centrifugal atomization process
Table of Contents
Imagine turning a scorching river of molten metal into a cloud of perfectly round, ultra-fine particles. That’s the magic of centrifugal atomization, a rapid solidification technique that’s been around for decades, silently shaping the world around us. But how exactly does it work? And what kind of incredible materials can it produce? Buckle up, because we’re diving deep into the fascinating world of centrifugal atomization!
Process Principle of Centrifugal Atomization Process
At the heart of this process lies a high-speed rotating disk. Think of it as a supercharged potter’s wheel. The molten metal, heated to extremely high temperatures, is meticulously fed onto this rapidly spinning disc. As the metal hits the disc, a thin film forms due to the centrifugal force – the same force that keeps water in a bucket when you spin it. But this isn’t your average water droplet situation. The centrifugal force acts like an invisible hand, tearing the molten metal film into tiny droplets. These droplets, flung outwards by the relentless spin, rapidly solidify in mid-air due to their small size and exposure to a controlled atmosphere (often inert gases like argon). The result? A cascade of perfectly round, super-fine metal powders with unique properties.
Process Characteristics of Centrifugal Atomization Process
- Rapid Solidification: The key advantage of centrifugal atomization lies in its incredibly fast cooling rates. As the metal droplets are flung outwards, they solidify in a matter of milliseconds. This rapid solidification creates a unique microstructure within the particles, often resulting in enhanced strength and improved properties compared to traditional methods.
- Particle Size Control: By adjusting the rotation speed of the disc, the flow rate of the molten metal, and even the design of the feeding nozzle, manufacturers can precisely control the size and distribution of the resulting metal powders. This fine-tuned control allows for the creation of powders perfectly suited for specific applications.
- Scalability: Centrifugal atomization can be scaled up for large-scale production, making it a commercially viable option for various industries.
Here’s a table summarizing the key characteristics of centrifugal atomization:
Characteristic | Description |
---|---|
Rapid Solidification | Ultra-fast cooling rates create unique microstructures |
Particle Size Control | Precise control over powder size and distribution |
Scalability | Suitable for both small and large-scale production |
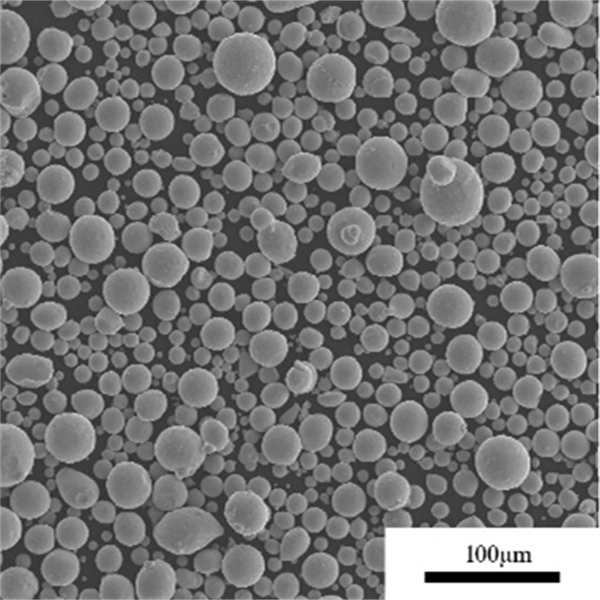
Metal Powders Produced by Centrifugal Atomization
Centrifugal atomization breathes life into a vast array of metal powders, each with its own set of properties and applications. Let’s explore some of the most common and fascinating ones:
- Stainless Steel Powders: Stainless steel’s resistance to corrosion makes it a popular choice in various industries. Centrifugal atomization produces spherical stainless steel powders perfect for Additive Manufacturing (AM), also known as 3D printing. These powders offer excellent flowability for smooth printing processes and contribute to the creation of strong, corrosion-resistant components.
- Nickel-Based Superalloy Powders: Imagine materials that can withstand extreme temperatures and harsh environments. Enter nickel-based superalloys. These high-performance alloys are used in jet engine components, rocket engines, and gas turbines. Centrifugal atomization produces these superalloy powders with exceptional high-temperature strength and creep resistance, making them crucial for pushing the boundaries of aerospace and power generation technologies.
- Aluminum Powders: Lightweight and versatile, aluminum powders find applications in everything from automotive components to food packaging. Centrifugal atomization produces spherical aluminum powders known for their excellent packing density and flowability. This translates to better performance in metal injection molding (MIM) and other powder metallurgy processes.
