Gas Atomizer Machines
Table of Contents
Gas atomizer machines are crucial in various industries for creating fine metal powders, essential for applications like 3D printing, pharmaceuticals, and aerospace. If you’re delving into the world of metal powders and gas atomization, this guide is your comprehensive resource.
Overview of Gas Atomizer Machines
Gas atomizer machines use high-pressure gas to disperse molten metal into fine droplets, which then solidify into powder. These machines are vital in producing high-quality, uniform metal powders, essential for numerous high-tech applications.
How Gas Atomizer Machines Work
The process begins with melting the metal in a furnace. Once molten, the metal is forced through a nozzle and subjected to a high-velocity gas stream, breaking it into tiny droplets. These droplets cool and solidify as they fall into a collection chamber, forming a fine metal powder.
Key Features of Gas Atomizer Machines
- High Efficiency: Produces uniform and spherical metal powders.
- Versatility: Can handle a wide range of metals and alloys.
- Precision: Control over particle size distribution.
- Scalability: Suitable for both small-scale and industrial-scale production.
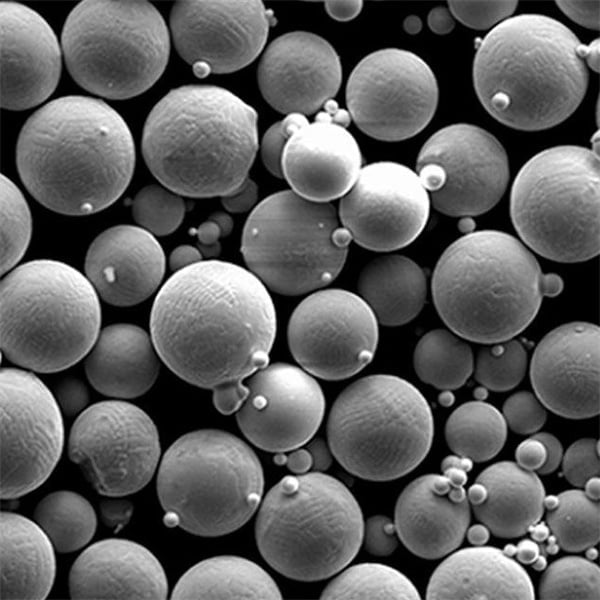
Types of Metal Powders Produced by Gas Atomizer Machines
Here’s a detailed look at some specific metal powder models produced by gas atomizer machines:
Metal Powder Model | Composition | Properties | Characteristics |
---|---|---|---|
Iron Powder | Pure iron or alloyed | High purity, magnetic properties | Spherical shape, high flowability |
Aluminum Powder | Pure aluminum | Lightweight, corrosion-resistant | Fine, spherical particles |
Copper Powder | Pure copper | High electrical and thermal conductivity | Uniform particle size distribution |
Titanium Powder | Ti-6Al-4V | High strength-to-weight ratio, biocompatibility | Suitable for aerospace and medical applications |
Nickel Powder | Ni-based alloys | High resistance to oxidation and corrosion | Used in superalloys for high-temperature applications |
Cobalt Powder | Co-Cr alloys | High wear resistance, biocompatibility | Ideal for dental and orthopedic implants |
Stainless Steel Powder | Various grades (e.g., 316L, 17-4PH) | Corrosion resistance, strength | Widely used in additive manufacturing |
Magnesium Powder | Pure magnesium | Lightweight, good strength | Used in aerospace and automotive industries |
Tungsten Powder | Pure tungsten or alloys | High density, high melting point | Used in heavy-duty applications |
Zinc Powder | Pure zinc | Good corrosion resistance, electrical conductivity | Used in galvanizing and battery applications |
Applications of Gas Atomizer Machines
Gas atomizer machines find applications across various industries due to their ability to produce high-quality metal powders with specific properties.
Application | Description |
---|---|
Additive Manufacturing | Metal powders used in 3D printing to create complex, high-strength parts |
Aerospace | Production of lightweight, high-strength components |
Medical Devices | Manufacture of biocompatible implants and prosthetics |
Electronics | High-purity powders for conductive pastes and components |
Automotive | Production of lightweight, high-strength parts for better fuel efficiency |
Pharmaceuticals | Fine powders for drug delivery systems |
Metal Injection Molding | Production of intricate and high-strength parts using fine metal powders |
Coatings | Metal powders used in thermal spraying to provide wear and corrosion resistance |
Battery Manufacturing | High-purity powders used in battery electrodes |
Welding and Soldering | Fine metal powders used in the production of welding and soldering materials |
Specifications, Sizes, Grades, and Standards
When selecting metal powders produced by gas atomizer machines, it’s essential to consider specifications, sizes, grades, and standards to ensure compatibility with your specific application.
