The application of DMLS technology in the field of molds
Table of Contents
Imagine a world where mold design transcends limitations. Where intricate geometries and internal cooling channels are no longer obstacles, but opportunities. This is the reality ushered in by Direct Metal Laser Sintering (DMLS) technology, revolutionizing the mold-making landscape. Buckle up, because we’re diving deep into the world of DMLS molds, exploring the how, the what, and the why behind this transformative technology.
DMLS technology: A 3D Printing Powerhouse for Molds
DMLS, also known as Selective Laser Melting (SLM), belongs to the family of Additive Manufacturing (AM) technologies. Think of it like a 3D printer on steroids, but instead of plastic filaments, it uses a high-powered laser to fuse together fine metallic powders, layer by layer, building the desired mold geometry. This layer-by-layer approach unlocks a treasure trove of benefits for mold makers:
- Unmatched Design Freedom: DMLS eliminates the constraints of traditional subtractive manufacturing (machining, milling). Complex internal features, conformal cooling channels that snake around intricate geometries – DMLS handles it all with ease. It’s like sculpting a mold from pure imagination.
- Reduced Lead Times: Gone are the days of waiting weeks for complex molds to be machined. DMLS allows for rapid prototyping and mold creation, significantly accelerating the product development cycle. Imagine getting your product to market faster with DMLS as your secret weapon!
- Enhanced Mold Performance: DMLS molds boast superior strength, thermal conductivity, and wear resistance compared to their traditionally manufactured counterparts. This translates to longer mold life, fewer production disruptions, and ultimately, higher profitability.
Now, let’s delve deeper into the world of metal powders used in DMLS mold-making. Buckle up for a materials science exploration!
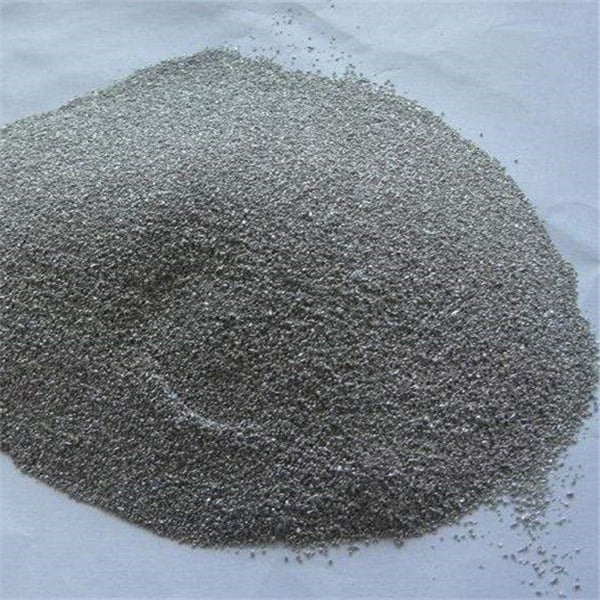
Choosing the Right Weapon for Your Molding Needs
The success of a DMLS mold hinges on the right choice of metal powder. Just like choosing the perfect paintbrush for your masterpiece, selecting the optimal powder ensures exceptional mold performance. Here’s a glimpse into some of the most popular metal powders used in DMLS mold-making, along with their unique properties:
Material | Composition | Properties | Common Applications |
---|---|---|---|
Stainless Steel 316L | Fe (Iron), Cr (Chromium), Ni (Nickel), Mo (Molybdenum) | Excellent corrosion resistance, good strength and ductility | Injection molding of various plastics, blow molding |
Maraging Steel | Fe (Iron), Ni (Nickel), Mo (Molybdenum), Ti (Titanium), Al (Aluminum) | High strength-to-weight ratio, excellent dimensional stability | Injection molding of high-performance plastics, molds for metal casting |
Inconel 625 | Ni (Nickel), Cr (Chromium), Mo (Molybdenum), Fe (Iron) | Exceptional high-temperature resistance, good corrosion resistance | Molds for aerospace components, hot melt molding applications |
Tool Steel (H13) | Fe (Iron), Cr (Chromium), Mo (Molybdenum), V (Vanadium) | High hardness and wear resistance, good thermal conductivity | Injection molding of abrasive plastics, compression molding |
Aluminum Alloy AlSi10Mg | Al (Aluminum), Si (Silicon), Mg (Magnesium) | Lightweight, good thermal conductivity | Low-pressure molding applications, prototyping molds |
Copper | Cu (Copper) | High thermal conductivity, excellent electrical conductivity | Injection molding of heat-sensitive plastics, molds for electroplating |
Titanium (Ti-6Al-4V) | Ti (Titanium), Al (Aluminum), V (Vanadium) | High strength-to-weight ratio, good biocompatibility | Medical implant molds, aerospace component molds |
Please note: This table is not exhaustive, and there are many other metal powders available for DMLS mold-making. The selection of the optimal powder depends on the specific application and desired mold properties.
