Comprehensive Guide of Arc Welding
Table of Contents
Overview of Arc Welding
Arc welding, a core technique in the field of metalworking, involves using an electric arc to melt and join metals. Whether you’re a professional welder, an engineering student, or just a curious mind, this guide will cover everything you need to know about arc welding—from the basics to the intricacies of metal powder models used in the process.
Arc welding isn’t just a method; it’s an art form where precision meets technology. Imagine fusing pieces of metal together with the sheer power of electricity—sounds fascinating, right? Let’s dive deep into the world of arc welding.
What is Arc Welding?
Arc welding is a process that uses an electric arc to generate heat, which melts and fuses metals. The power source, which can be either AC or DC, creates an arc between the electrode and the base material, producing temperatures up to 7,000 degrees Fahrenheit. This intense heat melts the metals, allowing them to join once they cool and solidify.
Key Components of Arc Welding
- Power Source: Supplies the electrical energy.
- Electrode: Conducts the current and melts to form the weld.
- Base Metal: The material being welded.
- Shielding Gas: Protects the weld area from atmospheric contamination (in some processes).
- Filler Material: Sometimes added to reinforce the weld.
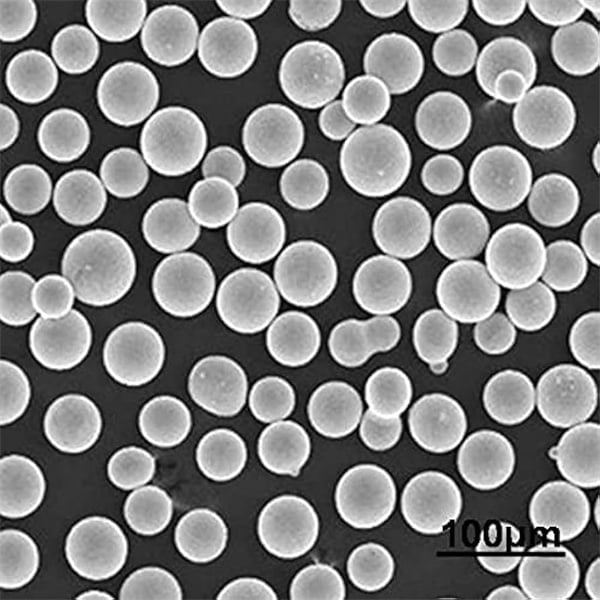
Types of Arc Welding
Arc welding comes in various forms, each suited for different applications and materials. Here’s a detailed look:
Type | Description | Applications | Characteristics |
---|---|---|---|
Shielded Metal Arc Welding (SMAW) | Uses a consumable electrode coated in flux. | Construction, shipbuilding | Versatile, portable, suitable for outdoor use. |
Gas Metal Arc Welding (GMAW/MIG) | Uses a wire electrode and shielding gas. | Automotive, manufacturing | High productivity, minimal cleanup, suitable for thin metals. |
Gas Tungsten Arc Welding (GTAW/TIG) | Uses a non-consumable tungsten electrode and shielding gas. | Aerospace, piping | High precision, clean welds, suitable for thin and thick metals. |
Flux-Cored Arc Welding (FCAW) | Similar to MIG but uses a flux-cored wire. | Heavy equipment, construction | High deposition rate, suitable for thicker materials. |
Submerged Arc Welding (SAW) | Uses a continuously fed electrode and granular flux. | Structural steel fabrication | High quality, deep weld penetration, limited to flat positions. |
Specific Metal Powder Models for Arc Welding
When it comes to arc welding, the choice of metal powders can significantly influence the quality and characteristics of the weld. Here are some specific metal powder models:
- H13 Tool Steel Powder: Known for its high toughness and resistance to thermal fatigue. Ideal for welding dies and tools.
- 316L Stainless Steel Powder: Offers excellent corrosion resistance and is used in food processing and marine applications.
- Inconel 625 Powder: High strength and excellent fatigue resistance, suitable for aerospace and chemical industries.
