3D Printing Metal Powders:Future trend of Gas Atomization
Table of Contents
The world of 3D printing is rapidly evolving, and metal additive manufacturing (AM) stands at the forefront of this technological revolution. But this revolution is fueled by a crucial ingredient: 3D Printing Metal Powders. These fine, spherical particles are the building blocks that 3D printers use to construct intricate and functional metal parts.
Gas atomization emerges as a dominant force in the production of these metal powders. This process, which involves breaking down molten metal into tiny droplets using a high-pressure gas stream, offers several advantages:
- High purity: The controlled environment minimizes contamination, resulting in high-quality powders.
- Superior flowability: The spherical shape allows for smooth movement within the 3D printing machine, ensuring consistent printing quality.
- Tailored properties: Different parameters can be adjusted to achieve specific particle sizes and morphologies, catering to diverse printing applications.
However, the future of gas atomization for 3D printing metal powders extends beyond simply maintaining its current position. Let’s delve deeper into some exciting trends that are poised to shape this landscape:
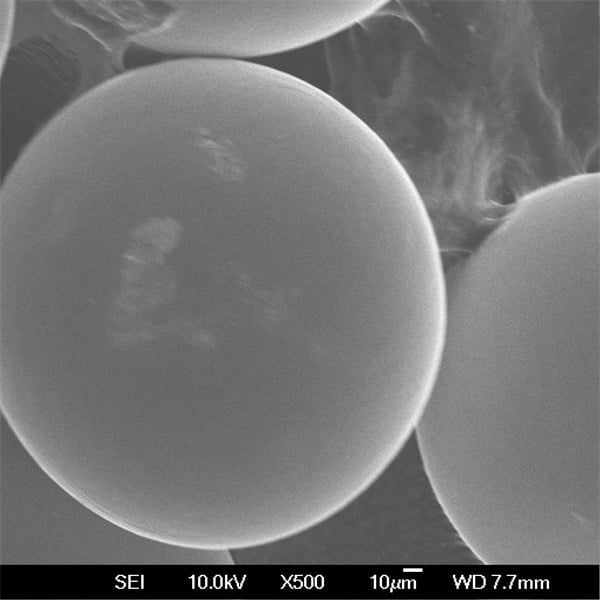
Gas atomization: Development of Cost-Effective Alternatives
The current gas atomization process, while effective, can be relatively expensive due to the high energy consumption and complex equipment involved. This can limit the accessibility of 3D-printed metal parts for certain applications and industries. To address this challenge, researchers are exploring alternative methods:
- Vacuum atomization: This technique utilizes a vacuum environment to achieve atomization, potentially reducing energy consumption compared to traditional gas atomization.
- Centrifugal atomization: This approach uses centrifugal force to break down molten metal, offering a simpler setup and potentially lower energy requirements.
While these alternatives are still under development, their success could significantly democratize 3D printing metal by making it more cost-effective. Imagine a future where even small businesses and individual makers can leverage the power of metal AM thanks to advancements in gas atomization technology.
3D Printing Metal Powders: Expansion of Material Compatibility
Currently, the range of metals available in gas-atomized powder form is limited compared to traditional manufacturing methods. This restricts the design possibilities and applications of 3D-printed metal parts. However, the future holds promise for increased material compatibility:
- Reactive metals: These metals, like titanium and aluminum, are prone to oxidation during gas atomization. Advancements in in-situ processes and protective atmospheres are paving the way for successful atomization of such reactive materials.
- Alloys and composites: Tailoring gas atomization parameters and exploring hybrid techniques like laser cladding holds the potential to create powders with unique combinations of properties, unlocking entirely new possibilities for 3D-printed parts.
Imagine a future where 3D printers can readily work with a diverse range of metals, from lightweight titanium for aerospace applications to high-strength steel for construction components. This expansion in material compatibility will undoubtedly fuel the growth and innovation within the 3D printing metal industry.
Gas Atomization: Precision Meets Sustainability
The increasing focus on sustainability in manufacturing is also influencing the development of gas atomization. Here are some promising trends:
- Recycling and closed-loop systems: Exploring ways to reintroduce scrap metal from the 3D printing process back into the gas atomization cycle can create a more sustainable and resource-efficient system.
- Environmentally-friendly atomization media: Replacing traditional inert gases with sustainable alternatives like nitrogen or argon can reduce the environmental impact of the process.
These advancements can contribute to a future where 3D printing metal goes beyond just creating innovative products; it also becomes a responsible and environmentally conscious manufacturing technology.
Embracing Innovation: Exploring the Future of Gas Atomization Techniques
Beyond the aforementioned trends, the future of gas atomization promises exciting breakthroughs in various areas:
1. Nanostructured Powders: Imagine building metal parts with properties closer to their bulk counterparts. Research is actively exploring the creation of nanostructured powders through gas atomization. These powders, with their incredibly small grain sizes, offer the potential for:
- Enhanced mechanical properties: Increased strength, ductility, and wear resistance compared to conventional powders.
- Tailored functionalities: By controlling the nanostructure, engineers can potentially influence specific properties like electrical conductivity or thermal expansion.
However, successfully producing and handling these tiny particles requires overcoming challenges like agglomeration (clumping) and handling difficulties. Nevertheless, the potential rewards are significant, paving the way for the development of next-generation 3D-printed metal parts with exceptional performance.
2. Composite Powders: Pushing the boundaries of material design, the future may see the emergence of composite powders produced through gas atomization. These powders would combine different materials within a single particle, offering unique combinations of properties:
- Functionally graded materials: Imagine a 3D-printed part with a core material for strength and a surface layer with enhanced wear resistance. Composite powders could make this a reality.
