6013 Metal Powder for MIM
Table of Contents
Introduction to 6013 Metal Powder for MIM
Metal injection molding (MIM) has revolutionized the manufacturing of complex, near-net-shape metal components. Imagine achieving intricate geometries and exceptional dimensional accuracy – all at a fraction of the cost and waste associated with traditional machining techniques. That’s the magic of MIM. But this innovative process hinges on a critical ingredient: the metal powder itself. And when it comes to pushing the boundaries of MIM capabilities, 6013 metal powder stands out as a true powerhouse.
This comprehensive guide delves into the world of 6013 powder for MIM, exploring its properties, applications, advantages, limitations, and various configurations. We’ll also unveil a range of alternative metal powders, equipping you with the knowledge to make informed decisions for your next MIM project.
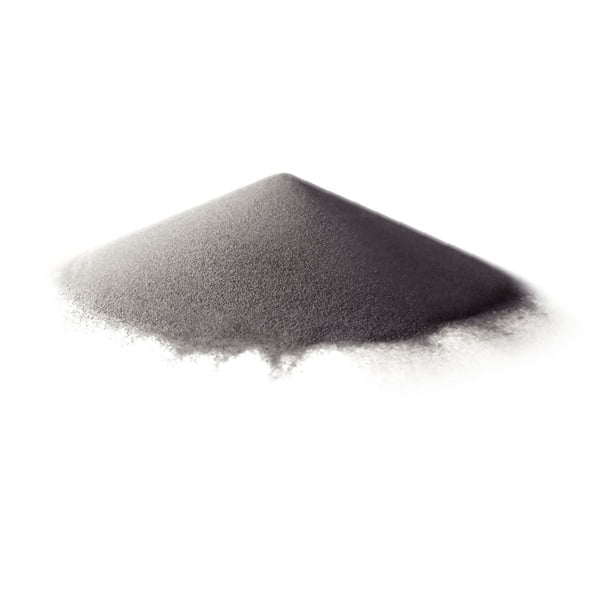
What is 6013 Metal Powder?
6013 metal powder is a workhorse material specifically formulated for MIM applications. It’s a low-alloy steel powder composed primarily of iron, with a carefully balanced mix of other elements like chromium, molybdenum, and carbon. This unique composition imbues 6013 powder with a remarkable set of characteristics:
- High Strength and Hardness: Compared to pure iron powders, 6013 boasts superior strength and hardness thanks to the presence of chromium and molybdenum. These elements form strengthening precipitates within the metal matrix, enhancing its resistance to wear and tear.
- Excellent Sinterability: Sintering is the crucial step in MIM where the loose powder particles bond together to form a solid metal object. 6013 powder excels in this process due to its controlled particle size distribution and optimized chemical composition. This translates to cleaner production runs with minimal defects from poor sintering.
- Good Corrosion Resistance: The presence of chromium in 6013 powder enhances its resistance to corrosion, particularly against mild environmental conditions. This makes it suitable for applications where some level of environmental exposure is expected.
- Cost-Effective: 6013 powder strikes a sweet spot between affordability and performance. While offering superior properties compared to pure iron powders, it remains a cost-effective option for a broad spectrum of MIM applications.
Metal Powder Options for MIM
While 6013 powder shines in the MIM arena, it’s not the only player in the game. Here’s a breakdown of ten other commonly used metal powders, highlighting their key features and how they stack up against 6013:
Metal Powder | Composition (wt%) | Key Properties | Applications | Compared to 6013 |
---|---|---|---|---|
316L Stainless Steel | Fe (bal), Cr (16-18), Ni (10-14), Mo (2-3) | Excellent corrosion resistance, high strength, biocompatible | Medical implants, aerospace components, chemical processing equipment | Offers superior corrosion resistance but at a higher cost |
17-4 PH Stainless Steel | Fe (bal), Cr (15-17), Ni (3-5), Cu (4) | High strength, good ductility, age-hardenable | Gears, fasteners, valves | Similar strength to 6013 but offers improved ductility and age hardening capabilities |
Inconel 625 | Fe (bal), Cr (20-24), Ni (58-62), Mo (5-8) | Exceptional high-temperature strength, excellent corrosion resistance | Turbine blades, aerospace components, chemical processing equipment | Significantly higher cost than 6013, better suited for demanding high-temperature applications |
Titanium Grade 2 | Ti (min. 99.2%) | Excellent biocompatibility, high strength-to-weight ratio | Medical implants, aerospace components, sporting goods | Offers superior biocompatibility and weight savings but comes at a premium price |
