Ceramic-Lined Induction Crucibles
Table of Contents
Imagine a crucible that combines the best of both worlds: the high-efficiency heating of induction with the superior chemical resistance and thermal insulation of ceramics. That’s the magic of the ceramic-lined induction crucible. But before we delve into its intricacies, let’s set the stage.
Induction Melting: A Modern Marvel
Induction melting utilizes the power of electromagnetism to heat metals. Here’s the gist: an alternating current flowing through a coil generates a magnetic field. When a conductive material (like metal) is placed within this field, eddy currents are induced within it, causing rapid heating.
Induction melting boasts several advantages:
- Clean and precise heating: No direct flame contact translates to minimal contamination and precise temperature control.
- Energy efficiency: Induction focuses heating on the metal, minimizing heat loss to the environment.
- Fast melting: Rapid heating cycles lead to increased productivity.
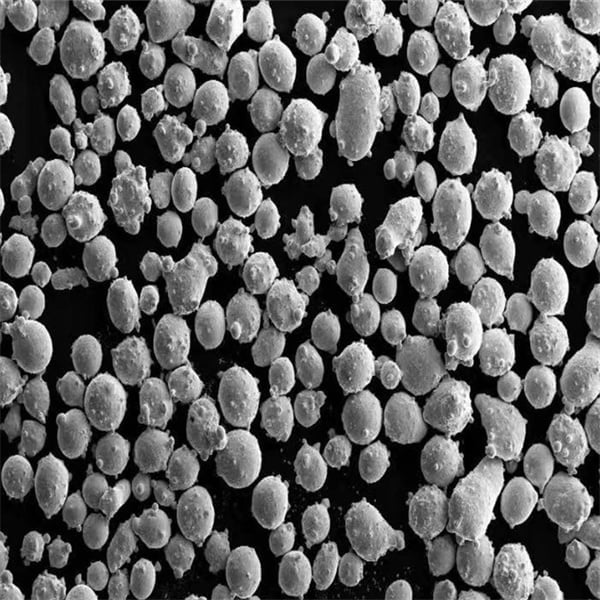
The Challenge: Material Compatibility
Induction coils are typically made of copper or aluminum. While these metals excel at generating magnetic fields, they’re not exactly ideal for holding molten metal. Here’s why:
- Reactivity: Certain molten metals react with copper or aluminum, leading to contamination and reduced crucible life.
- Oxidation: High temperatures can oxidize the coil material, compromising its performance.
Enter the Ceramic Lining: A Crucible Fit for a King (or Queen of Metalworking)
A ceramic-lined induction crucible addresses these challenges by incorporating a ceramic layer between the induction coil and the metal. This ingenious design offers several benefits:
- Chemical resistance: Many ceramics boast excellent resistance to molten metal, preventing contamination.
- Thermal insulation: The ceramic layer acts as a barrier, minimizing heat loss to the surrounding environment and improving energy efficiency.
- Durability: High-quality ceramics can withstand the intense heat and harsh conditions associated with induction melting.
Choosing the Right Ceramic Lining: A Balancing Act
Not all ceramics are created equal. The ideal ceramic lining for your application depends on several factors:
- Metal being melted: Different metals have varying degrees of reactivity. Choose a ceramic with superior resistance to the specific metal you’ll be working with.
- Temperature requirements: Ceramics have different thermal properties. Ensure the chosen lining can withstand the melting temperature of your metal.
- Oxidation resistance: Some ceramics are better suited for applications prone to oxidation.
Here’s a table outlining some common ceramic lining materials and their key properties:
Ceramic Lining Material | Key Properties | Applications |
---|---|---|
Alumina (Al2O3) | High melting point, excellent chemical resistance, good thermal conductivity | Aluminum, copper alloys, ferrous metals (except high-carbon steels) |
Zirconia (ZrO2) | Excellent high-temperature performance, good chemical resistance | Steel melting, reactive metals |
Mullite (3Al2O3.2SiO2) | High thermal shock resistance, good chemical resistance | Non-ferrous metals, glass melting |
Silicon Carbide (SiC) | High thermal conductivity, excellent wear resistance | High-temperature applications, applications requiring fast heating/cooling cycles |
the Power of Induction Melting
Induction melting shines in the realm of metal powders. Here’s why:
- Precise control: Induction heating allows for fine-tuned temperature control, crucial for preserving the properties of delicate metal powders.