- Multi-material printing: By strategically combining different composite powders, 3D printers could potentially create parts with intricate material variations within a single build, opening doors to entirely new design possibilities.
While technical hurdles like controlling the distribution and interaction of different materials within the composite powder exist, the potential benefits are undeniable. This technology could revolutionize the way we design and manufacture complex and multifunctional components.
3. Additive Manufacturing Advancements: The evolution of gas atomization is intricately linked to the advancements in 3D printing technologies. As additive manufacturing techniques become more sophisticated, they will place new demands on the capabilities of metal powders:
- Finer powder requirements: Future printing technologies with higher resolution might require even finer and more uniform powders for precise printing of intricate features.
- Novel powder characteristics: As printing processes evolve, the need for powders with unique properties, such as improved thermal conductivity or specific surface area, might emerge.
Gas atomization researchers and manufacturers will need to adapt and innovate to meet these evolving demands, ensuring that the powders remain compatible and optimized for the latest 3D printing advancements.
Conclusion: A Collaborative Future for Gas Atomization and 3D Printing
The future of gas atomization for 3D printing metal powders is not solely defined by technological advancements. It is also about fostering collaboration between various stakeholders within the industry:
- Material scientists: Developing novel alloys and composites to push the boundaries of material compatibility.
- Equipment manufacturers: Creating cost-effective and sustainable atomization technology.
- 3D printing machine developers: Optimizing printing processes to leverage the full potential of advanced powders.
- End-users: Providing valuable feedback and pushing the demand for innovative materials and applications.
Through this collaborative effort, gas atomization can continue to evolve as a critical enabler of 3D printing metal, shaping the future of manufacturing and leading to the creation of groundbreaking products across diverse industries.
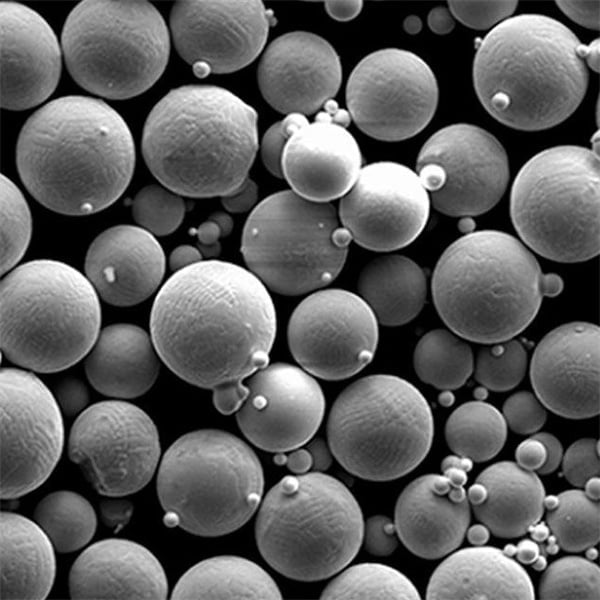
FAQ
1. What are the anticipated cost-reduction strategies for gas atomization?
- Alternative atomization methods: Exploring techniques like vacuum or centrifugal atomization, which may have lower energy requirements compared to traditional gas atomization.
- Process optimization: Refining the current gas atomization process to improve efficiency and potentially reduce energy consumption.
- Recycling and closed-loop systems: Reintroducing scrap metal from 3D printing back into the atomization cycle, minimizing waste and potentially lowering overall production costs.
2. How will the future of gas atomization address the issue of limited material compatibility?
- Advancements in in-situ processes and protective atmospheres: Enabling successful atomization of reactive metals like titanium and aluminum.
- Tailoring atomization parameters: Optimizing parameters to create powders suitable for a wider range of materials.
- Exploration of hybrid techniques: Utilizing methods like laser cladding in combination with gas atomization to create powders with unique material combinations.
3. What role will sustainability play in the future of gas atomization?
- Environmentally-friendly atomization media: Replacing traditional inert gases with sustainable alternatives like nitrogen or argon to reduce the environmental impact.
- Recycling and closed-loop systems: Implementing these systems to minimize waste and resource consumption within the gas atomization process.
- Development of energy-efficient atomization methods: Exploring alternative techniques or process optimizations to reduce the overall energy footprint of gas atomization.
4. How will nanostructured powders impact the future of 3D-printed metal parts?
- Enhanced mechanical properties: Nanostructured powders have the potential to offer increased strength, ductility, and wear resistance compared to conventional powders, leading to higher-performing 3D-printed parts.
- Tailored functionalities: By controlling the nanostructure, engineers may be able to influence specific properties like electrical conductivity or thermal expansion, creating parts with unique functionalities.
5. What are the challenges and opportunities associated with composite powders?
- Challenges: Controlling the distribution and interaction of different materials within the composite powder, and potential difficulties in handling and processing these fine particles.
- Opportunities: Enabling the creation of functionally graded materials and multi-material printed parts, opening doors to innovative designs and functionalities in 3D-printed metal components.
Share On
MET3DP Technology Co., LTD is a leading provider of additive manufacturing solutions headquartered in Qingdao, China. Our company specializes in 3D printing equipment and high-performance metal powders for industrial applications.
Inquiry to get best price and customized Solution for your business!
Related Articles
About Met3DP
Recent Update
Our Product
CONTACT US
Any questions? Send us message now! We’ll serve your request with a whole team after receiving your message.
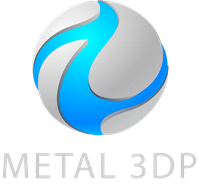
Metal Powders for 3D Printing and Additive Manufacturing
COMPANY
PRODUCT
cONTACT INFO
- Qingdao City, Shandong, China
- [email protected]
- [email protected]
- +86 19116340731