Metal Powder | Particle Size (µm) | Grade | Standard |
---|---|---|---|
Iron Powder | 10-100 | FE-123 | ASTM B213 |
Aluminum Powder | 1-75 | AL-101 | ISO 8068 |
Copper Powder | 5-45 | CU-99.9 | ASTM B170 |
Titanium Powder | 15-45 | TI-6Al-4V | ASTM F2924 |
Nickel Powder | 10-75 | Ni-201 | ASTM B330 |
Cobalt Powder | 15-53 | CoCrMo | ISO 5832-12 |
Stainless Steel Powder | 10-45 | 316L, 17-4PH | ASTM F3184 |
Magnesium Powder | 20-60 | Mg-90 | ASTM B243 |
Tungsten Powder | 1-100 | W-1 | ASTM B777 |
Zinc Powder | 5-50 | Zn-99.9 | ASTM B860 |
Suppliers and Pricing Details
Finding the right supplier for your metal powders is crucial. Here are some key suppliers and their pricing details:
Supplier | Metal Powder | Price (per kg) | Notes |
---|---|---|---|
AP&C | Titanium Powder | $450 | High-quality powders for aerospace |
Höganäs | Iron Powder | $8 | Extensive range of iron and steel powders |
Sandvik | Stainless Steel Powder | $50 | Customizable powders for additive manufacturing |
Praxair | Nickel Powder | $200 | High-purity powders for superalloys |
Valimet | Aluminum Powder | $30 | High-sphericality aluminum powders |
AMETEK | Cobalt Powder | $150 | Specialty powders for medical applications |
GKN Powder Metallurgy | Copper Powder | $25 | Powders for electronics and welding |
Tekna | Magnesium Powder | $120 | High-purity magnesium powders |
H.C. Starck | Tungsten Powder | $500 | Powders for heavy-duty applications |
Granutools | Zinc Powder | $20 | Fine powders for battery applications |
Comparing Gas Atomizer Machines: Pros and Cons
Different gas atomizer machines offer various advantages and limitations. Let’s compare some key aspects:
Aspect | Advantages | Limitations |
---|---|---|
Efficiency | High yield of uniform powders | Requires high energy consumption |
Versatility | Can handle a wide range of metals | Some machines may be limited to specific alloys |
Particle Size Control | Precise control over particle size distribution | Requires precise operational control |
Cost | Lower operational costs compared to other methods | High initial investment |
Maintenance | Generally low maintenance | Specialized components can be expensive to replace |
Scalability | Suitable for both small and large scale production | Larger machines may require significant space |
In-depth Look at Specific Metal Powder Models
1. Iron Powder
Composition and Properties: Iron powders typically come in pure or alloyed forms, with high purity being a critical factor. They are magnetic, which makes them suitable for applications like magnetic coatings and components.
Applications: Iron powders are widely used in automotive parts, magnetic materials, and as a filler material in plastics.
Characteristics: They have a spherical shape and high flowability, making them easy to handle and process.
2. Aluminum Powder
Composition and Properties: Aluminum powders are known for their lightweight and corrosion-resistant properties. These powders are usually fine and spherical, which enhances their performance in various applications.
Applications: Used extensively in the aerospace and automotive industries for making lightweight, strong components.
Characteristics: Fine particle size with high uniformity, which ensures consistent performance in manufacturing processes.
3. Copper Powder
Composition and Properties: Copper powders offer high electrical and thermal conductivity, making them ideal for electronic applications.
Applications: Commonly used in conductive inks, electronic components, and thermal management systems.
Characteristics: These powders have a uniform particle size distribution, which is crucial for applications requiring precise conductivity.
4. Titanium Powder
Composition and Properties: Titanium powders, especially Ti-6Al-4V, are known for their high strength-to-weight ratio and biocompatibility.
Applications: Widely used in aerospace, medical implants, and additive manufacturing due to their excellent properties.
Characteristics: Suitable for creating high-strength, lightweight components with complex geometries.
5. Nickel Powder
Composition and Properties: Nickel powders are used for their high resistance to oxidation and corrosion, particularly in high-temperature environments.
Applications: Essential in producing superalloys for turbine engines and other high-stress components.
Characteristics: These powders ensure the durability and longevity of components exposed to extreme conditions.
6. Cobalt Powder
Composition and Properties: Cobalt powders, especially Co-Cr alloys, are prized for their high wear resistance and biocompatibility.
Applications: Ideal for dental and orthopedic implants due to their excellent mechanical properties and biocompatibility.
Characteristics: High wear resistance and excellent performance in biomedical applications.
7. Stainless Steel Powder
Composition and Properties: Stainless steel powders come in various grades, such as 316L and 17-4PH, offering corrosion resistance and strength.
Applications: Extensively used in additive manufacturing to produce complex, high-strength parts.
Characteristics: These powders provide the necessary properties for producing durable and corrosion-resistant components.
8. Magnesium Powder
Composition and Properties: Magnesium powders are lightweight with good strength, making them suitable for applications where weight reduction is critical.
Applications: Predominantly used in aerospace and automotive industries for lightweight components.
Characteristics: These powders offer a good balance between weight and strength, enhancing performance in demanding applications.
9. Tungsten Powder
Composition and Properties: Tungsten powders are known for their high density and high melting point, which make them suitable for heavy-duty applications.
