What 3D Printing Metal Powders Can Plasma Atomization Produce?
Table of Contents
Not a sci-fi gadget, but a fine, metallic powder with the potential to revolutionize how we design and manufacture objects. This is the magic of plasma atomization, a technology capable of transforming molten metal into incredibly precise and versatile 3D Printing Metal Powders. But what exactly can this process create? Buckle up, because we’re about to delve into the fascinating world of 3D metal powders produced by plasma atomization.
Unveiling the Process: A Glimpse into Plasma Atomization
Before we explore the diverse materials plasma atomization can handle, let’s understand the process itself. Picture this: a molten stream of metal, heated to extreme temperatures by a plasma torch, is injected into a high-velocity gas stream. This forceful collision breaks the molten metal into tiny, spherical droplets that solidify mid-air, cooling rapidly to form the desired metal powder.
This innovative technique offers several advantages over traditional methods. The high temperatures achieved by the plasma torch allow for the processing of even the most challenging materials, like high-melting-point metals. Additionally, the rapid cooling process results in highly spherical and consistent particles, crucial for achieving optimal performance in 3D Printing Metal Powders processes like Selective Laser Melting (SLM) and Electron Beam Melting (EBM).
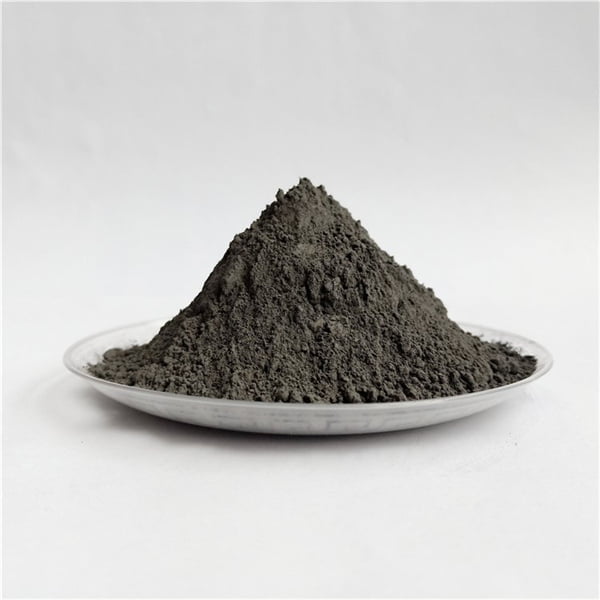
A Treasure Trove of Materials: Exploring the Potential of Plasma-Atomized Powders
Now, let’s unlock the treasure chest of possibilities. Plasma atomization boasts the capability of producing a vast array of 3D Printing Metal Powders, catering to diverse applications across various industries. Here are some prominent examples:
- Titanium and its Alloys: Often referred to as the “workhorse” of 3D printing metals, titanium is known for its exceptional strength, corrosion resistance, and biocompatibility. Plasma-atomized titanium powders are widely used in the aerospace, medical, and automotive industries for applications like aircraft components, medical implants, and high-performance car parts.
- Nickel-Based Superalloys: These high-temperature alloys are renowned for their ability to withstand extreme heat and stress, making them ideal for applications in jet engines, gas turbines, and rocket propulsion systems. Plasma atomization ensures consistent particle size and morphology, crucial for achieving the desired mechanical properties in these demanding applications.
- Stainless Steel: A familiar name, stainless steel finds its way into various applications due to its excellent corrosion resistance and affordability. Plasma-atomization allows for the creation of various stainless steel powder grades, catering to specific needs in the construction, medical, and consumer goods industries.
- Aluminum and its Alloys: Lightweight and readily available, aluminum offers a cost-effective option for various applications. Plasma-atomized aluminum powders are used in the automotive and aerospace industries due to their ability to achieve a good balance between strength and weight reduction.
- Cobalt-Chrome Alloys: Offering a unique combination of wear resistance, corrosion resistance, and biocompatibility, cobalt-chrome alloys are widely used in the medical device industry for applications like joint replacements and dental implants. Plasma atomization ensures the production of high-purity powders essential for these critical applications.
Beyond these, the list expands further to include:
- Copper and its alloys
- Molybdenum and its alloys
- Tungsten and its alloys
- Precious metals like gold and silver
The ability to tailor the process parameters allows for the creation of customized powders with specific properties, catering to the evolving needs of various industries.
