DED for automotive manufacturing
Table of Contents
The automotive industry is in a constant state of flux, driven by relentless demands for lighter, stronger, and more fuel-efficient vehicles. Enter Directed Energy Deposition (DED), a revolutionary additive manufacturing (AM) technology poised to transform the way cars are built. Imagine a process that builds complex metal parts layer by layer, offering unparalleled design freedom and customization. That’s the magic of DED, and it’s rapidly changing the game for automakers worldwide.
DED: A Metallic Marvel
DED, also known as Laser Metal Deposition (LMD) or Cold Metal Transfer (CMT), works like a high-tech sculptor. A concentrated energy source, typically a laser beam, melts metal powder fed into the machine. This molten metal is meticulously deposited onto a platform, building the desired part layer by layer.
Think of it like creating a 3D metal sketch with a laser pen, but on an industrial scale, with incredible precision and control. Unlike traditional manufacturing methods like machining or casting, DED eliminates the need for complex tooling and offers a much wider design space.
But what exactly are these metal powders that DED uses to build these automotive marvels? Buckle up, because we’re diving into the fascinating world of DED metal powders:
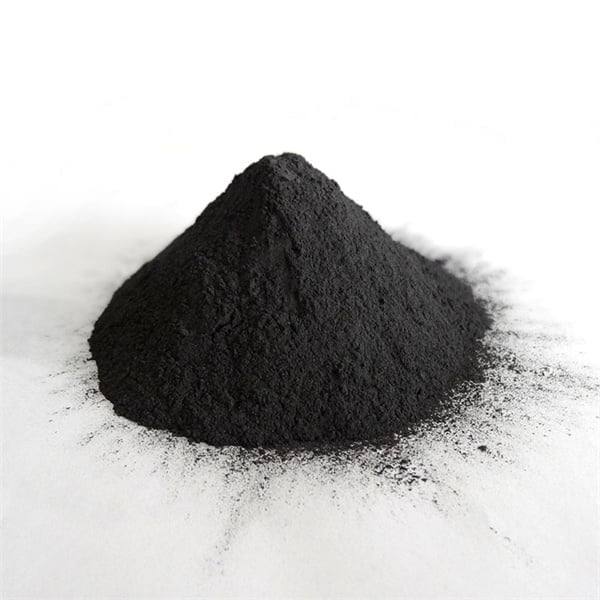
Metal Powders for DED: A Material Menagerie
The success of DED hinges on the specific metal powder used. Different powders offer unique properties, catering to a diverse range of automotive applications. Here’s a closer look at some of the most common DED metal powders and their characteristics:
Metal Powder | Composition | Properties | Applications in Automotive Manufacturing |
---|---|---|---|
Stainless Steel 316L | Fe (Iron), Cr (Chromium), Ni (Nickel), Mo (Molybdenum) | Excellent corrosion resistance, good mechanical strength, biocompatible | Exhaust manifolds, body panels (especially for high-end sports cars requiring superior corrosion resistance), medical device components used in ambulances |
Inconel 625 | Ni (Nickel), Cr (Chromium), Mo (Molybdenum), Fe (Iron) | Exceptional high-temperature performance, good oxidation resistance | Turbine blades, exhaust components, heat shields |
Aluminum Si7Mg0.3 | Al (Aluminum), Si (Silicon), Mg (Magnesium) | High strength-to-weight ratio, good weldability, excellent corrosion resistance | Lightweight suspension components, brake calipers, structural components requiring a balance of strength and weight |
Titanium Ti-6Al-4V | Ti (Titanium), Al (Aluminum), V (Vanadium) | High strength-to-weight ratio, excellent biocompatibility | High-performance engine components like connecting rods and pistons, prosthetic limbs used in specialized vehicles for people with disabilities |
Nickel Alloy 718 | Ni (Nickel), Cr (Chromium), Fe (Iron), Mo (Molybdenum), Nb (Niobium) | High strength, good creep resistance at elevated temperatures | Gears, shafts, aerospace components often used in high-performance racing cars |
Cobalt Chrome CoCrMo | Co (Cobalt), Cr (Chromium), Mo (Molybdenum) | High wear resistance, biocompatible | Hip replacement components used in specialized vehicles for people with disabilities, cutting and wear tools |
Tool Steel H13 | Fe (Iron), Cr (Chromium), Mo (Molybdenum), V (Vanadium) | High hardness, good wear resistance | Dies and molds for stamping and forming automotive parts |
Copper Cu | Cu (Copper) | Excellent thermal and electrical conductivity | Heat sinks for high-performance electronics used in electric vehicles, electrical busbars |
Inconel 718C | Ni (Nickel), Cr (Chromium), Fe (Iron), Mo (Molybdenum), Nb (Niobium) | Similar properties to Inconel 718, but with improved crack resistance | Critical engine components in high-performance and racing applications |
Maraging Steel 1.2379 | Fe (Iron), Ni (Nickel), Mo (Molybdenum), Co (Cobalt), Ti (Titanium) | High strength, excellent toughness | Critical safety components like steering knuckles and suspension arms |
This is just a glimpse into the diverse world of DED metal powders. As DED technology continues to evolve, we can expect an even wider range of powders to be developed, catering to even more specialized applications in the automotive industry.
