Factors for Choosing HIP Method
Table of Contents
Imagine a world where chronic hip pain becomes a distant memory. Where movement is smooth and effortless, and everyday activities regain their joy. This world is within reach thanks to advancements in hip implant technology, specifically Hot Isostatic Pressing (HIP). But with various HIP methods and metal powder options available, selecting the right one becomes crucial for a successful outcome.
This comprehensive guide delves into the factors influencing HIP method selection and explores a diverse range of metal powders used in the process. Buckle up, and let’s embark on a journey to understand the complexities and nuances of crafting the perfect hip implant for you.
Understanding Hot Isostatic Pressing (HIP)
HIP is a post-processing technique that transforms metal powders into high-performance components. Imagine a mold filled with metal powder particles – tiny, individual grains. During HIP, the mold is subjected to high pressure and temperature, causing the particles to fuse seamlessly. This eliminates internal voids and imperfections, resulting in a denser, stronger, and more reliable implant.
But the magic of HIP doesn’t stop there. Different methods and metal powders offer unique advantages and cater to specific surgical needs. Here’s what you need to consider:
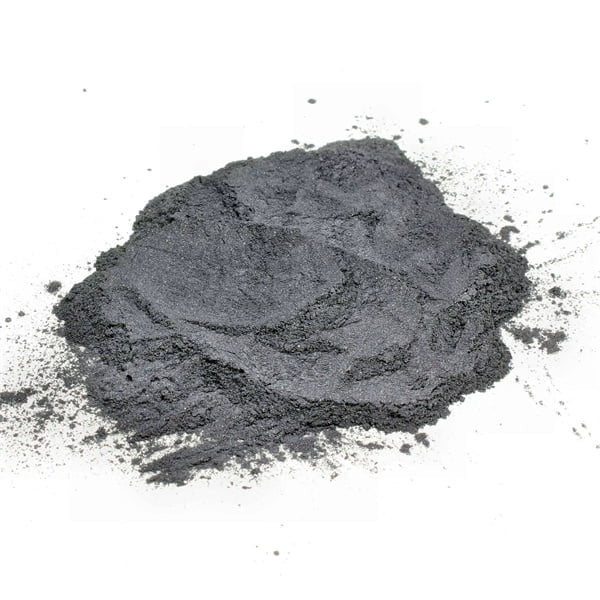
Factors Influencing HIP Method Selection
Choosing the optimal HIP method hinges on several key factors:
- The geometric shape of the final component: Complex geometries with intricate details benefit from methods that ensure uniform pressure distribution throughout the part. Conversely, simpler shapes may allow for more flexibility in the chosen method.
- What are the key mechanical properties (strength, ductility, conductivity) required for the final component?: Different methods can influence the final properties of the material. For instance, some methods prioritize strength, while others enhance fatigue resistance. Understanding the desired properties for the specific implant application is crucial.
- Material selection: The type of metal powder used plays a vital role. Each powder boasts distinct characteristics that influence the HIP process and final implant performance.
Metal Powders for HIP: A Diverse Palette for Crafting Implants
The world of metal powders for HIP is surprisingly diverse, offering a spectrum of options to suit various implant needs. Let’s delve into ten prominent choices:
Metal Powder | Description | Advantages | Considerations |
---|---|---|---|
Cobalt-Chrome (CoCr) | The workhorse of the industry, offering excellent biocompatibility, wear resistance, and mechanical strength. | Proven track record, readily available, versatile for various implant types. | Potential for metal ion release, higher cost compared to some alternatives. |
Titanium (Ti) | Biocompatible, lightweight, and corrosion-resistant, making it ideal for patients with allergies or weight concerns. | Offers a combination of strength and low weight, good osseointegration (bone integration). | May require specific HIP methods for optimal results, slightly higher cost than CoCr. |
Tantalum (Ta) | Offers exceptional biocompatibility and corrosion resistance, suitable for revision surgeries after failed implants. | Excellent bone in-growth properties, lower stiffness compared to CoCr, good for stress shielding concerns. | Higher cost compared to CoCr and Ti, limited availability of some powder variations. |
Nickel-Chromium (NiCr) | A cost-effective alternative to CoCr, with good wear resistance and mechanical properties. | Affordable, readily available. | Potential for allergic reactions in some patients, lower biocompatibility compared to CoCr and Ti. |
Molybdenum-Chromium (MoCr) | Offers superior wear resistance, particularly beneficial for younger, active patients. | Enhanced durability, good biocompatibility. | Higher cost compared to CoCr and Ti, requires specific HIP methods for optimal performance. |
Hydroxyapatite (HA) | A bioceramic material that promotes bone in-growth and osseointegration. | Excellent bone compatibility, facilitates faster healing. | Lower mechanical strength compared to metal alloys, may not be suitable for all implant types. |
Bioactive Glass (BG) | Another bioceramic option that encourages bone growth and offers antibacterial properties. | Enhanced bone bonding, potential for reduced infection risk. | Newer technology, limited clinical data compared to established options like HA. |
Nickel-Titanium (NiTi) | Offers unique shape-memory properties, allowing for minimally invasive surgical approaches. | Can conform to complex bone geometries, potentially reducing surgical trauma. | More complex manufacturing process, higher cost compared to traditional alloys. |
Composites (e.g., CoCr-HA) | Combine the strengths of different materials to create hybrid implants. | Tailored properties to address specific needs, improved bone in-growth with HA component. | Requires specialized processing techniques, limited availability compared to single-material options. |
Exploring the Advantages and Limitations of HIP Methods
Now that we’ve explored the diverse landscape of metal powders, let’s delve into the world of HIP methods themselves. Here, the choice hinges on factors like:
- Pressure and Temperature: Different methods utilize varying pressure and temperature combinations. Higher values generally result in denser materials but may come at the cost of increased processing time and energy consumption.
