The difference between SLM technology and EBM technology
Table of Contents
Additive manufacturing (AM), also known as 3D printing, has revolutionized the way we create complex metal components. But within this exciting realm, two titans stand out: Selective Laser Melting (SLM) and Electron Beam Melting (EBM). Both utilize a powder bed fusion technique, but their internal workings reveal fascinating distinctions. Let’s delve into the intricate dance of metal, untangling the key differences between SLM and EBM.
The Difference in Heat Sources
Imagine a skilled sculptor meticulously shaping clay. In SLM, a high-powered laser acts as the sculptor’s tool. This laser beam melts targeted regions of the metal powder, fusing them together layer by layer to create the desired 3D object.
EBM takes a different approach. Here, a concentrated electron beam acts as the heat source. Within a vacuum chamber, the electrons are accelerated to near the speed of light, generating immense heat upon impact with the metal powder. This localized melting allows for precise shaping of the object.
Table: Comparison of Heat Sources in SLM and EBM
Feature | Selective Laser Melting (SLM) | Electron Beam Melting (EBM) |
---|---|---|
Heat Source | High-powered Laser Beam | Accelerated Electron Beam |
Operating Environment | Inert Gas Atmosphere | Vacuum Chamber |
Melting Mechanism | Localized Melting by Laser | Localized Melting by Electron Impact |
Analogy: Think of SLM as using a focused laser pointer to melt specific areas of chocolate chips, creating a design. EBM, on the other hand, is like using a high-powered electron microscope’s beam to precisely melt tiny points on a sugar cube, building the desired shape layer by layer.
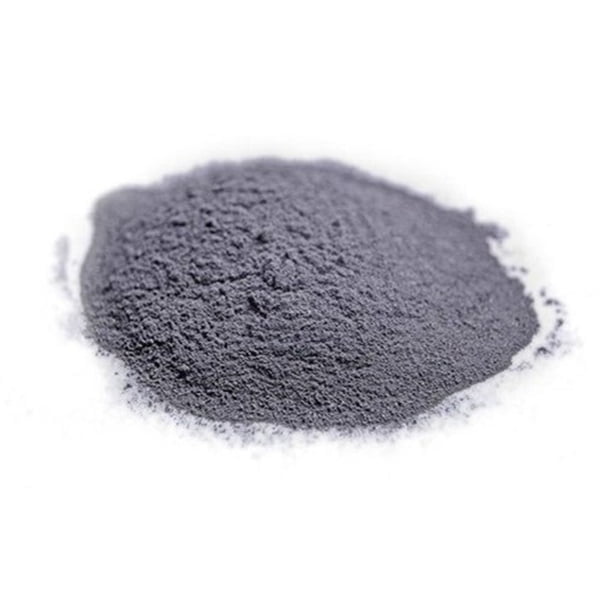
The Difference in Forming Environment
SLM operates in a shielded environment filled with inert gas, typically argon or nitrogen. This prevents oxidation, a detrimental process where the metal powder reacts with oxygen in the air, weakening the final product.
EBM, in contrast, thrives in a complete vacuum. This eliminates the risk of oxidation altogether and allows for processing of reactive metals like titanium, which are highly susceptible to oxidation in an air environment. However, maintaining a vacuum chamber adds complexity and cost to the EBM process.
Table: Comparison of Forming Environment in SLM and EBM
Feature | Selective Laser Melting (SLM) | Electron Beam Melting (EBM) |
---|---|---|
Operating Environment | Inert Gas Atmosphere (Argon, Nitrogen) | Vacuum Chamber |
Oxidation Risk | Moderate | Minimal |
Material Compatibility | Wide Range of Metals | Reactive Metals (e.g., Titanium) |
Metaphor: Imagine building a sandcastle on a breezy beach versus constructing one in a controlled, windless environment. SLM is like the beach build, where some sand particles might get blown away by the occasional gust. EBM is the controlled environment, ensuring a perfect sandcastle every time.
The Difference in Forming Accuracy
Both SLM and EBM boast impressive levels of detail and precision. However, subtle differences exist. SLM lasers can achieve finer focus points compared to electron beams. This translates to potentially sharper features and thinner walls in SLM-printed parts.
However, EBM offers superior layer-to-layer bonding due to the deeper penetration of the electron beam. This results in highly dense and isotropic (having the same properties in all directions) parts in EBM, making them ideal for applications requiring high structural integrity.