DED in Action: Transforming Automotive Manufacturing
Now that we’ve explored the fascinating world of DED metal powders, let’s see how this technology translates into real-world applications within the automotive industry. DED offers a multitude of benefits compared to traditional manufacturing methods, making it a game-changer for carmakers:
- Unparalleled Design Freedom: Unlike traditional methods constrained by tooling limitations, DED allows for complex geometries and internal features to be incorporated into designs. Imagine lightweight components with intricate lattice structures for optimal strength-to-weight ratios, or integrated cooling channels within engine blocks for improved thermal management. DED makes these design dreams a reality.
- Lightweighting Revolution: The automotive industry is on a relentless quest to shed pounds. DED, with its ability to build lightweight yet robust structures using materials like aluminum and titanium, is a key weapon in this weight-reduction battle. Lighter vehicles translate to better fuel efficiency, reduced emissions, and ultimately, happier customers concerned about the environment.
- Rapid Prototyping and On-Demand Manufacturing: Imagine needing a custom component for a prototype vehicle – traditionally, this would involve lengthy machining processes. DED offers a faster and more agile solution. With DED, complex prototypes can be created quickly and efficiently, accelerating the development cycle and getting innovative new cars to market faster. Additionally, DED allows for on-demand manufacturing of spare parts, especially for older or out-of-production vehicles, minimizing downtime and keeping cars on the road.
- Repair and Remanufacturing: DED isn’t just about creating new parts; it’s also a powerful tool for repairing and remanufacturing existing ones. Imagine a cracked engine block or a worn-out gear – traditionally, these parts would be replaced. DED offers a more sustainable and cost-effective solution. By selectively depositing material onto damaged areas, DED can breathe new life into worn-out components, extending their lifespan and reducing waste.
Here are some specific examples of how DED is already transforming automotive manufacturing:
- DED can be used to manufacture integrated transmission housings: Traditionally, transmission housings are complex assemblies made from multiple parts. DED allows for a single, lightweight housing to be built with intricate internal channels and features, improving efficiency and reducing weight.
- DED can be used to manufacture lightweight suspension components: By using DED with aluminum or titanium powders, carmakers can create suspension components that are both strong and lightweight, contributing to better handling and fuel efficiency.
- DED can be used to manufacture high-performance engine cylinder blocks: DED allows for the creation of complex cooling channels within engine blocks, leading to more efficient heat management and improved engine performance, especially in high-performance and racing applications.
- DED can be used to manufacture custom components for prototype vehicles: The rapid prototyping capabilities of DED allow carmakers to experiment with innovative designs and get new vehicles to market faster.
- DED can be used to repair and remanufacture critical automotive parts: From cracked engine blocks to worn-out gears, DED offers a cost-effective and sustainable solution for repairing and extending the lifespan of critical automotive components.
These are just a few examples, and as DED technology matures, we can expect to see even more innovative applications emerge, revolutionizing the way cars are built.
