Hastelloy Powders
Table of Contents
Hastelloy is a registered trademark referring to a series of nickel-based superalloys that are known for their strength, durability, and corrosion resistance. Hastelloy powders are powders made from various Hastelloy alloys that are used in powder metallurgy and additive manufacturing processes.
Overview of Hastelloy Powders
Hastelloy powders provide exceptional high-temperature strength, outstanding resistance to oxidation and corrosion, and good fabricability. They are ideal for applications exposed to extreme environments.
Some of the key properties and characteristics of Hastelloy powders include:
- High strength and hardness even at extreme temperatures
- Excellent corrosion resistance in a wide range of aggressive media
- Good weldability and fabricability
- Oxidation resistance at high temperatures
- Available in various particle sizes tailored for different applications
- Can be used in various powder metallurgy techniques as well as additive manufacturing
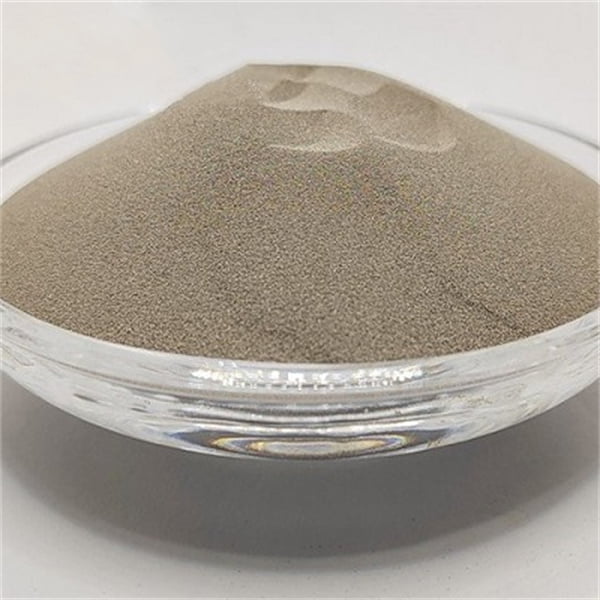
Types of Hastelloy Powders
Type | Composition | Key Characteristics |
---|---|---|
Hastelloy C276 | Nickel, chromium, molybdenum | Excellent corrosion resistance especially in oxidizing and reducing environments. Good fabrication characteristics. |
Hastelloy X | Nickel, chromium, iron, molybdenum | Outstanding high temperature strength. Excellent oxidation and corrosion resistance up to ~1200°C. Weldable. |
Hastelloy N | Nickel, chromium, molybdenum, iron | Resistant to nitric acid, nuclear irradiation. Higher strength than Hastelloy C. |
Hastelloy B3 | Nickel, molybdenum | Excellent resistance to reducing acids like hydrochloric acid even at elevated temperatures. |
Hastelloy G35 | Nickel, chromium, molybdenum | Better overall corrosion rates compared to other Hastelloys. Good pitting and crevice corrosion resistance. |
Applications and Uses of Hastelloy Powders
Area | Example Applications |
---|---|
Chemical processing | Reactors, vessels, pipes, pumps, valves exposed to corrosive chemicals at high temperatures |
Petrochemical | Crackers, reformers, tubing, transferring lines for various hydrocarbon processing |
Pollution control | Scrubbers, flue gas desulfurization systems, incinerators |
Aerospace | Engine components, aircraft ducting, brazing alloys |
Automotive | Exhaust system components, fuel system parts |
Biomedical | Implants, surgical instruments |
Hastelloy Powder Specifications
Parameter | Details |
---|---|
Alloy Grade | Most common grades: B3, C276, G30, N, X |
Particle shape | Spherical, irregular |
Particle size | Laser, plasma processes: 15-45 μm ;Binder jet: 45-150 μm |
Apparent density | Typically 2.5-4 g/cc |
Flow rates | >25 s/50 g |
Manufacturing standards | ASTM B213, AMS 2441, ASTM F3049 |
Hastelloy Powder Suppliers
Supplier | Particle Sizes | Alloy Grades |
---|---|---|
Supplier 1 | 10-75 μm | B3, C276, N, X |
Supplier 2 | 20-63 μm | B3, C276 |
Supplier 3 | 15-45 μm | C, C276, G30, G35 |
Typical pricing ranges from $50/kg for standard alloys and sizes to $200/kg for special grades. Lower prices are available for bulk orders.