- Minimal contamination: The contactless nature of induction heating minimizes contamination risks, essential for high-purity powders.
- Uniform melting: Induction creates consistent heating throughout the powder bed, promoting uniform melting and improved material properties.
Now, let’s explore some specific metal powders that can benefit from ceramic-lined induction crucibles:
- Titanium Powders: Widely used in aerospace and medical applications, titanium powders require clean, precise melting to maintain their high strength-to-weight ratio and biocompatibility. Ceramic-lined induction crucibles are ideal for preventing contamination and achieving uniform melting.
- Stainless Steel Powders: Used in various industries, stainless steel powders demand precise control over chromium and nickel content. The controlled atmosphere and minimal contamination offered by ceramic-lined induction crucibles are perfect for preserving these crucial elements.
- Nickel-Based Powders: In high-temperature applications like jet engines and turbines, nickel-based powders require exceptional strength and oxidation resistance. Ceramic-lined crucibles help maintain the integrity of these powders during melting.
- Aluminum Powders: Used in various applications from automotive parts to electronics, aluminum powders benefit from the rapid heating and efficient melting offered by induction. Ceramic linings prevent contamination and ensure consistent powder quality.
Beyond Metal Powders: Unveiling Diverse Applications
While metal powders represent a significant area for ceramic-lined induction crucibles, their applications extend far beyond:
- Jewelry Casting: The clean and precise heating of induction, coupled with the superior chemical resistance of ceramic linings, makes these crucibles perfect for melting precious metals like gold, silver, and platinum without worrying about contamination.
- Brazing and Soldering: Induction crucibles excel at rapidly melting brazing and soldering alloys, and the ceramic lining prevents unwanted reactions between the molten material and the crucible itself.
- Heat Treatment: The excellent temperature control offered by ceramic-lined induction crucibles makes them suitable for precise heat treatment processes for various metals.
Advantages of Ceramic-Lined Induction Crucibles
So, why choose a ceramic-lined induction crucible over traditional options? Here’s a breakdown of the key benefits:
- Superior chemical resistance: Protects your metal from contamination, ensuring the integrity of your final product.
- Enhanced energy efficiency: The ceramic lining minimizes heat loss, leading to lower energy consumption and reduced operating costs.
- Improved temperature control: Precise heating allows for optimal melting conditions and consistent material properties.
- Reduced oxidation: The ceramic barrier minimizes interaction between the molten metal and the atmosphere, lowering oxidation risks.
- Longer crucible life: The durable ceramic lining extends the lifespan of the crucible compared to traditional options.
- Cleaner work environment: The contactless heating of induction minimizes fumes and improves overall workshop air quality.
Disadvantages of Ceramic-Lined Induction Crucibles
While ceramic-lined induction crucibles offer numerous advantages, it’s essential to consider the potential drawbacks:
- Higher upfront cost: Compared to traditional crucibles, ceramic-lined options can have a higher initial price tag.
- Susceptibility to thermal shock: Rapid temperature changes can damage the ceramic lining, requiring careful handling and preheating procedures.
- Limited size options: Due to the complexity of manufacturing, ceramic-lined crucibles may not be available in all sizes as readily as traditional options.
Applications vs. Limitations
The decision to use a ceramic-lined induction crucible hinges on your specific needs. Here’s a table summarizing the key considerations:
Factor | Applications Favoring Ceramic Linings | Limitations to Consider |
---|---|---|
Metal type | Reactive metals, metals prone to contamination | May not be suitable for all metals |
Temperature requirements | High-temperature applications | Susceptible to thermal shock |
Production volume | Low to medium volume applications | Limited size options may not be ideal for high-volume production |
Budget | Applications where product quality and long-term cost savings are paramount | Higher upfront cost compared to traditional crucibles |
Finding the Perfect Crucible Partner
The availability of ceramic-lined induction crucibles can vary depending on your location and specific requirements. Here are some tips for finding reputable suppliers:
- Industry associations: Look for suppliers affiliated with industry associations relevant to your field (e.g., American Foundry Society, National Association of Manufacturers).
