3D Printing Metal Powders
Table of Contents
Overview of 3D Printing Metal Powders
3D printing, also known as additive manufacturing, allows for the creation of complex metal parts directly from digital models. This revolutionary technology uses metal powders as the raw material and fuses fine layers of material together to build up components layer-by-layer.
The specific metal powder used has a significant impact on the properties, performance, applications, and economics of metal 3D printed parts. This guide provides a comprehensive overview of metal powders for 3D printing, including:
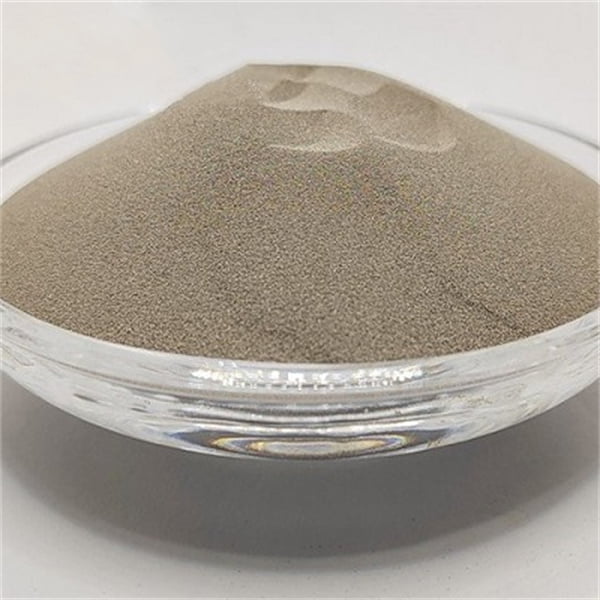
Types of Metal Powders for 3D Printing
This section covers the main categories and alloys of metal powders used in powder bed fusion and direct energy deposition 3D printing technologies.
Properties of Metal Powders
Key physical and chemical properties of metal powders that influence part quality are examined. Particle size distribution, morphology, flowability, and microstructure are discussed.
Applications of 3D Printing Metal Powders
The unique capabilities of metal additive manufacturing have lead to uptake in aerospace, medical, dental, automotive, and general engineering. Typical applications of different metal powder alloys are presented.
Metal Powder Specifications and Standards
Powder grades, size ranges, production methods, quality standards, and supply chain considerations for sourcing metal powders are provided.
Cost Analysis of Metal Powders
The costs associated with different metal alloys and quality grades are compared and contrasted. The economics of metal vs plastic powders is also discussed.
Advantages vs Limitations
The pros and cons of common metal powder varieties are weighed up in relation to part functionality requirements, mechanical properties achieved, production costs, quality control, and supply chain availability.
Equipped with this comprehensive guide, engineers, designers, procurement managers, and technical professionals will be able to select and source the optimal metal powder type for their specific application requirements and quality-to-price ratio expectations.
Types of Metal Powders for 3D Printing
Metal Category | Properties | Common Alloys | Applications |
---|---|---|---|
Steels | – High strength and wear resistance – Wide range of mechanical properties depending on alloy – Magnetic (except for some specialty steels) | – Stainless Steels (e.g., 17-4 PH, 316L, 304): Excellent corrosion resistance, good for parts exposed to fluids – Tool Steels (e.g., H13, A2, D2): High hardness, used for molds, dies, and cutting tools – Maraging Steels: High strength-to-weight ratio, ideal for aerospace components | Due to their versatility, steels are the most widely used metal powders in 3D printing. They offer a good balance of mechanical properties and are suitable for various applications. |
Aluminum Alloys | – Lightweight and good machinability – High strength-to-weight ratio – Excellent electrical conductivity – Not as strong as steels | – Aluminum-Silicon-Magnesium (AlSiMg) Alloys (e.g., 6061, 7075): Offer a good balance of strength and ductility, commonly used for prototypes and functional parts – Aluminum-Copper Alloys (e.g., 2024): High strength but lower corrosion resistance, suitable for aerospace components | Aluminum alloys are popular for applications where weight reduction is crucial. They are also easier to print compared to some other metals. |
Titanium Alloys | – High strength-to-weight ratio – Excellent corrosion resistance – Biocompatible (used in medical implants) | – Ti-6Al-4V (Titanium 6 Aluminum 4 Vanadium): The most commonly used titanium alloy in 3D printing, offers a good balance of strength, weight, and biocompatibility – Other titanium alloys: Tailored for specific properties like higher strength (e.g., Ti-6Al-4Mo) or improved biocompatibility (e.g., CP Ti) | Titanium alloys are valuable for applications requiring high strength, low weight, and resistance to corrosion. They are particularly useful in aerospace, biomedical, and chemical processing industries. |
Nickel-Based Alloys | – Excellent high-temperature strength and creep resistance – Corrosion resistant – Often used in harsh environments | – Inconel: A family of nickel-chromium alloys known for their high-temperature performance, used in gas turbine engines and heat exchangers – Hastelloy: Another group of nickel-based alloys offering superior corrosion resistance, suitable for chemical processing equipment | Nickel-based alloys are the go-to choice for applications exposed to extreme temperatures and corrosive conditions. They play a vital role in energy, aerospace, and chemical industries. |