- Titanium Powders: Renowned for its high strength-to-weight ratio and biocompatibility, titanium is a game-changer in medical implants and aerospace applications. Centrifugal atomization produces near-spherical titanium powders with a clean and consistent surface. These powders are crucial for creating lightweight, high-strength implants and components for the aerospace industry.
- Copper Powders: A highly conductive metal, copper finds applications in electrical components and heat sinks. Centrifugal atomization produces spherical copper powders with excellent electrical conductivity and thermal properties. These powders are ideal for creating high-performance electrical components and heat exchangers.
- Cobalt Powders: Cobalt plays a vital role in magnets and cutting tools. Centrifugal atomization produces fine cobalt powders with a high degree of purity and a uniform size distribution. These powders contribute to the creation of strong magnets and wear-resistant cutting tools.
- Tungsten Powders: Incredibly dense and heat-resistant, tungsten finds applications in armor plating, welding electrodes, and heat sink materials. Centrifugal atomization produces spherical tungsten powders with a high melting point and excellent mechanical properties. These powders are crucial for creating high-performance armor, welding electrodes, and heat sinks.
- Iron Powders: Iron, the workhorse of the metalworking world, finds applications in everything from construction materials to automotive components. Centrifugal atomization produces various iron powders, including soft iron powders for magnetic applications and high-purity iron powders for electronics.
Soft iron powders: These powders boast high magnetic permeability, making them ideal for transformer cores, inductors, and electromagnetic devices. Their spherical shape allows for efficient packing and improved core performance compared to irregularly shaped iron powders.
High-purity iron powders: Through meticulous control of the atomization process, manufacturers can create iron powders with exceptionally low impurity levels. These high-purity powders are crucial for applications in electronics, particularly in soft magnetic components used in high-frequency circuits.
- Molybdenum Powders: Highly resistant to corrosion and high temperatures, molybdenum finds applications in heating elements, electrodes, and rocket engine components. Centrifugal atomization produces spherical molybdenum powders with a high melting point and excellent thermal stability. These powders are vital for creating high-performance heating elements and components that can withstand extreme environments.
- Tantalum Powders: Renowned for its exceptional biocompatibility and corrosion resistance, tantalum is a star player in medical implants and capacitors. Centrifugal atomization produces fine tantalum powders with a smooth surface and high purity. These powders contribute to the creation of biocompatible implants and high-performance capacitors used in electronic devices.
Here’s a table summarizing the properties and applications of various metal powders produced by centrifugal atomization:
Metal Powder | Key Properties | Applications |
---|---|---|
Stainless Steel | Corrosion resistance, good flowability | Additive Manufacturing (3D printing), chemical processing equipment |
Nickel-Based Superalloy | High-temperature strength, creep resistance | Jet engine components, rocket engines, gas turbines |
Aluminum | Lightweight, good packing density | Automotive components, food packaging, metal injection molding (MIM) |
Titanium | High strength-to-weight ratio, biocompatibility | Medical implants, aerospace components |
Copper | Excellent electrical conductivity, thermal conductivity | Electrical components, heat sinks |
Cobalt | High purity, uniform size distribution | Magnets, cutting tools |
Tungsten | High density, heat resistance | Armor plating, welding electrodes, heat sinks |
Soft Iron (Iron Powders) | High magnetic permeability | Transformer cores, inductors, electromagnetic devices |
High-Purity Iron (Iron Powders) | Low impurity levels | Electronics, soft magnetic components |
Molybdenum | Corrosion resistance, high melting point | Heating elements, electrodes, rocket engine components |
Tantalum | Biocompatibility, corrosion resistance | Medical implants, capacitors |
Applications of Centrifugal Atomization Powders
The applications of centrifugal atomization powders extend far beyond the list above. These versatile materials are constantly pushing the boundaries of various industries. Here are some additional areas where they shine:
- Aerospace: Centrifugal atomization powders play a crucial role in creating lightweight, high-strength components for aircraft, spacecraft, and rocket engines. The ability to tailor powder properties allows for the creation of materials that can withstand extreme temperatures, harsh environments, and the rigors of space travel.
- Biomedical: The biocompatibility of certain metal powders, like titanium and tantalum, makes them ideal for creating medical implants. Centrifugal atomization produces these powders with a high degree of purity and a smooth surface, minimizing the risk of rejection and infection.