Applications: Used in industries requiring materials that can withstand extreme conditions, such as in heavy machinery and aerospace.
Characteristics: High-density powders with excellent resistance to extreme temperatures and mechanical wear.
10. Zinc Powder
Composition and Properties: Zinc powders are valued for their good corrosion resistance and electrical conductivity.
Applications: Commonly used in galvanizing, battery manufacturing, and as an additive in various chemical processes.
Characteristics: These powders offer reliable performance in applications where corrosion resistance and conductivity are essential.
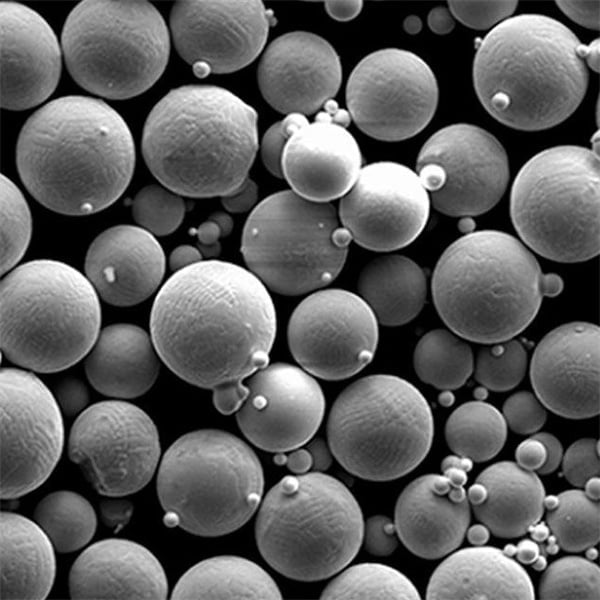
Advantages of Gas Atomizer Machines
Gas atomizer machines provide several significant advantages that make them a preferred choice in the production of metal powders.
- Uniform Particle Size Distribution: Achieves high uniformity in particle size, which is crucial for consistent performance in various applications.
- High Purity: Produces high-purity metal powders, essential for applications requiring specific material properties.
- Versatility: Capable of handling a wide range of metals and alloys, making them suitable for diverse industries.
- Scalability: Suitable for both small-scale and industrial-scale production, allowing flexibility in manufacturing processes.
- Efficiency: Provides high yield and efficiency, reducing waste and operational costs.
Disadvantages of Gas Atomizer Machines
Despite their many advantages, gas atomizer machines also have some limitations that should be considered.
- High Initial Investment: Requires significant upfront capital investment, which can be a barrier for smaller operations.
- Energy Consumption: High energy consumption during the atomization process can lead to increased operational costs.
- Maintenance: Specialized components can be expensive to replace, leading to higher maintenance costs.
- Space Requirements: Larger machines require substantial space, which can be a constraint in limited production environments.
FAQ
Question | Answer |
---|---|
What is a gas atomizer machine? | A machine that uses high-pressure gas to disperse molten metal into fine droplets, forming metal powders. |
What metals can be atomized? | Various metals, including iron, aluminum, copper, titanium, nickel, cobalt, stainless steel, magnesium, tungsten, and zinc. |
What are the applications of metal powders? | Applications range from additive manufacturing, aerospace, medical devices, electronics, automotive, to pharmaceuticals. |
What are the advantages of using gas atomizer machines? | High efficiency, uniform particle size distribution, high purity, versatility, and scalability. |
What are the disadvantages of gas atomizer machines? | High initial investment, energy consumption, maintenance costs, and space requirements. |
How to select the right metal powder? | Consider the composition, particle size, grade, and specific application requirements. |
Who are the key suppliers of metal powders? | Suppliers include AP&C, Höganäs, Sandvik, Praxair, Valimet, AMETEK, GKN Powder Metallurgy, Tekna, H.C. Starck, and Granutools. |
What are the costs associated with metal powders? | Prices vary by metal and supplier, ranging from $8 to $500 per kg depending on the type and quality of the powder. |
Conclusion
Gas atomizer machines play a pivotal role in modern manufacturing, enabling the production of high-quality metal powders essential for a wide array of applications. Whether you’re in aerospace, automotive, medical, or electronics industries, understanding the intricacies of gas atomization and selecting the right metal powders can significantly impact your production efficiency and product quality. With advancements in technology and a growing range of applications, gas atomizer machines are set to become even more integral to the manufacturing landscape.
Share On
MET3DP Technology Co., LTD is a leading provider of additive manufacturing solutions headquartered in Qingdao, China. Our company specializes in 3D printing equipment and high-performance metal powders for industrial applications.
Inquiry to get best price and customized Solution for your business!
Related Articles
About Met3DP
Recent Update
Our Product
CONTACT US
Any questions? Send us message now! We’ll serve your request with a whole team after receiving your message.
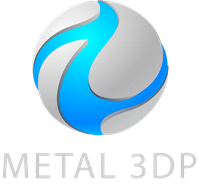
Metal Powders for 3D Printing and Additive Manufacturing