Refractory Metals | – Extremely high melting points – Excellent high-temperature strength – Often used in very demanding environments | – Tungsten: Known for its unmatched melting point, used in electrodes, rocket nozzles, and heat shields – Tantalum: Offers exceptional corrosion resistance at high temperatures, valuable for furnace components and chemical processing equipment | Refractory metals are irreplaceable for applications requiring the ability to withstand extreme heat and harsh environments. They are used in sectors like aerospace, defense, and high-temperature furnaces. |
Precious Metals | – High corrosion resistance – Excellent electrical conductivity – Biocompatible (some) | – Gold: Primarily used for its biocompatibility in medical applications like dental implants and electronics – Silver: Valuable for its electrical conductivity, used in electrical connectors and antennas – Other precious metals (e.g., platinum): Used in specialized applications like jewelry and medical devices | Precious metals offer unique properties that make them suitable for specific applications. However, their high cost limits their widespread use in 3D printing. |
Properties of Metal Powders for 3D Printing
Property | Description | Importance for 3D Printing |
---|---|---|
Particle Size and Distribution | Refers to the variation in the diameter of individual powder particles. Measured in micrometers (µm). | – Affects flowability: Consistent size and distribution ensure smooth spreading of powder across the printing bed, enabling good layer formation and detail. – Impacts density and porosity: Uniform particles pack tightly, leading to denser parts with superior mechanical properties. Conversely, a wider size distribution can create voids and decrease strength. – Influences laser penetration (LPBF) or melting efficiency (Electron Beam Melting): Finer powders require less energy to melt fully, but may be more susceptible to laser scattering or overheating. |
Particle Morphology | The shape of individual powder particles. | – Flowability: Spherical particles flow more easily, promoting even deposition. Irregular shapes can lead to inconsistencies and bridging (arches forming between particles). – Packing Density: Spherical particles pack more tightly, maximizing material utilization and final part density. – Surface Area: Highly irregular shapes have a larger surface area, impacting factors like reactivity and sintering behavior. |
Apparent Density | The bulk density of the powder, measured in grams per cubic centimeter (g/cm³). | – Material usage and handling: Higher apparent density allows for more material to be loaded in the printer hopper and reduces waste. – Flowability: Denser powders may flow less readily, requiring adjustments in printer settings. |
Flowability | The ease with which powder flows under its own weight. Measured using techniques like angle of repose or flow rate. | – Uniform deposition: Good flowability ensures consistent spreading of powder across each layer, leading to dimensional accuracy and surface finish. – Processability: Powders with poor flowability can cause feeding issues in 3D printing machines, hindering printability. |
Chemical Composition | The elemental makeup of the powder, including the primary metal and any alloying elements. | – Final material properties: The chemical composition dictates the mechanical properties (strength, ductility, corrosion resistance) of the printed part. – Sintering behavior: The presence of certain elements can influence the temperature and time required for effective sintering. |
Oxygen Content & Surface Chemistry | The amount of oxygen absorbed on the powder surface and the presence of surface oxides. Measured in weight percent (wt%). | – Flowability: High oxygen content can reduce flowability by creating surface oxides that increase friction between particles. – Sintering behavior: Excessive surface oxides can impede sintering by hindering inter-particle bonding. – Printability (LPBF): Oxygen can react with the laser beam, reducing its effectiveness and potentially leading to spatter or porosity. |
Moisture Content | The amount of water vapor adsorbed on the powder surface. Measured in wt%. | – Flowability: Moisture can cause particles to clump together, hindering flow and creating inconsistencies. – Printability (LPBF): Moisture can react with the laser beam, generating unwanted hydrogen gas that can lead to porosity or cracking in the final part. |
