Gas Atomized Prealloyed Spherical Ti-6Al-4V
Table of Contents
Imagine a material that’s strong as steel, yet light as a feather. A metal that boasts exceptional biocompatibility, making it the perfect choice for implants that seamlessly integrate with the human body. This isn’t science fiction; it’s the reality of gas atomized prealloyed spherical Ti-6Al-4V powder.
In the world of metal additive manufacturing (AM), also known as 3D printing, powders reign supreme. But not all powders are created equal. Gas atomized prealloyed spherical Ti-6Al-4V stands out as a champion, offering a unique blend of properties that have revolutionized various industries.
This article delves deep into the world of gas atomized prealloyed spherical Ti-6Al-4V powder, exploring its composition, properties, applications, and the specific models that dominate the market. We’ll also unveil its advantages and limitations, equipping you with the knowledge to determine if this wonder material is the perfect fit for your next project.
Composition and Properties of Gas Atomized Prealloyed Spherical Ti-6Al-4V Powder
Composition Breakdown:
At the heart of gas atomized prealloyed spherical Ti-6Al-4V powder lies a specific blend of elements:
- Titanium (Ti): The primary constituent, renowned for its strength, corrosion resistance, and low weight.
- Aluminum (Al): Enhances strength and hardenability.
- Vanadium (V): Promotes fine grain structure and improves mechanical properties.
The nominal composition (by weight percentage) typically falls within this range:
- Titanium (Ti): 88.5% – 91.5%
- Aluminum (Al): 5.5% – 6.75%
- Vanadium (V): 3.5% – 4.5%
Property Powerhouse:
The unique combination of elements and the gas atomization process imbue this powder with a remarkable set of properties:
- High Strength-to-Weight Ratio: Boasting a density lower than steel but comparable strength, this powder makes it possible to create lightweight yet robust structures.
- Excellent Corrosion Resistance: Similar to pure titanium, this powder exhibits exceptional resistance to corrosion, making it ideal for applications exposed to harsh environments.
- Biocompatibility: The human body readily accepts titanium, making gas atomized prealloyed spherical Ti-6Al-4V powder a prime choice for medical implants.
- Superior Powder Flowability: The spherical shape and smooth surface of the particles ensure smooth and consistent flow during the AM process, leading to high-quality printed parts.
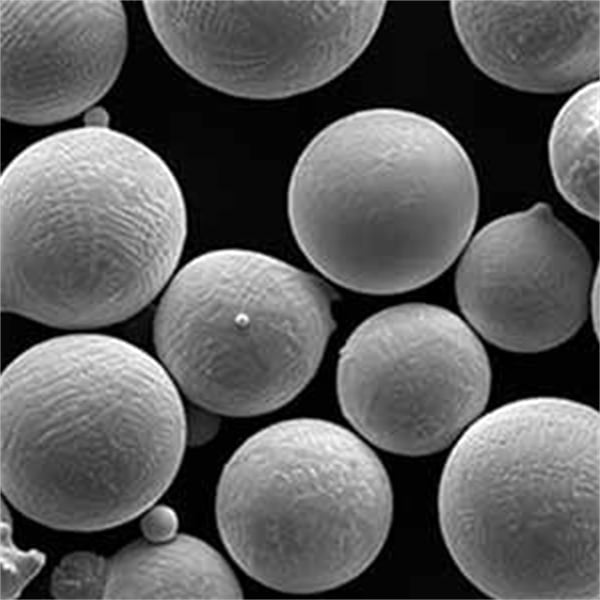
Applications of Gas Atomized Prealloyed Spherical Ti-6Al-4V Powder
The exceptional properties of gas atomized prealloyed spherical Ti-6Al-4V powder have opened doors to a vast array of applications across various industries. Let’s explore some key areas where this wonder material shines:
Aerospace and Defense:
- Lightweight Aircraft Components: The ability to create strong yet lightweight parts makes this powder ideal for aircraft structures, leading to improved fuel efficiency and increased payload capacity.
