Unveiling the Power of CVD Copper Powder: A Comprehensive Guide
Table of Contents
Copper, the reddish-brown metal prized for its exceptional conductivity, finds its application in a diverse range of industries from electronics to construction. But what if you could manipulate copper at a microscopic level, tailor its properties, and create intricate structures? Enter the fascinating world of CVD Copper Powder, a revolutionary technology that unlocks a plethora of possibilities.
CVD Copper Powder: A Metamorphosis of Copper
Imagine taking gaseous precursors and transforming them into tiny copper particles through a series of chemical reactions. This, in essence, is the magic behind CVD (Chemical Vapor Deposition) copper powder. Inside a controlled chamber, these precursors decompose and deposit copper atoms onto a substrate, building up layer by layer until individual copper particles form.
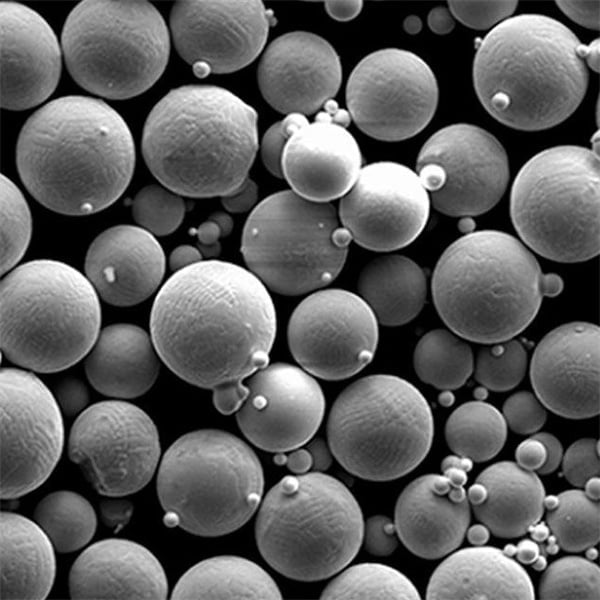
A Spectrum of CVD copper powder
The true beauty of CVD copper powder lies in its versatility. By altering parameters like temperature, pressure, and precursor gas composition, various types of copper powder can be meticulously crafted, each boasting unique properties:
Model | Description | Key Properties |
---|---|---|
Spherical Copper Powder | Smooth, ball-shaped particles with excellent flowability | High packing density, ideal for powder metallurgy applications. |
Dendritic Copper Powder | Tree-like branching structures with high surface area | Enhanced catalytic activity, suitable for chemical processing. |
Nanocrystalline Copper Powder | Extremely small grains (nanometers) offering superior strength and ductility | Ideal for creating high-performance composite materials. |
Copper-Tin Alloy Powder | Copper infused with tin, enhancing its resistance to oxidation | Perfect for applications requiring long-term exposure to harsh environments. |
Copper-Carbon Nanotube Composite Powder | Copper particles interwoven with carbon nanotubes | Combining the conductivity of copper with the mechanical strength of carbon nanotubes. |
Electrolytic Copper Powder | Derived from an electrolytic process, resulting in highly pure copper particles | Ideal for applications demanding excellent electrical conductivity. |
Anisotropic Copper Powder | Elongated or flattened particles with directional properties | Tailored for specific electrical and thermal conductivity needs. |
Hollow Copper Powder | Lightweight, hollow spheres offering low density and high surface area | Perfect for applications requiring weight reduction or enhanced catalytic performance. |
Copper Oxide Powder | Copper particles oxidized to form copper oxide with unique semiconducting properties | Utilized in sensors, electronics, and gas absorption applications. |
Copper-Silver Alloy Powder | Blending copper’s conductivity with silver’s antimicrobial properties | Ideal for creating self-sterilizing surfaces in healthcare settings. |
The Application of CVD Copper Powder in Different Fields
The diverse properties of CVD copper powder translate into a vast array of applications across various industries:
CVD Copper Powder can be used to manufacture conductive materials:
- Electrical components: High-performance electrical connectors, electrodes, and wires with enhanced conductivity and reliability.
