High Density Tungsten Powder
Table of Contents
High density tungsten powder possesses the greatest density among all metallic powders owing to tungsten’s extraordinarily high intrinsic density approaching that of gold. This unique attribute allows advanced design of compact, weight-efficient components across diverse sectors harnessing heavy powder pressing and sintering methodologies.
Overview of tungsten powder
With a density of 19.3 g/cm3 in solid form, tungsten packs immense weight into a tiny volume. By virtue of this, tungsten powder when compacted delivers unmatched density levels unachievable using any other material. Parts made from high-density tungsten powder find numerous applications in demanding environments.
Key drivers for utilizing high density tungsten powder include:
- High density similar to precious metals like gold, platinum
- Doubles the density available compared to lead, steel
- Enables heavy yet compact sizes and shapes
- Simple powder metallurgy route to end-use items
- Tailorable properties by mixing alloying elements
- Recyclability of high-value tungsten
Applications capitalizing on density span ballasts, radiation blocking, inertia, weighting of composites, vibration damping, and component miniaturization.
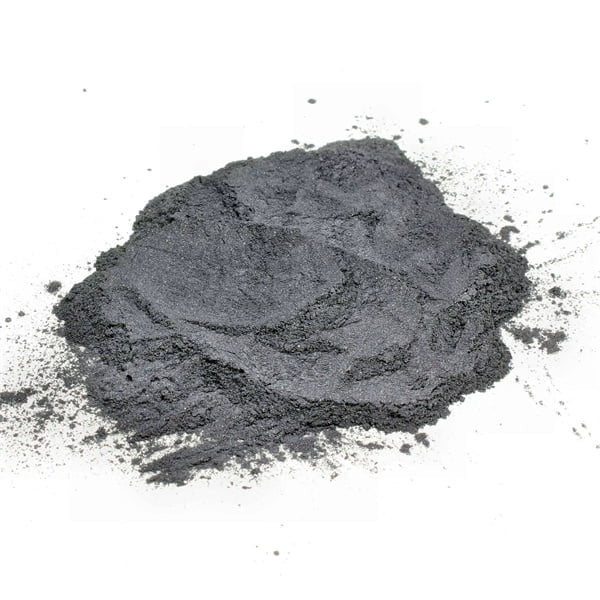
Types of High Density Tungsten Powder
While all tungsten powder varieties offer high density, certain grades and compositions impart optimal density levels after forming and sintering:
Type | Description | Typical Density |
---|---|---|
Pure tungsten | Higher purity above 99.95% ensures reliable density | ≥18 g/cm |
Doped tungsten | Small rare earth oxide additions like Y2O3 improves sintered density | ≥18.5 g/cm |
Tungsten-nickel-iron | Ni-Fe alloying provides excellent final density | ≥18 g/cm |
Tungsten heavy alloys | 90-97% W with Ni-Cu-Fe binder phases | ≥17.5 g/cm |
Tungsten composites | Mixes with gold, tantalum, depleted uranium etc. | up to 21 g/cm |
These enhanced formulations expand high-performance options beyond pure tungsten to tailored property combinations.
Composition of tungsten powder
High purity tungsten powder suitable for the highest possible density contains over 99.95% tungsten with only minor residual impurities:
Element | Maximum Content | Role |
---|---|---|
Tungsten (W) | 99.95% | Principal component |
Carbon (C) | 100 ppm | Grain growth inhibitor |
Oxygen (O) | 100 ppm | Surface oxide |
Copper (Cu) | 10 ppm | Residual trace impurity |
Silica (Si) | 20 ppm | Impurity |
Specialized heavy alloy grades have deliberate alloying additions like nickel, copper, iron etc. along with tungsten to enhance properties further.
Properties of tungsten powder
High density tungsten powder enables manufacture of near-net-shape parts boasting extreme density coupled with useful strength, hardness and thermal properties.
Physical Properties
Property | Value |
---|---|
Density | ≥18 g/cm<sup>3</sup> |
Melting point | 3380-3410°C |
Strength | Up to 1000 MPa |
Hardness | ≥400 VPN |
Thermal conductivity | ∼175 W/(m·K) |
Coefficient of thermal expansion | ∼4.5 μm/(m·K) |
These characteristics stem from tungsten’s intrinsic atomic structure and make it ideal for high-density applications needing thermal-mechanical integrity.
Mechanical Properties
Careful powder pressing and sintering imparts advantageous mechanical properties:
Property | Value |
---|---|
Hardness | Up to 550 VPN |
Yield Strength | ∼900 MPa |
Tensile Strength | Up to 1000 MPa |
Elongation | ∼10% to 15% |
Fracture Toughness | ∼20 MPa√m |
Fatigue Strength | 500 MPa |
Alloying elements like nickel, iron etc. help tailor ductility, toughness and machining characteristics.