- Cobalt Chrome Powder: Superior wear resistance and strength, often used in medical implants and turbine blades.
- Aluminum 6061 Powder: Lightweight with good mechanical properties, used in automotive and aerospace industries.
- Titanium Ti-6Al-4V Powder: High strength-to-weight ratio, corrosion-resistant, commonly used in aerospace and biomedical fields.
- Copper Alloy Powder: Excellent thermal and electrical conductivity, used in electrical components and heat exchangers.
- Tungsten Carbide Powder: Extremely hard and wear-resistant, ideal for cutting tools and wear-resistant coatings.
- Nickel Alloy 718 Powder: High strength and corrosion-resistant, used in gas turbines and power generation.
- Maraging Steel Powder: High strength and toughness, used in aerospace, tooling, and high-stress components.
Composition, Properties, and Characteristics
Metal Powder | Composition | Properties | Characteristics |
---|---|---|---|
H13 Tool Steel | Fe, Cr, Mo, V, Si, Mn | High toughness, thermal fatigue resistance | Ideal for hot work applications |
316L Stainless Steel | Fe, Cr, Ni, Mo | Excellent corrosion resistance | Used in harsh environments |
Inconel 625 | Ni, Cr, Mo, Nb, Fe | High strength, fatigue resistance | Suitable for extreme environments |
Cobalt Chrome | Co, Cr, Mo, Si | Superior wear resistance | Common in medical and aerospace applications |
Aluminum 6061 | Al, Mg, Si | Lightweight, good mechanical properties | Versatile for various lightweight structures |
Titanium Ti-6Al-4V | Ti, Al, V | High strength-to-weight ratio | Common in aerospace and biomedical applications |
Copper Alloy | Cu, Zn, Pb, Sn | Excellent thermal and electrical conductivity | Widely used in electrical and thermal management applications |
Tungsten Carbide | W, C | Extremely hard, wear-resistant | Ideal for cutting tools and wear-resistant applications |
Nickel Alloy 718 | Ni, Cr, Mo, Nb, Ti, Al | High strength, corrosion-resistant | Suitable for high-stress and high-temperature applications |
Maraging Steel | Fe, Ni, Co, Mo, Ti | High strength, toughness | Used in high-stress components and tooling |
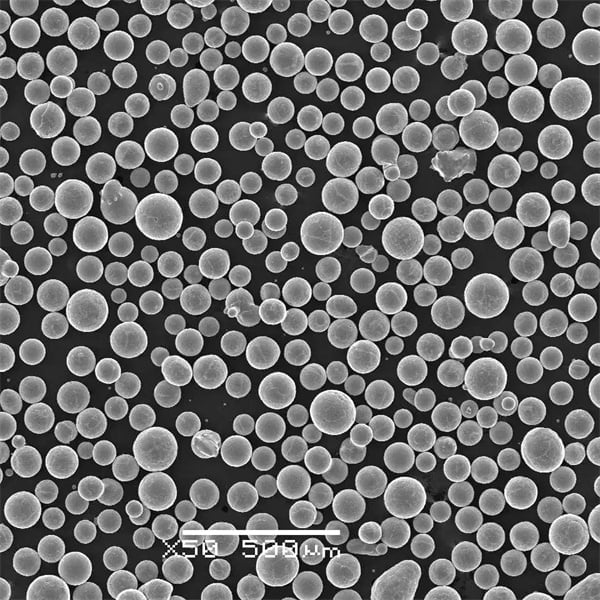
Applications of Arc Welding
Arc welding is used across various industries due to its versatility and efficiency. Let’s look at some applications:
Industry | Application |
---|---|
Construction | Structural steel fabrication, bridges, buildings |
Automotive | Bodywork, chassis assembly, exhaust systems |
Aerospace | Aircraft frames, engine components |
Shipbuilding | Hull construction, pipelines |
Manufacturing | Machinery, equipment, consumer goods |
Energy | Pipelines, power plants, offshore platforms |
Medical | Surgical instruments, implants |
Electronics | Circuit boards, connectors |
Specifications, Sizes, Grades, and Standards
Choosing the right specifications, sizes, grades, and standards is crucial for the success of any welding project. Here’s a detailed breakdown:
Material | Specification | Sizes | Grades | Standards |