Copper | Cu (min. 99.5%) | High electrical and thermal conductivity | Electrical connectors, heat sinks, brazing materials | Not a ferrous material, offers unique conductivity properties but lacks structural strength |
Nickel 200 | Ni (min. 99%) | Excellent ductility, good corrosion resistance | Electronic components, chemical processing equipment | Lower strength than 6013 but excels in ductility and specific applications |
4140 Chromoly Steel | Fe (bal), Cr (1.00-1.30), Mo (0.15-0.25), C (0.38-0.48) | High strength, good toughness | Gears, shafts, automotive components | Offers improved toughness compared to 6013 but may require higher sintering temperatures |
304L Stainless Steel | Fe (bal), Cr (18-20), Ni (8-12) | Good corrosion resistance, moderate strength | Food processing equipment, architectural components | Similar strength to 6013 but offers better corrosion resistance for specific applications |
Nitronic 60 | Fe (bal), Cr (14-18), Ni (35-38), Mo (3-4) | High strength, excellent corrosion resistance | Marine hardware, fasteners, pump components | Superior corrosion resistance to 6013 but at a higher cost |
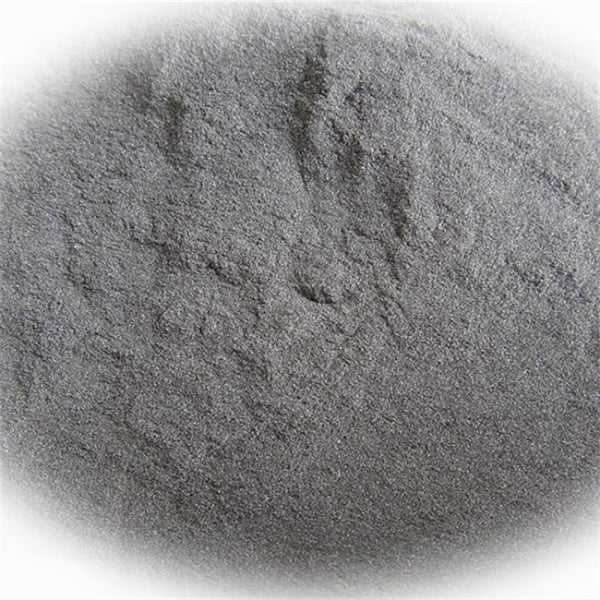
Applications of 6013 Metal Powder
The versatility of 6013 powder shines through its diverse range of applications. Here are some prominent examples:
- Automotive Industry: Gears, sprockets, linkages, valve components. 6013 powder’s strength and affordability make it ideal for producing complex, high-volume automotive parts.
- Consumer Electronics: Camera housings, connectors, heat sinks. Its ability to achieve intricate shapes and good thermal properties make it suitable for intricate electronic components.
- Medical Devices: Surgical instruments, implant components (depending on specific requirements). The biocompatible nature of 6013 powder, with proper post-processing, allows for its use in certain medical device applications. However, for critical implant applications, materials with superior biocompatibility like 316L stainless steel might be preferred.
- Power Tools: Gears, housings, saw blades. The strength and wear resistance of 6013 powder translate well into durable power tool components.
- Sporting Goods: Bicycle parts, firearm components (depending on specific requirements). Similar to medical devices, 6013 can be used in some sporting goods applications, but for high-stress components, materials with superior strength like 17-4 PH might be a better choice.
Advantages and Limitations of 6013 Metal Powder
Advantages:
- Cost-effective: Compared to high-alloy or exotic metal powders, 6013 offers a compelling balance between affordability and performance.
- Excellent Sinterability: Its optimized composition and particle size distribution ensure efficient sintering, leading to cleaner production runs with minimal defects.
- Good Strength and Hardness: The presence of chromium and molybdenum enhances its strength and hardness, making it suitable for various structural applications.
- Moderate Corrosion Resistance: The chromium content provides some level of protection against mild environmental corrosion.
Limitations:
- Lower Strength Compared to High-Alloy Powders: Compared to materials like 17-4 PH or Inconel 625, 6013 might not be suitable for applications demanding exceptional strength or high-temperature performance.
- Limited Corrosion Resistance: While offering some corrosion resistance, it wouldn’t be the first choice for applications requiring high resistance to harsh environments.
- Biocompatibility Concerns (for certain medical applications): While potentially usable for certain medical device components with proper post-processing, its biocompatibility might not be ideal for critical implants compared to materials like 316L stainless steel.
