TiNb Alloy Powder
Titanium niobium (TiNb) alloy powder is an advanced material with excellent properties for use in biomedical, aerospace, automotive and other demanding applications. This article provides a comprehensive guide to TiNb alloy powder covering composition, properties, processing, applications, specifications, suppliers, costs, handling and more.
Low MOQ
Provide low minimum order quantity to meet different needs.
OEM & ODM
Provide customized products and design services to meet unique customer needs.
Adequate Stock
Ensure fast order processing and provide reliable and efficient service.
Customer Satisfaction
Provide high quality products with customer satisfaction at the core.
share this product
Table of Contents
Introduction to TiNb Alloy Powder
TiNb alloy powder is composed of titanium and niobium metals. It offers a unique combination of high strength, low density, biocompatibility, corrosion resistance, fatigue and creep resistance at high temperatures.
TiNb alloys are part of a broader class of titanium intermetallic materials that have superior physical, chemical and mechanical properties compared to pure titanium. The addition of niobium as an alloying element enhances certain properties and allows tailoring TiNb alloys for specific applications.
Some key advantages of TiNb alloy powder include:
- High strength-to-weight ratio
- Ability to withstand extreme temperatures and stresses
- Resists wear, abrasion and corrosion in harsh environments
- Biocompatible and non-toxic for medical uses
- Can be processed into complex shapes using additive manufacturing
- Provides design flexibility for engineers
TiNb alloys compete with nickel and cobalt-based superalloys in the aerospace industry. They also offer an alternative to stainless steels for biomedical implants and devices. TiNb alloys are enabling new applications and designs not possible with other materials.
This article provides a technical reference covering the composition, properties, processing, applications, specifications, costs and other practical aspects of TiNb alloy powder.
TiNb Alloy Powder Composition
TiNb alloys contain primarily titanium and niobium as the key constituent elements. The niobium content typically ranges from 10% to 50% by weight, with the balance being titanium.
The ratio of Ti to Nb can be adjusted to create different grades of TiNb alloys optimized for certain properties. Some common TiNb grades include:
- Ti-10Nb – 10% niobium, 90% titanium
- Ti-35Nb – 35% niobium, 65% titanium
- Ti-45Nb – 45% niobium, 55% titanium
- Ti-50Nb – 50% niobium, 50% titanium
Additionally, small amounts of other elements like zirconium, tantalum, molybdenum, chromium may be added to further enhance properties. Oxygen and nitrogen may also be present as impurities.
Table 1: Chemical composition of common TiNb alloy grades
Alloy Grade | Niobium Content | Titanium Content |
---|---|---|
Ti-10Nb | 10% | 90% |
Ti-35Nb | 35% | 65% |
Ti-45Nb | 45% | 55% |
Ti-50Nb | 50% | 50% |
Controlling the composition is critical to achieve the desired properties in the final TiNb alloy product. Powder metallurgy techniques allow precise mixing of the constituent metals into an alloy powder feedstock.
TiNb Alloy Powder Properties
TiNb alloys exhibit a range of useful physical, mechanical and chemical properties that make them suitable for high performance applications. Some key properties include:
Physical Properties
- Density – 4.5 to 5.5 g/cm3, lower than steel and nickel alloys
- Melting point – 1550 to 1750°C depending on composition
- Electrical resistivity – 0.5 to 0.6 μΩ.m, higher than pure titanium
- Thermal conductivity – 6 to 22 W/m.K, lower than titanium
Mechanical Properties
- Tensile strength – 500 to 1100 MPa, increases with niobium content
- Yield strength – 300 to 900 MPa
- Elongation – 10% to 25%
- Hardness – 200 to 350 HV
- Fatigue strength – 400 to 600 MPa
Other Properties
- Corrosion resistance – Excellent due to protective oxide layer
- Wear resistance – Better than titanium due to hardness
- Biocompatibility – Non-toxic and non-allergenic
By adjusting the Ti/Nb ratio, properties like strength, ductility, hardness and elastic modulus can be optimized as per application requirements.