Comparative Analysis of Hastelloy Powders
Parameter | Hastelloy B3 | Hastelloy X | Hastelloy N |
---|---|---|---|
Oxidation resistance | Medium | Excellent | Good |
Abrasion resistance | Good | Medium | Excellent |
Fabrication | Excellent | Medium | Medium |
Availability | High | Medium | Low |
Cost | Low | High | Very high |
Advantages of Hastelloy Powders
- Withstand extremely corrosive environments
- Retain strength and hardness at elevated temperatures
- Easy to fabricate using various powder metallurgy techniques
- Components have excellent finished surface
- Excellent value considering performance benefits
- Can be used to repair and recondition damaged parts
Limitations of Hastelloy Powders
- Premium pricing of certain grades and alloys
- Limited number of suppliers globally
- Lower maximum operating temperature than some superalloys
- Requires dedicated storage and handling equipment
- Susceptible to some forms of localized corrosion
Hastelloy Powder Composition
As outlined before, Hastelloy powders are part of a family of nickel-based superalloys. Their unique properties come from careful selection of alloying elements.
Key Alloying Elements
- Nickel – Makes up the matrix and provides corrosion resistance. Content 50-65 wt%.
- Chromium – Solid solution strengthener. Enhances oxidation resistance. Typical 12-22% Cr.
- Molybdenum – Major contributor to corrosion resistance properties. 8-30% Mo.
- Iron – Cost saver. Adjusted based on properties needed. At most ~5% Fe.
- Cobalt – Added in some varieties enhance strength. Up to 2% Co.
- Tungsten – Further improves high temperature capabilities. ~4% W.
- Manganese – Deoxidizer during melting. ~1% Mn.
Small amounts of carbon, silicon, sulfur, boron, lead may be present. The balance is nickel plus incidental impurities.
The various Hastelloys differ only in the relative proportions of the alloying elements used. By optimizing the composition, powder producers can maximize a specific desirable quality.
Hastelloy Powder Characteristics
Hastelloy powders provide an exceptional combination of high strength, environmental stability, fabricability, and value. Some salient characteristics include:
Mechanical Properties
- Tensile strength ranging from 550 MPa to over 1400 MPa
- Yield strength 400 MPa to 1200 MPa
- Elongation 10% to 60% in high purity alloys
- Young’s modulus 150-220 GPa
- Melting point 1290°C to 1427°C
Physical Properties
- Density 7.9 to 9.8 g/cm<sup>3</sup>
- Specific heat capacity 0.1 – 0.16 cal/g/°C
- Thermal conductivity around 11 W/m-K
Environmental Resistance
- Retain ductility and toughness at cryogenic temperatures
- Excellent corrosion resistance in many inorganic acids, organic acids, salts
- High resistance to pitting, crevice corrosion and stress corrosion cracking
- Stable and protective oxide scale formation enhances oxidation resistance
These impressive characteristics of Hastelloy powders make them suitable for the most demanding applications. Their unique balance of fabricability and environmental resistance facilitates their usage across diverse industries.
Applications and Uses of Hastelloy Powders
Here are some of the major application areas and examples of where Hastelloy powders are used to manufacture high-performance components using various powder metallurgy techniques:
Chemical Processing Industry
- Reactors and vessel linings
- Condensers and heat exchangers
- Pipes, pumps, valves transporting acids and solvents
- Scrubbers and components handling flue gases
**Petroleum Refining Industry **
- Crackers and reformers
- Heat exchanger tubing
- Transfer lines for fuels and corrosive products
Pollution Control Applications
- Flue gas desulfurization system components
- Scrubber internals and slurry piping
- Incinerators and thermal oxidizers
Aerospace Industry
- Aircraft ducting and engine components
- Rocket motor casings
- Brazing alloys and filler material
Automotive Industry
- Exhaust system components and manifolds
- Fuel system parts like injector bodies
Biomedical Sector
- Surgical tools and medical instruments
- Implants and prosthesis
Hastelloys powders have been instrumental in enabling extreme performance in some of the most harsh and challenging environments across these industries. Their unique capabilities have facilitated major advancements and process intensifications over the years.
Specifications of Hastelloy Powders
Hastelloy powder products meant for industrial usage need to satisfy certain criteria related to composition, characteristics and quality checks.
