7050 aluminum alloy powder
Table of Contents
7050 aluminum alloy powder is a high-strength material increasingly used across aviation, aerospace, automotive and other demanding industries. This advanced alloy powder combines excellent mechanical properties with good corrosion resistance.
In this comprehensive guide, we will cover everything you need to know about 7050 aluminum alloy powder, including:
Overview of 7050 Aluminum Alloy Powder
7050 aluminum alloy powder belongs to the 7xxx series of high-strength alloys. It is considered a superior alternative to incumbent aerospace alloys like 2024 and 7075.
Key properties:
- High strength and hardness
- Good fracture toughness
- Excellent fatigue and creep resistance
- Good stress corrosion cracking resistance
- Low density
- Good machinability and polishability
Alloying elements:
- Zinc – 5.7-6.7%
- Magnesium – 2.0-2.6%
- Copper – 2.0-2.6%
- Zirconium – 0.08-0.15%
Production process:
7050 alloy powder is produced using gas atomization, a process which involves melting the alloy and disintegrating the molten stream into fine droplets that solidify into powder.
Particle size ranges:
- 15-45 microns for thermomechanical processing
- 45-150 microns for other PM processes
- Nanopowders under 100 nm
Applications:
- Aerospace and aviation parts
- Automotive components
- Structural parts
- Medical implants
- 3D printing powders
The combination of strength, toughness, machinability and corrosion resistance make 7050 alloy a versatile material across sectors.
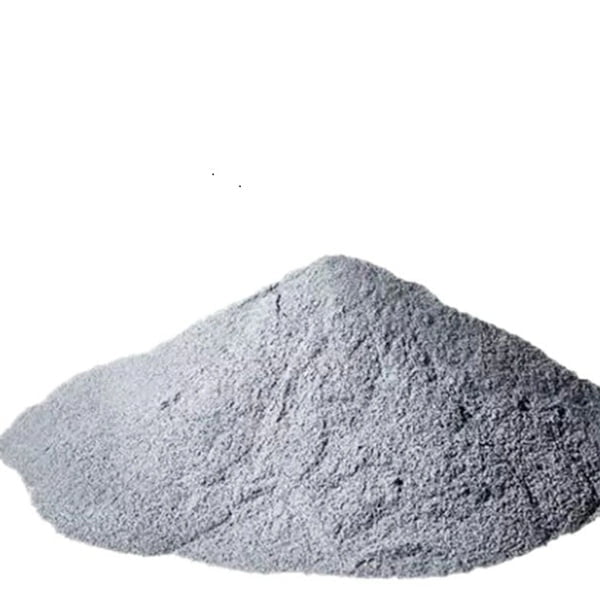
Types of 7050 Aluminum Alloy Powder
7050 aluminum alloy powder is commercially available in several forms:
Gas Atomized Powder
Produced using inert gas jets to break up molten metal into fine droplets.
Characteristics:
- Spherical particles with smooth surface
- Tight particle size distribution
- High purity and density
Applications:
- Additive manufacturing
- Metal injection molding
Water Atomized Powder
Involves disintegration of melt stream into water.
Characteristics:
- Irregular particle shapes
- Wider size distribution
- Oxidized surface, porosity
- Lower cost
Applications:
- P/M parts with less critical performance requirements
- MIM for consumer products
Mechanical Alloyed Powder
Powder particles are repeatedly welded, fractured and rewelld by ball milling.
Benefits:
- Microstructure refinement
- Alloy customization flexibilty
- Oxide-free powder
Recycled Powder
Reusing scrap/waste powder from AM and MIM processes.
Advantages:
- Environmental sustainability
- Reduced material costs
The powder production method significantly influences final part properties and performance.