Table: Comparison of Forming Accuracy in SLM and EBM
Feature | Selective Laser Melting (SLM) | Electron Beam Melting (EBM) |
---|---|---|
Layer Thickness | Thinner Layers Possible | Slightly Thicker Layers |
Feature Resolution | Finer Feature Details | Superior Layer-to-Layer Bonding |
Part Isotropy | High | Excellent |
Analogy: Think of drawing a detailed picture with a sharp pencil (SLM) versus using a thicker paintbrush (EBM). The pencil allows for finer lines, but the paintbrush creates a more uniform and solid image.
The Difference in Forming Speed
Speed is a crucial factor in any manufacturing process. Here, EBM takes the lead. The high energy density of the electron beam allows for faster melting and solidification compared to the laser in SLM. This translates to quicker build times for EBM, especially for larger components.
However, factors like laser power and scan speed can influence the build rate in SLM. As technology advances, SLM’s build times are constantly decreasing, narrowing the gap with EBM.
Table: Comparison of Forming Speed in SLM and EBM
Feature | Selective Laser Melting (SLM) | Electron Beam Melting (EBM) |
---|---|---|
Build Speed | Generally Slower | Generally Faster, Especially for Large Parts |
Influencing Factors | Laser Power, Scan Speed | Electron Beam Energy Density |
Metaphor: Imagine building a Lego model piece by piece. SLM might be like meticulously placing each small brick, while EBM is like using a larger, pre-assembled Lego module, significantly reducing the build time.
The Difference in Material Applicability
When it comes to material selection, both SLM and EBM offer a wide range of possibilities. However, there are some key distinctions:
- SLM: Offers a broader compatibility with various metal powders, including stainless steel, tool steels, nickel alloys, aluminum alloys, and even some precious metals like gold and silver.
- EBM: Particularly excels at processing reactive metals like titanium and its alloys, tantalum, and zirconium. These metals are prone to oxidation in an air environment, making EBM’s vacuum chamber a perfect fit.
Table: Examples of Metal Powders for SLM and EBM
Metal/Alloy | Description | SLM Compatibility | EBM Compatibility |
---|---|---|---|
Stainless Steel (316L) | Versatile, corrosion-resistant steel | Excellent | Good |
Tool Steel (H13) | High-strength steel for tooling applications | Good | Limited |
Nickel Alloy (Inconel 625) | High-temperature resistant alloy | Excellent | Excellent |
Aluminum Alloy (AlSi10Mg) | Lightweight alloy with good castability | Excellent | Limited |
Titanium Alloy (Ti6Al4V) | Strong, lightweight alloy for aerospace applications | Limited | Excellent |
Tantalum | Biocompatible metal for medical implants | Limited | Excellent |
Zirconium | Corrosion-resistant metal for nuclear applications | Limited | Excellent |
Here are some specific metal powder examples to consider:
- SLM:
- Stainless Steel 17-4 PH: Offers high strength and good corrosion resistance, making it ideal for demanding applications like aerospace components.
- Cobalt Chrome (CoCr): Biocompatible material used for medical implants like hip replacements and knee joints.
- Inconel 718: High-strength, high-temperature nickel alloy used in jet engine components and turbine blades.
- EBM:
- Titanium Alloy (Ti-6Al-4V ELI): Extra Low Interstitial version of Ti6Al4V offering superior purity for medical implants.
- Hastelloy C-276: A nickel-chromium-molybdenum alloy known for its exceptional corrosion resistance in harsh chemical environments.
- Copper (Cu): Offers high thermal and electrical conductivity, making it suitable for heat sinks and electrical components.
Analogy: Imagine a buffet with various food options. SLM offers a wider selection of dishes (metals) to choose from, while EBM caters specifically to those with dietary restrictions (reactive metals) who need a controlled environment (vacuum chamber) to enjoy their meals.
Pros and Cons of SLM and EBM Technologies
Table: Comparison of Pros and Cons of SLM and EBM
Feature | Selective Laser Melting (SLM) | Electron Beam Melting (EBM) |
---|---|---|
Pros | Wide range of metal compatibility, good surface finish, potential for finer features | Faster build times for large parts, excellent layer-to-layer bonding, ideal for reactive metals |
Cons | Slower build times for larger parts, higher susceptibility to oxidation for certain metals, complex support structure removal | Limited material compatibility compared to SLM, higher upfront cost due to vacuum chamber requirement |
Choosing the Right Technology:
The decision between SLM and EBM hinges on your specific project requirements:
- Material: If your desired metal is highly reactive (e.g., titanium), EBM is the clear choice. For a wider material selection, SLM offers greater flexibility.
- Part Complexity: Both technologies can handle intricate geometries. However, if ultra-fine features are crucial, SLM might be a better fit.