Alloy Grade Specifications
Hastelloys have several alloy variants like B3, X, C276 etc. used for different applications. The permissible compositional limits for major elements are given below for common grades:
Alloy | Ni wt% | Cr wt% | Fe wt% | Mo wt% | W wt% | Co wt% | Mn wt% | Si wt% |
---|---|---|---|---|---|---|---|---|
Hastelloy C276 | Balance | 14.5-16.5 | 4-7 | 15-17 | – | – | <1 | <0.08 |
Hastelloy B3 | Balance | 28-31 | 2.5 max | 4-6 | – | 1 max | <0.5 | <0.5 |
Hastelloy X | Balance | 20.5-23.5 | 17-20 | 8-10 | – | – | <1 | <0.5 |
Hastelloy N | Balance | 14.5-17 | 6-10 | 16-18 | – | – | <1.0 | <0.5 |
Particle Characteristics
Parameter | Range/Details |
---|---|
Particle morphology | Predominantly spherical, some irregular shaped particles acceptable |
Apparent density | Typically 2.5 – 4 g/cc |
Tap density | Up to 80% higher than apparent density |
Flow rates | >25 s/50 g ensures good powder flow |
Particle size distribution | Depends on application, usually 10-150 μm |
Manufacturing Standards
Common standards specifying requirements for metal powders for additive manufacturing:
- ASTM B213: Standard for Nickel and Nickel Alloy Powder
- AMS 2441: Nickel Alloy Powders Classification and Composition
- ASTM F3049: Standard Guide for Characterizing Particles Used in Additive Manufacturing
Quality Checks
- Chemical composition using OES or XRF
- Particle size distribution – sieve analysis
- Apparent/tap density measurement
- Powder flow rates – Hall flowmeter
- Microscopy for particle morphology
- Sampling as per ASTM B215
Well characterized Hastelloy powders satisfying these parameters provide consistency and high quality components in powder metallurgy processes.
Hastelloy Powder Suppliers
Some of leading global suppliers of Hastelloy powders for industrial manufacturing include:
Supplier 1
- Available Grades: B3, C276, N, X
- Particles sizes: 10 – 75 μm
- Shapes: Predominantly spherical
- Manufactures using gas atomization process
- Serves industries like chemical processing, oil & gas, automotive
Supplier 2
- Common Grades: B3, C276
- Particle range: 20 – 63 μm
- Apparent density ≥ 2.5 g/cc
- Made by plasma atomization technique
- Caters to aerospace, medical, and tooling applications
Supplier 3
- Alloys: Hastelloy C, C276, G30, G35
- Particle size distribution: 15 – 45 μm
- Highly spherical powder morphology
- Specializes in customized alloys and particle sizes
- Exports to additive manufacturers across the world
These leading producers use advanced powder making techniques to ensure reliable supply of high purity Hastelloy powders tailored for additive manufacturing processes.
Pricing for Hastelloy Powders
Cost Breakup
Hastelloy powder prices depend on:
- Base material cost – nickel is the most expensive
- Alloy complexity – higher alloying additions increase cost
- Stringent quality requirements
- Special particle characteristics
- Lower production volumes
- Processing and handling costs
Premium grades and special orders cost more owing to raw material costs and lower production scale. Commodity alloys and standard particle sizes are cheaper.
Price Ranges
Type | Price per kg |
---|---|
Standard alloys, standard particle sizes | $50 – $100 |
Special alloys, customized particles | $100 – $250 |
Research/small trial quantities | Can be > $200/kg |
Volume discounts available on bulk orders. Large OEMs get up to 30-40% lower prices. Overall Hastelloy powder prices have been declining gradually over the years owing to higher adoption and competition.
Price Drivers
Factors decreasing prices:
- Greater adoption and higher production volumes
- Process improvements bringing down metal powder costs
- Increasing number of suppliers and resulting competition
Factors increasing prices:
- Very specialized alloys requiring expensive raw materials
- Need for customized particle sizes and distributions
- Stringent aerospace or medical sector requirements
- Overall inflation and rising energy prices
Comparative Analysis of Various Hastelloy Powders
Hastelloys encompass a variety of alloys tailored to perform exceptionally well under certain conditions. A comparative analysis is provided below:
Parameter | Hastelloy B3 | Hastelloy X | Hastelloy N |
---|---|---|---|
Oxidation resistance | Medium | Excellent | Good |
Thermal stability | Up to 1095°C | Up to ~1200°C | Up to ~1100°C |
Fabricability | Excellent | Medium | Medium |
Corrosion resistance | Best against HCl, | Versatile resistance | Best against nitric acid |
Cost | Low | High | Very High |
Availability | High | Medium | Low |
Uses | Heat exchangers, chemical reactors | Aerospace components | Nuclear applications |
Summary
- Hastelloy B3 provides a cost-effective solution for handling hot corrosive media owing to easy fabrication.
- Hastelloy X is preferred for the highest temperature capabilities though relatively expensive.
- Hastelloy N gives unmatched performance against concentrated nitric acid despite its very high cost.