---|---|---|---|---|
H13 Tool Steel | ASTM A681 | Rods, bars, sheets | H13 | ASTM, AISI, DIN |
316L Stainless Steel | ASTM A240, ASTM A276 | Plates, sheets, bars | 316L | ASTM, AISI, ISO |
Inconel 625 | ASTM B443, AMS 5599 | Plates, sheets, bars | 625 | ASTM, AMS, ISO |
Cobalt Chrome | ASTM F75, ASTM F1537 | Rods, powders | F75 | ASTM, ISO |
Aluminum 6061 | ASTM B209, ASTM B221 | Sheets, plates, extrusions | 6061 | ASTM, SAE, ISO |
Titanium Ti-6Al-4V | ASTM B265, ASTM B348 | Bars, sheets, plates | Ti-6Al-4V | ASTM, AMS, ISO |
Copper Alloy | ASTM B36, ASTM B124 | Rods, bars, sheets | C11000, C28000 | ASTM, SAE, ISO |
Tungsten Carbide | ISO 9001, ASTM B777 | Powders, rods | WC-Co | ISO, ASTM |
Nickel Alloy 718 | ASTM B670, AMS 5662 | Sheets, bars, forgings | 718 | ASTM, AMS, ISO |
Maraging Steel | ASTM A538, AMS 6521 | Rods, sheets, bars | 300, 350 | ASTM, AMS, ISO |
Suppliers and Pricing Details
Pricing and supplier information are crucial for project planning and budgeting. Here’s a table summarizing some key suppliers and pricing details:
Supplier | Metal Powder | Price per kg (USD) | Location | Website |
---|---|---|---|---|
Carpenter Technology | H13 Tool Steel | $25 | USA | www.cartech.com |
Sandvik Materials | 316L Stainless Steel | $35 | Sweden | www.materials.sandvik |
Haynes International | Inconel 625 | $50 | USA | www.haynesintl.com |
Arcam AB | Cobalt Chrome | $45 | Sweden | www.arcam.com |
Alcoa Inc. | Aluminum 6061 | $20 | USA | www.alcoa.com |
Timet (Titanium Metals) | Titanium Ti-6Al-4V | $60 | USA | www.timet.com |
Luvata | Copper Alloy | $15 | Finland | www.luvata.com |
Kennametal | Tungsten Carbide | $70 | USA | www.kennametal.com |
VDM Metals | Nickel Alloy 718 | $55 | Germany | www.vdm-metals.com |
Bohler Uddeholm | Maraging Steel | $40 | Austria | www.bohler-uddeholm.com |
Pros and Cons of Arc Welding
Understanding the advantages and limitations of arc welding can help you decide if it’s the right method for your project.
Aspect | Advantages | Disadvantages |
---|---|---|
Versatility | Suitable for various metals and thicknesses | Requires skilled labor |
Equipment | Generally portable and cost-effective | Some processes need specific and costly equipment |
Quality | Can produce high-quality, strong welds | Potential for defects if not done correctly |
Speed | High productivity, especially in automated processes | Slower than some other methods (e.g., laser welding) |
Environment | Can be performed outdoors with proper protection | Shielding gas processes are sensitive to wind and drafts |
Material Cost | Some processes use inexpensive consumables (e.g., SMAW) | High-quality electrodes and filler materials can be costly |
Flexibility | Adaptable to various positions and conditions | Certain types like SAW are limited to specific positions |
Arc Welding Techniques and Best Practices
To achieve the best results in arc welding, follow these best practices:
- Proper Preparation: Clean the base metals thoroughly to remove contaminants.
