Metal Powders for High-Stress Engine Applications
Table of Contents
In the fast-paced world of engineering, where performance and durability are non-negotiable, the materials we use can make or break the success of a project. High-stress engine applications, such as those found in aerospace, automotive, and industrial machinery, demand materials that can withstand extreme conditions without compromising on reliability. Enter metal powders—specifically engineered for these demanding environments, they offer unique properties that traditional materials simply cannot match.
Overview OF high-stress engine applications
Metal powders are finely divided metals used in the production of advanced components. These powders are created through various processes, including atomization, reduction, electrolysis, and mechanical alloying. In high-stress engine applications, metal powders are prized for their strength, durability, thermal stability, and resistance to wear and corrosion. They are used to produce parts through methods like powder metallurgy, additive manufacturing (3D printing), and hot isostatic pressing (HIP).
Key Characteristics of Metal Powders for High-Stress Applications
- Strength and Durability: Metal powders offer high tensile strength and fatigue resistance, essential for components subjected to extreme loads.
- Thermal Stability: They maintain integrity at high temperatures, crucial for engine parts exposed to intense heat.
- Wear and Corrosion Resistance: Metal powders are engineered to resist wear and corrosion, extending the life of components in harsh environments.
- Precision and Customizability: These powders can be tailored to specific applications, ensuring optimal performance and efficiency.
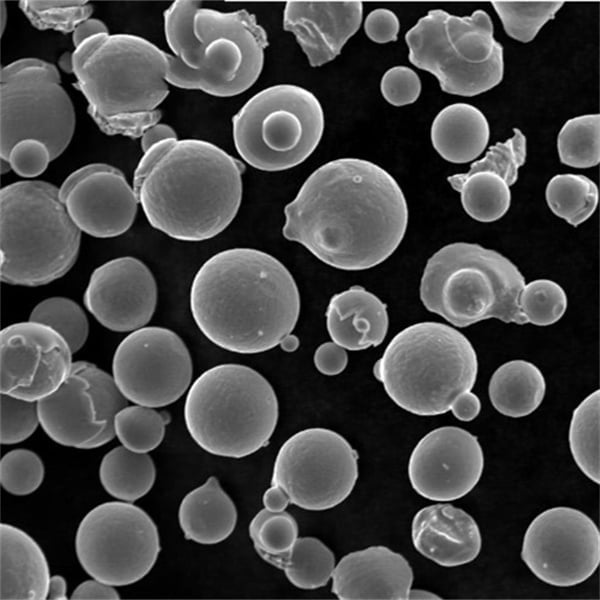
Types of Metal Powders and Their Properties
Below is a comprehensive table detailing various metal powders used in high-stress engine applications, their compositions, and key properties.
Metal Powder | Composition | Properties | Characteristics |
---|---|---|---|
Stainless Steel 316L | Fe, Cr, Ni, Mo, Mn, Si | High corrosion resistance, high strength | Excellent for marine and chemical environments |
Titanium Ti-6Al-4V | Ti, Al, V | High strength-to-weight ratio, biocompatible | Commonly used in aerospace and medical implants |
Inconel 718 | Ni, Cr, Fe, Mo, Nb, Ti, Al | Excellent high-temperature strength, corrosion resistance | Ideal for jet engines and gas turbines |
Aluminum AlSi10Mg | Al, Si, Mg | Lightweight, good thermal conductivity | Used in automotive and aerospace applications |
Cobalt-Chrome (CoCr) | Co, Cr, Mo, Si, Mn, Fe, Ni | High wear resistance, biocompatible | Perfect for medical implants and dental devices |
Maraging Steel | Fe, Ni, Mo, Co, Ti | Ultra-high strength, excellent toughness | Utilized in aerospace, tooling, and high-performance engineering |
Copper (Cu) | Cu, with small amounts of other elements | High thermal and electrical conductivity | Used in electrical components and heat exchangers |
Nickel Alloy 625 | Ni, Cr, Mo, Nb | Outstanding fatigue and thermal-fatigue strength | Preferred in aerospace and marine environments |
