The Application of EBM in Mold Manufacturing
Table of Contents
Imagine a world where mold manufacturing transcends traditional limitations. A world where intricate designs and complex cooling channels are no longer obstacles, but opportunities. This world is becoming a reality thanks to Electron Beam Melting (EBM) technology, a revolutionary additive manufacturing process shaking the foundations of the mold-making industry.
EBM technology utilizes a high-powered electron beam to selectively melt metal powder layer by layer, meticulously building three-dimensional objects. This innovative approach unlocks a treasure trove of benefits for mold manufacturers, pushing the boundaries of design freedom, production efficiency, and part performance.
But before diving into the exciting world of EBM applications in mold manufacturing, let’s establish a solid foundation.
An Exploration of EBM Technology
EBM operates in a vacuum chamber, ensuring a clean and controlled environment. The electron beam, with its immense power, melts the metal powder particles, fusing them together to create the desired mold geometry. This layer-by-layer approach offers exceptional precision, enabling the creation of intricate features that would be near impossible or incredibly expensive with traditional methods.
Here’s a captivating analogy: Think of EBM like a skilled sculptor meticulously building a masterpiece, one layer at a time. But unlike traditional sculpting, EBM utilizes a digital blueprint, allowing for unparalleled accuracy and repeatability.
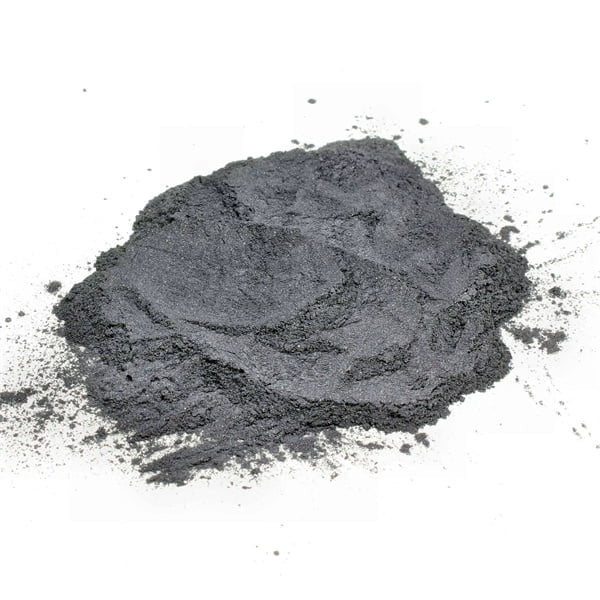
Metal Powders for EBM Applications
The success of EBM hinges on the specific metal powders used. Each powder boasts unique properties, catering to diverse mold-making requirements. Here’s a glimpse into some of the most popular metal powders employed in EBM:
Metal Powder | Composition | Properties | Applications in Mold Manufacturing |
---|---|---|---|
Stainless Steel 316L | 16-18% Chromium, 10-14% Nickel, 2-3% Molybdenum | Excellent corrosion resistance, high strength, biocompatible | Injection mold cores and cavities for medical devices, chemical processing equipment |
Inconel 625 | Nickel-chromium superalloy with additions of molybdenum, niobium, and iron | Exceptional high-temperature performance, outstanding resistance to oxidation and corrosion | Molds for turbine blades, aerospace components, hot-runner systems |
Maraging Steel 1.2709 | High nickel content with additions of molybdenum and titanium | Exceptional strength-to-weight ratio, good dimensional stability | Molds for high-pressure applications, cores for complex geometries |
Tool Steel H13 | Chromium-molybdenum alloy with additions of vanadium | High wear resistance, good hot-work performance | Molds for plastic injection molding with abrasive materials, inserts for stamping dies |
Copper | Pure copper | High thermal conductivity, excellent electrical conductivity | Molds requiring efficient heat transfer, electrodes for electrical applications (limited use due to high energy consumption in EBM) |
Titanium Ti6Al4V | Titanium alloy with 6% aluminum and 4% vanadium | High strength-to-weight ratio, good biocompatibility | Molds for aerospace components, medical implants (limited use due to higher cost) |
Nickel Alloy 718 | Nickel-chromium alloy with additions of iron, molybdenum, and niobium | High strength, good corrosion resistance, excellent machinability | Molds for demanding applications requiring a balance of strength and machinability |
Cobalt Chrome (CoCr) | Cobalt-chromium alloy | High wear resistance, excellent biocompatibility | Molds for wear-resistant components, medical implants (limited use due to higher cost) |
Tungsten | Pure tungsten | Extremely high melting point, high density | Molds for applications requiring high-temperature resistance, electrodes for welding (limited use due to high cost and difficulty in processing) |
Molybdenum | Pure molybdenum | High melting point, good thermal conductivity | Molds for applications requiring high-temperature resistance, heat sinks (limited use due to high cost) |
Please note: This table provides a general overview, and specific properties may vary depending on the manufacturer and powder grade.