- Build Speed: For large-scale projects, EBM’s faster build times can be advantageous.
- Cost: SLM generally has lower operating costs compared to EBM due to the absence of a vacuum chamber. However, factor in material cost and project turnaround time for a holistic analysis.
Conclusion
SLM and EBM are powerful additive manufacturing technologies, each with its own strengths and weaknesses. Understanding these differences empowers you to make informed decisions for your next project.
Here’s a final recap to solidify your knowledge:
- Think of SLM as a meticulous sculptor using a laser to precisely shape metal powder. It offers a wider material selection and excels at creating intricate details. However, build times can be slower, and some materials are more susceptible to oxidation.
- EBM, on the other hand, is like a high-powered furnace utilizing an electron beam to rapidly melt and fuse metal particles. It shines in processing reactive metals and boasts superior layer-to-layer bonding for high-strength parts. However, the vacuum chamber adds complexity and cost, and material compatibility is slightly narrower compared to SLM.
The future of metal additive manufacturing is bright. Both SLM and EBM are constantly evolving, with advancements in laser technology, powder development, and process optimization pushing the boundaries of what’s possible. As these technologies mature, we can expect even more intricate, robust, and innovative metal components to be created, shaping the future of various industries.
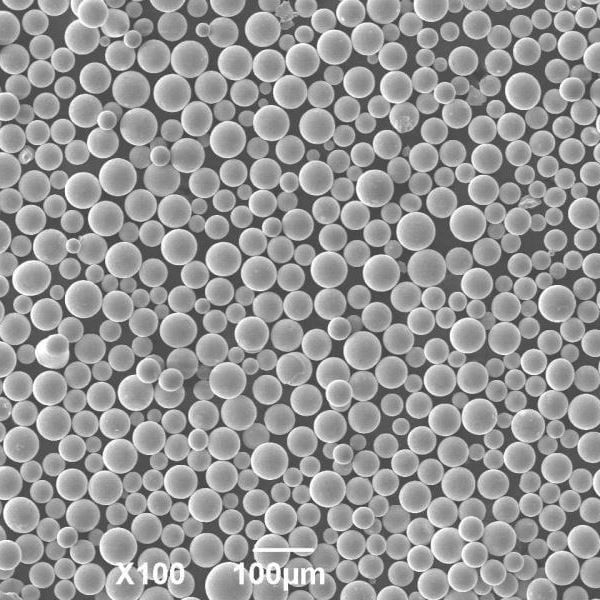
FAQ
1. Which technology is better, SLM or EBM?
There’s no one-size-fits-all answer. The best choice depends on your specific project requirements. Consider factors like:
- Material: SLM for wider selection, EBM for reactive metals.
- Part Complexity: Both handle complex geometries, SLM for ultra-fine features.
- Build Speed: EBM generally faster for large parts.
- Cost: SLM typically lower operating cost, consider material cost and turnaround time.
2. What are some applications of SLM and EBM?
- SLM: Aerospace components, medical implants, automotive parts, tooling and molds, jewelry.
- EBM: Aerospace components (especially for titanium parts), medical implants, chemical processing equipment, heat exchangers, dental implants.
3. Can SLM or EBM create fully functional parts?
Absolutely! Both technologies can produce high-density, near-net-shape components with excellent mechanical properties.
4. What are the limitations of SLM and EBM?
- SLM: Slower build speeds for larger parts, potential for residual stresses, support structure removal can be challenging.
- EBM: Limited material compatibility compared to SLM, higher upfront cost due to vacuum chamber, surface finish can be rougher than SLM.
5. Where can I learn more about SLM and EBM?
Numerous resources are available online and through professional organizations like the American Society for Testing and Materials (ASTM) and the Additive Manufacturing Users Group (AMUG).
By understanding the intricate dance between SLM and EBM, you can leverage the power of additive manufacturing to bring your next innovative metal project to life.
Share On
MET3DP Technology Co., LTD is a leading provider of additive manufacturing solutions headquartered in Qingdao, China. Our company specializes in 3D printing equipment and high-performance metal powders for industrial applications.
Inquiry to get best price and customized Solution for your business!
Related Articles
About Met3DP
Recent Update
Our Product
CONTACT US
Any questions? Send us message now! We’ll serve your request with a whole team after receiving your message.
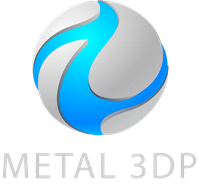
Metal Powders for 3D Printing and Additive Manufacturing