The application of Binder Jetting
Table of Contents
Binder jetting, the 3D printing technology that’s like a high-tech inkjet printer for metal, sand, and more, is revolutionizing manufacturing. Imagine building complex objects layer by layer, with unparalleled speed and versatility. That’s the magic of binder jetting, and its applications are as diverse as your imagination. Buckle up, because we’re diving deep into this fascinating technology and exploring how it’s transforming industries.
the Core of Binder Jetting
At the heart of binder jetting lies a dance between two key players: powder and binder. The printer bed is filled with a fine layer of powdered material, which can be metal, ceramic, sand, or even plastic. Then, an inkjet printhead, similar to the one in your home printer, comes into play. But instead of ink, it jets a binding agent onto the powder, selectively gluing particles together according to the digital blueprint. Layer by layer, the object takes shape, held together by the binder until it’s ready for post-processing, which can involve infiltration, sintering, or other techniques depending on the material.
Here’s where things get exciting: the variety of powders used in binder jetting opens doors to a vast array of applications. Let’s delve into the world of metal powders, a realm brimming with possibilities:
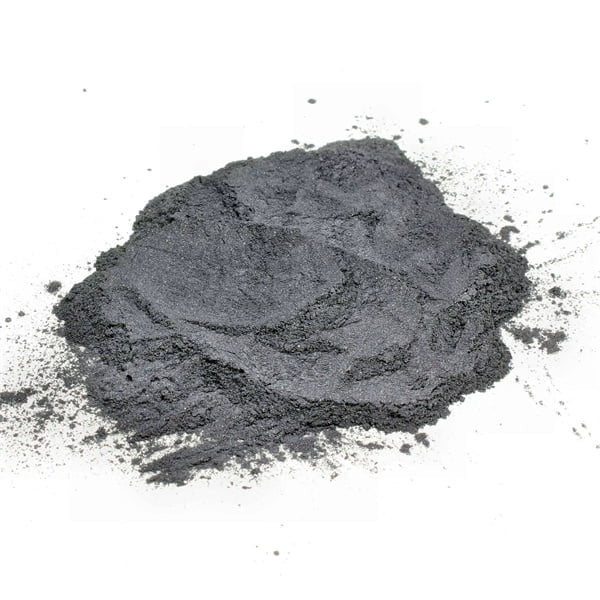
types of Metal Marvels suitbale for Binder Jetting
Binder jetting isn’t limited to just a few metals. The list of compatible powders is ever-growing, offering engineers a treasure trove of options to create parts with specific properties:
Metal Powder | Description | Properties | Applications |
---|---|---|---|
Stainless Steel 316L | The workhorse of metal powders, offering excellent corrosion resistance and biocompatibility. | Strong, durable, resists rust and biocompatible | Medical devices, aerospace components, chemical processing equipment |
Inconel 625 | A high-performance nickel-chromium superalloy known for its exceptional resistance to heat, corrosion, and oxidation. | High-temperature strength, oxidation resistance | Turbine blades, heat exchangers, rocket engine components |
Titanium 6Al-4V | An industry favorite for its light weight, high strength, and biocompatibility. | Strong, lightweight, biocompatible | Aerospace components, medical implants, sporting goods |
Aluminum (various alloys) | Lightweight and readily available, offering good strength-to-weight ratio. | Lightweight, good machinability | Automotive parts, heat sinks, electronics enclosures |
Copper | An excellent conductor of heat and electricity. | High thermal and electrical conductivity | Heat exchangers, electrical components, radiators |
Tool Steel | Formulated for creating durable tools and wear-resistant parts. | High hardness, wear resistance | Cutting tools, dies, molds |
Maraging Steel | A family of high-strength, low-alloy steels known for their exceptional toughness. | High strength, good toughness | Aerospace components, defense applications |
Cobalt Chrome | A biocompatible alloy offering excellent wear resistance. | Biocompatible, wear-resistant | Joint replacements, dental implants |
Nickel Alloys | A diverse group of alloys offering a range of properties, including high-temperature strength and corrosion resistance. | Tailored properties for specific needs | Chemical processing equipment, oil and gas components |
Precious Metals | Including gold, silver, and platinum, these offer unique properties like high conductivity and biocompatibility. | High electrical/thermal conductivity, biocompatibility (for specific metals) | Jewelry, electronics components, medical devices (limited applications) |
Table note: This table provides a brief overview of some popular metal powders used in binder jetting. Specific properties and applications can vary depending on the exact alloy composition and processing parameters.