Green Strength | The mechanical strength of the unsintered (or “green”) part after deposition. | – Handling: Higher green strength allows for more delicate handling of parts before the high-temperature sintering process. – Dimensional stability: Adequate green strength helps maintain part geometry during handling and preheating for sintering. |
Production and Classification of Metal Powders
Production Method | Process Description | Advantages | Limitations | Typical Metal Powders Produced |
---|---|---|---|---|
Milling | Metal chunks are crushed and ground down to a fine powder using ball mills, hammer mills, or attritor mills. | * Cost-effective for ductile metals * Produces a wide range of particle sizes * Can be used for brittle metals | * Irregular particle shapes can affect packing density * May introduce impurities * Not suitable for very fine powders | Iron, copper, aluminum, tin |
Atomization | Molten metal is broken up into droplets using a high-pressure gas or water stream, then rapidly solidified into spherical particles. | * Highly spherical particles for good packing density * Excellent control over particle size and distribution * Suitable for a wide range of metals | * Requires specialized equipment * May trap impurities in the solidified particles * Can be energy-intensive | Iron, steel alloys, nickel, copper, titanium |
Chemical Reduction | Metal oxides or halides are converted to pure metal powders through a chemical reaction with a reducing agent like hydrogen or carbon monoxide. | * High purity powders * Can produce very fine powders * Suitable for refractory metals like tungsten and molybdenum | * Complex and slow process * Requires careful control of reaction conditions * Limited production volumes | Tungsten, molybdenum, tantalum, nickel |
Electrolytic Deposition | An electric current is used to deposit metal ions from an electrolyte solution onto a cathode, forming a metal powder. | * High purity powders * Tight control over particle size and morphology * Offers good surface area for applications like catalysis | * Relatively slow process * Limited production capacity * Energy-intensive | Copper, nickel, silver, cobalt |
Classification | ||||
Powder Characteristic | Classification Method | Importance | ||
Particle Size | * Directly affects packing density, sintering behavior, and mechanical properties * Measured using sieving, laser diffraction, or image analysis | |||
Particle Shape | * Spherical shapes offer better packing density and flowability * Irregular shapes can be beneficial for interlocking and strength | |||
Chemical Composition | * Purity is crucial for many applications * Alloying elements can be incorporated for specific properties | |||
Flowability | * Ability of the powder to flow freely is essential for processing techniques like compaction | * Measured by angle of repose or flow rate tests |
Industrial Applications of 3D Printing Metal Powders
Industry | Application | Benefits | Material Examples |
---|---|---|---|
Aerospace | * Lightweight, high-strength components for rockets and satellites * Complex internal structures for jet engines * Heat exchangers for improved thermal management | * Reduced weight for increased fuel efficiency * Design freedom for intricate cooling channels * Faster turnaround time for prototypes and low-volume parts | * Titanium alloys (Ti-6Al-4V) * Nickel superalloys (Inconel 718) * Aluminum alloys (AlSi10Mg) |
Automotive | * Customizable, lightweight components for racing cars * Complex engine parts with internal cooling channels * Rapid prototyping of new designs and functionalities | * Improved performance through weight reduction * Enhanced engine efficiency with optimized cooling * Accelerated development cycles for faster innovation | * Aluminum alloys (A356) * Stainless steel (316L) * Tool steel (M2) |
Medical | * Personalized prosthetics and implants with improved biocompatibility * Surgical tools and instruments tailored to specific procedures * Patient-specific anatomical models for pre-surgical planning | * Customizable fit and function for improved patient outcomes * Enhanced surgical precision and efficiency * Better visualization and planning for complex surgeries | * Titanium alloys (Ti-6Al-4V) * Cobalt-chrome alloys (CoCrMo) * Tantalum |
Energy | * High-performance heat exchangers for power plants * Complex components for turbines and generators * Spare parts for legacy equipment, reducing downtime | * Improved energy efficiency through optimized heat transfer * Lightweight designs for increased power output * Reduced maintenance costs and faster repair times | * Nickel alloys (Inconel 625) * Stainless steel (304L) * Inconel claddings for corrosion resistance |
