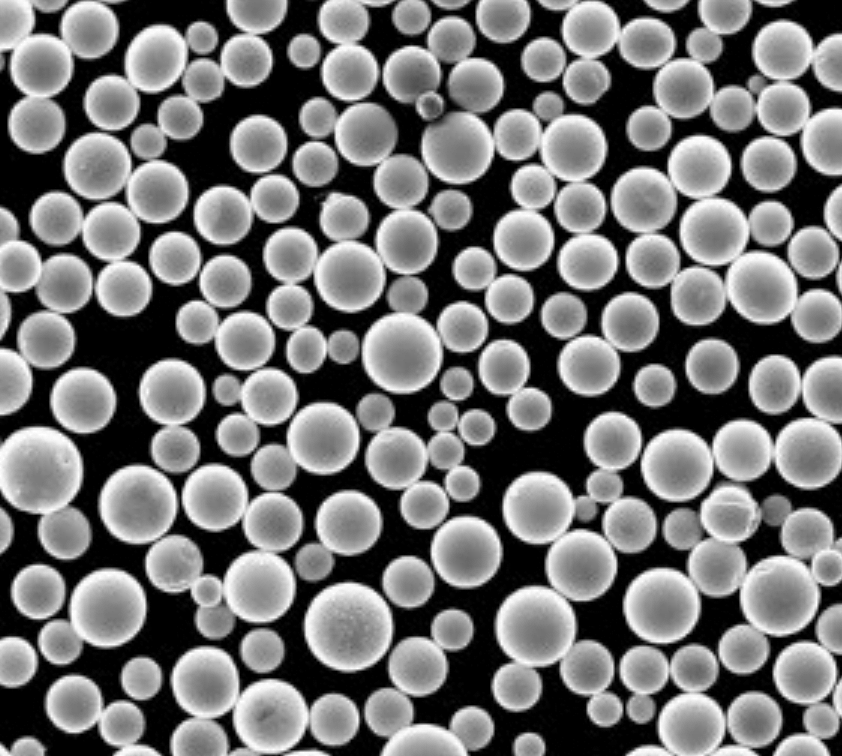
Faster Production: Printing the Future at Speed
Another advantage of plasma atomization is its faster production rate compared to other methods like gas atomization. This is primarily due to the higher temperatures achievable by plasma torches, allowing for faster melting and quicker disintegration of the metal feedstock. This translates to increased efficiency in powder production, ultimately leading to greater availability and potentially lower costs for end users.
Think of it like comparing a high-speed railway to a traditional train journey. Both reach the destination, but the former gets you there significantly faster. Similarly, plasma atomization helps bridge the gap between innovation and mass production in the realm of 3D metal printing.
A Material Menagerie: A World of Possibilities
The beauty of plasma atomization lies in its versatility. It can handle a wide range of metals, alloys, and even exotic materials like carbides, borides, and intermetallics. This opens doors to a plethora of applications across diverse industries.
Here’s a glimpse into the exciting world of plasma-atomized metal powders, showcasing some specific examples:
Metal Powder Models
Metal Powder Model | Composition | Properties/ Characteristics | Applications |
---|---|---|---|
316L Stainless Steel | Fe-18Cr-10Ni-2Mo | Excellent corrosion resistance, high strength, good ductility | Aerospace, medical implants, chemical processing equipment |
Inconel 625 | Ni-20Cr-9Mo-3Fe | Exceptional high-temperature strength and oxidation resistance | Gas turbines, heat exchangers, nuclear reactors |
Titanium-6 Aluminum-4 Vanadium (Ti-6Al-4V) | Ti-6Al-4V | High strength-to-weight ratio, good biocompatibility | Aerospace, medical implants, sporting goods |
Aluminum Si7Mg0.3 | Al-Si-Mg | Excellent castability, high strength, good corrosion resistance | Automotive components, electronics enclosures, consumer goods |
Copper | Cu | High electrical and thermal conductivity | Printed circuit boards, heat sinks, electrical connectors |
Nickel | Ni | High ductility and corrosion resistance | Electroplating, brazing alloys, catalysts |
Cobalt-Chrome (CoCr) | Co-Cr | High wear resistance, biocompatibility | Medical implants, dental prosthetics, surgical instruments |
Tungsten | W | High melting point, excellent wear resistance | Incandescent lamps, welding electrodes, cutting tools |
Tantalum | Ta | Exceptional corrosion resistance, biocompatibility | Capacitors, surgical implants, chemical processing equipment |
Niobium | Nb | High strength-to-weight ratio, superconductivity | Superconducting magnets, aircraft parts, nuclear reactors |
Additional Notes:
- This table represents a small selection of available plasma-atomized metal powders.
- The specific properties and applications of each powder can vary depending on the exact composition and processing parameters.
Unleashing the Potential of 3D Printing Metal Powder
While the ability to print intricate and complex shapes is certainly a defining feature of 3D printing, the true power lies in the functional aspects of the printed objects. Plasma-atomized metal powders unlock a new level of potential in this regard.
For instance, the superior mechanical properties of plasma-atomized powders, such as high strength, excellent fatigue resistance, and good corrosion resistance, enable the creation of highly functional parts for demanding applications.
Imagine printing a lightweight yet incredibly strong aircraft component using plasma-atomized titanium powder. Or, picture crafting biocompatible medical implants with intricate details and superior wear resistance, thanks to plasma-atomized cobalt-chrome powder. These are just a few examples of how plasma-atomization empowers 3D printing to go beyond mere aesthetics and delve into the realm of real-world functionality and performance.