As you can see, each metal powder boasts a unique set of properties, making it ideal for specific molding applications. For instance, if you’re molding high-temperature resistant plastics, Inconel 625 with its stellar heat tolerance becomes the clear champion. On the other hand, if lightweight molds with good thermal conductivity are your priority, Aluminum Alloy AlSi10Mg emerges as the frontrunner.
Beyond the Basics: A Deeper Look at Metal Powders
But the story doesn’t end there. The particle size, distribution, and flowability of the metal powder significantly impact the quality and performance of the DMLS mold. Finer powders generally result in smoother surface finishes on the mold, but can also be more challenging to work with due to reduced flowability. Conversely, coarser powders offer better flow characteristics but might lead to a slightly rougher mold surface. It’s a delicate balancing act, and experienced DMLS technicians understand the art of selecting the right powder with the optimal particle characteristics for the job.
There’s also the factor of powder chemistry to consider. The presence of certain elements or impurities in the powder can influence the laser melting process and ultimately affect the mold’s mechanical properties. For instance, the presence of oxygen in a steel powder can lead to increased porosity in the finished mold, reducing its strength. Reputable metal powder suppliers meticulously control the chemistry of their powders to ensure consistent and reliable performance in the DMLS process.
The Future of Metal Powders: Innovation on the Horizon
The world of metal powders for DMLS is constantly evolving. Researchers are developing new powder formulations with enhanced properties, pushing the boundaries of what’s possible with DMLS mold-making. Here are some exciting trends to keep an eye on:
- Metal powder blends: Imagine combining the excellent strength of maraging steel with the superior corrosion resistance of stainless steel 316L. Metal powder blends are making this a reality, offering unique property combinations that cater to specific molding applications.
- Nanopowders: Powders with even finer particle sizes are being explored, promising exceptional surface finishes and potentially enabling the creation of even more intricate mold features.
- Composites: The incorporation of non-metallic elements like ceramic particles into metal powders is another exciting avenue. This could lead to the development of DMLS molds with superior wear resistance and thermal management capabilities.
These advancements, coupled with continuous improvements in DMLS technology, paint a bright future for mold-making. We can expect to see even more complex, high-performance molds being produced with DMLS, revolutionizing various industries in the process.
DMLS Molds in Action: Unleashing Potential Across Industries
DMLS technology isn’t just a fancy buzzword; it’s a game-changer across various industries that rely on molds for production. Here are some compelling examples of how DMLS molds are making waves:
- Automotive Industry: DMLS molds are enabling the creation of complex, lightweight plastic components for cars, improving fuel efficiency and overall performance. Imagine intricate air intake manifolds or aerodynamic body panels – DMLS makes them possible.
- Medical Device Manufacturing: The biocompatible nature of certain metal powders like titanium makes DMLS ideal for creating molds for medical implants. This allows for the production of complex, patient-specific implants with exceptional precision.
- Consumer Electronics: The ever-shrinking size and intricate designs of electronic components are a perfect match for DMLS molds. With DMLS, manufacturers can create molds for producing highly functional and miniaturized electronic components.
- Aerospace Industry: The high strength-to-weight ratio and heat resistance of certain metal powders make DMLS a valuable tool for aerospace mold-making. Complex engine components and lightweight aircraft parts can be produced with DMLS molds, pushing the boundaries of aerospace design.
These are just a few examples, and the potential applications of DMLS molds continue to expand. As DMLS technology becomes more accessible and cost-effective, we can expect to see its adoption in even more industries, transforming the way products are designed and manufactured.
DMLS Molds: A Balancing Act – Weighing the Pros and Cons
While DMLS technology offers a plethora of benefits for mold-making, it’s essential to consider both the advantages and limitations before diving headfirst. Here’s a balanced perspective to help you make informed decisions:
Advantages of DMLS Molds:
- Unmatched Design Freedom: Unleash your creativity with complex geometries and internal features.
- Reduced Lead Times: Get your products to market faster with rapid prototyping and mold creation.
- Enhanced Mold Performance: Experience superior strength, wear resistance, and thermal conductivity.
- Lightweight Molds: Certain metal powders like aluminum offer weight reduction benefits.
- Conformal Cooling Channels: Optimize cooling efficiency for faster cycle times.
Limitations of DMLS Molds:
- Higher upfront cost: DMLS machines can be expensive compared to traditional mold-making equipment.
- Limited mold size: Current DMLS build volumes might not be suitable for very large molds.