Physical Attributes
Salient physical attributes of high density tungsten powder useful for designers:
Parameter | Value | Unit |
---|---|---|
Density | 18 to 19.3 | g/cm<sup>3</sup> |
Electrical Resistivity | 5.5 | μΩ·cm |
Thermal Conductivity | 170 | W/(m·K) |
Melting Point | 3410 | °C |
Boiling Point | 5930 | °C |
Specific Heat | 132 | J/(kg·K) |
The ultrahigh melting point and thermal conductivity ensure retention of strength and dimensional integrity at extreme temperatures.
Production of tungsten powder
Stage | Description | Key Points |
---|---|---|
1. Raw Material Acquisition | The process begins with mining tungsten ore, which primarily consists of wolframite and scheelite. | * Tungsten ores are found worldwide, but major producers include China, Peru, and Bolivia. * Mining methods vary depending on the deposit, but common techniques include open-pit and underground mining. * The mined ore undergoes crushing, grinding, and concentration processes to remove impurities and enrich the tungsten content. |
2. Chemical Processing | The concentrated ore is then converted into an intermediate chemical compound suitable for further purification and reduction. | * Ammonium paratungstate (APT) is the most widely used intermediate. It’s produced through a series of chemical reactions involving leaching, filtration, and precipitation. * APT offers advantages like high purity and good handling characteristics. * Other intermediate compounds like tungstic acid or tungsten oxides may also be used depending on the specific production process. |
3. High-Purity Oxide Production | Further purification steps ensure the removal of remaining impurities and achieve the desired level of tungsten oxide for reduction. | * APT undergoes additional purification steps like recrystallization or solvent extraction to meet the stringent purity requirements for tungsten powder production. * Tungsten oxides like WO3 (tungsten trioxide) or WO2 (tungsten dioxide) are often the final product of this stage. * The choice of oxide and its specific characteristics can influence the final tungsten powder properties. |
4. Hydrogen Reduction | The purified tungsten oxide is then reduced to metallic tungsten powder using hydrogen gas in a controlled furnace environment. | * This stage is the heart of tungsten powder production. Hydrogen acts as a reducing agent, taking oxygen away from the tungsten oxide and leaving behind pure tungsten metal particles. * The reduction process occurs in pusher furnaces or rotary furnaces at precisely controlled temperatures (typically between 600°C and 1100°C) and hydrogen gas flow rates. * Careful control of these parameters is crucial for achieving the desired tungsten powder properties like particle size, morphology, and purity. |
5. Powder Classification and Finishing | The raw tungsten powder from the reduction furnace undergoes further processing to achieve the final desired characteristics. | * The powder is screened and classified to obtain specific particle size distributions. Different applications require powders with varying particle sizes and morphologies. * Additional processes like milling or granulation may be used to refine the particle size and shape further. * The powder may also be subjected to degassing treatments to remove any residual hydrogen from the reduction process. |
6. Quality Control | Throughout the production process, rigorous quality control measures are implemented to ensure the final tungsten powder meets all the required specifications. | * Chemical analysis determines the elemental composition and purity of the powder. * Particle size distribution and morphology are analyzed using techniques like laser diffraction and electron microscopy. * Other tests may assess properties like density, flowability, and sintering behavior. * Maintaining consistent quality is essential for the performance of tungsten products made from the powder. |
Applications of tungsten powder
Category | Application | Properties Leveraged | Examples |
---|---|---|---|
Industrial & Manufacturing | Machining & Cutting Tools | Extreme hardness, wear resistance | – Drill bits – Milling inserts – End mills – Turning tools |
Dies & Molds | High melting point, thermal stability | – Extrusion dies for wires and filaments – Hot stamping dies – Plastic injection molding tools | |
Electrodes | High melting point, good electrical conductivity | – Inert gas welding (TIG) electrodes – Resistance welding electrodes | |
Filaments & Heating Elements | High melting point, good electrical conductivity | – Incandescent light bulb filaments – Furnace heating elements | |
Catalysts | High surface area, ability to promote chemical reactions | – Ammonia production catalysts – Hydrocarbon processing catalysts | |
Pigments & Coatings | High density, opacity to X-rays | – Radiation shielding for medical equipment – X-ray contrast agents | |
Electrical & Electronics | Electrical Contacts & Switches | High melting point, good electrical conductivity, arc resistance | – Relay contacts – Circuit breaker contacts – High-voltage switchgear contacts |
Heat Sinks | High thermal conductivity | – Electronic component heat dissipation | |
Semiconductor Manufacturing | High density, etch resistance | – Tungsten plugs and vias in integrated circuits – Gate electrodes in transistors | |
Consumer Goods | Sporting Goods (Golf Clubs, Fishing Weights) | High density for weight distribution | – Golf club weighting for improved swing – Fishing weights for deeper, faster sinking |
