The Atomization Process
Table of Contents
Imagine a sculptor, meticulously chipping away at a massive block of stone, transforming it into a delicate figurine. The atomization process operates on a similar principle, but instead of chisels and stone, it utilizes high-powered jets to break down molten metals or liquids into minuscule, highly-functional particles.
This article delves deep into the fascinating world of atomization, exploring its intricacies, the specific types of metal powders it produces, and its diverse applications across various industries.
An Overview of Atomization
At its core, atomization is a process that transforms a liquid – typically molten metal – into a fine mist or powder. This is achieved by subjecting the liquid to a high-pressure stream of gas or water, which disrupts its flow and creates a multitude of tiny droplets. These droplets rapidly solidify as they fall through a collection chamber, resulting in a collection of highly-coveted metal powders with unique properties.
There are two primary methods for atomization:
- Gas Atomization: In this method, an inert gas, like nitrogen or argon, is used to break down the molten metal. This technique produces highly spherical powders with excellent flow characteristics and minimal oxidation.
- Water Atomization: Here, a high-pressure water jet disrupts the molten metal stream. This method is generally more cost-effective but results in less spherical and potentially more oxidized powders compared to gas atomization.
The choice between these methods depends on the desired powder characteristics, material type, and cost considerations.
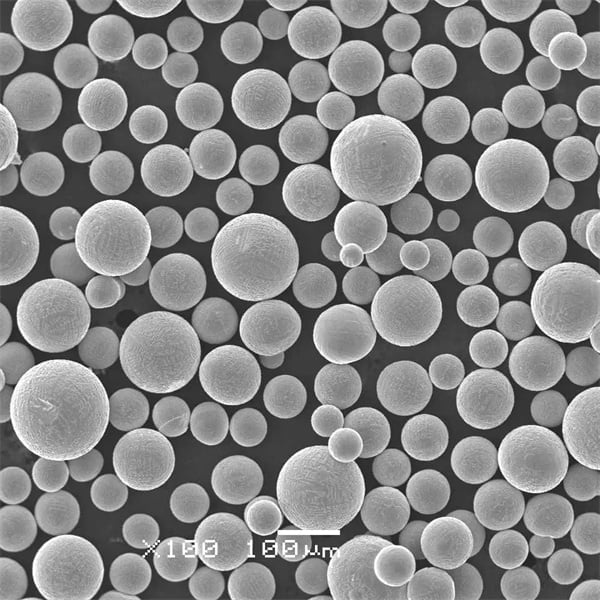
Exploring Different Metal Powders
The atomization process unlocks a treasure trove of metal powders, each possessing a distinct set of properties and applications. Let’s delve into ten such fascinating metal powders:
1. Stainless Steel Powders:
- Composition: Primarily iron, chromium, nickel, and varying amounts of other elements like molybdenum and nitrogen.
- Properties: Excellent corrosion resistance, high strength, good formability.
- Applications: Additive manufacturing (3D printing) of complex components, injection molding for intricate parts, thermal spraying for wear and corrosion resistance.
2. Nickel-Based Superalloy Powders:
- Composition: Nickel as a base element, combined with chromium, cobalt, molybdenum, and other elements depending on the specific alloy.
- Properties: Exceptional high-temperature strength, resistance to oxidation and creep (deformation under stress at high temperatures).
- Applications: Gas turbine engine components, aerospace parts, heat exchangers operating in extreme environments.
3. Titanium Powders:
- Composition: Primarily titanium, with small amounts of oxygen, nitrogen, and other elements depending on the grade.
- Properties: High strength-to-weight ratio, excellent biocompatibility, corrosion resistance.
- Applications: Additive manufacturing of lightweight and strong aerospace parts, biomedical implants for superior bone integration.
4. Aluminum Powders:
- Composition: Primarily aluminum, with varying levels of silicon, iron, and other elements depending on the alloy.
- Properties: Lightweight, good electrical conductivity, highly recyclable.
- Applications: Additive manufacturing for rapid prototyping and lightweight components, pyrotechnics (for producing sparks and smoke effects).