Properties of 7050 Aluminum Alloy Powder
7050 alloy powder possesses an exceptional combination of mechanical properties:
Property | Function |
---|---|
High strength | Withstands heavy loads without permanent deformation |
Fatigue strength | Resists crack growth under cyclic stresses |
Fracture toughness | Ability to absorb impact energy before cracking |
Hardness | Resistance to surface wear and indentation |
Creep resistance | Retains strength and shape under sustained loads and heating |
Corrosion resistance | Performs reliably in harsh environments |
Thermal conductivity | Rapidly conducts heat away from parts |
Electrical conductivity | Allows use in conductive components |
Low density | Reduces component weight |
These properties make 7050 suitable for critical structural parts across aviation, defense, automotive and other demanding applications.
Applications and Uses of 7050 Aluminum Alloy Powder
7050 aluminum alloy powder is increasingly deployed in the following sectors and applications:
Industry | Applications |
---|---|
Aerospace | Airframe parts, wing skins, fuselage structures, fasteners, engine components |
Aviation | Seats, doors, landing gear and wheels, hydraulic components |
Automotive | Pistons, driveshafts, valves, brackets, gears, steering parts |
Industrial | Robotics, tooling, conveyors, rigs, marine hardware |
Electronics | Housings, heat sinks, EMI/RFI shielding |
Medical | Implants, prosthetics, instrumentation |
Other niche uses include sporting goods, ammunition, high-end bicycles and camera equipment.
The lightweight strength of 7050 makes it a material of choice for critical structures and components.
7050 Aluminum Alloy Powder Specifications
7050 aluminum alloy powder can be customized as per application requirements:
Parameter | Options |
---|---|
Alloy composition | Zn, Mg, Cu, Zr, Mn |
Particle size | 15-45 microns, 45-150 microns, nanoparticles |
Particle shape | Spherical, irregular |
Density | Up to 98% of theoretical |
Flowability | Excellent to average |
Surface oxide | Low (<2%) |
Contamination | Minimized (ppm levels) |
Defects | Low porosity and satellites |
Common compositions:
- Zn: 5.7-6.7%
- Mg: 2-2.6%
- Cu: 1.9-2.6%
Size ranges:
- Fine powder <45 μm for AM
- Coarse 45-150 μm for MIM
Controlling powder quality is vital to achieve required material performance.
Design and Engineering Standards for 7050 Alloy
Key design and quality standards for 7050 aluminum alloy include:
- ASTM B854 – Standard Specification for 7050 Aluminum Alloy Powder
- AMS 4126 – 7050 Alloy Metallic Powders for PM Applications
- AMS 4290 – Metallurgical Processes for Recycle of 7050 Alloy
- ASTM E8 – Tensile Testing of Metallic Materials
- ISO 209 – Determination of Grain Size
- SAE AIR5714 – Process Characterization of Powder Bed Fusion
- AMS 2175 – Heat Treatment of Aluminum Powder Metallurgy Alloys
Compliance ensures optimal powder quality and consistent alloy performance.
Suppliers of 7050 Aluminum Alloy Powder
Reputable 7050 alloy powder manufacturers include:
Company | Location | Products | Pricing |
---|---|---|---|
Advanced Powders | USA | Gas atomized 7050 | $xx to $xxx/kg |
Praxair Surface Technologies | USA | Water and gas atomized | $xx to $xxx/kg |
Valimet | USA | Custom alloys and sizes | $xx to $xxx/kg |
Ecka Granules | Germany | Water atomized Al alloys | $xx to $xxx/kg |
TLS Technik | Germany | Gas and water atomized | $xx to $xxx/kg |
Other major suppliers:
- Sandvik Osprey
- Hoganas
- CNPC Powder
- Mitsui Kinzoku
When selecting a supplier, consider factors like production capacity, lead times, reliability, technical support and pricing.
How to Choose a 7050 Alloy Powder Supplier
Here are key considerations when choosing a 7050 aluminum alloy powder supplier:
- Technical expertise in aluminum PM processing
- Stringent quality assurance – sampling, testing, analysis, documentation
- Qualifications and certifications – ISO, AS9100 etc.
- Spherical morphology capabilities for additive manufacturing
- Customization flexibility – size, shape, composition, density
- Production capacity to meet demand volumes
- R&D competence for novel alloys and parameters
- Reasonable pricing structure for quality products
- Strong customer service and technical support
Partnering with a knowledgeable supplier minimizes development issues and ensures high, consistent powder quality tailored to your application.