Diving Deeper: Advantages and Considerations
While plasma atomization unlocks a vast potential, it’s essential to consider both its advantages and limitations:
Advantages:
- High-purity powders: The process minimizes contamination, resulting in high-quality powders for demanding applications.
- Spherical and consistent particles: This ensures optimal flowability and printability in 3D printing processes.
- Wide range of materials: Plasma atomization can handle a diverse spectrum of metals and alloys.
- Tailored properties: Process parameters can be adjusted to achieve specific powder characteristics.
Considerations:
- Cost: Compared to traditional methods, plasma atomization can be a more expensive process.
- Environmental impact: The high energy consumption associated with the process requires careful consideration.
The Future Unfolds: Where Plasma-Atomized Powders are Headed
The potential of plasma-atomized powders extends far beyond the current applications, shaping the future of various industries and pushing the boundaries of what’s possible. Here’s a glimpse into what the future holds for this transformative technology:
Cost Reduction Strategies:
While offering numerous advantages, the high cost of plasma-atomization remains a hurdle for wider adoption. However, several advancements are paving the way for a more cost-effective future:
- Process optimization: Refining the plasma atomization process itself can lead to significant cost reductions. This includes exploring alternative energy sources, optimizing powder collection techniques, and minimizing waste generation.
- Economies of scale: As the demand for plasma-atomized powders increases, economies of scale will kick in, driving down the cost per unit of powder produced.
- Recycling and reuse: Implementing efficient recycling and reuse strategies for unutilized powder can not only reduce costs but also minimize the environmental impact of the process.
Development of Novel Materials:
The future holds immense potential for the creation of entirely new materials using plasma atomization. Here are some exciting possibilities:
- Multi-material and composite powders: Imagine powders combining different metals or even integrating non-metallic materials like ceramics or polymers. This could unlock a new generation of materials with unique combinations of properties, catering to highly specialized applications.
- Functionally graded powders: These powders would possess a gradual variation in composition or properties throughout their volume. This opens doors to the creation of components with tailored properties in different regions, optimizing performance and efficiency.
- Nanoparticles: Exploring the creation of even finer powders in the nanoscale range could lead to the development of entirely new materials with unique properties for applications in fields like electronics, medicine, and catalysis.
Wider Adoption Across Industries:
As the technology matures and costs become more competitive, plasma-atomized powders are poised for wider adoption across various industries:
- Construction: 3D printing with metal powders could revolutionize the construction industry, enabling the creation of lighter, stronger, and more sustainable buildings. Imagine 3D-printed bridges, customized building components, and even entire structures fabricated on-site using plasma-atomized powders.
- Space Exploration: The need for lightweight and high-performance materials in spacecraft is crucial. Plasma-atomized powders with their unique properties could be instrumental in creating components for rockets, satellites, and even future space habitats.
- Consumer Goods: The potential for customization and on-demand manufacturing extends beyond traditional applications. Imagine personalized electronics with unique designs and functionalities, or even 3D-printed musical instruments tailored to individual preferences, all made possible with plasma-atomized powders.
3D Printing Metal Powders: Applications of Plasma-Atomized Powders
The potential applications of plasma-atomized powders extend far beyond the examples mentioned earlier. Here’s a glimpse into how these innovative materials are shaping various industries:
Aerospace: The relentless pursuit of lighter and stronger aircraft demands advanced materials. Plasma-atomized titanium and aluminum alloys are being used to create lightweight yet robust components for airplanes, satellites, and rockets. These components offer significant weight reductions compared to traditional materials, leading to increased fuel efficiency and improved overall performance.
Medical: The medical field is witnessing a revolution in personalized medicine, and 3D printing plays a crucial role. Plasma-atomized powders like titanium, cobalt-chrome, and tantalum are used to create custom-made implants for knees, hips, and other joints. These implants offer excellent biocompatibility, reducing the risk of rejection by the body. Additionally, the ability to tailor the porosity of the powder allows for the creation of implants that mimic the natural bone structure, promoting better bone ingrowth and long-term functionality.
