Cold Spray Additive Manufacturing Technology
Table of Contents
Cold Spray Additive Manufacturing technology is revolutionizing the world of manufacturing. This groundbreaking technique allows for the creation and repair of metal components with unprecedented precision and efficiency. In this article, we’ll dive deep into the world of CSAM, exploring its applications, advantages, limitations, and much more.
Overview of Cold Spray Additive Manufacturing Technology
Cold Spray Additive Manufacturing (CSAM) is an innovative process that involves the use of high-velocity metal particles to create or repair components. Unlike traditional methods that rely on melting and solidifying materials, CSAM uses kinetic energy to bond metal particles together, making it a low-heat process ideal for sensitive materials.
Key Details of CSAM:
- Process: High-velocity metal particle deposition.
- Temperature: Low heat, typically below the melting point of the material.
- Materials Used: Metals such as aluminum, copper, titanium, and more.
- Applications: Aerospace, automotive, electronics, and more.
- Advantages: Minimal thermal stress, high precision, material flexibility.
- Limitations: Equipment cost, surface finish quality, limited material range.
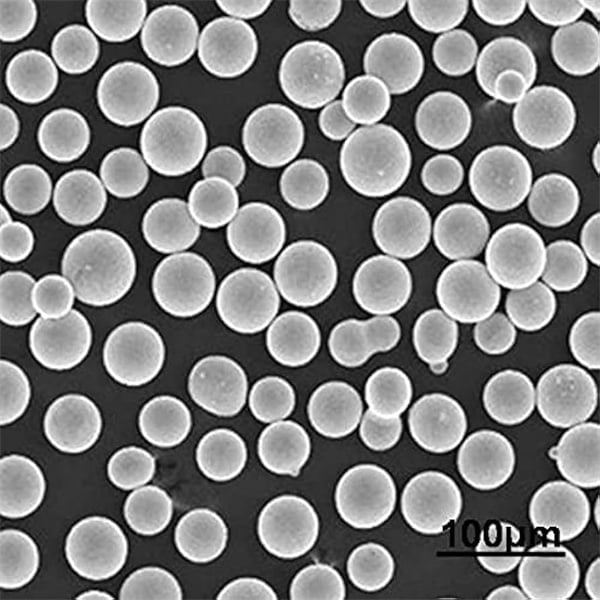
Types of Metal Powders Used in CSAM
Selecting the right metal powder is crucial for achieving optimal results in CSAM. Here, we’ll list specific metal powder models, their composition, properties, and characteristics.
Metal Powder | Composition | Properties | Characteristics |
---|---|---|---|
Aluminum 7075 | Al-Zn-Mg-Cu | High strength, lightweight | Ideal for aerospace components |
Copper C110 | 99.9% Copper | Excellent conductivity | Used in electrical and thermal applications |
Titanium Ti-6Al-4V | Ti-Al-V | High strength-to-weight ratio, corrosion resistance | Preferred for biomedical implants |
Stainless Steel 316L | Fe-Cr-Ni-Mo | High corrosion resistance, strength | Used in marine and chemical industries |
Nickel 625 | Ni-Cr-Mo | Oxidation resistance, high strength | Suitable for high-temperature applications |
Magnesium AZ31 | Mg-Al-Zn | Lightweight, good machinability | Utilized in automotive and aerospace sectors |
Cobalt-Chromium | Co-Cr | High wear resistance, biocompatibility | Commonly used in dental and orthopedic implants |
Inconel 718 | Ni-Cr-Fe | High yield strength, creep resistance | Ideal for gas turbines and aerospace engines |
Tungsten Carbide | WC | Extreme hardness, wear resistance | Used in cutting tools and wear parts |
Zinc-Aluminum ZA-27 | Zn-Al-Cu | Good casting properties, high strength | Utilized in automotive components |
Applications of Cold Spray Additive Manufacturing Technology
Cold Spray Additive Manufacturing finds use in a variety of industries due to its unique capabilities. Below is a table summarizing the key applications.
Industry | Applications |
---|---|
Aerospace | Repairing and manufacturing turbine blades, landing gear, and structural components |
Automotive | Producing lightweight parts, repairing engine components, and manufacturing prototypes |
Electronics | Creating heat sinks, repairing circuit boards, and producing conductive tracks |
Marine | Repairing ship hulls, producing corrosion-resistant components |
Medical | Manufacturing biocompatible implants, repairing medical devices |
Energy | Producing and repairing parts for gas turbines, oil rigs, and wind turbines |
Advantages of Cold Spray Additive Manufacturing Technology
Cold Spray Additive Manufacturing offers several notable advantages over traditional manufacturing methods:
- Minimal Thermal Stress: Since the process operates at low temperatures, there is minimal thermal stress and distortion in the materials being processed. This makes it ideal for repairing sensitive components without compromising their structural integrity.