- Missile and Rocket Parts: Components requiring high strength-to-weight ratio and excellent corrosion resistance can be effectively manufactured using this powder.
Medical and Dental Applications:
- Biocompatible Implants: From bone screws and plates to dental implants, this powder finds extensive use due to its biocompatibility and excellent long-term performance in the human body.
- Custom Prosthetic Devices: The ability to 3D print intricate structures using this powder allows for the creation of personalized prosthetic devices that perfectly match a patient’s needs.
Automotive Industry:
- High-Performance Engine Parts: Components like connecting rods and pistons can be manufactured using this powder, leading to reduced weight and improved engine performance.
- Luxury Car Components: The combination of strength and aesthetics makes this powder ideal for creating lightweight yet robust components for high-end vehicles.
Consumer Goods:
- Sporting Goods: Lightweight and durable components for bicycles, golf clubs, and other sporting equipment can be effectively produced using this powder.
- Consumer Electronics: The ability to create complex and intricate structures opens doors for innovative applications in consumer electronics.
Beyond these sectors, gas atomized prealloyed spherical Ti-6Al-4V powder is making waves in various other industries, including:
- Chemical Processing
- Oil and Gas Exploration
- Jewelry
Popular Metal Powder Models: A Look at the Champions
The market boasts a diverse range of gas atomized prealloyed spherical Ti-6Al-4V powder models, each with its own unique characteristics. Here, we explore ten prominent models to help you navigate the options:
- APEX Ti-6Al-4V (AMPO):
- Renowned for its excellent flowability and packing density, leading to high-quality printed parts with minimal porosity.
- Offers a broad particle size distribution, catering to a variety of AM processes.
- Well-suited for applications demanding exceptional mechanical properties.
- LPW Ti-6Al-4V (LPW Technology):
- Known for its tight particle size distribution, resulting in consistent and predictable printing behavior.
- Certified to meet various aerospace industry standards, making it a trusted choice for demanding applications.
- A go-to option for users seeking consistent and reliable printing experiences.
- EOS Titanium Ti64 (EOS GmbH):
- Optimized for use with EOS AM systems, ensuring seamless compatibility and optimal printing performance.
- Available in a variety of particle sizes to cater to different layer thicknesses and desired surface finish.
- A popular choice for users invested in the EOS ecosystem.
- SLM Solutions Ti64 (SLM Solutions GmbH):
- Specifically formulated for use with SLM Solutions’ machines, offering a perfect match for their laser melting technology.
- Stringently controlled oxygen content ensures high ductility and toughness in the final printed parts.
- Ideal for users seeking a powder specifically tailored to SLM Solutions’ printers.
- Höganäs AM Titanium Ti6Al4V (Höganäs AB):
- Backed by a reputable brand known for high-quality metal powders, this model offers consistent performance and reliable results.
- Available in a wide range of particle sizes and flow characteristics to cater to diverse printing needs.
- A dependable option for users seeking a versatile and well-established powder.
- Materialise AM Ti6Al4V (Materialise NV):
- Developed by a company at the forefront of AM technology, this powder benefits from cutting-edge research and development.
- Offers excellent printability with minimal spatter and good surface finish.
- A strong choice for users seeking a powder from a company deeply invested in AM advancements.
- Proto Labs Ti-6Al-4V (Proto Labs Inc.):
- Geared towards rapid prototyping applications, this model prioritizes fast turnaround times with good printability.
- May not be ideal for applications requiring the absolute highest mechanical properties.
- A suitable option for users focused on rapid prototyping and quick design iterations.
- Additive Industries Ti6Al4V (Additive Industries B.V.):
- Specifically developed for use with Additive Industries’ Metal Additive Manufacturing (MAM) machines.
- Offers good flowability and packing density, leading to efficient powder utilization during printing.
- A perfect choice for users invested in the Additive Industries’ MAM platform.
- GfE Ti-6Al-4V (GfE Gesellschaft für Elektrometallurgie mbH):
- This model prioritizes high purity and low oxygen content, resulting in exceptional mechanical properties in the final printed parts.