The selection depends on the operating environment and performance requirements of the application versus budget constraints.
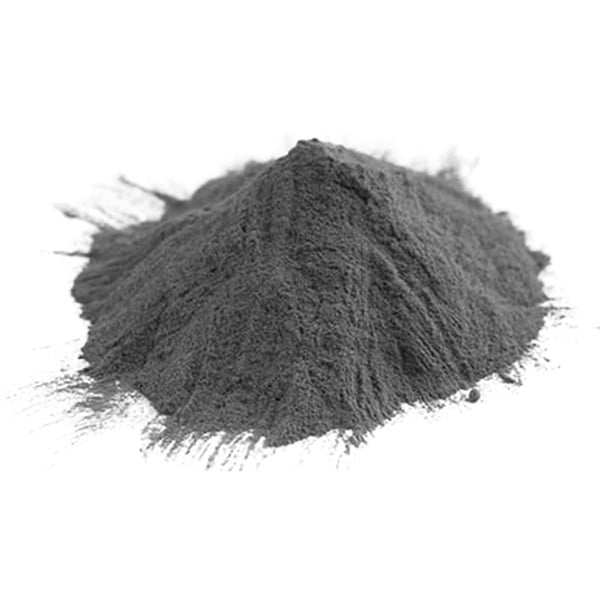
Advantages and Limitations of Hastelloy Powders
Benefits
- Withstand extremely corrosive environments
- Retain hardness and strength at elevated temperatures
- Components have excellent surface finish
- Used for repairs and upgrades of damaged parts
- Special grades available for niche applications
- Easy to process into complex shapes compared to wrought alloys
Potential Drawbacks
- More expensive than steel powders
- Limited number of global suppliers
- Not suited for very high temperature applications
- May still undergo localized corrosion types
- Dedicated handling systems needed to prevent contamination
Mitigation Strategies
- Use cheaper grades like B3 where possible
- Re-use scrap powder to reduce material costs
- Opt for wrought forms for less critical applications
- Use protective coatings in highly corrosive media
- Implement rigorous powder handling and storage protocols
With sound design and proper practices, limitations posed by Hastelloy powders can be effectively mitigated to leverage their significant benefits.
FAQ
Why choose Hastelloy powders over conventional wrought forms of the same alloys?
Hastelloy powders provide greater design flexibility compared to wrought products like sheets, bars or fittings. Components with complex geometries can be manufactured easily using powder metallurgy techniques. This enables significant part consolidation and performance improvements not feasible through standard fabrication means.
What are some examples of niche applications where Hastelloy powders provide unique capabilities over competitive materials?
Some niche applications where Hastelloy powders outperform other alloys:
- Glass moulds with exceptional surface finish and longevity
- Components of nuclear reactors resisting radioactive exposure
- High performance auto racing car parts operating at extreme temperatures
- Portable chemical process equipment parts exposed to harsh environments
- Biomedical instruments and implants
What key steps are involved in qualifying new Hastelloy powder alloys for specialized industrial applications?
Key qualification steps when validating new Hastelloy powder alloys:
- Computer simulation of expected corrosion rates and thermal processes
- Small scale lab corrosion testing for chemical compatibility
- Initial trial runs and sampling to validate composition
- Stringent composition checks using advanced microanalysis techniques
- Measurement of particle characteristics relevant to application
- Testing powder flowability and bulk density
- Investigation of optimal compaction and sintering parameters
- Fabrication of test coupons or prototype parts
- Exposing samples to operating environments on bench-scale
- Final adjustments of composition within specification limits
Extensive testing and characterization is performed to prove fitness for purpose before granting final product approval.
Is it advisable to use Hastelloy powders beyond their recommended maximum operating temperatures for specialized applications?
Using Hastelloy powders above recommended temperature limits is highly risky and not advisable. Their high-temperature strength, creep resistance and corrosion allowances rapidly degrade beyond certain thresholds leading to sudden failures.
Share On
MET3DP Technology Co., LTD is a leading provider of additive manufacturing solutions headquartered in Qingdao, China. Our company specializes in 3D printing equipment and high-performance metal powders for industrial applications.
Inquiry to get best price and customized Solution for your business!
Related Articles
About Met3DP
Recent Update
Our Product
CONTACT US
Any questions? Send us message now! We’ll serve your request with a whole team after receiving your message.
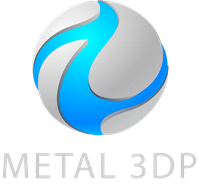
Metal Powders for 3D Printing and Additive Manufacturing