The application of DED in the medical field
Table of Contents
Imagine a world where damaged bones can be repaired with implants perfectly customized to fit your unique anatomy. A world where surgeons wield tools built layer-by-layer to match the intricate needs of complex procedures. This future is rapidly approaching, thanks to the innovative technology known as Directed Energy Deposition (DED).
DED, also sometimes referred to as Laser Metal Deposition (LMD), is a revolutionary 3D printing technique that utilizes a high-powered energy source, like a laser or electron beam, to melt and fuse metal powders together, creating a three-dimensional object. This technology holds immense potential for the medical field, offering unprecedented possibilities for creating personalized implants, complex surgical tools, and even biocompatible structures for tissue regeneration.
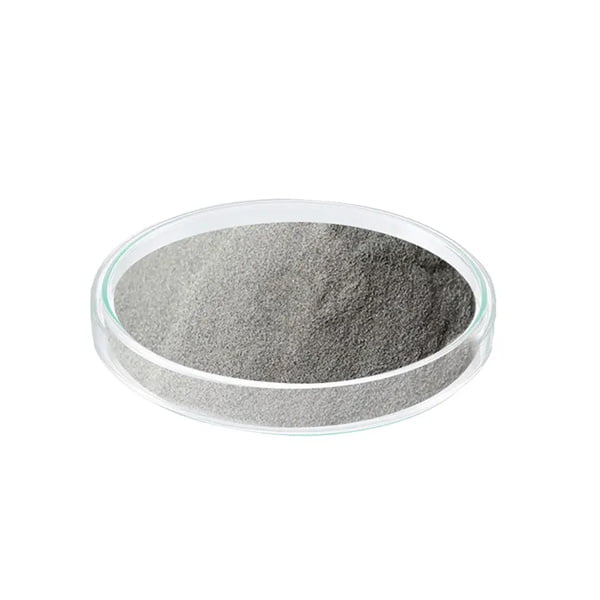
10+ Metal Powders Powering Medical DED Applications
The success of DED in medical applications hinges on the utilization of specific metal powders with properties tailored for the human body. Here, we delve into a selection of these metallic marvels, exploring their unique characteristics and potential uses:
1. Titanium Grade 2 (CP Ti):
- Composition: Pure titanium (Ti)
- Properties: Excellent biocompatibility, corrosion resistance, and good strength-to-weight ratio.
- Applications: Widely used for implants like bone screws, plates, and dental abutments due to its safety and compatibility with bone tissue.
- Advantages: Proven track record in medical applications, readily available, and cost-effective.
- Limitations: Lower strength compared to some other titanium alloys.
2. Titanium Grade 6 (Ti-6Al-4V):
- Composition: Titanium alloy with 6% aluminum (Al) and 4% vanadium (V)
- Properties: Superior strength and fatigue resistance compared to Grade 2 Ti, retains good biocompatibility.
- Applications: Ideal for load-bearing implants like hip replacements, knee components, and trauma fixation devices.
- Advantages: Offers a balance of strength, biocompatibility, and osseointegration (bone bonding).
- Limitations: Slightly higher cost than Grade 2 Ti.
3. CoCrMo (Cobalt-Chromium-Molybdenum):
- Composition: Alloy of cobalt (Co), chromium (Cr), and molybdenum (Mo)
- Properties: Excellent wear resistance, high strength, and good corrosion resistance.
- Applications: Primarily used for articulating components in artificial joints like hip and knee replacements due to its low wear properties.
- Advantages: Proven wear resistance translates to longer implant lifespan.
- Limitations: Concerns regarding potential metal ion release and potential allergic reactions in some patients.
4. Tantalum:
- Composition: Pure tantalum (Ta)
- Properties: Highly biocompatible, corrosion resistant, and radiolucent (doesn’t show up on X-rays)
- Applications: Used for implants requiring radiolucency for post-operative imaging, such as cranial implants and dental restorations.
- Advantages: Offers a unique combination of biocompatibility and radiolucency.
- Limitations: Relatively high cost compared to other options.
5. Nickel-Chromium (Ni-Cr):
- Composition: Alloy of nickel (Ni) and chromium (Cr)
- Properties: High strength, corrosion resistance, and good wear resistance.
- Applications: Primarily used for manufacturing medical instruments due to its affordability and good mechanical properties.
- Advantages: Cost-effective option for instruments requiring strength and wear resistance.
- Limitations: Not ideal for implants due to potential allergic reactions to nickel in some individuals.
6. Stainless Steel 316L:
- Composition: Steel alloy containing iron (Fe), chromium (Cr), nickel (Ni), and molybdenum (Mo)
- Properties: Affordable, readily available, good corrosion resistance, and moderate strength.
- Applications: Used for some surgical instruments and temporary implants due to its cost-effectiveness.
- Advantages: Affordable choice for non-permanent implants and instruments.
- Limitations: Lower strength compared to titanium alloys, not ideal for long-term implants.
7. Inconel 625:
- Composition: Nickel-chromium-based superalloy with additions of molybdenum (Mo) and niobium (Nb)
- Properties: Exceptional high-temperature performance, good strength, and corrosion resistance.
- Applications: Potential use in future for implants requiring high wear resistance and durability in harsh environments.
- Advantages: Offers superior strength and high-temperature performance.
- Limitations: High cost and potential biocompatibility concerns require further investigation.
8. Polyetheretherketone (PEEK):
- Composition: High-performance polymer known for its excellent mechanical properties.
- Properties: Biocompatible, lightweight, good strength, and radiolucent.
- Applications: Primarily used for spinal implants and cages due to its combination of strength, radiolucency, and compatibility with bone tissue.