Table 2: Typical properties of Ti-35Nb alloy
Property | Value |
---|---|
Density | 5.2 g/cm3 |
Melting point | 1600°C |
Tensile strength | 650 MPa |
Yield strength | 550 MPa |
Elongation | 15% |
Elastic modulus | 60 GPa |
Hardness | 250 HV |
TiNb Alloy Powder Applications
The unique properties of TiNb alloys make them suitable for demanding applications in various industries:
Aerospace
- Engine components – blades, discs, fasteners
- Airframe parts – landing gear, wings, fuselage
- Hydraulic systems – pumps, valves, actuators
Automotive
- Valve springs, engine valves
- Connecting rods, turbocharger rotors
- Motor racing components
Biomedical
- Orthopedic implants – knee, hip
- Dental implants, crowns
- Surgical instruments
- Medical devices
Chemical Industry
- Heat exchangers, reactors
- Pumps, valves, pipes
- Corrosion-resistant equipment
Other Applications
- Sporting goods – golf clubs, bike frames
- High-end watches and jewelry
- Electrical contacts and connectors
- High temperature furnace parts
The combination of strength, temperature resistance, corrosion resistance and biocompatibility allows TiNb alloys to substitute heavier materials across these industries.
Table 3: TiNb alloy applications by industry
Industry | Applications |
---|---|
Aerospace | Engine components, airframe parts, hydraulic systems |
Automotive | Valve springs, engine valves, connecting rods |
Biomedical | Implants, dental, surgical instruments, devices |
Chemical | Heat exchangers, reactors, pumps, valves |
Other | Sporting goods, watches, electrical contacts, furnace parts |
TiNb Alloy Powder Processing
TiNb alloy powder can be produced via different processing routes:
Metal Powder Blending
- elemental titanium and niobium powders are blended together in the required composition
- blended powder mixture is mechanically alloyed to form the TiNb alloy powder
Gas Atomization
- molten TiNb alloy is atomized with an inert gas into fine droplets
- droplets solidify into spherical alloy powder particles
Plasma Rotating Electrode Process (PREP)
- TiNb electrode rod is melted using plasma arc and spun at high speeds
- centrifugal force causes droplets to break off and solidify into particles
Hydride-Dehydride (HDH) Method
- Ti and Nb metals are converted into brittle hydride powders
- hydride powders are blended, dehydrided, crushed and sieved
The particle size, morphology, flowability and microstructure of the powder can be controlled by selecting the appropriate manufacturing process. This influences the final properties after consolidation.
Table 4: TiNb alloy powder production methods
Method | Description | Particle Size | Morphology |
---|---|---|---|
Mechanical alloying | Blending and milling Ti and Nb powders | 10 – 50 microns | Irregular, angular |
Gas atomization | Inert gas atomization of molten alloy | 15 – 150 microns | Spherical |
Plasma rotating electrode | Centrifugal disintegration of melted electrode | 50 – 150 microns | Spherical |
HDH process | Hydriding, dehydriding, crushing blended powders | 10 – 63 microns | Irregular, angular |
Consolidation of TiNb Alloy Powder
TiNb alloy powder can be converted into full-density components using various powder metallurgy consolidation techniques:
Hot Isostatic Pressing (HIP)
- encapsulated powder is HIPped at high temperature and pressure
Vacuum Sintering
- powder is compacted and sintered in vacuum furnace
Spark Plasma Sintering
- powder is simultaneously heated and compressed by pulsed DC current
Metal Injection Molding (MIM)
- powder is mixed with binder, molded, debinded and sintered
Additive Manufacturing
- powder bed fusion (SLM, EBM) or directed energy deposition (DED)
HIP and vacuum sintering can achieve close to full density while retaining fine microstructure. Additive manufacturing offers greater geometric freedom. The consolidation process can be optimized to achieve the desired properties.