Consumer Goods | * Luxury jewelry and fashion accessories with intricate details * Limited-edition, customizable sporting equipment * Functional prototypes for rapid design iteration | * High-quality, personalized designs for unique products * Faster product development cycles and reduced time-to-market * Creation of complex geometries not possible with traditional methods | * Gold, silver, and platinum powders * Aluminum alloys (AlSi7Mg) * Stainless steel (17-4 PH) |
Defense | * Lightweight armor components with high ballistic protection * Customizable weapon parts for improved ergonomics * Rapid prototyping and production of specialized equipment | * Enhanced soldier protection with reduced weight burden * Improved weapon performance and user comfort * Faster development and deployment of specialized defense technology | * Titanium alloys (Ti-4Al-3Mo) * Armor steel * Inconel alloys for high-temperature applications |
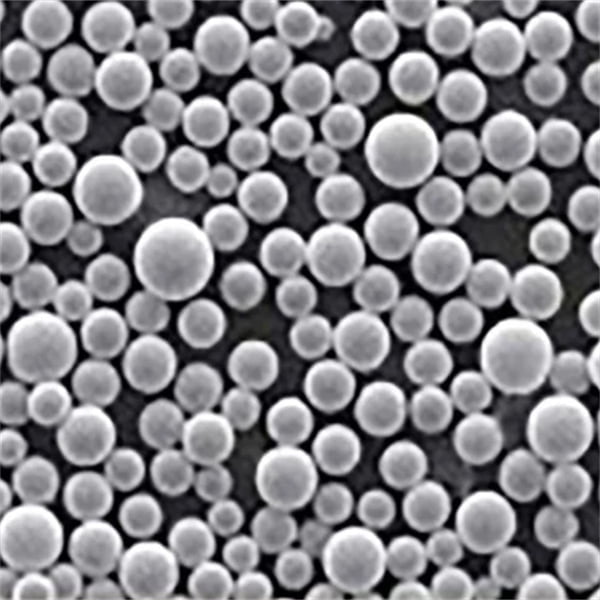
Metal Powder Specifications, Grades and Supply Chain
Aspect | Description | Key Considerations |
---|---|---|
Metal Powder Specifications | Metal powders for 3D printing differ significantly from their bulk counterparts. These finely-sized particles (typically 15-105 microns) require strict control over various properties to ensure successful printing and high-quality parts. | * Particle Size Distribution (PSD): PSD significantly impacts resolution, surface finish, and flowability. Laser-based systems often use finer powders (15-45 microns) for intricate details, while Electron Beam Melting (EBM) can handle larger particles (45-105 microns) due to its deeper melt pool. * Chemical Composition: Matching the desired final part properties necessitates precise control over the powder’s chemical makeup. Alloying elements and trace elements can significantly influence mechanical strength, corrosion resistance, and printability. * Flowability: Powder needs to flow freely and consistently within the printer’s build chamber to ensure proper layer formation. Spherical particle morphology and narrow PSD enhance flowability. * Apparent Density and Packing Density: These properties determine the amount of powder required to fill the build volume and influence final part porosity. * Moisture Content: Excess moisture can lead to spattering, inconsistencies, and defects during printing. |
Metal Powder Grades | Due to the critical role of metal powder in the 3D printing process, various grades are available catering to specific applications and printer types. | * Virgin Powders: Produced directly from primary or secondary metal sources, offering high purity and consistent properties for demanding applications like aerospace components. * Pre-alloyed Powders: These powders are already blended with alloying elements during atomization, reducing the need for post-processing and ensuring precise composition control. * Recycled Powders: Recycled powders from unused or support material offer a sustainable and cost-effective option, though strict quality control is necessary to avoid contamination and performance issues. * Atomization Process: The method used to create the powder particles (gas atomization, water atomization, plasma atomization) influences factors like particle size, morphology, and oxygen content, making them suitable for specific printing techniques. |
Supply Chain for 3D Printing Metal Powders | The metal powder supply chain for 3D printing involves several key players working together to deliver high-quality powders to end-users. | * Metal Producers: These companies provide the raw materials used for powder production. * Powder Manufacturers: They specialize in atomizing molten metal into fine particles using various techniques. Reputable manufacturers adhere to strict quality control protocols and offer powders with consistent properties and certifications. * Metal Powder Distributors: These companies act as intermediaries, stocking and supplying powders from various manufacturers to meet the needs of 3D printing service providers and end-users. * Additive Manufacturing Machine Manufacturers: Some printer manufacturers may also offer compatible metal powders, often optimized for their specific machines. * Certification Bodies: Independent organizations establish and enforce standards for metal powder properties used in additive manufacturing, ensuring quality and performance consistency. |
Cost Analysis of Metal Powders for AM
Metal powders are orders of magnitude more expensive than typical plastic filaments and sinter powders for 3D printing. Costs vary significantly for different alloys, size distributions, quality levels, order volumes and geographic regions.