- May have a slightly higher cost compared to some competitors.
- Ideal for users seeking the absolute best possible mechanical performance from their printed parts.
- Custom Engineered Powders (Various Suppliers):
- Several suppliers offer the ability to customize gas atomized prealloyed spherical Ti-6Al-4V powder to specific requirements.
- This can involve tailoring particle size distribution, oxygen content, or even adding additional alloying elements.
- The best option for users with unique needs or those seeking powders optimized for a specific application.
Choosing the Right Champion: Considerations for Selecting Your Powder
With such a diverse range of models available, selecting the perfect gas atomized prealloyed spherical Ti-6Al-4V powder for your project requires careful consideration. Here are some key factors to keep in mind:
- AM Process: Different AM processes have varying requirements for powder characteristics. Ensure the chosen powder aligns with the specific printing technology you’ll be using.
- Particle Size Distribution: The desired layer thickness and surface finish of your printed parts will influence the ideal particle size distribution.
- Mechanical Properties: Consider the specific strength, ductility, and other mechanical properties required for your application and choose a powder formulated to meet those demands.
- Cost: Powder cost can vary depending on the brand, specifications, and order quantity. Weigh the cost against the desired performance and project budget.
- Supplier Reputation: Choose a reputable supplier with a proven track record of quality and consistency in their powder production.
- Certification Standards: For critical applications, ensure the powder meets relevant industry standards (e.g., aerospace standards) to guarantee quality and performance.
Advantages and Limitations of Gas Atomized Prealloyed Spherical Ti-6Al-4V Powder
While gas atomized prealloyed spherical Ti-6Al-4V powder offers a compelling set of advantages, it’s essential to acknowledge its limitations to make informed decisions.
Advantages:
- Superior Mechanical Properties: The combination of titanium, aluminum, and vanadium delivers exceptional strength, toughness, and fatigue resistance.
- Lightweight Design: The low density of titanium translates to lightweight printed parts, ideal for applications demanding weight reduction.
- Excellent Corrosion Resistance: Similar to pure titanium, this powder boasts outstanding resistance to corrosion, making it suitable for harsh environments.
- Biocompatibility: The human body readily accepts titanium, making this powder a prime choice for medical implants with excellent long-term biocompatibility.
- Design Flexibility: AM allows for the creation of complex geometries that are difficult or impossible with traditional manufacturing techniques.
Limitations:
- Cost: Gas atomized prealloyed spherical Ti-6Al-4V powder can be more expensive compared to some conventional materials.
- Process Complexity: AM requires specialized equipment and expertise, leading to a higher barrier to entry compared to traditional manufacturing.
- Surface Roughness: While AM technology continues to evolve, 3D printed parts can exhibit a slightly rougher surface finish compared to some machined components.
- Post-processing Requirements: Depending on the application, 3D printed parts using this powder may require additional post-processing steps like heat treatment or surface finishing.
Making the Call: Is Gas Atomized Prealloyed Spherical Ti-6Al-4V Powder Right for You?
By understanding the composition, properties, applications, and available models of gas atomized prealloyed spherical Ti-6Al-4V powder, alongside its advantages and limitations, you’re well-equipped to make an informed decision.
Here are some scenarios where this wonder material might be the perfect fit:
- You require a high strength-to-weight ratio for components in the aerospace or automotive industry.
- Biocompatibility is paramount for medical implants or prosthetics.
- Design freedom and the ability to create complex geometries are crucial for your project.
However, if cost is a significant constraint or your application doesn’t necessitate the unique properties of this powder, alternative materials and manufacturing techniques might be more suitable.
The Future of Gas Atomized Prealloyed Spherical Ti-6Al-4V Powder: A Bright Horizon
The future of gas atomized prealloyed spherical Ti-6Al-4V powder is bright. As AM technology continues to advance, we can expect:
- Reduced Powder Costs: With advancements in production techniques and increased demand, the cost of this powder is expected to become more competitive.