Remember, this is just a glimpse into the ever-expanding world of metal powders for binder jetting. New materials are constantly being developed, pushing the boundaries of what’s possible.
the application of Binder Jetting
Now that we’ve met the key players, let’s explore the incredible applications binder jetting is enabling across industries:
- Automotive Components: Imagine lighter, stronger car parts produced at high volumes. Binder jetting is making this a reality for components like pistons, brake calipers, and even engine blocks. The technology’s ability to handle complex geometries allows for intricate internal structures, leading to weight reduction and improved performance.
- Aircraft Components: The aerospace industry demands parts that are both lightweight and incredibly strong. Binder jetting steps up to the challenge, producing intricate components like brackets, housings, and even engine parts using high performance metals like titanium and Inconel. Compared to traditional manufacturing methods, binder jetting offers faster turnaround times and the ability to create complex internal structures that can optimize weight and fuel efficiency.
- Medical Devices: Binder jetting’s biocompatible metal powders like stainless steel 316L and cobalt chrome are revolutionizing medical device production. The technology allows for the creation of customized implants like knee replacements and spinal cages, perfectly tailored to individual patients. Additionally, binder jetting can be used to manufacture intricate surgical instruments and medical prototypes.
- Consumer Electronics Products: From customized heat sinks for laptops to intricate housings for mobile devices, binder jetting is finding its way into the consumer electronics world. The technology’s ability to produce complex shapes with good dimensional accuracy makes it ideal for creating lightweight and aesthetically pleasing electronics components.
Binder Jetting’s Versatility
While metal powders are a major focus, binder jetting isn’t limited to them. Here’s a peek into the broader world of materials this technology can handle:
- Sand: Binder jetting with sand is a game-changer for the foundry industry. It allows for the creation of complex and intricate sand molds and cores, used for casting metal parts. Compared to traditional methods, binder jetting offers higher accuracy, reduced waste, and the ability to create intricate internal features.
- Ceramics: From biocompatible implants to heat-resistant components, binder jetting is making waves in the ceramics industry. The technology allows for the creation of complex ceramic shapes with good surface quality, ideal for a variety of applications.
- Plastics: Binder jetting can be used for prototyping and even limited-run production of plastic parts. While not as widely used for final parts compared to other 3D printing technologies like FDM, binder jetting offers advantages like high resolution and the ability to use a wider range of plastic materials.
The Future of Binder Jetting
Binder jetting is still evolving, but its potential is undeniable. Here are some exciting trends shaping the future of this technology:
- Multi-material Printing: Imagine a single object with different materials seamlessly integrated. Binder jetting is on the cusp of achieving this, allowing for the creation of parts with varying properties within a single build.
- Faster Printing Speeds: Researchers are constantly pushing the boundaries of printing speed in binder jetting. This will further increase the technology’s competitiveness with traditional manufacturing methods, especially for high-volume production.
- Improved Material Properties: As research progresses, we can expect to see new metal powders and other materials specifically developed for binder jetting, offering even better properties and performance.
- Wider Adoption: With its growing capabilities and decreasing costs, binder jetting is poised for wider adoption across various industries. From automotive giants to medical device manufacturers, more companies will leverage this technology to create innovative products.
pros and cons of Binder Jetting
Binder jetting boasts an impressive list of advantages, but it’s important to consider its limitations as well:
Advantages:
- Speed: Binder jetting can be significantly faster than other 3D printing technologies, especially for larger objects.
- Cost-Effectiveness: For high-volume production of complex metal parts, binder jetting can be more cost-effective than traditional methods like machining.