- Online marketplaces: Several online platforms specialize in industrial equipment, including ceramic-lined crucibles.
- Manufacturer websites: Many induction furnace manufacturers also offer compatible crucibles.
Pricing Considerations: A Balancing Act
As mentioned earlier, ceramic-lined induction crucibles generally have a higher upfront cost compared to traditional options. However, several factors can influence the price:
- Crucible size: Larger crucibles naturally cost more.
- Ceramic lining material: The type of ceramic used can affect the price.
- Manufacturer reputation: Reputable brands with high-quality materials may command a premium.
Here’s a table providing a general price range for various sizes of ceramic-lined induction crucibles (Note: Prices may vary depending on supplier and material):
Crucible Capacity | Price Range (USD) |
---|---|
Up to 1 kg | $100 – $300 |
1 kg – 5 kg | $300 – $700 |
5 kg – 10 kg | $700 – $1200 |
Above 10 kg | Contact supplier for quote |
The Final Verdict: A Niche Product or a Foundry Game-Changer?
Ceramic-lined induction crucibles aren’t a one-size-fits-all solution. They excel in applications where contamination control, precise temperature control, and long crucible life are critical. However, their higher upfront cost and potential for thermal shock require careful consideration. Here’s a final analysis to help you decide:
- For the discerning melter: If you prioritize high-purity metals, consistent material properties, and long production runs, ceramic-lined induction crucibles are a worthwhile investment. Their superior chemical resistance, energy efficiency, and longer lifespan can translate to significant cost savings in the long run.
- For the budget-conscious operator: If you’re working with less reactive metals and cost is a primary concern, traditional crucibles might be a more suitable option. However, consider the potential downsides like contamination risks and shorter crucible life, which could lead to higher overall costs over time.
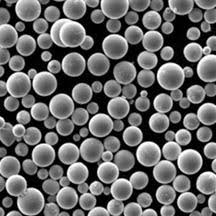
The Future of Ceramic-Lined Induction Crucibles
The future of ceramic-lined induction crucibles is brimming with potential. Here are some exciting trends to watch:
- Advanced ceramic materials: Research and development efforts are continuously improving the properties of ceramic linings, making them even more durable, resistant to thermal shock, and suitable for even higher temperatures.
- Standardization and wider availability: As the technology matures, ceramic-lined crucibles are expected to become more readily available in various sizes and configurations, catering to a broader range of applications.
- Cost reduction: Manufacturing advancements and increased adoption are likely to drive down the cost of ceramic-lined crucibles, making them more accessible to a wider range of metalworking operations.
FAQ
Question | Answer |
---|---|
What are the main advantages of ceramic-lined induction crucibles? | Superior chemical resistance, enhanced energy efficiency, improved temperature control, reduced oxidation, longer crucible life, cleaner work environment. |
What are the limitations of ceramic-lined induction crucibles? | Higher upfront cost, susceptibility to thermal shock, limited size options compared to traditional crucibles. |
Are ceramic-lined induction crucibles suitable for all metals? | No, they are ideal for reactive metals and applications demanding high purity. Traditional crucibles might be sufficient for less reactive metals. |
How much do ceramic-lined induction crucibles cost? | The price varies depending on size, material, and brand. Expect a range of $100-$1200 for crucibles up to 10 kg capacity. |
Where can I buy ceramic-lined induction crucibles? | Reputable suppliers, industry association directories, online marketplaces, and manufacturer websites are good starting points. |
Share On
MET3DP Technology Co., LTD is a leading provider of additive manufacturing solutions headquartered in Qingdao, China. Our company specializes in 3D printing equipment and high-performance metal powders for industrial applications.
Inquiry to get best price and customized Solution for your business!
Related Articles
About Met3DP
Recent Update
Our Product
CONTACT US
Any questions? Send us message now! We’ll serve your request with a whole team after receiving your message.
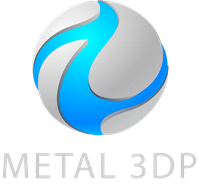
Metal Powders for 3D Printing and Additive Manufacturing