- Correct Electrode Selection: Choose the right electrode type and size for the material and position.
- Maintaining Arc Length: Keep a consistent arc length suitable for the electrode type.
- Proper Shielding: Ensure adequate shielding to protect the weld pool from contamination.
- Control Heat Input: Use appropriate current settings to control the heat input and avoid warping.
- Welding Speed: Maintain a steady welding speed to ensure a uniform weld bead.
- Safety Measures: Always wear protective gear, including gloves, helmet, and eye protection.
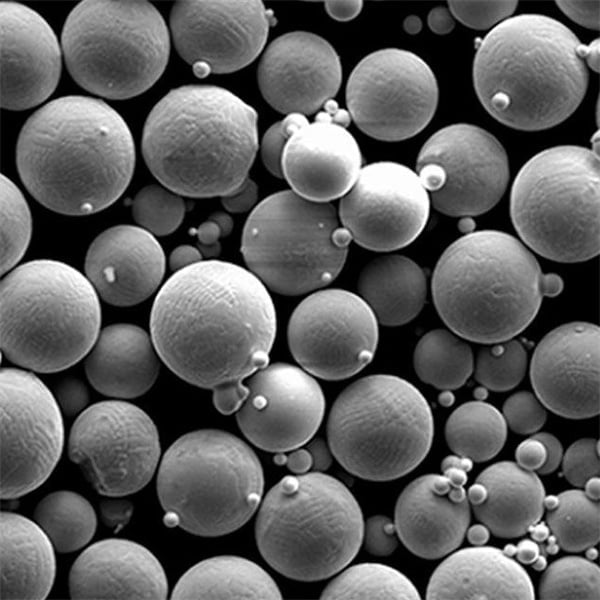
FAQs
Question | Answer |
---|---|
What is arc welding used for? | Arc welding is used for joining metals in construction, automotive, aerospace, shipbuilding, and manufacturing. |
What are the types of arc welding? | Common types include SMAW, GMAW/MIG, GTAW/TIG, FCAW, and SAW. |
How does arc welding work? | It uses an electric arc to generate heat that melts and fuses metals. |
What materials can be welded with arc welding? | Steel, stainless steel, aluminum, nickel alloys, titanium, and more. |
What is the difference between MIG and TIG welding? | MIG uses a consumable wire electrode and is faster; TIG uses a non-consumable tungsten electrode and is precise. |
What safety precautions should be taken during arc welding? | Wear protective gear, ensure proper ventilation, and follow safety protocols to avoid burns and electrical hazards. |
How do you choose the right electrode for arc welding? | Consider the base metal, welding position, and desired properties of the weld. |
Can arc welding be automated? | Yes, many arc welding processes can be automated for increased efficiency and consistency. |
What is the role of shielding gas in arc welding? | It protects the weld pool from atmospheric contamination, ensuring a clean weld. |
What are common defects in arc welding and how can they be prevented? | Common defects include porosity, cracks, and slag inclusion; they can be prevented by proper technique and preparation. |
Arc welding is a versatile and robust method for joining metals, suitable for a wide range of applications from industrial fabrication to artistic metalworking. By understanding the types, techniques, and best practices, you can ensure high-quality welds that meet your project’s specifications. Whether you’re a seasoned welder or just starting, mastering arc welding opens up a world of possibilities in metalworking.
Share On
MET3DP Technology Co., LTD is a leading provider of additive manufacturing solutions headquartered in Qingdao, China. Our company specializes in 3D printing equipment and high-performance metal powders for industrial applications.
Inquiry to get best price and customized Solution for your business!
Related Articles
About Met3DP
Recent Update
Our Product
CONTACT US
Any questions? Send us message now! We’ll serve your request with a whole team after receiving your message.
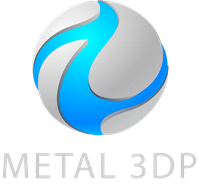
Metal Powders for 3D Printing and Additive Manufacturing