Understanding 6013 Metal Powder Specifications
When selecting 6013 powder for your MIM project, it’s crucial to understand its various specifications. Here’s a breakdown of key parameters to consider:
Specification | Description | Impact on Performance |
---|---|---|
Chemical Composition | The precise percentages of iron, chromium, molybdenum, carbon, and other elements. | Dictates the final properties of the sintered component, such as strength, hardness, and corrosion resistance. |
Particle Size Distribution | The range of sizes and distribution of the powder particles. | Affects packing density during molding, sinterability, and surface finish of the final part. |
Apparent Density | The weight of powder per unit volume in its loose, uncompacted state. | Influences material handling and mold filling during the MIM Influences material handling and mold filling during the MIM process. |
Flowability | The ease with which the powder flows under pressure. | Critical for uniform mold filling and achieving consistent part density. |
Oxygen Content | The amount of oxygen present in the powder particles. | Excessive oxygen can lead to internal oxidation and weaken the final component. |
Sourcing 6013 Metal Powder: Suppliers and Pricing
Several reputable suppliers offer 6013 metal powder for MIM applications. Here’s a table outlining some potential vendors (Disclaimer: This is not an exhaustive list, and inclusion does not constitute endorsement):
Supplier | Location | Product Offerings | Estimated Price Range (per kg) |
---|---|---|---|
Changsha TIJO Metal Materials Co., Ltd. | China | Gas-atomized 6013 powder with various particle size distributions | $15-25 |
Höganäs AB | Sweden | Atomized 6013 powder with customized options | $20-30 |
AP Powder Company | USA | AMSR (Atomized Metal Shot Remelt) 6013 powder | $25-35 |
Carpenter Additive | USA | Premium grade 6013 powder with tight compositional control | $30-40 |
Pricing
It’s important to note that the pricing of 6013 metal powder can vary depending on several factors, including:
- Supplier: Different suppliers might have varying pricing structures based on production costs and market dynamics.
- Order Quantity: Bulk purchases often attract lower per-unit costs compared to smaller orders.
- Powder Specifications: Premium grade powders with tighter compositional control or specific particle size distributions might command a higher price.
Considerations When Choosing a Supplier
Beyond price, here are some crucial aspects to consider when selecting a 6013 metal powder supplier:
- Reputation and Quality: Opt for established suppliers known for consistent quality and adherence to industry standards.
- Product Offerings: Ensure the supplier offers 6013 powder with specifications that align with your project requirements.
- Technical Support: Look for suppliers that provide technical expertise and can assist with material selection and processing guidance.
- Delivery Lead Times: Factor in delivery lead times to ensure a smooth production flow.
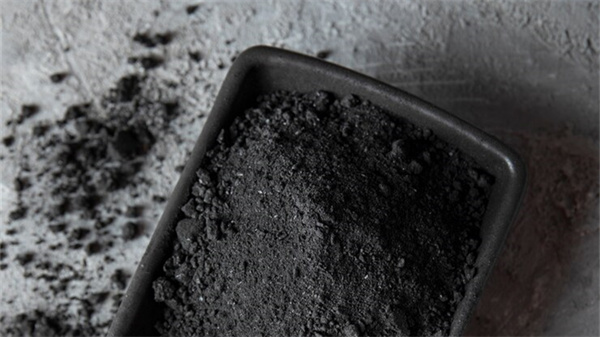
FAQ
Q: Is 6013 metal powder safe for use in medical devices?
A: The biocompatibility of 6013 powder can vary depending on the specific application. While it might be suitable for certain medical device components with proper post-processing, for critical implants requiring optimal biocompatibility, materials like 316L stainless steel are generally preferred. Consulting with a medical device expert is crucial for determining the most suitable material for your specific application.
Q: Can 6013 metal powder be used for high-temperature applications?
A: 6013 powder offers moderate high-temperature performance compared to high-alloy options like Inconel 625. For applications requiring exceptional strength and heat resistance at elevated temperatures, other metal powders might be a better choice.
Q: What are the advantages of using 6013 metal powder over traditional machining techniques?
A: MIM with 6013 powder offers several advantages over traditional machining, including:
- Near-net-shape manufacturing: MIM allows for producing complex geometries with minimal material waste.
- Dimensional accuracy: MIM parts achieve high dimensional accuracy, reducing the need for extensive post-processing.
- Cost-effectiveness: For high-volume production of intricate parts, MIM with 6013 powder can be a more cost-effective approach compared to machining.
- Design flexibility: MIM allows for the creation of intricate features and thin walls that would be challenging or impossible to achieve through machining.
Conclusion
6013 metal powder stands as a workhorse material for MIM applications. Its affordability, good sinterability, and balanced strength properties make it a versatile choice for diverse industries. By understanding its specifications, limitations, and available supplier options, you can leverage the power of 6013 powder to create complex, near-net-shape metal components with efficiency and precision.
Share On
MET3DP Technology Co., LTD is a leading provider of additive manufacturing solutions headquartered in Qingdao, China. Our company specializes in 3D printing equipment and high-performance metal powders for industrial applications.
Inquiry to get best price and customized Solution for your business!
Related Articles
About Met3DP
Recent Update
Our Product
CONTACT US
Any questions? Send us message now! We’ll serve your request with a whole team after receiving your message.
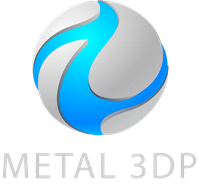
Metal Powders for 3D Printing and Additive Manufacturing