Vibration Damping | High density | – Dampeners in tennis rackets and archery equipment – Vibration dampers in machinery | |
Advanced Applications | Additive Manufacturing (3D Printing) | Fine particle size, good flowability | – 3D printed components for aerospace and automotive industries – Medical implants |
Nuclear Energy | High melting point, neutron absorption | – Control rods in nuclear reactors – Nuclear waste shielding | |
Military & Defense | Armor-Piercing Penetrators | High density, extreme hardness |
Specifications
Key parameters defined for high density tungsten powder:
Grades of Tungsten Powder
Grade Designation | Average Particle Size (Microns) | Purity (Minimum % Tungsten) | Applications |
---|---|---|---|
Ultrafine Tungsten Powder | < 1.0 | ≥ 99.95 | – Thermal Spray Coatings for turbine blades and other high-wear applications due to excellent sinterability and flowability. |
1.0 – 3.0 | ≥ 99.95 | – Diamond Tools with superior wear resistance and sharpness for cutting and grinding hard materials. | |
3.0 – 5.0 | ≥ 99.9 | – Electronic Substrates with minimal impurities for high electrical conductivity and thermal stability in integrated circuits. | |
Fine Tungsten Powder | 5.0 – 10.0 | ≥ 99.5 | – Cemented Carbide Cutting Tools offering a good balance between hardness, toughness, and fracture resistance for machining various materials. |
10.0 – 15.0 | ≥ 99.0 | – Heavy Duty Electrical Contacts requiring high melting point, arc resistance, and electrical conductivity in power switching applications. | |
15.0 – 22.0 | ≥ 98.5 | – Electrodes for Tungsten Inert Gas (TIG) Welding due to their ability to produce a stable arc and concentrated heat. | |
Medium Tungsten Powder | 22.0 – 32.0 | ≥ 98.0 | – Penetrators and Kinetic Energy Projectiles leveraging tungsten’s high density for superior armor penetration. |
32.0 – 45.0 | ≥ 97.0 | – Radiation Shielding Materials in medical equipment and nuclear facilities due to tungsten’s ability to absorb X-rays and gamma rays. | |
Coarse Tungsten Powder | 45.0 – 75.0 | ≥ 96.0 | – Ballast Weights for counterweights and vibration dampeners utilizing tungsten’s high density for compact size and effectiveness. |
> 75.0 | ≥ 95.0 | – Shot Peening Media for surface strengthening metal components through a cold working process. |
Standards of Tungsten Powder
Property | Description | Importance | Typical Standards |
---|---|---|---|
Purity | Tungsten powder purity refers to the percentage of tungsten metal (W) present in the powder by weight. Impurities can significantly affect the physical and mechanical properties of tungsten products. | Higher purity generally translates to better performance in applications that rely on properties like electrical conductivity, melting point, and strength. However, extremely high purity may not always be necessary or cost-effective. | – High Purity (99.9% W and above): Used for electronics, filaments, and electrodes where excellent electrical conductivity is crucial. – Standard Purity (99.5% W – 99.9% W): Suitable for various applications like cemented carbide cutting tools, heat sinks, and radiation shielding. – Lower Purity (Below 99.5% W): Used in some specific applications like plastic fillers or as a raw material for further purification. |
Particle Size & Distribution | Particle size refers to the average diameter of individual tungsten particles in the powder. Particle size distribution describes the variation in particle sizes within a powder sample. | Particle size and distribution significantly impact the processing behaviour and final properties of tungsten products. For example, finer particles can offer better sinterability but may be more challenging to handle. | – Micron-Sized Powders (1 – 50 microns): Commonly used for cemented carbide production, thermal spraying, and additive manufacturing. – Submicron Powders (Below 1 micron): Used in applications requiring high surface area, like catalysts and conductive coatings. – Nano Powders (Below 100 nanometers): Emerging area with potential applications in electronics and composite materials. |
Apparent Density | Apparent density represents the weight of tungsten powder per unit volume, considering the spaces between particles. It influences how much powder can be packed into a mold and the final density of the sintered product. | Higher apparent density allows for more efficient use of powder and can lead to denser final products with improved mechanical properties. | – High Density Powders (>10 g/cm³): Used for applications requiring high strength and wear resistance, like cemented carbide tools. – Standard Density Powders (7 – 10 g/cm³): Commonly used for various applications where a balance between density and processing ease is desired. – Low Density Powders (<7 g/cm³): May be used in applications where loose packing or flowability is important, such as some thermal spraying processes. |
Flowability | Flowability refers to the ease with which tungsten powder can move and be poured. It is crucial for efficient handling and processing in various applications. | Good flowability ensures smooth powder feeding in machinery and minimizes segregation of different particle sizes within the powder. | – Free-Flowing Powders: Achieved through specific particle size distribution and surface treatments to minimize particle-particle interactions. – Additives: May be used to improve flowability by reducing friction between particles. |