- Surface Finish: While improving, DMLS mold surfaces might require additional post-processing for some applications.
- Powder Availability: The selection of metal powders for DMLS applications might be limited compared to traditional materials.
Making the DMLS Decision: Is it Right for You?
The decision to adopt DMLS mold-making depends on your specific needs and priorities. If you require complex mold designs, rapid prototyping capabilities, and high-performance molds, DMLS might be the perfect solution. However, if cost is a major concern, or your application demands very large molds, traditional methods might be more suitable. Ultimately, a thorough cost-benefit analysis considering your production volumes, lead time requirements, and desired mold properties is crucial before making the switch to DMLS.
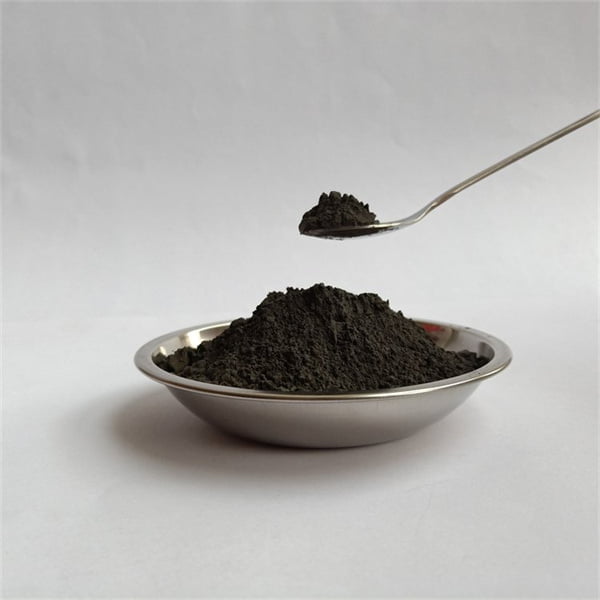
FAQ
Let’s address some of the most frequently asked questions regarding DMLS molds:
Q: How strong are DMLS molds compared to traditionally manufactured molds?
A: DMLS molds, when made with the appropriate metal powder, can be significantly stronger than traditionally machined molds. This is due to the inherent density and lack of internal defects achievable with the DMLS process.
Q: Are DMLS molds suitable for high-volume production?
A: While DMLS excels in prototyping and low- to medium-volume production, its suitability for high-volume applications depends on the specific mold design and production requirements. The cost per unit mold might be higher for DMLS compared to traditional methods for very high volumes.
Q: What kind of post-processing is required for DMLS molds?
A: The level of post-processing needed for DMLS molds depends on the application and desired surface finish. Some molds might require minimal post-processing, while others might benefit from techniques like sandblasting or polishing to achieve a smoother surface finish.
Q: Can I repair DMLS molds if they get damaged?
A: Depending on the extent of the damage, DMLS molds can sometimes be repaired using techniques like welding or laser cladding. However, the feasibility and cost-effectiveness of repairs need to be evaluated on a case-by-case basis.
Q: Where can I find a company that offers DMLS mold-making services?
A: With the growing popularity of DMLS technology, there’s an increasing number of companies offering DMLS mold-making services. Conduct thorough research to find a reputable service provider with experience in your specific industry and desired metal powders.
The Future of DMLS Molds: A Canvas for Innovation
DMLS technology stands at the forefront of a mold-making revolution. As the technology matures, we can expect to see advancements in:
- DMLS machine capabilities: Larger build volumes, faster printing speeds, and even more sophisticated laser control systems are on the horizon.
- Metal powder innovation: New powder formulations with enhanced properties and printability will continue to push the boundaries of what’s possible.
- Reduced costs: As DMLS technology becomes more widespread, the cost of DMLS machines and metal powders is expected to decrease, making it more accessible to a wider range of manufacturers.
These advancements paint a promising future for DMLS mold-making. Imagine a world where complex, high-performance molds can be produced quickly and cost-effectively, enabling the creation of innovative products across various industries. DMLS technology is not just shaping the future of molds; it’s shaping the future of manufacturing itself.
Share On
MET3DP Technology Co., LTD is a leading provider of additive manufacturing solutions headquartered in Qingdao, China. Our company specializes in 3D printing equipment and high-performance metal powders for industrial applications.
Inquiry to get best price and customized Solution for your business!
Related Articles
About Met3DP
Recent Update
Our Product
CONTACT US
Any questions? Send us message now! We’ll serve your request with a whole team after receiving your message.
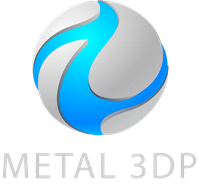
Metal Powders for 3D Printing and Additive Manufacturing