This diverse selection of metal powders empowers mold manufacturers to tailor their creations to specific needs. From the exceptional corrosion resistance of Stainless Steel 316L to the high-temperature prowess of Inconel 625, EBM offers a material symphony for crafting superior molds.
Revolutionizing Mold Manufacturing
Now, let’s delve into the transformative ways EBM technology is revolutionizing mold manufacturing:
EBM technology can be used to manufacture components for injection molds:
- Cores and Cavities: EBM’s ability to produce intricate features allows for the creation of complex mold cores and cavities, previously unattainable with traditional methods. This translates to the production of highly detailed plastic parts with superior quality.
- Conformal Cooling Channels: Traditional cooling channels in injection molds can be restrictive. EBM shines in this arena, enabling the fabrication of conformal cooling channels that precisely follow the mold cavity’s contours. This significantly improves cooling efficiency, leading to faster cycle times, reduced warping, and superior part quality in injection molded products.
Imagine this: intricate channels snaking around a complex mold cavity, like a network of veins ensuring optimal temperature control. This is the power of conformal cooling channels made possible by EBM.
- Lightweight Molds: Certain metal powders, like Titanium Ti6Al4V, offer exceptional strength-to-weight ratios. By leveraging EBM with these materials, manufacturers can create lightweight molds that are easier to handle and maneuver, reducing overall production costs and improving ergonomics.
Think of it like this: a mold that performs like a heavyweight but feels like a featherweight. This advantage is particularly valuable for large or complex molds used in high-volume production environments.
EBM technology can be used to manufacture components for stamping molds:
- Mold Inserts: Stamping dies are subjected to immense pressure and wear. EBM allows for the creation of high-strength, wear-resistant mold inserts using materials like Maraging Steel 1.2709 and Tool Steel H13. These inserts extend the lifespan of stamping molds, leading to significant cost savings in the long run.
Imagine a mold insert that withstands the relentless pounding of a stamping press, like a shield deflecting a barrage of arrows. EBM-made inserts provide exceptional durability for demanding stamping applications.
- Complex Features: EBM’s ability to produce intricate geometries facilitates the creation of complex features in stamping dies, such as intricate bends and micro-textures. This opens doors for the production of innovative stamped parts with unique functionalities.
Think of it like this: EBM carves intricate details onto a stamping die with unparalleled precision, akin to a master engraver meticulously crafting a design. This enables the creation of highly functional and visually appealing stamped parts.
Beyond Injection and Stamping Molds: Diverse Applications of EBM
The transformative power of EBM extends beyond injection and stamping molds. Here are some additional applications:
- Blow Molds: EBM-manufactured blow mold cores can feature intricate surface details, leading to the production of high-quality blow molded parts with superior aesthetics and functionality.
- Compression Molds: EBM technology can be used to create compression mold components requiring exceptional thermal conductivity, such as cores for molding rubber products. Copper or copper alloys would be ideal choices for such applications due to their excellent heat transfer properties.
- Electroforming Molds: EBM-made mandrels can be used for electroforming processes, enabling the creation of complex and highly detailed molds for specialized applications.
This list is just a glimpse into the vast potential of EBM in mold manufacturing. As the technology matures and costs become more competitive, we can expect even wider adoption and groundbreaking advancements in this exciting domain.
Advantages and Considerations of EBM in Mold Manufacturing
EBM technology offers a plethora of advantages for mold manufacturers, but it’s also crucial to consider some key aspects:
Advantages:
- Design Freedom: EBM unlocks the potential for creating molds with intricate features and complex cooling channels, previously limited by traditional methods.
- Improved Part Quality: The high precision and accuracy of EBM lead to the production of molds that create superior quality plastic and metal parts with minimal defects.
- Production Efficiency: Conformal cooling channels enabled by EBM can significantly reduce cycle times in injection molding, leading to increased production output.
- Lightweight Molds: EBM allows for the creation of lightweight molds using specific metal powders, enhancing ergonomics and reducing production costs.