5. Copper Powders:
- Composition: Primarily copper, with potential trace amounts of oxygen and other elements.
- Properties: Excellent electrical and thermal conductivity, good machinability.
- Applications: Electrical contacts and connectors, heat sinks for managing thermal transfer, additive manufacturing for conductive components.
6. Iron Powders:
- Composition: Primarily iron, with varying levels of carbon, oxygen, and other elements depending on the type (e.g., atomized iron powder, carbonyl iron powder).
- Properties: Magnetic properties (varies depending on type), good machinability, high density.
- Applications: Soft magnetic components for transformers and inductors, metal injection molding for complex shapes, friction materials for brakes and clutches.
7. Cobalt Powders:
- Composition: Primarily cobalt, with potential trace amounts of iron, nickel, and other elements.
- Properties: High magnetic strength, wear resistance, good hardness.
- Applications: Cutting tools, permanent magnets, hardfacing for wear resistance on components.
8. Tungsten Powders:
- Composition: Primarily tungsten, with potential trace amounts of oxygen, carbon, and other elements.
- Properties: Extremely high melting point, excellent density, good wear resistance.
- Applications: Tungsten inert gas (TIG) welding electrodes, filaments for incandescent lamps, armor-piercing ammunition.
9. Molybdenum Powders:
- Composition: Primarily molybdenum, with potential trace amounts of oxygen, carbon, and other elements.
An Overview of Atomization
Beyond the core methods, atomization can be further categorized based on the pressure used to break down the liquid:
- High-Pressure Gas Atomization (HGPA): This method utilizes extremely high gas pressures (up to 30 MPa or 4,351 psi) to produce exceptionally fine powders with a narrow size distribution. HGPA powders are ideal for applications demanding high precision and consistent properties.
- Low-Pressure Gas Atomization (LGPA): Here, lower gas pressures (typically below 10 MPa or 1,450 psi) are employed. This results in coarser powders compared to HGPA but offers a more cost-effective approach. LGPA powders are well-suited for applications where precise particle size is less critical.
Additional Factors Influencing the Atomization Process:
- Melt Temperature: The temperature at which the metal is atomized significantly impacts the final powder characteristics. Higher temperatures can lead to larger and more spherical particles, while lower temperatures might yield smaller and less spherical powders.
- Atomization Gas Flow Rate: The rate at which the gas is introduced into the molten metal stream affects the size and distribution of the resulting particles. Higher flow rates generally produce finer powders.
Beyond Metals: Atomization for Diverse Materials
The power of atomization extends beyond metals. This versatile process can be used to create powders from a wide range of materials, including:
- Ceramics: Alumina, zirconia, and silicon carbide powders are produced for applications like wear-resistant components and high-performance cutting tools.
- Plastics: Polymers like nylon and polyethylene can be atomized to create fine powders for use in additive manufacturing, coatings, and composite materials.
- Food and Pharmaceuticals: Foodstuffs like milk and coffee can be atomized for instant applications, while pharmaceuticals leverage this process to create controlled-release drug delivery systems.
Advantages of the Atomization Process
The atomization process offers a multitude of advantages, making it a cornerstone in various industries:
- Production of High-Purity Powders: Atomization allows for the creation of powders with minimal contamination, ensuring consistent and predictable material properties.
- Precise Control over Powder Morphology: By adjusting various parameters, the size, shape, and distribution of the powder particles can be precisely controlled, catering to specific application requirements.
- Enhanced Material Properties: The rapid solidification inherent in atomization can lead to unique microstructures within the powder particles, improving properties like strength, ductility, and corrosion resistance.
- Tailored Powders for Diverse Applications: The ability to atomize a wide range of materials creates a vast library of powders suitable for countless applications.
- Efficient and Scalable Process: Modern atomization techniques are efficient and can be scaled up for high-volume production, making them suitable for industrial applications.
Disadvantages of Atomization
While a powerful tool, atomization does come with certain drawbacks:
- High Energy Consumption: The process requires significant energy to generate the high pressures or high-velocity jets needed for atomization.
- Cost Considerations: Setting up and operating an atomization plant can be expensive, impacting the final cost of the produced powders.