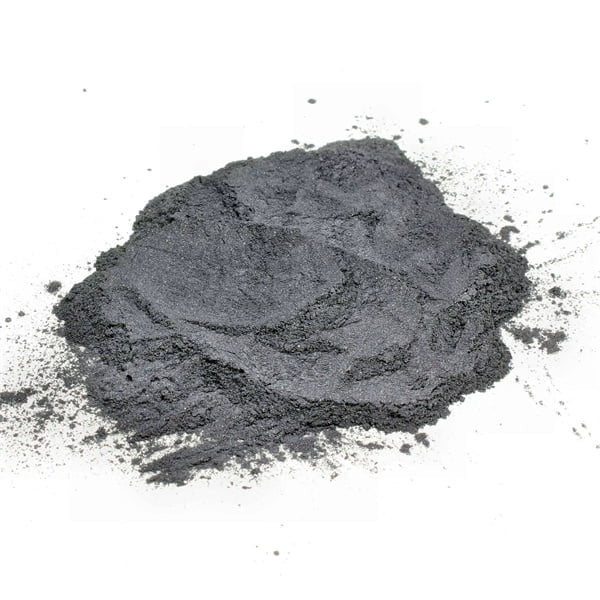
Advantages and Limitations of DED in Automotive Manufacturing
Advantages:
- Unmatched design freedom: Create complex geometries and integrate features impossible with traditional methods.
- Lightweighting: Build strong yet lightweight components for improved fuel efficiency.
- Rapid prototyping: Accelerate development cycles with quick and efficient prototype creation.
- On-demand manufacturing: Produce custom parts as needed, minimizing inventory requirements.
- Repair and remanufacturing: Extend the lifespan of critical components and reduce waste.
Limitations:
- Cost: DED systems and metal powders can be expensive compared to traditional methods.
- Build speed: DED can be slower than some traditional manufacturing techniques for large-volume production.
- Surface finish: DED parts may require additional post-processing for a smooth finish.
- Process control: DED requires careful control of parameters to ensure part quality and consistency.
The Future of DED in Automotive Manufacturing
The future of DED in automotive manufacturing is bright. As DED technology continues to evolve, we can expect to see:
- Reduced costs: Advancements in DED systems and metal powders will make the technology more cost-competitive with traditional methods.
- Increased build speeds: Faster DED processes will make the technology suitable for higher-volume production runs.
- Improved surface finishes: Advanced DED techniques will produce parts with smoother finishes, reducing the need for post-processing.
- Wider range of materials: New DED metal powders will be developed, catering to a broader spectrum of automotive applications.
DED: Material Selection Considerations
We previously explored a variety of DED metal powders, but choosing the right one for your specific application requires careful consideration. Here are some key factors to keep in mind:
- Desired part properties: This is the most crucial factor. Match the powder’s properties (strength, corrosion resistance, weight, etc.) to the needs of the final part. For instance, if you’re building a lightweight suspension component, aluminum Si7Mg0.3 would be a good choice due to its high strength-to-weight ratio. Conversely, if you’re building a turbine blade that needs to withstand extreme temperatures, Inconel 625 would be a better option due to its exceptional high-temperature performance.
- Compatibility with the DED system: Not all DED systems are created equal. Ensure the powder you choose has the appropriate particle size distribution and flowability for optimal performance within your specific DED machine. Consult your machine’s manufacturer for recommended powders or compatible powder characteristics.
- Cost: DED metal powders can vary significantly in price. Consider the cost of the powder itself, as well as any additional processing costs associated with the chosen material. For instance, some exotic powders like Maraging Steel 1.2379 might offer superior strength but come at a premium compared to more common options like Stainless Steel 316L.
- Environmental impact: Sustainability is a growing concern in the automotive industry. Consider the environmental footprint of the powder’s production and recyclability. Some powders, like aluminum and titanium, are more readily recycled than others, contributing to a more sustainable manufacturing process.
- Availability: Ensure the powder you choose is readily available from a reputable supplier. Production delays due to powder shortages can disrupt your manufacturing process.