- Finer Powders: The development of finer powders will enable the creation of even more intricate and detailed 3D printed parts.
- Tailored Properties: Advancements in powder metallurgy will allow for the creation of powders with even more precisely tailored properties for specific applications.
Gas atomized prealloyed spherical Ti-6Al-4V powder is more than just a material; it’s a gateway to innovation. By harnessing its potential, we can unlock a world of possibilities in various industries, pushing the boundaries of design and engineering.
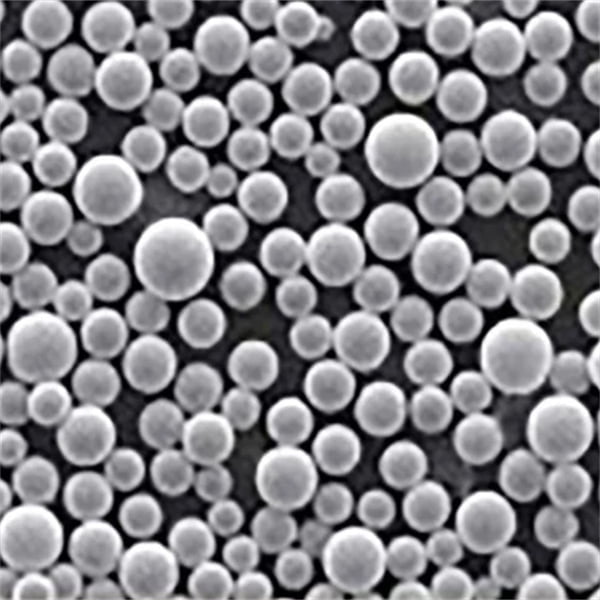
FAQ
Q: What are the typical sizes available for gas atomized prealloyed spherical Ti-6Al-4V powder?
A: The available particle sizes typically range from 15-50 microns (μm) to 100-175 μm. The specific size distribution will vary depending on the powder model and supplier.
Q: How is gas atomized prealloyed spherical Ti-6Al-4V powder stored?
A: This powder is hygroscopic, meaning it absorbs moisture from the air. Therefore, it’s crucial to store it in a sealed container under an inert atmosphere (e.g., argon) to prevent moisture absorption and oxidation.
Q: Can gas atomized prealloyed spherical Ti-6Al-4V powder be recycled?
A: Yes, unused powder can often be recycled and reused in the AM process. This helps to minimize waste and reduce overall production costs.
Q: Are there any safety precautions to consider when handling gas atomized prealloyed spherical Ti-6Al-4V powder?
A: Yes, handling this powder requires following safety protocols:
- Respiratory Protection: When handling the powder, wear a respirator with a high-efficiency particulate air (HEPA) filter to prevent inhalation of fine particles.
- Skin Protection: Wear gloves to avoid skin contact with the powder, as it can cause irritation in some individuals.
- Eye Protection: Safety glasses with side shields are recommended to protect your eyes from airborne particles.
- Flammable Considerations: While not readily flammable, titanium powder can ignite under specific conditions. Avoid sparks, open flames, and high temperatures when handling the powder.
- Proper Disposal: Do not dispose of unused powder in regular trash. Consult the safety data sheet (SDS) for proper disposal procedures.
Share On
MET3DP Technology Co., LTD is a leading provider of additive manufacturing solutions headquartered in Qingdao, China. Our company specializes in 3D printing equipment and high-performance metal powders for industrial applications.
Inquiry to get best price and customized Solution for your business!
Related Articles
About Met3DP
Recent Update
Our Product
CONTACT US
Any questions? Send us message now! We’ll serve your request with a whole team after receiving your message.
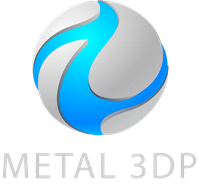
Metal Powders for 3D Printing and Additive Manufacturing
COMPANY
PRODUCT
cONTACT INFO
- Qingdao City, Shandong, China
- [email protected]
- [email protected]
- +86 19116340731