- Material Versatility: The diverse range of metal powders compatible with EBM caters to a wide spectrum of mold-making requirements.
Considerations:
- Cost: Currently, EBM technology can be more expensive compared to traditional methods. However, the cost is steadily decreasing, and the long-term benefits like improved part quality and production efficiency can offset the initial investment.
- Build Time: EBM builds parts layer by layer, which can lead to longer build times compared to some traditional methods. However, advancements in EBM technology are continuously working to reduce build times.
- Surface Finish: EBM-produced parts may require post-processing for a smoother surface finish, depending on the specific application.
The Verdict: EBM technology is a powerful tool that is rapidly transforming the landscape of mold manufacturing. While cost and build time remain considerations, the advantages in design freedom, part quality, and production efficiency make EBM a compelling choice for manufacturers looking to push the boundaries and achieve superior results.
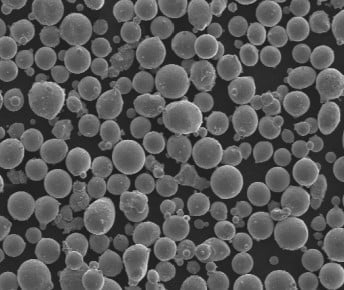
FAQ
Q: What are the typical sizes of molds that can be manufactured using EBM?
A: The build envelope of EBM machines varies depending on the manufacturer and model. However, EBM can typically produce molds ranging in size from a few centimeters to several hundred millimeters in each dimension. For larger molds, manufacturers may segment the design and build the mold in sections that are then assembled.
Q: How does the surface finish of EBM-produced molds compare to traditionally manufactured molds?
A: EBM-produced parts can have a slightly rougher surface finish compared to molds machined from solid metal blocks. This is because the layer-by-layer nature of EBM creates a stepped effect on the surface. However, the level of surface roughness can be mitigated through post-processing techniques like polishing or blasting, depending on the specific application requirements. In some cases, the inherent surface texture of EBM-made molds can be beneficial, such as in applications where it promotes better adhesion between the mold and the molded part.
Q: Is EBM environmentally friendly compared to traditional mold-making methods?
A: EBM offers some environmental advantages over traditional methods. The process operates in a vacuum chamber, minimizing emissions and airborne contaminants. Additionally, EBM utilizes a high degree of material efficiency, with minimal waste compared to subtractive manufacturing techniques like machining. However, the energy consumption of EBM can be higher compared to some traditional methods. As renewable energy sources become more prevalent, the environmental footprint of EBM is expected to improve further.
Q: What are the future prospects of EBM technology in mold manufacturing?
A: The future of EBM in mold manufacturing is brimming with exciting possibilities. As the technology matures, we can expect:
- Reduced Costs: Advancements in EBM technology and increased adoption are likely to drive down costs, making it more accessible to a wider range of mold manufacturers.
- Faster Build Times: Ongoing research and development efforts are focused on increasing the speed of EBM machines, further enhancing production efficiency.
- New Material Developments: The exploration of new metal powders specifically tailored for mold-making applications will continue to expand the capabilities of EBM.
- Integration with Design Software: Seamless integration of EBM technology with mold design software will streamline workflows and optimize designs for EBM production.
EBM is poised to become a mainstream technology in the mold-making industry, empowering manufacturers to create innovative and high-performance molds that push the boundaries of design and functionality.
In Conclusion
EBM technology is revolutionizing the world of mold manufacturing. Its ability to create intricate features, conformal cooling channels, and lightweight molds is transforming the way manufacturers approach mold design and production. While cost and build time remain considerations, the long-term benefits of EBM make it a compelling choice for those seeking to achieve superior results. As EBM technology continues to evolve, we can expect even greater advancements and a future where EBM becomes an indispensable tool for creating high-quality molds across diverse manufacturing applications.
Share On
MET3DP Technology Co., LTD is a leading provider of additive manufacturing solutions headquartered in Qingdao, China. Our company specializes in 3D printing equipment and high-performance metal powders for industrial applications.
Inquiry to get best price and customized Solution for your business!
Related Articles
About Met3DP
Recent Update
Our Product
CONTACT US
Any questions? Send us message now! We’ll serve your request with a whole team after receiving your message.
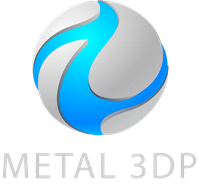
Metal Powders for 3D Printing and Additive Manufacturing