Table 5: TiNb alloy powder consolidation techniques
Method | Description | Density | Microstructure | Geometry |
---|---|---|---|---|
HIP | High pressure, high temperature | Near full density | Fine | Simple shapes |
Vacuum sintering | Sintering in vacuum furnace | Near full density | Fine | Simple shapes |
Spark plasma sintering | Pulsed current and pressure | Full density | Ultrafine | Simple shapes |
Metal injection molding | Powder + binder molding | Near full density | Ultrafine | Complex shapes |
Additive manufacturing | Powder bed fusion or directed energy deposition | Near full density | Coarse | Complex shapes |
Specifications for TiNb Alloy Powder
TiNb alloy powder is available in various specifications tailored for different applications:
Compositions: Grades with 10% to 50% niobium content
Particle Size: 10 to 150 microns
Morphology: Spherical, irregular or blended
Production Method: Gas atomized, HDH, blended elemental
Purity: >99.5% titanium, >99.8% niobium
Oxygen Content: <2000 ppm
Flowability: Hall flow rate > 23 sec/50g
Apparent Density: ≥ 2.5 g/cc
Tap Density: ≥ 3.5 g/cc
Chemical composition, particle size distribution, morphology, flow rate and density are commonly specified properties. Custom alloys and powder specifications can be produced for specific applications.
Table 6: Typical specification of Ti-35Nb gas atomized powder
Parameter | Specification |
---|---|
Alloy composition | Ti-35Nb |
Particle size | 15 to 45 microns |
Morphology | Spherical |
Production method | Gas atomization |
Purity | Ti >99.5%, Nb >99.8% |
Oxygen content | <1500 ppm |
Flow rate | >38 sec/50g |
Apparent density | ≥ 2.7 g/cc |
Tap density | ≥ 4.2 g/cc |
Suppliers of TiNb Alloy Powder
Some leading global suppliers of titanium niobium alloy powder include:
- AP&C – titanium and niobium alloy powders
- Atlantic Equipment Engineers – spherical and angular powders
- TLS Technik – gas atomized TiNb alloys
- Metal Technology – blended elemental and prealloyed powders
- Sandvik Osprey – gas atomized spherical powders
- Carpenter Additive – customized alloy powders
TiNb alloys are also offered by suppliers of titanium and niobium metals. Both standardized alloys and custom compositions can be sourced from these powder producers.
Table 7: TiNb alloy powder suppliers
Company | Materials | Production Methods |
---|---|---|
AP&C | Ti, Nb, TiNb alloys | Gas atomization |
Atlantic Equipment Engineers | Ti, Nb, TiNb alloys | Gas atomization, blending |
TLS Technik | TiNb alloys | Gas atomization |
Metal Technology | TiNb alloys | Blended elemental, prealloyed |
Sandvik Osprey | TiNb alloys | Gas atomization |
Carpenter Additive | Custom TiNb alloys | Gas atomization |
Cost of TiNb Alloy Powder
TiNb alloy powder is more expensive than titanium or niobium powder alone. Cost depends on:
- Composition – higher Nb content increases cost
- Purity – cost increases for higher purity
- Particle size and distribution
- Production method – gas atomized powder costs more
- Order quantity – larger volumes have lower cost
Indicative pricing for TiNb alloy powder in small quantities:
- Ti-10Nb: $100 to $300 per kg
- Ti-35Nb: $200 to $500 per kg
- Ti-50Nb: $300 to $800 per kg
Pricing reduces significantly for bulk orders of hundreds of kilos or several tons.
Table 8: Indicative pricing of TiNb alloy powders
Alloy | Pricing ($/kg) |
---|---|
Ti-10Nb | $100 – $300 |
Ti-35Nb | $200 – $500 |
Ti-50Nb | $300 – $800 |
Handling and Storage of TiNb Alloy Powder
As a reactive metallic powder, some care is needed when handling TiNb alloy powder:
- Store in sealed containers in a dry, inert atmosphere to prevent oxidation and contamination
- Avoid contact with oxygen, moisture, oils, combustible materials
- Prevent accumulation of fine powders on surfaces or equipment
- Ground all conductive equipment used in handling
- Use spark-proof tools and minimize dust generation
- Wear gloves and respiratory protection when handling
- Use grounded ventilation systems and avoid dust clouds
- Keep away from heat, flames, sparks and other ignition sources
- Follow safety data sheet for proper PPE and precautions
If stored properly in a dry, inert atmosphere, TiNb alloy powder has a typical shelf life of 12 months. Improper storage conditions can lead to oxidation, loss of flowability, or ignition hazards.