- High Precision: CSAM allows for high-precision manufacturing, enabling the production of complex geometries and fine details that might be challenging with other methods.
- Material Flexibility: A wide range of metals can be used in CSAM, from lightweight aluminum to dense tungsten carbide, making it versatile for various applications.
- Reduced Waste: The process is additive, meaning material is only deposited where needed, reducing waste and making it more environmentally friendly.
- Enhanced Properties: The cold spray process can enhance the properties of the deposited material, such as increasing hardness, wear resistance, and corrosion resistance.
Disadvantages of Cold Spray Additive Manufacturing Technology
Despite its many advantages, CSAM does come with some limitations:
- Equipment Cost: The initial investment in CSAM equipment can be high, which may be a barrier for smaller companies or those with limited budgets.
- Surface Finish Quality: The surface finish achieved with CSAM may not be as smooth as that produced by other methods, necessitating additional finishing processes.
- Material Range: While CSAM can handle a variety of metals, it is not suitable for all materials, limiting its applicability in certain industries.
- Complexity: The process requires specialized knowledge and expertise to operate effectively, which can be a limiting factor for some organizations.
Specifications, Sizes, Grades, and Standards in CSAM
Understanding the specifications, sizes, grades, and standards is essential for selecting the right materials and ensuring quality in CSAM processes.
Specification | Description |
---|---|
ASTM F2924 | Standard for titanium and titanium alloy powders for additive manufacturing |
ISO/ASTM 52900 | General principles for additive manufacturing |
AMS 4999 | Standard for nickel alloy powders for cold spray |
Grade 5 Titanium | Ti-6Al-4V, widely used in aerospace and medical applications |
316L Stainless Steel | High corrosion resistance, used in marine and chemical industries |
Copper C110 | High conductivity, used in electrical applications |
Aluminum 7075 | High strength-to-weight ratio, used in aerospace |
Inconel 718 | High temperature and creep resistance, used in aerospace and energy sectors |
Suppliers and Pricing Details
Finding reliable suppliers and understanding pricing details is crucial for budgeting and planning CSAM projects.
Supplier | Material | Pricing (per kg) | Notes |
---|---|---|---|
Metal Powders USA | Aluminum 7075 | $50 – $70 | Bulk discounts available |
Advanced Powders | Copper C110 | $30 – $50 | High purity options |
Titanium Source | Titanium Ti-6Al-4V | $200 – $250 | Medical and aerospace grades |
SteelTech | Stainless Steel 316L | $40 – $60 | Custom alloy compositions |
NickelWorks | Nickel 625 | $150 – $200 | High-temperature applications |
MagnesiumMart | Magnesium AZ31 | $70 – $90 | Lightweight automotive parts |
Cobalt Co. | Cobalt-Chromium | $250 – $300 | Dental and orthopedic use |
Inconel Innovations | Inconel 718 | $180 – $220 | Turbine and high-temperature use |
Tungsten World | Tungsten Carbide | $300 – $350 | Extreme hardness applications |
Zinc Alloys Inc. | Zinc-Aluminum ZA-27 | $20 – $40 | Automotive and industrial parts |
Comparing Pros and Cons of CSAM Materials
When choosing materials for CSAM, it’s essential to weigh the pros and cons of each option. Here’s a comparison of some popular materials.