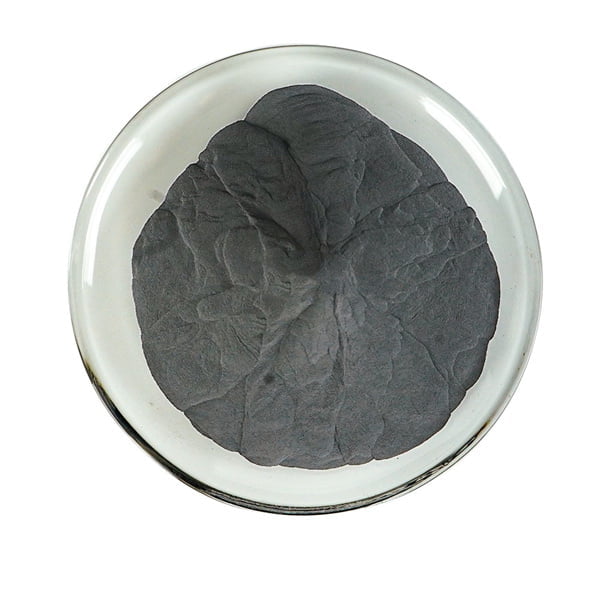
Here’s a table summarizing some key considerations for different types of DED metal powders:
Desired Part Property | Potential DED Metal Powders | Considerations |
---|---|---|
High strength-to-weight ratio | Aluminum Si7Mg0.3, Titanium Ti-6Al-4V | Availability, cost-effectiveness |
Excellent high-temperature performance | Inconel 625, Inconel 718 | Compatibility with DED system |
Good corrosion resistance | Stainless Steel 316L, Aluminum Si7Mg0.3 | Environmental impact |
High wear resistance | Cobalt Chrome CoCrMo, Tool Steel H13 | Surface finish requirements |
Biocompatibility | Stainless Steel 316L, Titanium Ti-6Al-4V | Used in specialized vehicles for people with disabilities |
Remember, choosing the right DED metal powder is a critical step in ensuring the success of your project. By carefully considering the factors mentioned above, you can select the ideal powder to meet your specific needs and achieve optimal results.
FAQ
Here are some frequently asked questions (FAQs) about DED in automotive manufacturing, presented in a clear and informative table format:
Question | Answer |
---|---|
What are the main benefits of using DED in automotive manufacturing? | DED offers unparalleled design freedom, enables lightweighting of vehicles, facilitates rapid prototyping and on-demand manufacturing, and allows for repair and remanufacturing of critical components. |
What are some limitations of DED? | DED systems and metal powders can be expensive compared to traditional methods. Build speeds can be slower for large-volume production, surface finishes might require post-processing, and the process requires careful control for consistent part quality. |
What types of metal powders are commonly used in DED for automotive applications? | Stainless Steel 316L, Inconel 625, Aluminum Si7Mg0.3, Titanium Ti-6Al-4V, Nickel Alloy 718, and many more, each with specific properties suited for different applications. |
Is DED suitable for high-volume production? | While DED is not currently ideal for mass production of simple parts, it’s becoming increasingly viable for smaller-batch, high-value components or those with complex geometries. |
How is DED impacting the future of the automotive industry? | DED is expected to play a significant role in the future of automotive manufacturing, enabling lighter, more fuel-efficient vehicles, faster development cycles, and more sustainable manufacturing practices. |
By understanding the potential and limitations of DED, as well as the intricacies of DED metal powder selection, automotive manufacturers can leverage this transformative technology to create the next generation of vehicles.
Share On
MET3DP Technology Co., LTD is a leading provider of additive manufacturing solutions headquartered in Qingdao, China. Our company specializes in 3D printing equipment and high-performance metal powders for industrial applications.
Inquiry to get best price and customized Solution for your business!
Related Articles
About Met3DP
Recent Update
Our Product
CONTACT US
Any questions? Send us message now! We’ll serve your request with a whole team after receiving your message.
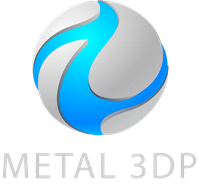
Metal Powders for 3D Printing and Additive Manufacturing