- Heat sinks: Efficient heat dissipation in electronic devices due to copper’s excellent thermal conductivity.
- Electromagnetic shielding: Effectively shields sensitive electronics from electromagnetic interference.
CVD Copper Powder can be used to manufacture anti-corrosion coatings:
- Protecting metal surfaces: Provides a protective layer on steel, aluminum, and other metals, significantly extending their lifespan.
- Enhancing chemical resistance: Offers superior protection against harsh chemicals, ideal for applications in the chemical and oil & gas industries.
The application of CVD copper coating in the chemical industry:
- Catalysis: CVD copper powder acts as a catalyst in various chemical reactions, improving their efficiency and selectivity.
- Filtration: Copper powder-based filters offer efficient removal of impurities from liquid and gas streams.
The application of CVD copper coating in the petroleum and natural gas industry:
- Corrosion prevention: Protects pipelines and equipment from the corrosive effects of fluids and gases in the oil and gas industry.
- Enhanced heat transfer: Improves the efficiency of heat exchangers utilized in petroleum processing.
The application of CVD copper coating in marine engineering:
- Biofouling prevention: Discourages the growth of marine organisms on ship hulls and underwater structures, reducing drag and improving fuel efficiency.
- Corrosion protection: Offers effective protection against saltwater corrosion, extending the lifespan of marine infrastructure.
The application of CVD copper coating in the electronic industry:
- Interconnects: Creates high-density, low-resistance interconnects for advanced electronic devices.
- Packaging: Provides shielding and heat dissipation in electronic packages.
Advantages and Limitations of CVD Copper Powder
CVD copper powder boasts several advantages:
- High purity: The controlled environment of CVD minimizes contamination, resulting in highly pure copper powder.
- Tailored properties: Precise control over the deposition process allows for the customization of particle size, morphology, and surface properties.
- Uniformity: CVD ensures consistent particle size and morphology, leading to consistent material properties.
- Wide range of applications: The diverse properties of CVD copper powder open doors to a vast array of applications.
However, CVD copper powder also has limitations:
- Cost: The complex nature of the CVD process can make it more expensive compared to traditional powder production methods.
- Scalability: Scaling up CVD production for large-scale applications can be challenging.
- Safety considerations: Handling certain precursor gasses used in CVD requires strict safety protocols.
Choosing the Right CVD Copper Powder: A Balancing Act
Choosing the right CVD (Chemical Vapor Deposition) copper powder is akin to an acrobat walking a tightrope – it requires precise balancing between various factors to achieve optimal performance. Here’s a breakdown of the key considerations to ensure you select the most suitable powder for your application:
1. Identifying the Desired Properties:
Imagine building a house – you wouldn’t use the same materials for the foundation as you would for the roof. Similarly, the ideal CVD copper powder for your application hinges on the specific properties you need. Here are some crucial ones to consider:
- Particle size and morphology: The size and shape of the powder particles significantly impact factors like packing density, surface area, and ultimately, the final product’s properties. For instance, smaller, spherical particles might be ideal for achieving high density and smooth surfaces, while larger, irregular particles might be preferred for applications requiring specific electrical conductivity.
- Purity: The level of impurities in the powder directly affects the final product’s performance. High-purity powders often translate to superior conductivity, strength, and resistance to corrosion.
- Conductivity: For applications relying heavily on electrical current flow, the powder’s conductivity is paramount. Different powders offer varying levels of conductivity, so selecting the one that aligns with your application’s specific electrical needs is crucial.
2. Tailoring the Choice to Your Application:
Just like a car engine needs different components compared to a smartphone, the demands of your application will dictate the ideal CVD copper powder. Here are some key questions to ask yourself:
- Operating environment: Will the final product be exposed to extreme temperatures, harsh chemicals, or high pressures? The powder must be able to withstand the anticipated environmental conditions.