Table 9: TiNb alloy powder handling guidelines
Parameter | Guidelines |
---|---|
Storage | Sealed containers, dry inert atmosphere |
Atmosphere | Avoid oxygen, moisture, oils, combustibles |
Equipment | Ground all conductive equipment |
Tools | Use non-sparking tools |
Ventilation | Grounded ventilation system |
PPE | Gloves, respiratory protection |
Precautions | Avoid heat, flames, sparks |
Shelf life | 12 months in inert atmosphere |
Safety Data Sheet for TiNb Alloy Powder
Like other reactive metal powders, some important safety precautions for TiNb alloy:
- Wear PPE – gloves, eye protection, mask/respirator
- Avoid inhalation of powders – use respiratory protection
- Avoid contact with skin and eyes
- Wash thoroughly after handling powder
- Avoid ignition sources, powders may be flammable
- Use proper grounding and ventilation
- Inert storage atmosphere to prevent oxidation
- Avoid spills and dust accumulation on surfaces
- Follow instructions on SDS and warning labels
First aid:
- Inhalation: Move to fresh air. Get medical help if needed.
- Skin contact: Wash with soap and water. Get help if irritation persists.
- Eye contact: Flush eyes with water for 15 minutes. Get medical attention.
- Ingestion: Drink water. Get medical assistance if discomfort occurs.
Always refer to SDS from supplier for complete health and safety information before handling and processing TiNb alloy powder.
Table 10: Key safety measures for TiNb alloy powder
Safety Item | Precautions |
---|---|
PPE | Gloves, goggles, N95 mask |
Inhalation | Use respiratory protection |
Skin contact | Wash affected area with soap and water |
Eye contact | Flush eyes with water for 15 minutes |
Ingestion | Drink water. Get medical help if needed. |
Ventilation | Use grounded ventilation hoods |
Grounding | Ground all equipment during handling |
Ignition | Avoid sparks, flames, heat sources |
Storage | Inert atmosphere away from flammable materials |
Quality Inspection of TiNb Alloy Powder
To ensure TiNb alloy powder meets specifications, various quality checks are performed:
- Chemical analysis – ICP, GDMS or LECO analysis to verify composition and purity
- Particle size analysis – laser diffraction or sieve analysis for size distribution
- Morphology – SEM imaging to check particle shape and surface topology
- Flow rate – Hall flow meter test for powder flowability
- Density – apparent density and tap density measurements
- Oxygen/nitrogen – inert gas fusion analysis for interstitial impurities
- Phase identification – XRD analysis to determine phases present
Powder properties are tested on each batch to quality standards like ASTM B939, ASTM F3049, EN 10204 3.1. Powder can be blended between lots to achieve uniformity.
Table 11: Testing methods for TiNb alloy powder
Test | Method | Standard |
---|---|---|
Composition | ICP, GDMS, LECO | ASTM E1479, ASTM E2330 |
Particle size distribution | Laser diffraction, sieving | ASTM B822 |
Morphology | SEM imaging | ASTM B822 |
Flow rate | Hall flow meter | ASTM B213 |
Density | Scott volumeter | ASTM B212 |
Oxygen/Nitrogen | Inert gas fusion | ASTM E1019 |
Phase analysis | X-ray diffraction | ASTM E1876 |
Medical Applications of TiNb Alloy
Due to their biocompatibility, high strength and low modulus, TiNb alloys are widely used for medical implants and devices:
Orthopedic Implants
- Knee and hip replacements
- Bone plates, screws
- Spinal fixation devices
- Dental implants and bridges
TiNb alloys like Ti-35Nb and Ti-45Nb match the elastic modulus of human bone while providing high fatigue strength. This reduces stress shielding compared to stiffer titanium alloys.