- Powder Oxidation: During atomization, particularly with water atomization, there’s a risk of the powder particles oxidizing, which can affect their properties.
- Safety Concerns: The process can involve handling high-temperature molten metals and high-pressure gases, necessitating strict safety protocols.
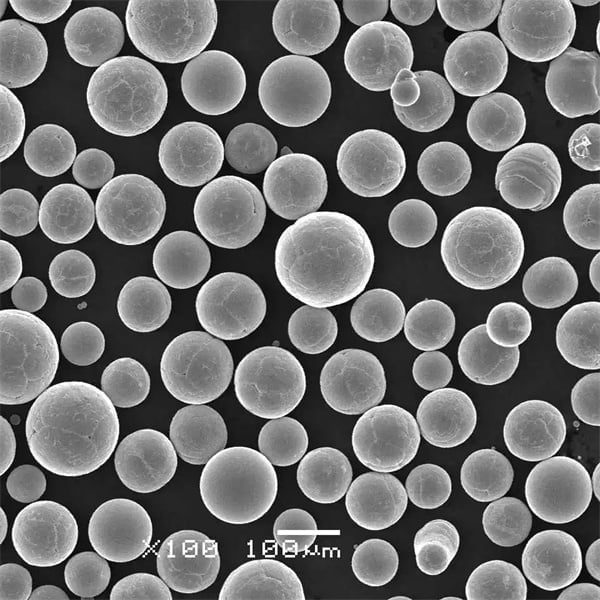
A Comparison of Gas and Water Atomization
When choosing between gas and water atomization, several key factors come into play:
Powder Characteristics:
- Sphericity: Gas atomization generally produces more spherical powders compared to water atomization. Spherical particles offer better flowability, packing density, and are more suitable for additive manufacturing processes.
- Oxidation: Water atomization can introduce more oxygen into the powder particles compared to gas atomization. This might be a concern for applications requiring high corrosion resistance.
Cost Considerations:
- Initial Investment: Gas atomization equipment typically requires a higher initial investment compared to water atomization setups.
- Operational Costs: The cost of the atomization gas (e.g., argon, nitrogen) can be a significant factor in gas atomization, while water atomization has lower operational costs associated with the atomization medium.
Applications:
- High-Performance Applications: When precise powder morphology and minimal oxidation are crucial (e.g., additive manufacturing of aerospace components), gas atomization is often the preferred choice.
- Cost-Sensitive Applications: For less critical applications where cost is a primary concern (e.g., production of metal injection molding feedstock), water atomization might be a more viable option.
- Environmental Impact: The high energy consumption associated with atomization can contribute to greenhouse gas emissions. Additionally, the disposal of wastewater generated during water atomization needs to be carefully managed to minimize environmental impact.
Mitigating the Drawbacks: Strategies for Optimization
Despite the limitations, several strategies can be employed to optimize the atomization process and address its potential drawbacks:
- Energy-Efficient Technologies: Advancements in atomization technology are leading to the development of more energy-efficient processes, such as ultrasonic atomization, which utilizes sound waves for atomization.
- Material Recycling: Recycling of metal scraps and powders back into the atomization process can reduce the environmental impact and production costs.
- Closed-Loop Water Systems: Implementing closed-loop water systems in water atomization can significantly reduce water consumption and wastewater generation.
- Strict Safety Measures: Enforcing stringent safety protocols during atomization, including proper ventilation, personal protective equipment, and operator training, can minimize safety risks.
the Applications of atomization process
Atomized powders find application across a vast spectrum of industries, playing a vital role in shaping our world:
Additive Manufacturing (3D Printing): Metal powders like stainless steel, titanium, and nickel superalloys are the building blocks for creating complex and high-performance components using 3D printing technologies.
Metal Injection Molding (MIM): This process utilizes atomized powders to create intricate metal parts through a combination of molding and sintering. MIM is suitable for mass production of small, complex components.
Thermal Spraying: Atomized powders are used to coat surfaces with a layer of metal, ceramic, or other materials. Thermal spraying enhances properties like wear resistance, corrosion resistance, and thermal insulation.