Installing and Operating 7050 Alloy Powder Equipment
Here are some installation and operation guidelines for 7050 powder processing equipment:
Equipment | Installation Tips | Operation/Maintenance |
---|---|---|
Gas atomizer | Utilities hookup, power, nitrogen, cooling | Monitor gas flow, temperature; clean nozzles |
Mill | Level foundation, emergency stop | Control speed, cooling water; media change |
Mesh sifters | Anchor firmly | Inspect screens; clean; prevent clogging |
Mixers | Ground electrically, access | Do not overmix; check blade condition |
Powder feeder | Calibrate, test connectivity | Change spiders; inspect rollers, screws |
Safety:
- Use dust collection systems
- Provide proper grounding
- Wear appropriate PPE
- Follow lockout/tagout procedures
- Install emergency stops
Proper installation matched with preventive maintenance minimizes problems and improves equipment longevity.
How to Choose a 7050 Alloy Powder Equipment Manufacturer
When selecting powder equipment manufacturers, key factors include:
Parameter | Preferences |
---|---|
Expertise | Experience with similar aluminum alloy equipment |
Proven designs | Field-tested reliability |
Customization | Ability to modify for specific needs |
Production scale | Matches output rate needs |
Easy maintenance | Quick cleaning and part replacement |
Automated features | For productivity and consistency |
Energy efficiency | Reasonable power consumption |
Safety mechanisms | Interlocks, E-stops, sensors |
Temperature controls | For optimal heating and cooling |
Training and support | Installation help, troubleshooting |
Choose industry-recognized manufacturers providing customizable equipment engineered for safety, longevity and performance.
Pros and Cons of 7050 Aluminum Alloy Powder
Advantages
- High strength and hardness
- Excellent fatigue and fracture resistance
- Good corrosion and SCC resistance
- Lightweight compared to steels
- High thermal and electrical conductivity
- Good machinability and polishability
- Recyclable and environmentally friendly
Limitations
- Lower strength than steels and titanium alloys
- Susceptible to galvanic corrosion
- Requires surface protection in some environments
- High cost compared to 2xxx and 6xxx alloys
- Limited high temperature capability
- Difficult to weld in certain tempers
- Anisotropic properties
Understanding the strengths and limitations aids selection of 7050 alloy versus alternatives. Proper design and processing is key.
Comparing 7050 Alloy Powder to Alternatives
VS 2024 Al Alloy
- Higher strength and fracture toughness
- Better SCC resistance
- Higher cost
- Lower thermal stability
VS 7075 Al Alloy
- Higher strength with similar toughness
- Better stress corrosion cracking resistance
- Lower thermal stability
- More expensive
VS 6061 Al Alloy
- Much greater strength
- Lower corrosion resistance
- More difficult to weld and machine
- Higher cost
VS Ti-6Al-4V Alloy
- Lower strength and hardness
- Lighter weight
- Better thermal and electrical conductivity
- Lower service temperature capabilities
VS Maraging Steels
- Lower strength but higher fracture toughness
- Lighter weight
- Better corrosion resistance
- Lower service temperatures
7050 aluminum alloy offers an optimal balance of strength, toughness, weight and corrosion resistance for critical applications in aerospace, aviation and other sectors.
Future Outlook
The 7050 aluminum alloy powder market is forecast to expand at 8%+ CAGR over the next decade, driven by:
- Increasing adoption in aerospace and aviation sectors
- Next-generation lower density aircraft components
- Automotive lightweighting trends
- Growth of metal additive manufacturing
- High-performance racing applications
- Declining use of incumbent 2xxx and 7xxx alloys
Key future trends include:
- Development of novel 7xxx alloys rivaling 7050
- Powder recycling and reuse initiatives
- Nanopowder and microstructure optimization
- Automation and smart manufacturing
- Inventory management and just-in-time powder supply
With growing demand from high-performance sectors, continued innovation will shape the future landscape of 7050 and other advanced aluminum alloy powders.