- Design Freedom: Binder jetting allows for the creation of intricate geometries and internal features, previously impossible with traditional manufacturing.
- Material Versatility: The technology can handle a wide range of metal powders, ceramics, and even some plastics.
Limitations:
- Post-Processing: Binder jetting parts often require additional post-processing steps like sintering or infiltration, which can add time and complexity to the process.
- Material Properties: While properties are improving, binder jetting parts may not always achieve the same mechanical strength as parts produced with traditional methods.
- Surface Finish: The surface finish of binder jetting parts can be rougher compared to some other 3D printing technologies.
Making the Choice: Binder Jetting vs. Other Additive Manufacturing Methods
When choosing an additive manufacturing method, understanding the strengths and weaknesses of each technology is crucial. Here’s a quick comparison of binder jetting with some of its competitors:
- FDM (Fused Deposition Modeling): FDM is a more established technology known for its affordability and wide range of filament materials. However, FDM parts are generally weaker and have a lower resolution compared to binder jetting.
- SLS (Selective Laser Sintering): However, SLS is typically slower and more expensive compared to binder jetting.
- Electron Beam Melting (EBM): EBM is a high-end technology that produces very strong metal parts. However, it’s limited to a few materials and is significantly more expensive than binder jetting.
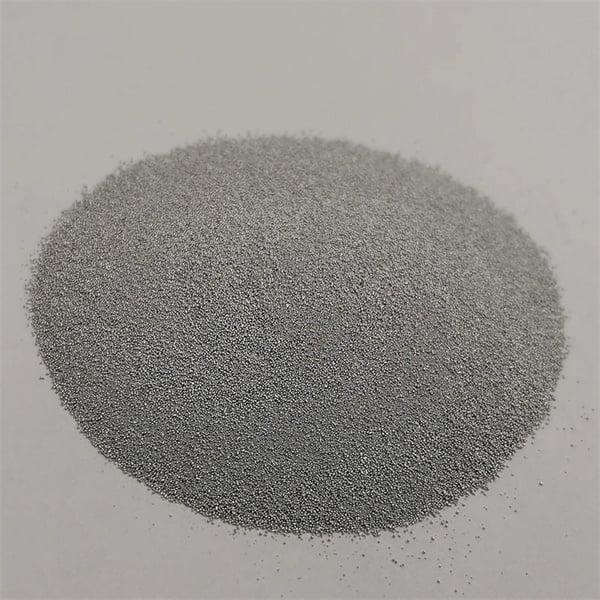
FAQs
Here are some frequently asked questions about binder jetting to quench your thirst for knowledge:
Question | Answer |
---|---|
What is the difference between binder jetting and inkjet printing? | While both technologies use a jetting process, binder jetting uses a binding agent to adhere powder particles together, while inkjet printing deposits ink onto a surface to create an image. |
Is binder jetting safe? | Binder jetting itself is not inherently dangerous. However, as with any industrial process, safety precautions should be taken when handling powders and using the machinery. |
What is the environmental impact of binder jetting? | Binder jetting can offer some environmental benefits compared to traditional manufacturing methods. For example, it can reduce waste material and energy consumption. However, the environmental impact also depends on the specific materials and processes used. |
What are the future applications of binder jetting? | The future of binder jetting is bright! We can expect to see this technology used in a wider range of industries, from aerospace and automotive to healthcare and consumer electronics. Advancements in multi-material printing and faster printing speeds will further unlock its potential. |
Share On
MET3DP Technology Co., LTD is a leading provider of additive manufacturing solutions headquartered in Qingdao, China. Our company specializes in 3D printing equipment and high-performance metal powders for industrial applications.
Inquiry to get best price and customized Solution for your business!
Related Articles
About Met3DP
Recent Update
Our Product
CONTACT US
Any questions? Send us message now! We’ll serve your request with a whole team after receiving your message.
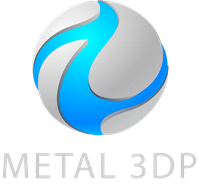
Metal Powders for 3D Printing and Additive Manufacturing