Cardiovascular Devices
- Stents
- Pacemaker casings
- Guidewires
- Surgical instruments
The corrosion resistance, non-toxicity and non-magnetism of TiNb alloys make them suitable for devices that contact blood and tissues.
TiNb Alloy Grades for Medical Use
- Ti-10Nb to Ti-50Nb
- Ti-Nb-Zr, Ti-Nb-Ta for adjusted properties
- ISO 5832-11 and ASTM F2066 standards
Lower modulus Ti-35Nb and Ti-45Nb are commonly used. Higher Nb strengthens but increases modulus. Small Zr/Ta additions further tailor properties.
Advantages of TiNb Alloys for Biomedical Use
- Excellent biocompatibility and osseointegration
- High strength and fatigue resistance
- Low modulus close to bone
- Non-toxic, non-allergenic
- Corrosion resistant
- Non-magnetic
TiNb alloys provide the best combination of strength, biocompatibility, corrosion resistance and elastic modulus for implants.
Challenges of TiNb Alloy Medical Components
- Difficult machining and fabrication
- Costlier than Ti-6Al-4V alloy
- Requires rigorous quality control and testing
- Longer-term clinical data still evolving
Being relatively new for medical use, manufacturing and licensing of TiNb components can be more complex. But their advantages outweigh short-term challenges.
Automotive Uses of TiNb Alloy
The high strength, temperature resistance and fatigue life of TiNb alloys make them attractive for automotive parts:
Valve Springs
- Higher strength allows lower spring mass
- Reduces valve float at high RPM
- Allows higher power output
Engine Valves
- Withstands high temperature exhaust gases
- Resists wear and deformation
- Lightweight
Connecting Rods
- High strength-to-weight ratio
- Reduces reciprocating mass
- Allows higher RPM and power
Turbocharger Rotors
- Maintains strength at high temperatures
- Resists creep deformation
- Thermal shock resistance
- Low density
Motor Racing Components
- Lightweight suspension, chassis parts
- Superior fatigue life
Reduced mass and inertia combined with temperature and fatigue resistance lead to higher engine performance and efficiency.
Challenges of TiNb Alloys for Automotive
- High cost compared to steel alloys
- Processing difficulties with powder metallurgy
- Limited suppliers and manufacturing experience
- Uncertain cost-benefit ratio
The benefits may justify premium pricing for high-end vehicles and motorsports initially. Broader adoption depends on TiNb powder producers driving down costs.
Aerospace Applications of TiNb Alloys
TiNb alloys compete with nickel superalloys for aircraft engine and airframe applications needing strength at low temperatures:
Engine Components
- Turbine blades, discs, casings
- Compressor blades
- Shafts, fasteners
- Thrust reversers
Structural Parts
- Landing gear
- Wings, ribs, stringers
- Fuselage frames
- Hydraulic tubing
Benefits
- 30-50% lower density than Ni superalloys
- Saves weight
- Similar strength and creep resistance
- Withstands high stresses and temperatures
Challenges
- Higher costs than titanium alloys currently
- Processing difficulties compared to wrought alloys
- Limited production experience and availability
- Property data still evolving
The aerospace industry is conservative, so extensive testing and qualification programs are needed to prove viability and establish supply chains before adopting new alloys like TiNb.
Other Applications of TiNb Alloys
In addition to medical, automotive and aerospace uses, TiNb alloys are also suitable for:
- Marine – Propellers, pump shafts, fittings
- Chemical – Heat exchangers, condensers, piping
- Sporting goods – Golf clubs, bicycle frames, rackets
- Power generation – Steam and gas turbine components
- Electronics – Sputtering targets, capacitors
- Jewelry – Watches, rings, piercings
- Oil and gas – Downhole tools, valves, pumps
The corrosion resistance, biocompatibility and electrical properties expand the utility of TiNb alloys across diverse industries.
Continuing research and development will uncover new applications as manufacturing experience with TiNb alloy powder grows. Their unique balance of properties will enable designs not feasible with other materials.