- Uniformity: Ensuring consistent pressure distribution throughout the mold is crucial for a uniform microstructure and optimal implant properties. Some methods excel at achieving this uniformity, particularly for complex geometries.
- Cost: The complexity and equipment requirements of each method influence the overall cost. Balancing cost-effectiveness with desired implant properties is vital.
Here’s a breakdown of some prominent HIP methods:
HIP Method | Description | Advantages |
---|---|---|
Conventional HIP (ConvHIP): The traditional method, utilizing high pressure and temperature in a sealed vessel. | Proven technology, readily available, suitable for various geometries. | May not achieve optimal uniformity for complex shapes, higher processing time and energy consumption compared to some newer methods. |
Cold Isostatic Pressing (CIP) + HIP: A two-step process where the powder is first compacted at room temperature (CIP) before HIP treatment. | Improves initial packing density, potentially leading to denser final product compared to ConvHIP. | Requires additional processing step, may not be necessary for all geometries. |
Hot Isostatic Pressing with Gas Assisted Densification (HIP-GAD): Utilizes an inert gas to penetrate the powder bed during HIP, enhancing densification. | Achieves higher density compared to ConvHIP, particularly beneficial for complex geometries. | More complex equipment setup compared to ConvHIP, potential for gas entrapment requiring additional degassing steps. |
HIP Method | Description | Advantages |
---|---|---|
Vacuum Assisted Hot Isostatic Pressing (VA-HIP): Combines HIP with vacuum to remove trapped gases before and during pressurization. | Minimizes gas entrapment, leading to improved material properties. | Requires specialized equipment, may be more expensive compared to ConvHIP. |
Direct Manufacturing (DM) – HIP: A hybrid approach where a 3D printed metal structure is infiltrated with a molten metal during HIP. | Enables creation of complex geometries with internal lattices, potentially improving implant performance. | Requires advanced 3D printing and HIP expertise, limited availability compared to traditional methods. |
The Intricate Dance Between Method and Material
The success of the HIP process hinges on the delicate interplay between the chosen method and the metal powder. Here’s how they influence each other:
- Powder morphology: The size, shape, and distribution of powder particles can impact the effectiveness of different HIP methods. For instance, finer powders may benefit from methods like HIP-GAD for optimal densification.
- Material properties: The melting point and flow characteristics of the metal powder influence the selection of pressure and temperature parameters during HIP.
Choosing the Right Combination: A Collaborative Effort
Selecting the ideal HIP method and metal powder combination is rarely a one-person job. Orthopaedic surgeons, implant manufacturers, and material scientists often collaborate to determine the optimal solution for each specific patient case. Factors like the patient’s age, activity level, and underlying medical conditions play a role in this decision-making process.
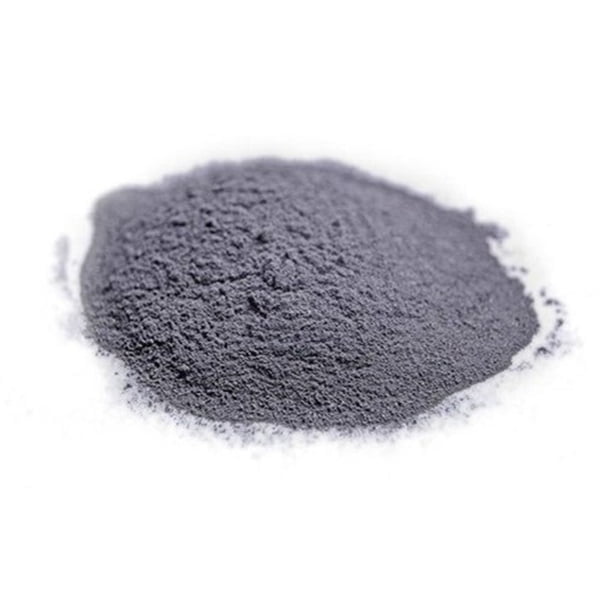
FAQ
Here are some commonly asked questions regarding HIP methods and metal powders:
FAQ | Answer |
---|---|
What is the strongest metal powder for hip implants? | There’s no single “strongest” option. Cobalt-Chrome offers excellent strength, while Molybdenum-Chromium prioritizes wear resistance. The choice depends on the specific implant application. |
Are there any risks associated with HIP? | Like any medical procedure, there are potential risks. However, modern HIP techniques are highly refined, and the benefits generally outweigh the risks. |
How long do hip implants made with HIP typically last? | The lifespan of a hip implant depends on various factors like material selection, patient activity level, and surgical technique. With proper care, modern HIP implants can last for 15-20 years or even longer. |
Conclusion
Choosing the right HIP method and metal powder is a crucial step in creating a durable, biocompatible, and long-lasting hip implant. By understanding the factors at play and the diverse options available, patients and medical professionals can work together to determine the optimal solution for a successful surgical outcome. Remember, this journey towards a pain-free future requires a collaborative effort, and the knowledge you’ve gained empowers you to actively participate in this decision-making process.
Share On
MET3DP Technology Co., LTD is a leading provider of additive manufacturing solutions headquartered in Qingdao, China. Our company specializes in 3D printing equipment and high-performance metal powders for industrial applications.
Inquiry to get best price and customized Solution for your business!
Related Articles
About Met3DP
Recent Update
Our Product
CONTACT US
Any questions? Send us message now! We’ll serve your request with a whole team after receiving your message.
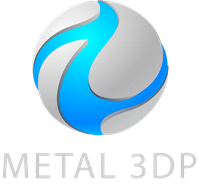
Metal Powders for 3D Printing and Additive Manufacturing