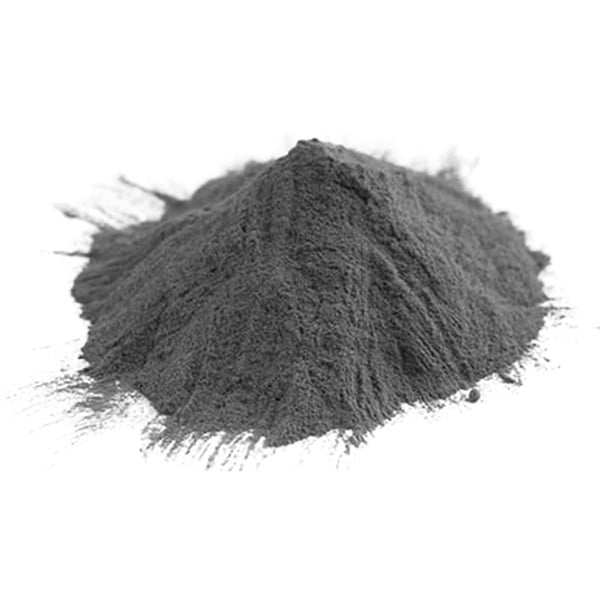
FAQ
Q: What are the main alloying elements in 7050 aluminum alloy?
A: The main alloying elements are zinc, magnesium, copper and zirconium. Trace elements like silicon, iron, manganese, chromium and titanium may also be present.
Q: What is 7050 alloy used for?
A: Key applications are aerospace structural components, aviation parts, automotive components, and high-performance equipment due to its strength.
Q: Is 7050 stronger than 2024 and 7075 aluminum alloys?
A: Yes, 7050 exhibits higher yield and tensile strength compared to incumbent 2024 and 7075 aerospace alloys.
Q: Is 7050 corrosion resistant?
A: 7050 possesses good SCC resistance and corrosion resistance in certain tempers, superior to other 7xxx alloys. Proper heat treatment optimizes corrosion performance.
Q: What is the difference between 7050 and 7075 aluminum alloy?
A: 7050 has higher strength, hardness, and SCC resistance compared to 7075, while 7075 offers better fracture toughness and thermal stability.
Q: What are common tempers for 7050 aluminum?
A: Commonly used tempers include T7351, T7451, T74511, and T7651. The T7451 temper offers the best combination of strength, SCC resistance and fracture toughness.
Q: Is 7050 aluminum weldable?
A: Weldability is fair. Friction stir welding and gas metal arc welding offer good results. Susceptibility to hot cracking must be controlled with optimized filler and process parameters.
Q: What is the typical density of 7050 aluminum alloy?
A: The density of 7050 alloy is around 2.83 g/cm3, which is significantly lower than steels, nickel alloys and titanium alloys.
Q: What are common uses of 7050 alloy in the aerospace industry?
A: Structural aircraft components including wing skins, fuselage frames, bulkheads, fasteners, landing gear parts, wheels and other critical airframe parts.
Q: Is 7050 alloy cheaper than titanium alloys?
A: Yes, 7050 aluminum is significantly more economical compared to widely used titanium alloys like Ti-6Al-4V while providing substantial weight savings over steels.
Share On
MET3DP Technology Co., LTD is a leading provider of additive manufacturing solutions headquartered in Qingdao, China. Our company specializes in 3D printing equipment and high-performance metal powders for industrial applications.
Inquiry to get best price and customized Solution for your business!
Related Articles
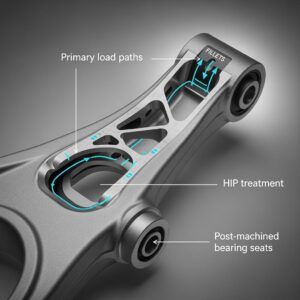
Metal 3D Printing for U.S. Automotive Lightweight Structural Brackets and Suspension Components
Read More »About Met3DP
Recent Update
Our Product
CONTACT US
Any questions? Send us message now! We’ll serve your request with a whole team after receiving your message.