- Additive Manufacturing (AM): Powders produced by centrifugal atomization are perfect for 3D printing processes. Their spherical shape and consistent size distribution ensure smooth powder flow and high-quality printed parts.
- Catalysis: Finely dispersed metal powders can be used as catalysts in chemical reactions. Centrifugal atomization allows for the creation of these powders with a high surface area, maximizing their catalytic efficiency.
- Energy Storage: Certain metal powders are crucial for the development of next-generation batteries. Their unique properties can contribute to higher energy density and improved battery performance.
Choosing Centrifugal Atomization Powders
Choosing the right centrifugal atomization powder for your application requires careful consideration of several factors. Here’s a breakdown of some key parameters to keep in mind:
- Powder Composition: The specific metal or alloy composition of the powder will dictate its properties and suitability for your application. Consider factors like corrosion resistance, strength, and thermal conductivity when making your selection.
- Particle Size and Distribution: The size and distribution of the powder particles significantly impact its behavior in various processes. For instance, finer powders offer better packing density but may be more challenging to flow freely. Conversely, larger particles might flow better but have lower packing density.
- Powder Morphology: The shape of the powder particles influences their packing behavior, flowability, and even their performance in certain applications. Spherical powders generally offer the best flowability and packing density compared to irregularly shaped particles.
- Surface Area: The surface area of the powder particles plays a critical role in applications like catalysis and powder metallurgy. Powders with a high surface area can interact more effectively with other materials, leading to improved performance.
- Purity: The level of impurities present in the powder can significantly impact its properties. For applications like electronics and medical implants, high-purity powders are essential to ensure optimal performance and biocompatibility.
Here’s a table summarizing the key considerations when choosing centrifugal atomization powders:
Consideration | Description |
---|---|
Powder Composition | Metal or alloy composition dictates properties |
Particle Size and Distribution | Impacts behavior in various processes |
Powder Morphology | Shape influences packing, flowability, and performance |
Surface Area | Crucial for applications like catalysis and powder metallurgy |
Purity | Level of impurities impacts properties |
Beyond the Basics: Exploring Additional Factors for Advanced Applications
For specific applications, additional factors might come into play when choosing centrifugal atomization powders. These can include:
- Flowability: The ease with which the powder flows is crucial for processes like powder metallurgy and additive manufacturing. Powders with good flowability ensure smooth operation and consistent product quality.
- Apparent Density: This refers to the density of the powder in its loose form. It’s a crucial factor in determining the amount of powder needed for a specific application.
- Sinterability: This describes the ability of the powder particles to bond together during a high-temperature sintering process. It’s essential for applications like metal injection molding (MIM).
- Grain Size: The size of the grains within the powder particles can influence the final properties of the product. Controlling grain size can be crucial for achieving desired mechanical properties.
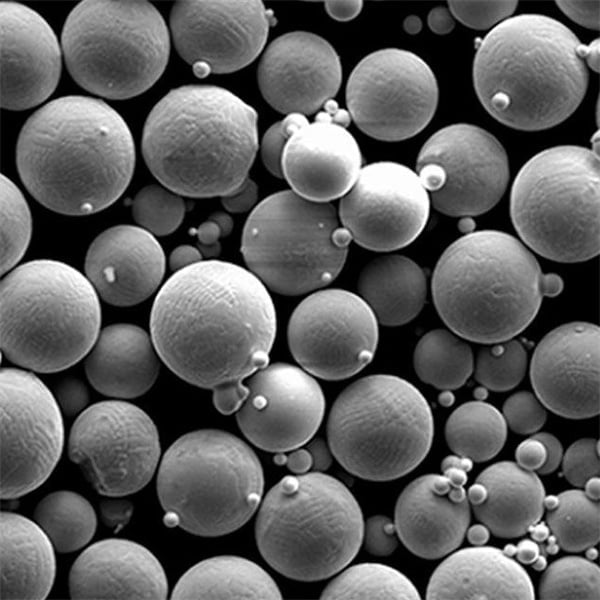
Suppliers, Specifications, and Setting the Stage for Success
Finding the Perfect Fit: A Look at Centrifugal Atomization Powder Suppliers
The world of centrifugal atomization powders boasts a diverse range of suppliers, each with its own expertise and capabilities. Here are some factors to consider when choosing a supplier:
- Material Expertise: Look for a supplier with experience in producing the specific metal or alloy powder you require.
- Quality Control: Ensure the supplier has a robust quality control system to guarantee the consistency and purity of the powders.