This table provides indicative cost ranges for common alloys and grades suitable for major metal AM processes:
Metal Powder | Alloy Varieties | Cost per Kg |
---|---|---|
Stainless Steel | 316L, 17-4PH, 303, 440C | $$ |
Tool Steel | H13, M2, M4, D2 | $$$ |
Titanium Alloys | Ti-6Al-4V, Ti 6242, TiAl | $$$$ |
Aluminum Alloys | 2024, 7075, 6061 | $$ |
Inconel | 625, 718 | $$$$ |
Cobalt Chrome | CoCr MP1, CoCrMo | $$$$ |
Where $ = tens, $$ = hundreds, $$$ = thousands in US Dollars per kg.
More niche alloys or highly specific material properties and distributions further increase costs due to lower production volumes. Small scale batch production also has a cost premium over bulk orders.
Metal vs Plastic Powder Costs
Material | Typical Cost per Kg |
---|---|
PLA Plastic | $20-50 |
ABS Plastic | $25-100 |
Stainless Steel 316L | $50-150 |
Aluminum 2024 | $70-200 |
Inconel 718 | $150-600 |
While metal powders are 10-100x more expensive than plastics per unit weight due to material intensity, metals provide vastly superior mechanical properties, thermal resistance, and end-use potential.
In summary, alloy selection, purity grades, distribution specs and order parameters significantly influence powder costs. But enhanced part performance justifies higher metal prices for critical applications.
Now that powder expenses have been examined, the next section compares the pros and cons of different alloys.
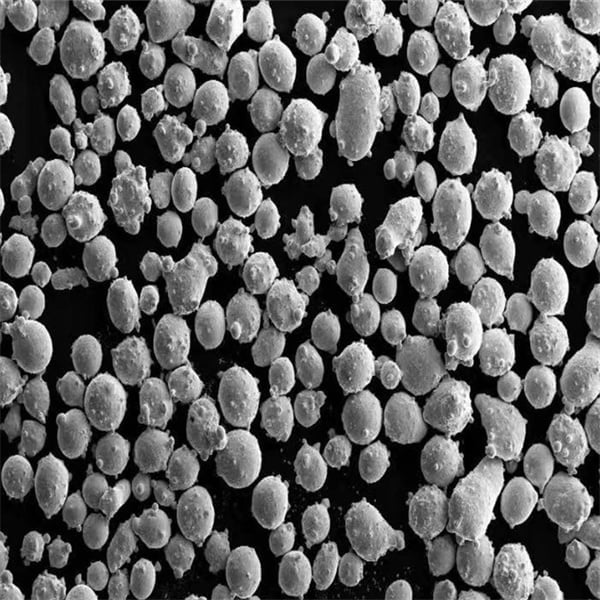
Advantages vs Limitations of Metal Powders
Advantages | Limitations |
---|---|
Design Flexibility and Complex Geometries | Part Size and Shape Constraints |
Metal powders excel at creating intricate shapes that would be highly challenging or wasteful to produce through traditional machining. Powder metallurgy allows for the formation of near-net shapes, minimizing the need for subsequent machining steps. This translates to intricate gears, internal channels, and lattice structures that wouldn’t be possible with other methods. | While metal powders offer exceptional design freedom, there are limitations to the size and complexity achievable. Very large parts or those with extreme thin features may be difficult to manufacture consistently due to challenges in powder flow and compaction uniformity. |
Material Efficiency and Reduced Waste | Initial Powder Cost |
Powder metallurgy boasts a significant advantage in terms of material utilization. Unlike machining, where a significant portion of the raw material ends up as scrap, powder metallurgy uses a near-additive approach. Only the amount of powder needed for the final part is used, minimizing waste and lowering overall material costs, especially for high-volume production runs. | Metal powders themselves can be more expensive than bulk materials used in traditional manufacturing processes. This can be a significant drawback for low-volume production or applications where cost is a critical factor. |
Tailored Material Properties | Porosity and Density Variations |
A unique advantage of metal powders lies in their ability to influence the final properties of the part. By selecting specific powder types, controlling particle size distribution, and utilizing various sintering techniques, manufacturers can achieve desirable characteristics like porosity, electrical conductivity, and magnetic permeability. This level of control allows for the creation of parts specifically engineered for their intended function. | One of the inherent challenges of powder metallurgy is achieving consistent and uniform density throughout the part. The compaction process can lead to variations in porosity, which can impact the mechanical properties of the final product. Strict control measures and potentially additional processing steps may be necessary to ensure parts meet density specifications. |
