7050 Aluminium Alloy Powder
Table of Contents
Overview of 7050 aluminium alloy powder
7050 aluminium alloy powder is a strong, tough, heat-treatable alloy powder that has high strength properties combined with excellent fatigue resistance. It is part of the 7xxx series of aluminium alloys, with zinc being the primary alloying element.
7050 alloy powder offers a high strength-to-weight ratio and is commonly used in structural and high-stress applications in the aerospace, automotive, and defence industries. Parts made from 7050 powder metallurgy techniques can replace components traditionally made of steel, titanium or nickel alloys.
Some key properties and characteristics of 7050 aluminium alloy powder include:
7050 Aluminium Alloy Powder Properties
Properties | Details |
---|---|
Alloy Designation | 7050 |
Alloying Elements | Zinc, magnesium, copper, zirconium |
Density | 2.83 g/cm3 |
Melting Point | Around 635°C |
Strength | Very high, with ultimate tensile strength over 510 MPa after heat treatment |
Fatigue Strength | Excellent compared to other 7xxx alloys |
Corrosion Resistance | Moderate, less than pure aluminium |
Conductivity | Good electrical and thermal conductivity |
Workability | Fair machinability and formability |
Weldability | Low due to high alloy content |
The high zinc and copper content in 7050 powder enables heat treatment to achieve very high yield and tensile strengths while also providing good fatigue resistance compared to other aerospace aluminium alloys.
The following sections provide more details on the composition, processing methods, properties, applications, specifications, pricing, advantages and limitations of 7050 aluminium alloy powder.
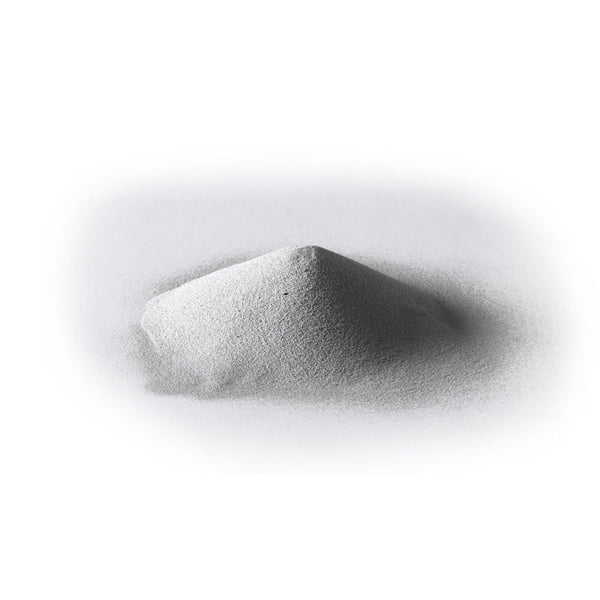
Composition of 7050 aluminium alloy powder
The 7050 aluminium alloy consists of the following typical elemental composition:
7050 Aluminium Alloy Composition
Element | Weight % |
---|---|
Aluminium (Al) | 87.7 – 91.4% |
Zinc (Zn) | 5.7 – 6.7% |
Magnesium (Mg) | 1.9 – 2.6% |
Copper (Cu) | 2.0 – 2.5% |
Zirconium (Zr) | 0.08 – 0.15% |
Other (Fe, Si, Mn, Cr, Ti) | <0.15% each |
The high levels of zinc enable precipitation hardening heat treatments to achieve very high strength. Magnesium and copper add to the age hardening effects with zinc.
Zirconium is added for grain structure control. Iron, silicon, manganese, chromium and titanium are present as impurity elements with small individual limits.
7050 aluminium alloy powder Processing
7050 aluminium alloy powder can be manufactured into fully-dense powder metallurgy components using techniques like:
- Hot Isostatic Pressing (HIP)
- Direct hot extrusion
- Metal Injection Molding
HIP involves encapsulating the powder in a container and applying heat and very high isostatic pressures in special vessels to consolidate the powder. This avoids prior compaction steps and achieves uniform properties and net shape or near-net shape parts.
Direct hot extrusion involves compacting powder into billets and then forcing it through a die to produce long profiles or rods. The high pressure and heat bond the particles during deformation into a fully dense product.
Metal injection molding allows shaping more complex net or near-net shape parts from powder using specialized tooling. The powder-binder mixture known as feedstock is injected into molds and then subjected to debinding and sintering.
The 7050 aluminium alloy powder itself is atomized from molten alloys into fine spherical powders around 10 – 45 microns diameter using inert gas atomization or water atomization processes. The purity, particle size distribution, morphology and surface oxide content is carefully controlled to enable full density during consolidation.