- Advantages: Offers a unique alternative to metal implants, particularly for weight-sensitive applications.
- Limitations: Lower strength compared to some metal alloys, potential wear concerns over long periods.
9. Nickel-Titanium (NiTi):
- Composition: Shape memory alloy composed of nickel (Ni) and titanium (Ti)
- Properties: Possesses unique “shape memory” effect, regaining its original shape upon heating. Offers superelasticity, returning to its original form after deformation.
- Applications: Potential future use for stents, orthodontic wires, and other medical devices requiring shape memory or superelastic properties.
- Advantages: Shape memory and superelasticity properties offer unique functionalities for certain applications.
- Limitations: Technical challenges remain in DED processing of NiTi, and biocompatibility requires further evaluation.
10. Copper (Cu):
- Composition: Pure copper (Cu)
- Properties: Excellent electrical conductivity, antibacterial properties, and good workability.
- Applications: Potential future use for antimicrobial implants and components in medical devices requiring electrical conductivity.
- Advantages: Antibacterial properties offer a potential benefit in reducing implant-associated infections.
- Limitations: Limited research on DED processing of copper for medical applications, potential toxicity concerns require further investigation.
the Future of Medical DED
This list merely scratches the surface of the vast potential metal powders hold for medical DED. Researchers are constantly exploring new alloys and composites, pushing the boundaries of what’s possible. Here’s a peek into some exciting advancements on the horizon:
- Biocompatible Alloys: Development of new alloys specifically designed for optimal biocompatibility, potentially reducing concerns about metal ion release and allergic reactions.
- Functionally Graded Materials: DED’s ability to create objects with varying properties within a single structure could lead to implants that seamlessly integrate with bone tissue, mimicking its natural gradient in strength and elasticity.
- Porous Metals: DED allows for the creation of porous metal structures that encourage bone ingrowth and improve osseointegration, potentially leading to faster healing and improved implant stability.
- Personalized Implants: DED can create custom implants tailored to individual patients’ anatomy, potentially leading to a significant improvement in fit and function.
These advancements, coupled with ongoing research and development, promise to revolutionize the medical field. From creating life-saving implants to developing intricate surgical tools, DED has the potential to transform patient care and usher in a new era of personalized medicine.
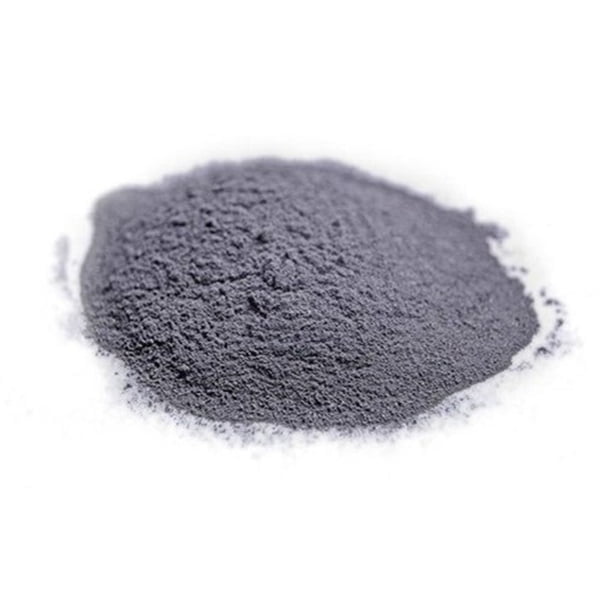
FAQs
Q: What are the advantages of using DED for medical applications?
A: DED offers several advantages over traditional manufacturing methods for medical devices:
- Customization: DED allows for the creation of personalized implants perfectly tailored to a patient’s unique anatomy.
- Complexity: DED can create intricate structures with complex geometries, enabling the development of advanced surgical tools and implants.
- Lightweight Design: DED allows for the creation of lightweight implants using materials like titanium and PEEK, reducing weight-related complications.
- Reduced Waste: DED is a more sustainable manufacturing method compared to traditional techniques, minimizing material waste.
Q: Are there any limitations to using DED in medical applications?
A: While DED offers exciting possibilities, some limitations exist:
- Cost: DED technology is still under development, and the cost of DED-manufactured implants can be higher than traditional methods.
- Regulation: Regulatory frameworks for DED-produced medical devices are still evolving, requiring additional time and resources for approval.
- Limited Material Availability: Not all metals are readily available in DED-compatible powder forms, restricting design possibilities.
Q: What’s the future outlook for DED in the medical field?
A: The future of DED in medicine is incredibly bright. As technology advances, costs decrease, and regulations adapt, DED is poised to become a mainstream manufacturing method for a wide range of medical devices. The potential for personalized implants, complex surgical tools, and biocompatible structures promises to revolutionize patient care and improve outcomes for millions.
In Conclusion
DED represents a transformative technology with the power to reshape the medical landscape. From customized implants to innovative surgical tools, DED offers a glimpse into a future of personalized medicine where patient needs are met with unparalleled precision and care.
Share On
MET3DP Technology Co., LTD is a leading provider of additive manufacturing solutions headquartered in Qingdao, China. Our company specializes in 3D printing equipment and high-performance metal powders for industrial applications.
Inquiry to get best price and customized Solution for your business!
Related Articles
About Met3DP
Recent Update
Our Product
CONTACT US
Any questions? Send us message now! We’ll serve your request with a whole team after receiving your message.
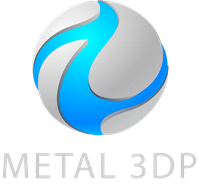
Metal Powders for 3D Printing and Additive Manufacturing