Morphology | Morphology refers to the shape and form of individual tungsten particles. | Particle morphology can influence packing behaviour, sintering characteristics, and the final microstructure of tungsten products. | – Spherical Powders: Offer good packing density and flowability. – Angular Powders: May create a more interlocking network during sintering, potentially leading to improved strength. – Dendritic Powders: Can be used for specific applications where their branching structure offers advantages. |
Oxygen Content | Oxygen content refers to the amount of oxygen present in the tungsten powder, typically as oxides. Excessive oxygen can affect the final properties of tungsten products. | – Low oxygen content is generally desired for most applications to ensure optimal performance. – Strict oxygen limits are often specified for high-performance applications like electronics and filaments. | |
Tap Density | Tap density is a measure of the packing density of tungsten powder achieved through a standardized tapping process. It provides an indirect measure of flowability and apparent density. | – Higher tap density indicates better packing efficiency and can be used as a quality control parameter. | – Industry standards often specify minimum tap density requirements for different tungsten powder grades. |
Pricing
Representative pricing of tungsten powder suitable for high density uses:
Grade | Price |
---|---|
Ultrafine | $800 to $1200 per kg |
Submicron | $500 to $900 per kg |
Fine | $100 to $250 per kg |
Medium | $50 to $150 per kg |
Heavy Alloys | $40 to $100 per kg |
Smaller particle sizes, higher purity, special dopants, and lower quantity increase cost. Recycled scrap powder is cheaper.
Pros and Cons
Advantages | Disadvantages |
---|---|
Unmatched High Melting Point: Tungsten powder boasts the highest melting point of any metal, reaching a staggering 3,422°C (6,192°F). This exceptional property allows it to excel in applications exposed to extreme temperatures, like furnace linings, rocket nozzles, and heat shields for spacecraft re-entry. | Costly Investment: Extracting and processing tungsten is a complex procedure, leading to a higher price tag compared to more common metals. This can be a significant hurdle for applications where cost is a major factor. |
Superior Heat and Electrical Conductivity: Tungsten powder excels in conducting both heat and electricity efficiently. This makes it ideal for applications requiring efficient thermal management, like heat sinks in electronics, or electrical components like filaments in incandescent lamps and electrodes for welding. | Dense and Demanding: Tungsten’s remarkable density, a direct consequence of its tightly packed atomic structure, translates to its powder form as well. This high density can pose challenges during processing. Specialized techniques and equipment might be necessary to handle and shape tungsten powder effectively. |
Exceptional Wear and Corrosion Resistance: Tungsten powder exhibits outstanding resistance to wear and tear, alongside exceptional corrosion resistance. This makes it perfect for applications requiring exceptional durability in harsh environments, like armor-piercing projectiles, drill bits for tough materials, and components used in chemical processing plants. | Potential Health Risks: Tungsten powder, if inhaled, can irritate the lungs and potentially lead to health complications. Strict safety protocols and proper ventilation are crucial when working with tungsten powder to minimize exposure risks. |
Tailorable Alloying Potential: Tungsten powder readily forms alloys with various metals, significantly enhancing their properties. This allows engineers to create custom-designed materials with specific combinations of strength, hardness, and heat resistance for applications like high-performance cutting tools and jet engine components. | Limited Global Supply: The primary source of tungsten is geographically concentrated, with China dominating global production. This can lead to supply chain vulnerabilities and potential price fluctuations. |
Biocompatible Applications: Tungsten exhibits good biocompatibility, making its powder form suitable for certain medical applications. For instance, tungsten-based implants can be used for hip replacements due to their exceptional strength and wear resistance. | Specialized Suppliers: Due to the unique properties and potential safety concerns of tungsten powder, sourcing it from reputable and experienced suppliers is essential. These suppliers can provide high-quality, well-characterized powder alongside technical support to ensure safe handling and optimal performance in the desired application. |
Emerging Applications in 3D Printing: Tungsten powder is finding new applications in the rapidly advancing field of additive manufacturing, also known as 3D printing. Its unique combination of properties makes it suitable for printing high-performance metal parts for aerospace, automotive, and medical industries. | Counterfeit Concerns: The high value of tungsten powder can attract manufacturers of counterfeit products. Working with qualified suppliers with rigorous quality control practices helps mitigate the risk of receiving inferior or impure material. |
Suppliers
Prominent merchants and manufacturers supplying high density tungsten and tungsten alloy powders globally include:
Company | Locations |
---|---|
Buffalo Tungsten | United States |
Wolfram Company | Austria |
Plansee Group | Europe |
Midwest Tungsten | United States |
Xiamen Tungsten | China |
JX Nippon | Japan |
Toshiba Materials | Japan |
GTP Schaefer | Germany |
These corporations cater reliable world-class powders to commercial markets.