- Production Capacity: Consider the supplier’s production capacity to meet your needs, especially if you require large volumes of powder.
- Technical Support: A reliable supplier should offer technical support to assist you in choosing the right powder and optimizing your process.
Specifying Your Needs: Understanding Powder Specifications
Centrifugal atomization powders come with a variety of specifications that define their properties. Here are some common specifications to be aware of:
- Chemical Composition: The exact percentage of each element present in the powder.
- Particle Size Distribution: The range of sizes present in the powder particles, typically represented as a distribution curve.
- Apparent Density: The density of the powder in its loose form.
- Flowability: Measured by tests that determine the ease with which the powder flows.
- Surface Area: The total surface area of the powder particles per unit mass.
Understanding Costs: A Look at Centrifugal Atomization Powder Pricing
The cost of centrifugal atomization powders can vary depending on several factors, including:
- Material: The cost of the raw material used to produce the powder.
- Purity: Higher purity powders typically command a higher price.
- Particle Size and Distribution: Powders with specific size requirements may be more expensive.
- Volume: Larger quantities typically benefit from economies of scale, leading to lower per-unit costs.
The Bottom Line: Choosing the Right Centrifugal Atomization Powder for Optimal Results
Selecting the right centrifugal atomization powder is a critical step towards achieving success in your application. By carefully considering the factors outlined above – powder composition, particle size, morphology, surface area, purity, and additional application-specific parameters – you can choose a powder that delivers the desired properties and performance. Remember to research reputable suppliers, understand powder specifications, and factor in costs to make an informed decision.
FAQ
Q: What are the advantages of centrifugal atomization compared to other powder production methods?
Centrifugal atomization offers several advantages over other powder production methods:
- Rapid Solidification: The high cooling rates achieved during centrifugal atomization lead to the formation of unique microstructures within the powder particles. This can result in improved strength, hardness, and other desirable properties compared to powders produced by slower cooling methods.
- Fine and Uniform Powders: Centrifugal atomization excels at producing fine and uniformly sized powders. This is crucial for many applications, such as additive manufacturing and powder metallurgy, where consistent particle size ensures smooth processing and high-quality products.
- Scalability: Centrifugal atomization processes can be scaled up for large-scale production, making them commercially viable for various industries.
- Spherical Morphology: Centrifugal atomization typically produces powders with a more spherical morphology compared to other methods. This translates to better flowability, packing density, and overall performance in many applications.
Q: Are there any limitations to centrifugal atomization?
While a powerful technique, centrifugal atomization does have some limitations:
- Limited Material Selection: Not all materials are suitable for centrifugal atomization. The process can be challenging for materials with high melting points or those that are prone to oxidation.
- Yield Losses: During the atomization process, a small portion of the molten metal can be lost as splashing or fines. This can be a concern for high-value materials.
- Powder Segregation: Depending on the particle size distribution, some segregation might occur during storage or handling. Measures might be needed to ensure consistent powder properties throughout use.
Q: How does centrifugal atomization compare to other rapid solidification techniques?
Centrifugal atomization is one of several rapid solidification techniques used to produce metal powders. Here’s a brief comparison with two other common methods:
- Gas Atomization: Similar to centrifugal atomization, gas atomization uses a high-pressure gas stream to break up molten metal into droplets. It offers faster cooling rates but might result in less spherical powder morphologies compared to centrifugal atomization.
- Water Atomization: This method uses a high-pressure water jet to atomize molten metal. It’s a simpler and less expensive process but typically produces larger and more irregularly shaped particles compared to centrifugal or gas atomization.
The choice of the most suitable rapid solidification technique depends on factors like the desired powder properties, material compatibility, and cost considerations.
Share On
MET3DP Technology Co., LTD is a leading provider of additive manufacturing solutions headquartered in Qingdao, China. Our company specializes in 3D printing equipment and high-performance metal powders for industrial applications.
Inquiry to get best price and customized Solution for your business!
Related Articles
About Met3DP
Recent Update
Our Product
CONTACT US
Any questions? Send us message now! We’ll serve your request with a whole team after receiving your message.
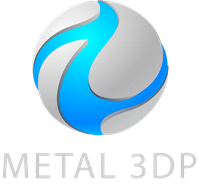
Metal Powders for 3D Printing and Additive Manufacturing
COMPANY
PRODUCT
cONTACT INFO
- Qingdao City, Shandong, China
- [email protected]
- [email protected]
- +86 19116340731