High Production Rates and Automation | Limited Material Selection |
Powder metallurgy lends itself well to automation, making it ideal for high-volume production runs. The near-net shaping capabilities minimize the need for extensive secondary machining, leading to faster production cycles and lower labor costs. This automation also enhances consistency and repeatability in part quality. | The availability of metal powders for specific applications can be limited compared to traditionally used materials. Some high-performance alloys or exotic metals may not be readily available in powder form, restricting the design possibilities for certain applications. |
Superior Surface Finish | Strength and Anisotropy |
Metal powder parts often boast excellent surface finishes due to the inherent nature of the compaction and sintering process. This can eliminate the need for additional finishing steps, reducing production costs and time. The smooth surface finish can also be beneficial for applications requiring tight tolerances or improved tribological properties (friction and wear). | The strength of powder metal parts can be lower compared to their wrought counterparts due to the presence of residual porosity. Additionally, the compaction process can introduce anisotropy, where the material properties differ depending on the direction of force applied. Careful design considerations and process optimization are crucial to mitigate these limitations. |
FAQ
This FAQ section provides answers to common questions on metal powders for additive manufacturing:
Q: What is the most widely used metal for 3D printing?
A: 316L stainless steel sees heavy adoption for end-use parts across aerospace, automotive, medical devices and industrial components due to its affordability, availability and moderate corrosion resistance.
Q: Which alloy offers the best strength-to-weight ratio?
A: Titanium alloys like Ti-6Al-4V provide very high specific strength exceeding aluminum and approaching high-end steels. Medical implants leverage titanium’s biocompatibility and strength. Diffusion bonding improves interlayer adhesion.
Q: How are material properties of metal AM parts different than tradition methods?
A: Unique thermal profiles from laser/electron beam melting create differentiated microstructures, often eliminating grain boundaries to improve strength and hardness. But properties become directionally dependent on build orientation.
Q: What methods can improve surface finish?
A: Additional post-processing via CNC machining and grinding or specialized electro-polishing achieves surface roughness requirements under 5 microns for the highest quality standards. Annealing can also reduce residual stresses.
Q: Which alloy printed best for high temperature applications?
A: Nickel superalloys like Inconel 718 retains strength and corrosion resistance up to 700°C and sees use in jet engine combustion chambers, rocket nozzles and nuclear reactors.
Share On
MET3DP Technology Co., LTD is a leading provider of additive manufacturing solutions headquartered in Qingdao, China. Our company specializes in 3D printing equipment and high-performance metal powders for industrial applications.
Inquiry to get best price and customized Solution for your business!
Related Articles
About Met3DP
Recent Update
Our Product
CONTACT US
Any questions? Send us message now! We’ll serve your request with a whole team after receiving your message.
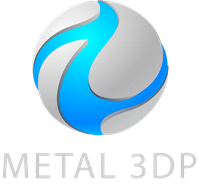
Metal Powders for 3D Printing and Additive Manufacturing