Battery Technologies: Nickel and lithium powders are crucial components in the production of high-performance batteries for electric vehicles and electronic devices.
Catalysts: Finely atomized powders with high surface areas are used as catalysts in various chemical reactions, accelerating reaction rates and improving process efficiency.
Pharmaceuticals: Atomization allows for the creation of drug particles with controlled size and release profiles, enabling targeted drug delivery within the body.
Food and Agriculture: Instant coffee, powdered milk, and fertilizers often utilize atomized ingredients for improved shelf life, functionality, and controlled release properties.
The Evolving Landscape of Atomization
The future of atomization is brimming with exciting possibilities:
- Nanoparticle Atomization: The ability to produce even finer, nanoparticle-sized powders using advanced atomization techniques will open doors for novel applications in nanotechnology and medicine.
- Multi-Material Atomization: Developments in co-atomization techniques will enable the creation of powders with a blend of different materials, leading to the development of composite materials with unique properties.
- Sustainable Atomization: Research into more energy-efficient atomization processes and increased utilization of recycled materials will contribute to a more sustainable atomization future.
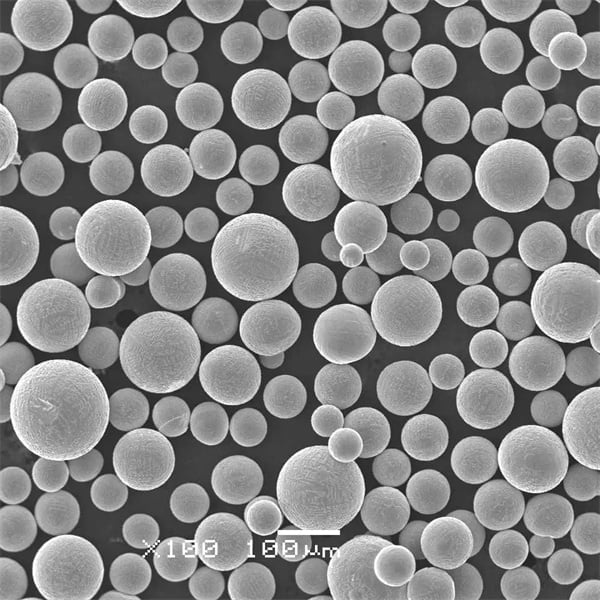
FAQ
Q: What is the difference between atomization and pulverization?
A: While both processes create smaller particles, atomization typically deals with liquids, transforming them into fine powders. Pulverization, on the other hand, focuses on breaking down solid materials into smaller pieces.
Q: Can any liquid be atomized?
A: Atomization is most commonly used for metals and other materials that can be melted. However, with the right techniques, some viscous liquids (like certain polymers) can also be atomized.
Q: How is the size of the atomized powder particles controlled?
A: The size of the powder particles is influenced by several factors, including the pressure of the atomization gas or water jet, the melt temperature, and the nozzle design. By adjusting these parameters, the desired particle size distribution can be achieved.
Q: What safety precautions are necessary during atomization?
A: Atomization processes involve high temperatures and potentially hazardous materials. Therefore, proper ventilation, personal protective equipment (PPE) for operators, and adherence to safety protocols are essential to minimize risks.
Q: What is the future of atomization?
A: The future of atomization is promising, with advancements in technology leading to the development of more efficient, sustainable, and precise atomization processes. This will pave the way for the creation of novel materials and applications across various industries.
Share On
MET3DP Technology Co., LTD is a leading provider of additive manufacturing solutions headquartered in Qingdao, China. Our company specializes in 3D printing equipment and high-performance metal powders for industrial applications.
Inquiry to get best price and customized Solution for your business!
Related Articles
About Met3DP
Recent Update
Our Product
CONTACT US
Any questions? Send us message now! We’ll serve your request with a whole team after receiving your message.
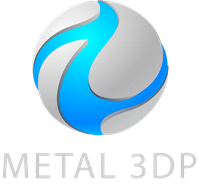
Metal Powders for 3D Printing and Additive Manufacturing