Material | Pros | Cons |
---|---|---|
Aluminum 7075 | High strength-to-weight ratio, corrosion-resistant | Expensive compared to other aluminum grades |
Copper C110 | Excellent electrical and thermal conductivity | Relatively soft, can deform under stress |
Titanium Ti-6Al-4V | High strength, biocompatible, corrosion-resistant | Very expensive, difficult to machine |
Stainless Steel 316L | High corrosion resistance, good mechanical properties | Heavier than aluminum and titanium |
Nickel 625 | High temperature and corrosion resistance | Expensive, can be challenging to process |
Magnesium AZ31 | Lightweight, good machinability | Highly flammable, requires careful handling |
Cobalt-Chromium | High wear resistance, biocompatible | Very expensive, difficult to process |
Inconel 718 | High yield strength, excellent creep resistance | Very expensive, difficult to machine |
Tungsten Carbide | Extreme hardness, high wear resistance | Very brittle, difficult to machine |
Zinc-Aluminum ZA-27 | Good casting properties, high strength | Lower corrosion resistance compared to other alloys |
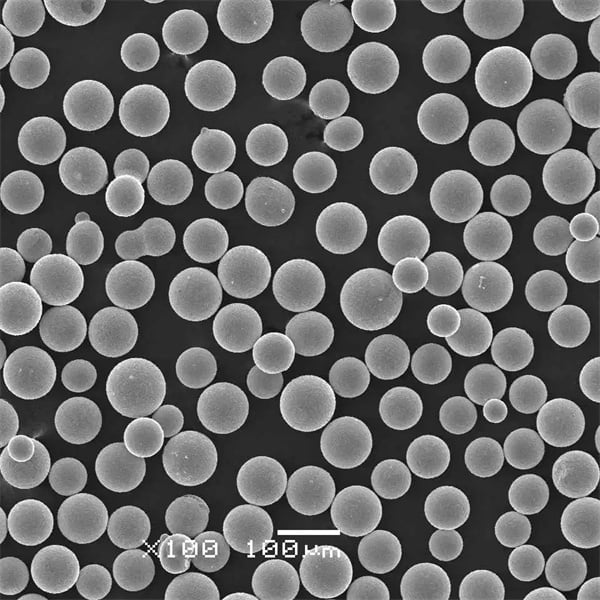
FAQ
Q: What is Cold Spray Additive Manufacturing (CSAM)?
A: CSAM is a manufacturing process that uses high-velocity metal particles to create or repair components. The process operates at low temperatures, minimizing thermal stress on the materials.
Q: What materials can be used in CSAM?
A: CSAM can utilize a wide range of metals, including aluminum, copper, titanium, stainless steel, nickel alloys, magnesium, cobalt-chromium, and more.
Q: What are the main advantages of CSAM?
A: The main advantages of CSAM include minimal thermal stress, high precision, material flexibility, reduced waste, and enhanced material properties.
Q: Are there any limitations to CSAM?
A: Yes, limitations include the high cost of equipment, potential surface finish issues, limited material range, and the complexity of the process.
Q: What industries benefit most from CSAM?
A: Industries such as aerospace, automotive, electronics, marine, medical, and energy benefit significantly from CSAM due to its precision and material capabilities.
Q: How does CSAM compare to traditional manufacturing methods?
A: Compared to traditional methods, CSAM offers lower thermal stress, higher precision, and reduced material waste. However, it may have higher equipment costs and surface finish limitations.
Q: Can CSAM be used for both manufacturing and repairing components?
A: Yes, CSAM is versatile and can be used for both creating new components and repairing existing ones, making it highly valuable in maintenance and manufacturing applications.
Q: What are some common applications of CSAM?
A: Common applications include repairing turbine blades, manufacturing lightweight automotive parts, creating heat sinks, and producing biocompatible medical implants.
Q: How does the cost of CSAM materials compare to traditional materials?
A: The cost of CSAM materials can vary significantly, with some materials being more expensive due to their specialized properties and processing requirements.
Q: What should I consider when selecting a material for CSAM?
A: Consider factors such as the material’s properties, application requirements, cost, and the specific advantages and limitations of each material.
Conclusion
Cold Spray Additive Manufacturing technology is a game-changer in the world of manufacturing. Its unique process, which minimizes thermal stress and allows for high-precision manufacturing, opens up new possibilities for a wide range of industries. By understanding the materials, applications, advantages, and limitations of CSAM, manufacturers can make informed decisions to leverage this innovative technology to its fullest potential.
Whether you’re in aerospace, automotive, medical, or another industry, CSAM offers a versatile and efficient solution for creating and repairing components. With ongoing advancements and growing adoption, the future of manufacturing is undoubtedly bright with Cold Spray Additive Manufacturing at the forefront.
Share On
MET3DP Technology Co., LTD is a leading provider of additive manufacturing solutions headquartered in Qingdao, China. Our company specializes in 3D printing equipment and high-performance metal powders for industrial applications.
Inquiry to get best price and customized Solution for your business!
Related Articles
About Met3DP
Recent Update
Our Product
CONTACT US
Any questions? Send us message now! We’ll serve your request with a whole team after receiving your message.
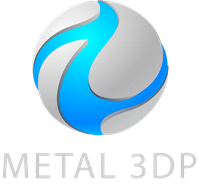
Metal Powders for 3D Printing and Additive Manufacturing