Tungsten Carbide | WC, Co | Extremely hard, high wear resistance | Essential for cutting tools and abrasives |
Hastelloy X | Ni, Cr, Mo, Fe | High oxidation resistance, good high-temperature strength | Suitable for gas turbines and industrial furnace components |
Applications of Metal Powders in High-Stress Engine Environments
Metal powders are employed across a wide range of high-stress engine applications. Here’s a detailed look at where and how these advanced materials are used:
Application | Industry | Usage | Advantages |
---|---|---|---|
Jet Engine Components | Aerospace | Turbine blades, combustors, nozzles | High strength at elevated temperatures, corrosion resistance |
Automotive Engine Parts | Automotive | Pistons, turbochargers, cylinder liners | Lightweight, enhances fuel efficiency, reduces wear |
Industrial Machinery | Manufacturing | Gears, bearings, hydraulic components | High durability, wear resistance |
Medical Implants | Healthcare | Hip and knee replacements, dental implants | Biocompatible, corrosion resistant |
Heat Exchangers | Energy | Tubes, plates, fins | Excellent thermal conductivity, corrosion resistance |
Tooling and Molds | Tool and Die Making | Cutting tools, dies, molds | High hardness, wear resistance |
Gas Turbines | Power Generation | Blades, vanes, combustion chamber linings | High-temperature stability, oxidation resistance |
3D Printed Components | Various | Custom parts, rapid prototyping | Design flexibility, material efficiency |
Electrical Components | Electronics | Conductors, connectors, heat sinks | High electrical conductivity, thermal management |
Marine Components | Marine Engineering | Propellers, shafts, underwater housings | Corrosion resistance, high strength |
Specifications, Sizes, Grades, and Standards
Metal powders for high-stress applications come in a variety of specifications to meet the stringent demands of different industries. The following table outlines typical specifications, sizes, grades, and standards.
Metal Powder | Specifications | Sizes (µm) | Grades | Standards |
---|---|---|---|---|
Stainless Steel 316L | ASTM A276, AMS 5648 | 15-45, 45-105 | 316L, 1.4404 | ASTM, ISO, AMS |
Titanium Ti-6Al-4V | ASTM B348, AMS 4928 | 15-45, 45-150 | Grade 5, Grade 23 | ASTM, ISO, AMS |
Inconel 718 | ASTM B637, AMS 5662 | 15-53, 53-150 | 718 | ASTM, AMS, UNS |
Aluminum AlSi10Mg | ISO 3522, DIN EN 1706 | 15-45, 45-100 | AlSi10Mg | ISO, DIN |
Cobalt-Chrome (CoCr) | ASTM F75, ISO 5832-4 | 20-53, 53-150 | F75, F1537 | ASTM, ISO |
Maraging Steel | AMS 6512, ASTM A579 | 15-45, 45-105 | 18Ni(300), Grade 300 | AMS, ASTM |
Copper (Cu) | ASTM B170, ASTM B187 | 20-63, 63-150 | C10100, C11000 | ASTM, SAE |
Nickel Alloy 625 | ASTM B443, AMS 5599 | 15-45, 45-150 | 625 | ASTM, AMS, UNS |
Tungsten Carbide | ISO 4499, ASTM B777 | 1-10, 10-20, 20-45 | WC-Co, 94 WC-6 Co | ISO, ASTM |
Hastelloy X | ASTM B572, AMS 5536 | 15-45, 45-105 | X, UNS N06002 | ASTM, AMS, UNS |
Suppliers and Pricing Details
Finding the right supplier is crucial for obtaining high-quality metal powders. The table below lists reputable suppliers and estimated pricing.