- Mechanical loads: Will the product experience significant mechanical stress? The powder’s particle size, morphology, and density will influence its ability to handle such loads.
- Electrical conductivity requirements: As mentioned earlier, the powder’s conductivity needs to match your application’s specific electrical demands.
3. Achieving Cost-Effectiveness:
While striving for the best performance, remember that cost plays a crucial role. Striking a balance between the desired properties, application requirements, and budget is essential. Consider exploring cost-effective alternatives that meet your application’s core needs without compromising on critical functionalities.
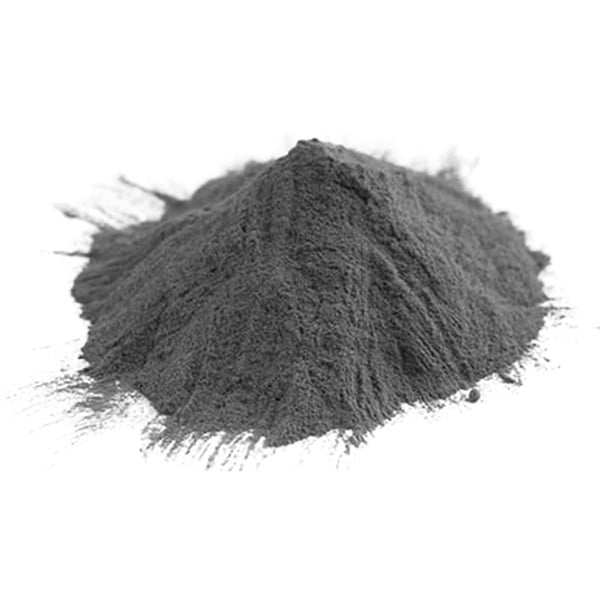
FAQs
Table: Frequently Asked Questions about CVD Copper Powder
Question | Answer |
---|---|
What are the different types of CVD copper powder available? | CVD copper powder comes in various forms, including spherical, dendritic, nanocrystalline, and more, each with unique properties tailored for specific applications. |
What are the advantages of using CVD copper powder? | CVD copper powder offers high purity, tailored properties, uniformity, and a wide range of applications. |
What are the limitations of using CVD copper powder? | CVD copper powder can be expensive, challenging to scale for large-scale production, and requires safety considerations when handling precursor gasses. |
How do I choose the right CVD copper powder for my application? | Consider the desired properties, application requirements, and cost-effectiveness when selecting the most suitable CVD copper powder. |
Where can I buy CVD copper powder? | Several companies worldwide supply CVD copper powder. Conduct thorough research to find reputable vendors offering the specific type and quality you require. |
Conclusion
CVD copper powder, with its unique properties and diverse applications, presents a transformative technology for various industries. By understanding its potential and limitations, you can harness the power of CVD copper powder to unlock innovative solutions and propel your projects forward. As research and development in this field continue to advance, we can expect even more exciting possibilities to emerge, shaping the future of materials science and engineering.
Share On
MET3DP Technology Co., LTD is a leading provider of additive manufacturing solutions headquartered in Qingdao, China. Our company specializes in 3D printing equipment and high-performance metal powders for industrial applications.
Inquiry to get best price and customized Solution for your business!
Related Articles
About Met3DP
Recent Update
Our Product
CONTACT US
Any questions? Send us message now! We’ll serve your request with a whole team after receiving your message.
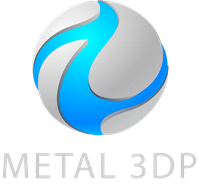
Metal Powders for 3D Printing and Additive Manufacturing
COMPANY
PRODUCT
cONTACT INFO
- Qingdao City, Shandong, China
- [email protected]
- [email protected]
- +86 19116340731