Automotive: The automotive industry is constantly striving for lighter and more fuel-efficient vehicles. Plasma-atomized aluminum and magnesium alloys are being explored for the creation of lightweight car parts, contributing to improved fuel efficiency and reduced emissions. Additionally, these materials offer the potential for complex geometries, enabling the design of innovative car components with enhanced performance characteristics.
Consumer Goods: The potential for personalized and high-performance products extends to the consumer goods sector as well. Plasma-atomized metal powders can be used to create customized jewelry, sporting equipment, and even high-end consumer electronics. Imagine owning a pair of custom-made running shoes with soles 3D printed from a lightweight and durable aluminum alloy, or a personalized phone case crafted from a unique blend of metal powders.
Beyond these sectors, the applications of plasma-atomized powders are constantly being explored in fields like:
- Energy: The development of next-generation batteries and fuel cells might involve the use of specialized metal powders created through plasma atomization.
- Defense: The creation of lightweight armor and high-performance weapon components could benefit from the unique properties of these powders.
- Construction: Utilizing metal powders in 3D printing for construction applications could lead to lighter, stronger, and more sustainable building materials.
The potential applications of plasma-atomized powders seem boundless, and as technology continues to advance, we can expect to see even more innovative and groundbreaking applications emerge in the years to come.
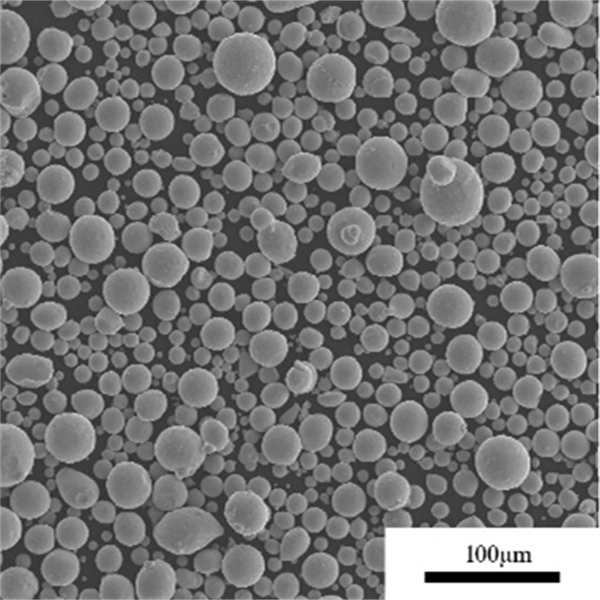
FAQ
1. What are the typical sizes of plasma-atomized powders?
Plasma-atomized powders can range in size from 10 micrometers to 300 micrometers, with the specific size depending on the desired application and the material being processed.
2. How does the cost of plasma-atomized powders compare to other metal powders?
Plasma-atomized powders can be more expensive than powders produced by traditional methods like gas atomization. However, the high purity, consistency, and tailored properties of these powders often justify the cost for demanding applications.
3. Is plasma atomization an environmentally friendly process?
The high energy consumption associated with the process raises concerns about its environmental impact. However, ongoing research and development efforts strive to optimize the process and implement sustainable practices to minimize the environmental footprint.
4. What are the future trends in plasma atomization technology?
Future trends likely involve cost reduction strategies to make this technology more accessible, exploration of novel materials with unique properties, and wider adoption across various industries as 3D printing technology continues to evolve.
5. Where can I learn more about plasma atomization and its applications?
Numerous resources are available online and in libraries, including research papers, industry reports, and websites of companies involved in plasma atomization technology and 3D metal printing. Additionally, attending industry events and conferences can provide valuable insights into the latest advancements and applications in this exciting field.
Share On
MET3DP Technology Co., LTD is a leading provider of additive manufacturing solutions headquartered in Qingdao, China. Our company specializes in 3D printing equipment and high-performance metal powders for industrial applications.
Inquiry to get best price and customized Solution for your business!
Related Articles
About Met3DP
Recent Update
Our Product
CONTACT US
Any questions? Send us message now! We’ll serve your request with a whole team after receiving your message.
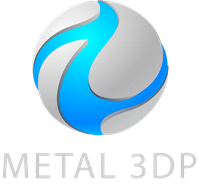
Metal Powders for 3D Printing and Additive Manufacturing
COMPANY
PRODUCT
cONTACT INFO
- Qingdao City, Shandong, China
- [email protected]
- [email protected]
- +86 19116340731