Supplier | Metal Powders Available | Price Range (per kg) | Contact Information |
---|---|---|---|
Höganäs AB | Stainless Steel, Nickel Alloys, Copper, Titanium | $50 – $200 | www.hoganas.com |
Carpenter Technology | Stainless Steel, Titanium, Cobalt-Chrome, Maraging Steel | $100 – $300 | www.carpentertechnology.com |
Sandvik Materials | Titanium, Nickel Alloys, Stainless Steel | $80 – $250 | www.materials.sandvik |
GKN Hoeganaes | Nickel Alloys, Copper, Stainless Steel, Aluminum | $70 – $220 | www.gkngroup.com |
Praxair Surface | Inconel, Hastelloy, Tungsten Carbide, Cobalt-Chrome | $150 – $400 | www.praxairsurfacetechnologies.com |
Kennametal | Tungsten Carbide, Cobalt-Chrome, Maraging Steel | $120 – $350 | www.kennametal.com |
AP&C | Titanium, Stainless Steel, Aluminum | $90 – $280 | www.advancedpowders.com |
Erasteel | Maraging Steel, Stainless Steel | $110 – $330 | www.erasteel.com |
ATI Powder Metals | Nickel Alloys, Titanium, Stainless Steel | $95 – $270 | www.atimetals.com |
Oerlikon Metco | Cobalt-Chrome, Nickel Alloys, Titanium, Aluminum | $100 – $320 | www.oerlikon.com/metco |
Advantages and Disadvantages of Metal Powders in High-Stress Applications
Understanding the pros and cons of using metal powders is essential for making informed decisions. The table below compares the advantages and limitations.
Advantages | Disadvantages |
---|---|
High Strength and Durability: Ideal for components subjected to extreme loads | Cost: Generally more expensive than traditional materials |
Thermal Stability: Maintain integrity at high temperatures | Complexity of Production: Requires advanced manufacturing techniques |
Wear and Corrosion Resistance: Extends the life of components in harsh environments | Availability: Limited availability for some specialized powders |
Precision and Customizability: Can be tailored to specific applications | Material Waste: Potentially higher material waste during production |
Design Flexibility: Enables complex geometries and lightweight structures | Processing Time: Some processes can be time-consuming |
In-Depth Comparison of Specific Metal Powders
To provide a clearer picture, let’s delve deeper into the comparison of some popular metal powders used in high-stress engine applications.
Stainless Steel 316L vs. Inconel 718
- Stainless Steel 316L: Known for its excellent corrosion resistance and high strength, 316L is widely used in marine and chemical environments. It’s also relatively affordable compared to other high-performance alloys.
- Inconel 718: This nickel-chromium alloy offers outstanding high-temperature strength and corrosion resistance, making it a favorite for jet engines and gas turbines. However, it comes at a higher cost than 316L.
Titanium Ti-6Al-4V vs. Aluminum AlSi10Mg
- Titanium Ti-6Al-4V: With a high strength-to-weight ratio and excellent biocompatibility, this alloy is perfect for aerospace and medical applications. It’s more expensive but provides superior performance in critical applications.
- Aluminum AlSi10Mg: Lightweight and with good thermal conductivity, this alloy is commonly used in automotive and aerospace sectors. It’s more affordable than titanium alloys but offers less strength and wear resistance.
Cobalt-Chrome (CoCr) vs. Tungsten Carbide
- Cobalt-Chrome (CoCr): This alloy is highly resistant to wear and biocompatible, making it ideal for medical implants and dental devices. It’s pricier but necessary for applications requiring durability and biocompatibility.
- Tungsten Carbide: Known for its extreme hardness and wear resistance, tungsten carbide is essential for cutting tools and abrasives. It’s less versatile than CoCr but excels in applications demanding toughness.