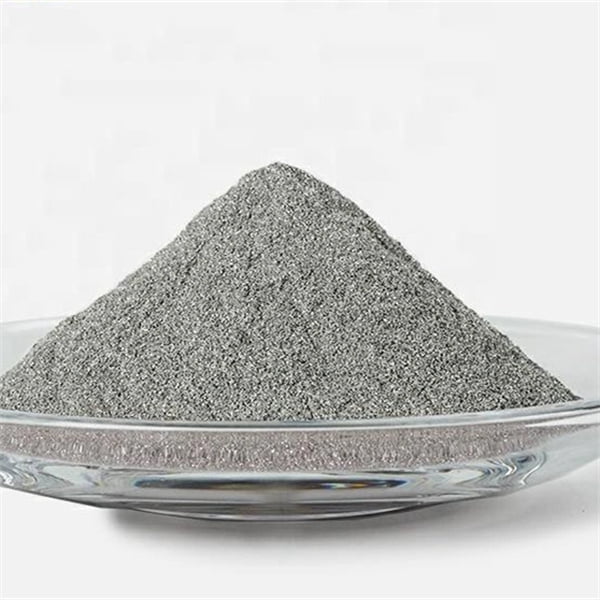
FAQs
Question | Answer |
---|---|
What is high density tungsten powder? | Tungsten powder possessing density from 18 to 19.3 g/cm<sup>3</sup> – highest among all metal powders |
How is high density tungsten powder manufactured? | Reduction of purified tungsten oxide combined with specialized milling for desired particle sizes |
What is high density tungsten powder used for? | Fabricating counterweights, radiation shielding, ballast, weighting compounds, vibration damping components, etc. |
What are the different varieties of high density powders? | Pure tungsten, doped tungsten with rare earth oxides, tungsten-nickel-iron alloys, tungsten heavy alloys etc. |
What are the advantages of high density tungsten powder? | Extreme density in compact volumes unmatched by other powders; net-shape manufacturability into complex parts |
What are the limitations of tungsten powders while using them? | Relatively lower hardness than tungsten carbide; limited toughness and ductility pose machining challenges |
How does high density tungsten powder compare against traditional dense materials like lead? | Safer than toxic lead; higher melting point than lead; economically priced against precious metals with similar density |
Summary
With extraordinary density among elemental metals, high purity tungsten powder offers designers unique capabilities for weight-sensitive applications needing compact profiles not feasible earlier. Advances in powder manufacture, pressing, sintering and secondary processing overcome brittleness limitations unlocking wider use. Blending and alloying provides additional tailoring of physical properties across demanding electrical, nuclear, automotive and aerospace domains where high density couples critically with strength, hardness and thermal pedigree.
As sustainable sources back reliable global supply chains, designers now harness density extremes in tungsten powder towards precision engineering functionality across industries where heaviness and compactness together drive value. Leading manufacturers will pursue crossing density thresholds beyond 20 g/cm3 in the coming decade as tungsten assumes greater strategic importance.
Share On
MET3DP Technology Co., LTD is a leading provider of additive manufacturing solutions headquartered in Qingdao, China. Our company specializes in 3D printing equipment and high-performance metal powders for industrial applications.
Inquiry to get best price and customized Solution for your business!
Related Articles
About Met3DP
Recent Update
Our Product
CONTACT US
Any questions? Send us message now! We’ll serve your request with a whole team after receiving your message.
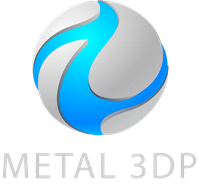
Metal Powders for 3D Printing and Additive Manufacturing