Future Outlook for TiNb Alloys
- Expanding medical use driven by aging population and need for better implants
- Adoption in aerospace accelerating to reduce weight
- Automotive use escalating due to high performance needs
- Oil and gas interest rising for deep sea exploration hardware
- Manufacturing via powder metallurgy and AM techniques improving
- New grades being developed to tailor properties
- Supply chain expanding as producers add TiNb alloy capacity
- Costs declining with higher production volumes
- Broader awareness and acceptance across industries
The future looks bright for TiNb alloys to become a new advanced material that displaces traditional alloys in the most demanding applications. Their success hinges on continued investments to improve affordability.
Key Takeaways on TiNb Alloy Powder
- TiNb alloys offer superior mechanical properties compared to titanium
- Stronger, stiffer and higher hardness than pure titanium
- Lower density and higher strength than nickel/steel alloys
- Outstanding high temperature performance
- Resists creep, fatigue and corrosion in harsh environments
- Excellent biocompatibility for medical implants
- Adjustable properties by changing Ti/Nb ratio
- Produced via blended elemental or prealloyed powder metallurgy
- Powder can be consolidated using AM, HIP, MIM or sintering
- Leading applications in aerospace, automotive, biomedical industries
- Future prospects positive driven by lightweighting and high performance needs
TiNb alloys represent an advanced metallic material breakthrough enabled by powder metallurgy techniques. As manufacturing costs decline, they are poised to disrupt several industries demanding lightweight, strong and temperature resistant alloys.
Frequently Asked Questions on TiNb Alloy Powder
Here are answers to some common questions about TiNb alloy powder:
Q: What are the main advantages of TiNb alloys over titanium alloys?
TiNb alloys have higher strength, stiffness, hardness, wear resistance, and high temperature performance compared to titanium alloys. They also have lower density than nickel and steel alloys.
Q: Which industries use TiNb alloys?
The main applications are in aerospace, automotive, biomedical, chemical, marine, and power generation industries. Usage is expanding as powder metallurgy production increases.
Q: What is the typical price range of TiNb alloy powder?
Pricing ranges from around $100/kg for Ti-10Nb to $300-800/kg for Ti-50Nb depending on composition, quality and order volume. Prices are declining as production expands.
Q: What particle size is common for TiNb alloy powder?
Particle sizes from 10 to 150 microns are typical. Fine powders 10-45 microns are preferred for additive manufacturing. Coarser up to 150 micron powders are used for press and sinter applications.
Q: How are TiNb alloy powders produced?
Main production methods include gas atomization, plasma spheroidization, hydride-dehydride process, and blended elemental. Gas atomized and plasma spheroidized powders have spherical morphology preferred for AM.
Q: What standards apply to TiNb alloys in medical use?
ISO 5832-11 and ASTM F2066 standards cover the composition, mechanical properties, quality control testing and processing requirements for surgical implant grade TiNb alloys.
Q: Can TiNb alloys be 3D printed?
Yes, TiNb alloy powders are compatible with laser powder bed fusion, electron beam powder bed fusion and directed energy deposition 3D printing processes. Parameters need optimization for good density and properties.
Q: Are there health risks associated with TiNb powders?
Like other metal powders, certain precautions are needed when handling TiNb powders to minimize dust explosion risks and inhalation exposures. But the alloy itself is highly biocompatible.
Q: What is the outlook for adoption of TiNb alloys?
The future looks promising with expanding use of TiNb alloys driven by the need for lightweight, strong and heat resistant materials. Adoption will accelerate as powder metallurgy production costs decrease.
This covers the key questions engineers have regarding specification, processing, applications and the prospects of TiNb alloy powder as an emerging advanced material. Reach out for any other specific queries.
Get Latest Price
About Met3DP
Product Category
HOT SALE
CONTACT US
Any questions? Send us message now! We’ll serve your request with a whole team after receiving your message.
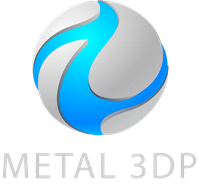
Metal Powders for 3D Printing and Additive Manufacturing
COMPANY
PRODUCT
cONTACT INFO
- Qingdao City, Shandong, China
- [email protected]
- [email protected]
- +86 19116340731