Demystifying the Specs: A Tale of Sizes, Grades, and Standards
While the advantages of plasma atomization are clear, navigating the technical specifications can be daunting. Here’s a breakdown of key aspects to consider:
Plasma-Atomized Metal Powder Specifications:
Parameter | Description |
---|---|
Particle Size Distribution (PSD) | The range of sizes present in the powder, typically expressed in micrometers (µm). A narrow PSD is desirable for consistent printing. |
Apparent Density | The bulk density of the powder, measured in grams per cubic centimeter (g/cm³). It influences powder flow and packing efficiency during printing. |
Flowability | The ease with which the powder flows, impacting its handling and printability. |
Sphericity | The degree to which the particles resemble perfect spheres. Higher sphericity translates to better flow and packing. |
Oxygen Content | The amount of oxygen present in the powder, which can affect its mechanical properties and printability. Low oxygen content is generally preferred. |
Grade | The chemical composition and properties of the powder, as defined by industry standards. |
Standards:
Several international and national standards govern the production and properties of metal powders for additive manufacturing, including:
- ASTM International (ASTM)
- International Organization for Standardization (ISO)
- Aerospace Material Specifications (AMS)
- Military Standard (MIL)
These standards specify requirements for particle size, chemical composition, flowability, and other critical parameters, ensuring consistency and quality across different suppliers.
Pricing:
The cost of plasma-atomized metal powders can vary depending on several factors, including:
- The specific metal or alloy
- The powder’s purity and grade
- The particle size distribution
- The quantity ordered
Generally, exotic materials and tighter particle size distributions command a higher price tag. However, as the technology matures and production volumes increase, the cost of plasma-atomized powders is expected to become more competitive.
A Balanced View: Weighing the Pros and Cons
While plasma atomization offers significant advantages, it’s essential to acknowledge its limitations:
Advantages:
- Highly spherical particles for improved flow and printability
- Faster production rate compared to other atomization methods
- Versatility in handling a wide range of materials
- Superior mechanical properties of printed parts
Limitations:
- Higher cost compared to some other atomization methods
- Potential for higher oxygen content in the powder, requiring careful handling and storage
- May not be suitable for all applications due to cost and material limitations
Ultimately, the choice between plasma atomization and other methods depends on the specific requirements of the application, considering factors like budget, desired material properties, and printing process compatibility.
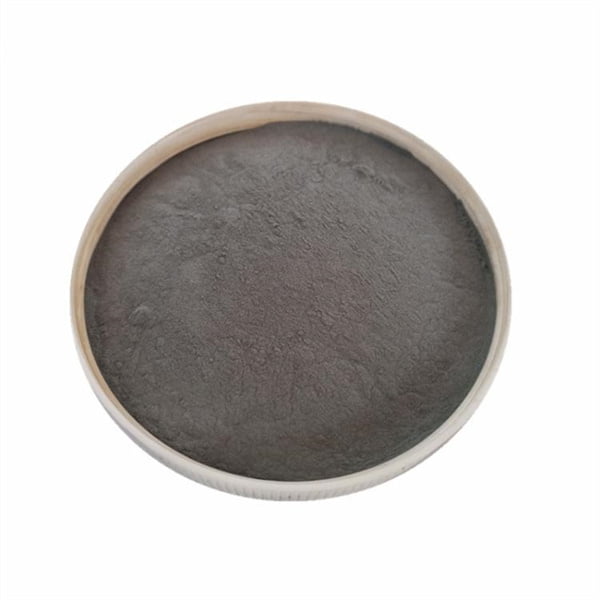
FAQs
Q: What are the advantages of plasma atomization for 3D printing metal powders?
A: Plasma atomization offers several advantages, including highly spherical particles for better flow and printability, faster production rates, versatility in handling various materials, and the ability to create printed parts with superior mechanical properties.
Q: What are some limitations of plasma atomization?
A: While advantageous, plasma atomization can be more expensive compared to other methods, might have a higher oxygen content in the powder, and may not be suitable for all applications due to cost and material limitations.
Q: What are some typical applications of plasma-atomized metal powders?
A: Plasma-atomized powders are used in various applications across diverse industries, including aerospace, medical implants, automotive components, electronics, and energy production.
Q: How does the particle size distribution (PSD) of a powder affect 3D printing?
A: A narrow PSD is desirable for consistent printing, as it ensures uniform flow and packing of the powder during the printing process.
Q: What are some important standards for plasma-atomized metal powders?
A: Several international and national standards govern the production and properties of metal powders, including ASTM, ISO, AMS, and MIL standards. These standards ensure consistency and quality across different suppliers.
Share On
MET3DP Technology Co., LTD is a leading provider of additive manufacturing solutions headquartered in Qingdao, China. Our company specializes in 3D printing equipment and high-performance metal powders for industrial applications.
Inquiry to get best price and customized Solution for your business!
Related Articles
About Met3DP
Recent Update
Our Product
CONTACT US
Any questions? Send us message now! We’ll serve your request with a whole team after receiving your message.
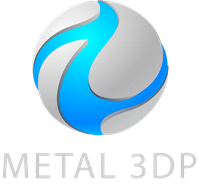
Metal Powders for 3D Printing and Additive Manufacturing