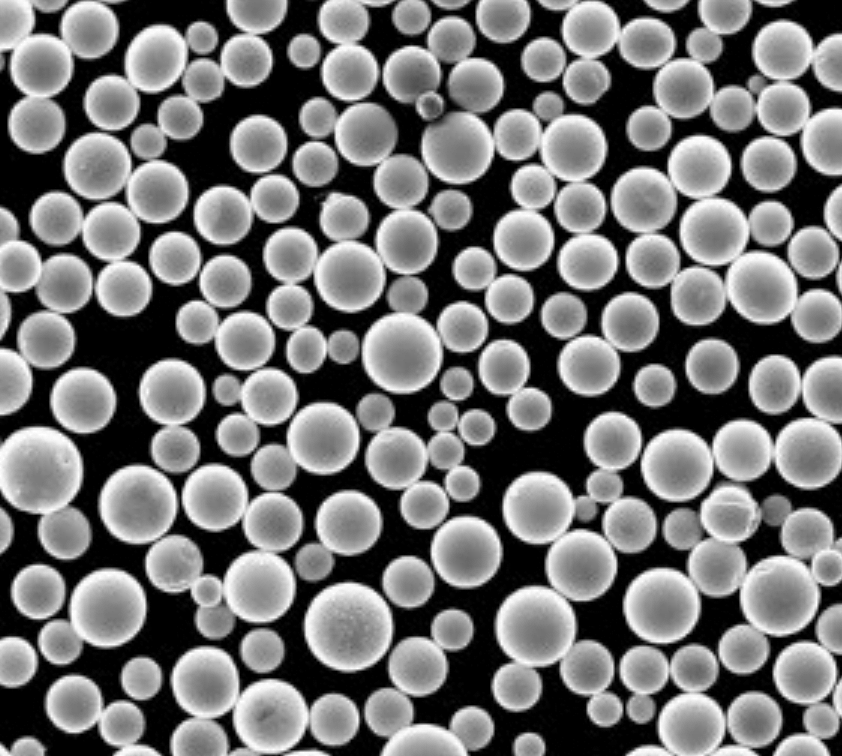
FAQ
Question | Answer |
---|---|
What are metal powders? | Metal powders are finely divided metals used to produce components through various manufacturing processes. |
Why use metal powders in high-stress engine applications? | They offer high strength, durability, thermal stability, and resistance to wear and corrosion. |
What are the common manufacturing processes for metal powders? | Atomization, reduction, electrolysis, and mechanical alloying. |
Which industries benefit from metal powder components? | Aerospace, automotive, industrial machinery, healthcare, energy, and electronics. |
What is the advantage of using titanium alloys? | High strength-to-weight ratio and excellent biocompatibility. |
Are metal powders more expensive than traditional materials? | Yes, they are generally more expensive due to the advanced manufacturing techniques required. |
Can metal powders be customized for specific applications? | Yes, they can be tailored to meet the specific needs of different applications. |
What are the limitations of using metal powders? | Higher cost, complexity of production, limited availability, potential material waste, and processing time. |
How do I choose the right metal powder for my application? | Consider factors like strength, thermal stability, corrosion resistance, and specific industry requirements. |
Where can I buy high-quality metal powders? | Reputable suppliers include Höganäs AB, Carpenter Technology, Sandvik Materials, and Praxair Surface. |
Conclusion
Metal powders represent a significant advancement in materials technology, offering unparalleled performance in high-stress engine applications. Whether it’s the strength and corrosion resistance of stainless steel 316L, the high-temperature stability of Inconel 718, or the biocompatibility of titanium Ti-6Al-4V, each metal powder brings unique benefits tailored to meet the demands of various industries. By understanding the properties, applications, and suppliers of these advanced materials, engineers and manufacturers can make informed decisions to enhance the performance and longevity of their high-stress components.
Share On
MET3DP Technology Co., LTD is a leading provider of additive manufacturing solutions headquartered in Qingdao, China. Our company specializes in 3D printing equipment and high-performance metal powders for industrial applications.
Inquiry to get best price and customized Solution for your business!
Related Articles
About Met3DP
Recent Update
Our Product
CONTACT US
Any questions? Send us message now! We’ll serve your request with a whole team after receiving your message.
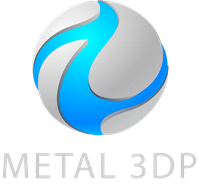
Metal Powders for 3D Printing and Additive Manufacturing