7050 aluminium alloy powder Properties
The properties of parts made from 7050 aluminium alloy powder can be tailored by varying processing parameters. Some typical properties after heat treatment are:
7050 Aluminium Alloy Powder Properties
Property | As-HIP Condition | T6 Heat-Treated | T7 Heat-Treated |
---|---|---|---|
Mechanical | |||
Tensile Strength | Around 350 MPa | Over 510 MPa | Around 490 MPa |
Yield Strength | Around 310 MPa | Over 455 MPa | Around 415 MPa |
Elongation | Over 10% | Around 11% | Around 12% |
Hardness | Around 150 HB | Over 175 HB | Around 170 HB |
Physical | |||
Density | 2.83 g/cm3 | 2.83 g/cm3 | 2.83 g/cm3 |
Electrical Conductivity | 43% IACS | 36% IACS | 39% IACS |
Other | |||
Shelf Life | Excellent, 5 years typical | – | – |
Corrosion Resistance | Good in peak-aged temper | Good in peak-aged temper | Good in peak-aged temper |
Weldability | Poor | Poor | Poor |
Machinability | Fair | Fair | Fair |
Fatigue Strength | Excellent | Excellent | Excellent |
The T6 temper involves solution heat treatment followed by artificial aging to achieve peak strength. T7 conditioning applies an overaging treatment after T6 to provide improved stress corrosion cracking resistance at slightly reduced strength levels.
7050 alloy powder has low density combined with high strength levels leading to excellent specific strength properties. The thermal and electrical conductivity is moderate for an aluminium alloy. Corrosion resistance is poorer than pure aluminium but acceptable in most environments.
Fatigue strength in particular is outstanding for aerospace aluminium alloys, while machinability and weldability is inferior to more formable alloys like 6061 due to the high zinc levels.
7050 aluminium alloy powder Applications
The combination of properties makes 7050 aluminium alloy powder suitable for:
Applications of 7050 Aluminium Alloy Powder
Industry | Application | Reasons |
---|---|---|
Aerospace | Structural airframe parts, landing gear, wings, fittings | High strength-to-weight ratio, fatigue performance |
Automotive | Chassis, suspension, transmission cases | High specific strength, replaces cast alloys |
Industrial | Robotics, rigging, lifting equipment | Strength, weldability issues less critical |
Defence | Armour plate, military vehicles | Ballistic protection, moderate density |
Marine | Brackets, naval ship parts | Corrosion resistance in marine environments |
Sports | Bicycle parts, golf club heads | Performance characteristics |
For aerospace use, 7050 is second in use only to 7075 aluminium alloy for strength-critical airframe components requiring durability. HIP processed parts tend to replace forgings and billet-based parts.
Automotive and defence applications take advantage of lightweighting and performance over more conventional aluminium or magnesium alloys, with improved mechanical properties over composites.
7050 aluminium alloy powder Specifications
7050 alloy powder and consolidated products meet various specifications that define the composition limits, processing methods, properties and quality requirements for aerospace and defence applications:
7050 Aluminium Alloy Powder Specifications
Standard | Title |
---|---|
AMS 4282 | Metallic Powder for PM Structural Parts |
AMS 4285 | Alloy HIP Consolidated Powder for PM Structural Parts |
ASTM B947 | Powder Metallurgy (PM) Aluminum Alloys |
AA 7050 | Aluminum Association 7050 Alloy |
Specifications cover powder size distribution, shape and flow characteristics, impurity limits, typical density and mechanical properties in different heat treatment conditions, sampling procedures, testing methods, inspection criteria and documentation requirements.
7050 aluminium alloy powder Suppliers
Some leading global suppliers of 7050 aluminium alloy powders include:
7050 Aluminium Alloy Powder Suppliers
Company | Location |
---|---|
Sandvik Osprey | UK |
Alpoco | UK |
Valimet Inc. | USA |
These companies offer gas- or water-atomized 7050 aluminium alloy powders customized for additive manufacturing or metal injection molding feedstock applications with specialized particle size distributions and shapes.
In addition, major metal powder producers and consolidators have extensive experience working with 7050 alloy systems optimized for hot isostatic pressing to aerospace component specifications.
7050 aluminium alloy powder Cost
7050 aluminium alloy powder prices depend significantly on:
- Purity / Impurity levels
- Particles size distribution
- Morphology and shape
- Purchase quantity
- Additional processing like sieving
Indicative pricing for gas-atomized spherical 7050 powder suitable for additive manufacturing is around $50 – $65 per kg. Prices are higher for tighter distributions needed for MIM feedstocks or hot isostatic pressing.
7050 aluminium alloy powder Pros and Cons
Advantages of 7050 Aluminium Alloy Powder
- Highest strength 7xxx series alloy
- Excellent fatigue performance
- Low density
- Used extensively in aerospace industry
- Replaces steels and titanium alloys
- Parts can be complex, monolithic shapes
Limitations of 7050 Aluminium Alloy Powder
- Moderate corrosion resistance
- Weldability issues
- Lower thermal / electrical conductivity
- Cost is higher than normal extrusion alloys
- Processing has more controls and qualifications
For many critical structural parts needed in performance applications, 7050 delivers the vital combination of strength, damage tolerance and low weight. Despite some fabrication and corrosion drawbacks, the capabilities offset the slightly higher powder cost where weight savings matter.
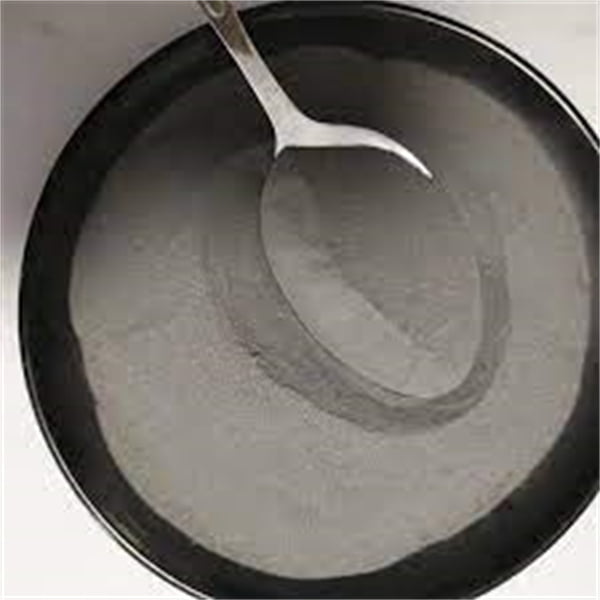
FAQs
Frequently Asked Questions on 7050 Aluminium Alloy Powder
Q: What is 7050 aluminium alloy?
A: 7050 is a very high strength 7xxx series aluminium alloy containing major additions of zinc, magnesium and copper plus trace additions like zirconium. It is age-hardenable to achieve an exceptional combination of tensile properties and fatigue resistance.
Q: Is 7050 stronger than 7075?
A: Yes, 7050 aluminium alloy has slightly higher ultimate tensile and yield strengths than the very popular 7075 alloy in peak-aged tempers, along with superior fatigue strength. It matches the corrosion resistance of 7075.
Q: What are some uses of 7050 aluminium?
A: Key uses are aircraft structural parts like wing skins, fittings and pylons, helicopter rotor components like spindles, automotive chassis and suspension parts, applications like armour, space booms, lifting equipment, and sporting goods like golf clubheads and bicycle rims.
Q: What processing methods can make 7050 alloy parts?
A: While traditional wrought processes like extrusion and forging can make 7050 products, powder metallurgy techniques are growing rapidly including hot isostatic pressing (HIP), direct hot extrusion and metal injection molding (MIM) to exploit the alloy’s strengths.
Q: Is 7050 aluminium weldable?
A: No, welding of 7050 alloy is very difficult compared to medium or lower strength alloys due to cracking issues cause by its high zinc and copper content. Mechanical fastening or adhesive bonding are alternate joining methods recommended.
Q: What replaces 7050 aluminium alloys?
A: For the highest strength requirements where fatigue life is less critical, very high strength aerospace aluminium alloys like C465 or 7085 are being evaluated to replace certain applications of 7050 alloy. Composites and advanced metal alloys are also competing solutions.
Share On
MET3DP Technology Co., LTD is a leading provider of additive manufacturing solutions headquartered in Qingdao, China. Our company specializes in 3D printing equipment and high-performance metal powders for industrial applications.
Inquiry to get best price and customized Solution for your business!
Related Articles
About Met3DP
Recent Update
Our Product
CONTACT US
Any questions? Send us message now! We’ll serve your request with a whole team after receiving your message.
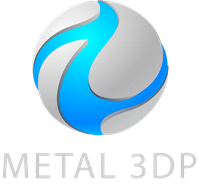
Metal Powders for 3D Printing and Additive Manufacturing